There just isnt a easy answer that covers zone 6a wall retro fits, is there?

I’m newer to GBA as well as newer to the whole subject of air sealing, insulation, etc.. Forgive my lack of understanding but I am surprised that there isnt all encompassing answers to retrofits in specific zones. For instance I live in zone 6A. I have 2×4 walls, completely uninsulated, 2 layers of drywall, buffalo board sheathing, and I think tar paper all covered by a layer of wood siding and then a layer of steel siding. Now I’m going to reside my house. I intend to get off both layers of siding and I was advised to replace the sheathing as well. So I’ve been googling exterior wall retro fits. Jeepers, I’ve read so many peoples totally different plans and materials to do the same thing- zone 6a retrofit. The widely different plans was enough to blow a fuse in my brain just trying to take it all in and distill it to my level of understanding. I’ve grasped two golden rules to fit all zone 6a: r11.25 of exterior foam board for 2×4 walls of r19 or less. And no poly barriers. So I believe what I need is to pump the walls with cellulose and put a minimum of r11.25 eps on. Doesnt that work for all zone 6a? Can we simplify some basic standards like that for people like me who struggle to understand all the jargon you professionals toss around? Excuse my plaintive cry of under education. I’m sorry for being a whiner. Anyhoodlydoodle, will someone give me the golden approval of stuffing cellulose to my 2×4 walls-plywood sheathing-housewrap-minimum r11.25 eps-rainscreen-bugscreen-siding. Sound ok enough? 🤔 thank you so much for any advice or comments.
GBA Detail Library
A collection of one thousand construction details organized by climate and house part
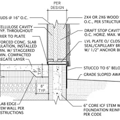
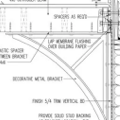
Replies
"There's more than one way to skin a cat "
- Code is code. It doesn't matter how one gets there. Retrofits are by their very nature unique because homeowners have different goals in mind with regards to what features of the house they want to preserve. Codes differ from state to state, locale to locale. So you can either build to the code adopted by your state/local govt OR build to the latest code revision. Keep in mind that builders are most familiar with local code.
Current code (2018 IECC) states the following for a wall in Zone 6: R20+R5 or R13+R10.
https://www.energycodes.gov/sites/default/files/becu/2018_IECC_residential.pdf
You have a 2x4 exterior wall so outside of using closed-cell spray foam it's going to be difficult to pack R20 into that kind of wall. R13 cavity insulation is easy. It can be spray foam, cellulose, fiberglass, mineral wool, whatever. R10 is also easy because it can be exterior mineral wool/rigid foam or an all-in-one product like ZIP-R.
Just mind your flashing details for your windows.
Hi Trina.
I understand and can relate to your feelings.
Building, and especially retrofit work, is a far cry from factory standardized protocols. There are times when I do think a more standardized approach would have its benefits (efficiency of implementation, simplification of education of trades, etc) but there's a slew of reasons it's not that realistic or desirable at this time. Especially with retrofits, where every situation (existing conditions and finish goals) is different.
What can be universally helpful are the underlying building science principles. Given your approach of exterior insulation, this article may help explain a key concept or two: https://www.greenbuildingadvisor.com/article/combining-exterior-rigid-foam-with-fluffy-insulation
Also many, many, links off that article to a wealth of knowledge and discussion of different approaches.
Re your situation: hopefully you realize what a large task pulling off the exterior all the way to the studs is. What was the advise to replace the sheathing based on? If you DON'T replace the sheathing, blown-in cellulose is probably a good approach. If you DO, you could still use blown-in, but you could perhaps also consider batts since the walls would be open.
Regardless of if the sheathing is new or old, try to establish an air barrier somewhere (at sheathing or foam layer most likely). Not establishing a solid air barrier would be a wasted opportunity for a retrofit of this scale.
Trina,
Your proposed wall system meets the current international Residential Code requirements for your zone, and it is a "safe" wall assembly in terms of moisture management. Bottom line: It will work, and be a huge improvement over what you've got now.
If you spend some extra time and effort on making the sheathing layer airtight, your energy performance and comfort will be even better.
Hello Trina,
I understand the confusion. I'm in zone 5a and had a similar issue trying to decide how to retrofit.
I had the same basic wall assembly: Plaster over board, 2x4 framing, Celotex/Buffalo Board, and then plywood board and batten siding. I initially intended to just re-side over the existing plywood base, but unfortunately the previous owner had partially replaced it with T1-11, and put a 6mil poly underneath it.
Once I dug into it, I decided to go for a deep energy retrofit, and that's where things went a little nuts.
My steps:
Remove all exterior finishes and sheathing - Air sealing in that era was non-existent, and using a combo product like Zip makes it much easier.
Attach Exterior insulation - I added (2) layers of reclaimed polyiso totaling 4.25". With framing factored in, I'm getting around R40.
Slab Insulation - I've dug around the perimeter, and added 3" of XPS.
Add rainscreen - I'm using 1x4 vertical strapping.
Add good siding - I'm using LP Smartside. Easy to handle, works like wood, not as ludicrously expensive as wood.
Interior - I have gutted a number of areas, and have the luxury of access to the interior. I'm using Intello as my interior air barrier, with dense pack cellulose. I've added a service cavity in some areas.
Attic - I've air-sealed the attic floor, added baffles, and blown to R60.
My recommendations for you:
I believe you posted earlier with your project goals, and that much of this will be handed off to a contractor. I had also intended to pass it off, but I couldn't get them to understand the project. To make this more palatable, and less problematic, I would recommend using practices and products that they can handle similar to things they already do.
Your configuration above would work for sure, but harder to deal with. You're basically talking about adding 3" of EPS to the exterior. Using a rainscreen of 1x material, that means using a screw around 5.5" long to get adequate fastener penetration. It gets really hard to find those studs with thicker foam.
Sheathing -
Buffalo Board is typically 3/4-1" thick, at least what I have come across. That means that your framing setback is around 1/2-3/4". That makes some room to use a sheathing product like Zip-R. It installs in a very similar fashion to typical sheathing, and with Zip-R, R-6, you can still use a normal nailer.
While that only gets you to R6, adding 1.5" of foam to the exterior would be quite simple compared to thicker foam you mention above. Depending on product, that will get you an additional R5-7.5ish. Again, it uses normal-ish products. 3.5-4" screws to attach furring strips.
Other opportunities:
I rewired all of the exterior walls when I removed the siding and sheathing. It's a point of coordination that might be tough for you, but I'm glad I did.
While these recommendations don't make for passive house levels of insulation, it's going to take your house from a leaky, uninsulated shell to a reliably air-tight and durable shell. I'm not sure about your community, but I would recommend speaking to your building officials for some local info.
This calculator also helps compare some different wall configurations too:
https://www.appliedbuildingtech.com/fsc/calculator
Don't get too discouraged, you can get to your goals, you just need to find the right crew, make the right material choices, and make sure you think through details. Windows, corners, flashing, trim, etc all become a little different with exterior insulation.
You can do it!
I would not remove the old sheathing unless it is in bad shape. Depending on the thickness it is somewhere between R1.5 to R2 of free insulation.
You can fill the stud cavities from the outside with either dense pack cellulose or fiberglass by cutting a couple of holes in each stud bay.
The rest of your wall should work quite well. In your zone you need a minimum of R7.5 of exterior insulation with 2x4 walls, your R11.25 is well above that.
Awww it was really nice to wake up and find so many helpful people taking the time to assist me. I thank you all very much for your time and for starting my day with a smile! I was advised that the buffalo board should be replaced because it doesnt take a nail very well. And I assume because of its age as well? It's a 1953 home. I've had multiple companies come by to take a look and talk it over. Most of them gave blank stares when I starting bringing up GBA ideals of insulation and airsealing. (We in south dakota do not have offical code I discovered.) And when I asked what they suggested, well... i know just enough from reading articles here that many of you would be shocked at the suggestions given. This is why I needed advice so badly so I could lay out exact points to request of the crew. Thank you again
It would be good to find a contractor that has done exterior insulation.
With a rain screen and exterior insulation the siding is nailed to the rain screen strapping not to the sheathing. The fact that the buffalo board doesn't hold nails (it won't hold nails even when new) is irrelevant.
I would only remove the sheathing if you need to do a lot of wiring.
Trina - No problem, you can sort it out, it just takes some proper planning.
Akos -
My main concern with the removing the buffalo board is for air-sealing. While it does offer up some R-value, air-sealing with that in place has challenges.
I did a few experiments with tapes, sealants, and liquid flashing to test adhesion. STPE products like FastFlash, and liquid flash cured, and had a reasonable bond.
While the exterior foam could be used as an air-barrier, I think it's a less durable, and more difficult solution. Pulling sheathing, adding sealant at top and bottom plates and taping seams is a proven way to get air-sealing done and protected well.
I definitely agree with finding a contractor that is familiar with exterior insulation, it can be wonky.
I would agree, trying to tape fiberboard is very hard.
It would be much better to detail a better house wrap (Intello or Tyvek commercial) as the air barrier.
You can also always nail up a layer of plywood/osb over the fiber board, still less work than striping it.