Swedish platform framing and other non-conventional framing practices

I’m in early stages of planning my new home and I want to build using swedish platform framing priniciples as described in the “new american wall” articles on this site and the lamidesign site.
I’m curious, for anyone who has built with this framing method or other non-conventional framing practices, what additional challenges did you face with respect to plan approval and framing inspection, and how did you overcome them?
Any and all words of wisdom are welcome!
Best,
Steve
GBA Detail Library
A collection of one thousand construction details organized by climate and house part
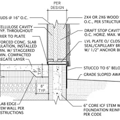
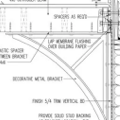
Replies
I've designed a couple of super insulated homes with Swedish platform framing in Ontario, Canada. Here are some comments:
1- Hire a structural engineer, show him the newUSA site from Lamidesign. As it's a variation of standard wood-framing, he had no issues doing the engineering. Standard wood-framing also works well with the plans examiner and inspector. Meet with them early in the design process.
2- Clarify the loads on all drawings and details. On a 2-storey house, we loaded the roof trusses on the main 2x6 walls. We loaded the second floor deck onto the inner 2x4 utility wall, which loads on the first floor deck. The plywood sub-floor on the second floor deck is sandwiched between the first floor and second floor 2x6 wall, tying the system together. We "header wrapped" that sub-floor for air-tightness.
3- On the first project, we used a standard 8" poured concrete wall. It worked but was a bit tight for space, as we loaded the outer 2x6 wall and the 1st/2nd floor on there side by side, a certain amount of bearing surface is required for both. On the second project, we used an ICF foundation and spec'd a 10" form for the top ICF course (rest of the foundation was 8" core). Alternatively, you could use a brick ledge form, in my case, with the brick ledge on the interior (less thermal bridging). The engineer will spec the rebar.
4- We panelized the wall systems. It's not required but the walls were extra thick for super insulation.
Anthony, very helpful, thank you! I am going back and forth on ICF's vs a poured in place foundation with mineral wool board insulation - how did you end up deciding on ICFs? We're building with a walkout basement on a sloping lot. I'm scheduled to meet with an ICF contractor next week to discuss the project.
We're likely looking at site-built walls. While I cant totally get behind the panelization concept (i was a manufacturing engineer for a number of years) our market just isn't set-up for it yet. I do have an excellent framing crew I've worked with in the past and I have total confidence in them, even with raising and placing 2x8 walls. I love watching them - they know all the tricks, and I learn something new every time!