Thermal performance of steel embedded in foam

The company Legalett out of Canada offers an EPS panel system (Thermalwall) designed to make installing thick exterior foam both easier and with less thermal bridging at screw heads. Its made for both ICFs and wood frames walls. They do this by embedding a steel channel 3 inches inside each foam panel that has a foam insert that is replaced after installing screws. I have attached a photo from their marketing that shows this. Here is a link to their product page. http://www.legalett.ca/eps-foam-panel-wall-insulation-passive-house-zne-leed-nzeb-thermalwall-ph.html
My main concern relates to the steel that’s embedded in the foam. While the company claims an 8″ panel provides R-32 with virtually no thermal bridging (since the screws are buried in foam), I still am left wondering if the steel inside the panel will have any effect on the total R value of the wall due to the poor thermal properties of steel. I have read elsewhere on green building advisor about the thermal perils of using steel studs, I just am unsure if the same principles would apply here. Maybe someone more intelligent than I in the subject of thermal dynamics can weight in.
Thanks!!
-Chris
GBA Detail Library
A collection of one thousand construction details organized by climate and house part
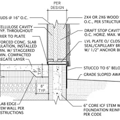
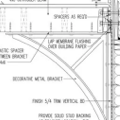
Replies
Since the steel plate runs parallel to the surface it won't transmit heat from the cold side to the warm side. The only transmission will be through the screws. The heads will still be covered with 3" of foam so the transmission should be negligible.
Thanks for the reply, I suppose I made steel boogieman but didn't think logically about it.
I agree with DC here. The issue with steel studs is that they are studs — they go all the way from one wall surface to the other, which allows them to conduct heat from the inside surface to the outside (or vice versa). The channel in that panel is not in contact with either surface, so it doesn’t do anything to thermally bridge the two surfaces together.
Don’t worry about screws being thermal bridges. The very small cross sectional area of the screws in comparison to the size of a wall panel makes the heat lost through the screws essentially irrelevant. I calculated the total heat loss through a 4x8 piece of wall sheathing due to screws a few months ago and posted the results in this forum. The TOTAL heat lost through ALL of the screws was somewhere in the single digit BTU/hour range (I don’t remember the exact number). Since the ends of the fasteners are embedded in wood (or insulation, in the case of the panel you’re looking at), the total heat loss will be even less.
I think I’d compared the total losses to the thermal losses through air leaks in your keyholes. It’s so small so as to be essentially immeasurable.
Bill
Bill thanks for the detailed response. Whenever I did research on the subject of thermal bridging of screws, I often got a mixed response. But it seems overwhelmingly more to the side that its not so much an issue.
I’ve seen the confusion too. I think it’s because people know steel is much more thermally conductive than wood (or insulation), so they get all concerned and try to minimize the impact of the fasteners.
What those people don’t stop to think about is that a typical nail is about 1/10” or so in diameter, so even with an 8” grid nailing schedule, which is 72 nails per 4x8 foot panel. That’s about 0.566 square inches of total fastener area compared to 4,608 total square inches of panel area. The total area of the fasteners is less than 0.013% of the total area of the panel, so the additional thermal conductivity of those fasteners doesn’t actually contribute very much in terms of total energy losses to structure.
Bill
Hi All,
I have posted this pic before. The screws are steel and 8" long. They embed into 2x10's supporting 2" of iso foam first, then 4" EPS nailbase next. The joist bays were sprayed with closed cell. It is a future deck area off the upstairs bedroom. We had limited depth to work with here and the main roof areas have 8 1/2" nailbase over the sheathing - r-19 batt under. The ten" screws ghost a bit less. I suspect the foam supports conduction of heat loss via the joists by keeping the heat losses sideways (so to speak) lower than if the screw is embedded into wood the whole distance like timber framing.
It may be true that the total cross sectional area of each nail or screw is trivial relative to the panel area, but if one does take into account the thermal conductivity differences, I think it reveals what shows in the picture.
To refresh the discussion, wood has a general thermal conductivity value of .15 BTU/(ft-hr-F), carbon steel 34 -56 BTU/(ft-hr-F) average of 45 or 300 times the conductivity of wood. Is it unreasonable to then adjust the 0.013% area by 300x to arrive at 3.9%? This would translate into very close to 1.25 sq ft of area relative to the 32 sq ft of a 4x8 panel. Thermally this would appear to be the equivalent of eliminating that much insulation area from screw head to anchor point material - in this case my iso-eps sandwhich.
The steel channels in the system referred to would seem to likely suffer similar compromise rates as the steel screws holding the channel would feed heat outward and be relatively lossless given the surrounding foam. The screws penetrating from the cladding side would complete the bridge, again with relative efficiency due to the protective foam they pass through.
I believe that ORNL found a similar situation that compromised the total thermal performance of the Thermomass system of foundation walls. The fiberglass stand offs used to center the foam in the middle of the forms did not substantially degrade thermal performance but the numerous steel form ties required to hold everything together did.
I have not had time to review the downloads I took from the site and will remain open to proof of effectiveness on a whole wall basis. Meantime, I am not convinced that the dimples I see do not represent a non-trivial heat loss.
Basically correct, but since the fasteners are embedded into the 2x10s, the wood acts to insulate the fasteners a bit. This makes the overall thermal conductivity somewhat less than it would be if it was just a nail sticking through the sheathing into nothing.
My guess is that in your pic, you are using screws that are significantly larger diameter than the usual nails used to hold up wall sheathing. Larger screws most certainly will conduct more thermal energy compared with smaller fasteners.
In your pic, the total thermal losses are essentially integrated over time by the snow. This means the relatively small losses through the fasteners melt the snow gradually as it is accumulating resulting in a more noticeable amount of “dimple” than you might expect. The losses will still be relatively small compared with the rest of the structure, but they are there.
I suppose you could try using adhesive to assemble the final layers of the structure so that the fastener heads are buried under the last sheet of insulation to eliminate the thermal bridging of the fasteners, but you’d probably run into problems with inspectors due to your “no fastener” installation of the final layers of the assembly.
Bill
Bill,
Yes indeed the screws have a greater cross section per unit than nails, but there are fewer than when nailing off a panel as you chose for an example. This is not quite relevant though, as the presence of a loss path was what I wished to illustrate. The total losses will be driven by the total cross sectional area regardless of how it is achieved. The subject of anchoring thick foam usually leads to discussions about loss values and big screws. They do leak heat, how much and the overall performance hit is the discussion.
I disagree with your assigning additional significance to the losses through each screw being accumulated and thus over represented in the snow pits. All heat losses, whether through fasteners or field areas of walls or roofs will be accumulative. The steel screws just lose more faster than the field areas and can overcome the melting point of snow to reveal themselves.
Accounting for losses through whatever pathway is relevant. Whole wall ratings and framing factors look at heat losses with the same eye toward localized effective insulation value reductions. Effective R value reductions can also occur from excessive framing or window openings. Both cases create pathways for heat to be lost, albeit windows are somewhat special cases. Long steel screws might be best likened to excessive framing. Advanced framing is intended to reduce whole wall loss values, avoiding long screws should have a similar effect.
I suggest the embedded steel channels (in the mentioned product), if attached both to interior framing and to exterior cladding via steel fasteners, will degrade the performance relative to the pure foam areas. Not too controversial an idea. How bad the effect is could be determined with a whole wall test such as ORNL has done for other assemblies. The trade off may be a more builder friendly way to get a still much better result than other exterior insulation options. Certainly fastener conductivity creates questions as to the ultimate functional R value of 2" ZipR with the required high density of fasteners for shear strength.
To your other points...The conductivity of the steel in fasteners remains whatever it is regardless of placement. I believe I attempted to describe the condition of a fastener's loss rate being tempered by whatever it was stuck into. In my case the top 2" of the 2x10. The final loss rate would be of course tempered by the effective R value of the first 8" or so of wood, which would regulate the amount of heat loss for the cross section of each fastener to effectively something around R9 I think.
If one drilled a hole through all the other layers directly down to the 2x10 top, the heat loss for that hole's cross section would be R9 times a very small area. However, that cross section has a thermal conductivity 300x larger than a completely empty hole thanks to the steel shaft. I may be mistaken on the absolute increase in loss rate, but it appears to be non-trivial. That said, if I had anchored into a concrete wall or the top of a twenty inch glu-lam I would expect the effective R values and losses via the steel fastener to be very different.
A steel screw's high conductivity simply represents direct loss to the outside temperatures during winter (and a similar heat load during the summer). My own thoughts on the matter led me to use the Quadlock system as the base foam insulation on the house walls. Special plastic hangers, which lock the panel pieces onto the wall, are screwed with very short fasteners directly to the sheathing. The plastic locking parts are much less conductive than steel, so their profile, which reaches near the face of each 4 1/2" thick block, don't represent a huge loss channel. I chose a synthetic stucco finish, which was applied to low density foam adhered directly to the Quadlock material. At least for my walls, there are no metallic pathways present except for the starter channel at the bottom. This is working quite well compared to the roof system from a thermal aspect.
The total BTU losses represented by the hundreds of long steel screws used to hold down the nailbase may be small against overall energy consumption, but it still annoys me to see them taunting me every light snow fall.
What I had meant by the screw being embedded in wood is that the screw is somewhat insulated by that wood, similar to covering the screw head with another layer of insulation. The screw in that case has less total thermal losses than it would if it was driven through the sheathing and left exposed on both sides. The thermal conductivity of the screw material itself does not change, but it’s somewhat encased in insulation that reduces the total amount of thermal energy that will be lost through the screw due to the extra insulation.
I don’t disagree with you that there most certainly IS heat lost through the metal fasteners. There absolutely is. What I’m saying is that if you look at all of the heat lost through an entire structure, walls, Windows, keyholes, everything, the overall impact of the fasteners themselves is pretty small. You could potentially lower total thermal losses more for less money/effort with additional insulation or air sealing compared to fancy fasteners and unusual attachment methods (I haven’t calculated any of this though). It’s like chasing a very small potential improvement when there are other, more significant improvements that would be easier to implement.
Bill
I think the melting you are seeing is related to the thermal mass of the screws rather than conductance
AS they say, there is math for that, and the square footage of screws is what it is
Trying to figure this one out... a little help? It takes energy to melt the snow, and conduction is the mechanism of energy transfer. Where's the specific heat capacity come into play?
black EPDM roof absorbs heat from sun
no thermal mass to speak of in the foam
screw heads store heat
snow falls, snow melts when it hits still warmer screw heads[ and washers]
Just seems a more likely theory than enough heat travelling up the screw
In my admittedly long winded discussion, I did note that the screws can only convey/lose as much heat as the warmest point they are stuck in (the 2x10). I also noted it is not a huge amount, but not completely without merit to consider in designing. When building, I did extensive air sealing, installed .15 and .19 windows, fussed design details at the sill level and most every where else, and generally drove the builder to distraction. I have achieved a energy usage for heat in the 1.3-1.5 BTU/SF/HDD so I am not distraught about the screw leakage, just annoyed.
The Quadlock method may have been slightly more costly than attempting sheet goods, but for the thickness attained I am doubtful. We would have ended up needing several hundred more long and expensive screws, plus the builder was more willing to work with the Quadlock system.
The screw heads in the picture are just underneath the roof membrane, so it is effectively open to the air temps. I would analogize that the heat flow in the steel shank is protected by the insulation it passes through just as hot water would be protected by insulation wrapped around the pipe carrying it. True, if the screw head was covered by more insulation, the losses would be lower by whatever value the insulation had. Same is true when doing exterior insulation to minimize stud loss.
It might help to analogize the cold head of the screw passing through insulation by imagining someone dressed up in a big warm snow suit with the pants bottom cut out. Sitting on a park bench would certainly draw the heat out of you.
That just wouldn't be a good fashion to promote.
If you have 32 1/4 inch screws in an r 32 4x8 panel it lowers the r value of that panel to like r31.65 or something. assuming an r value of 1 for the screws.
its a rounding error