surface bonding cement versus lime treatment on interior face of CMU foundation

I have an 1960’s CMU foundation/walkout basement with brick exterior above grade- climate zone 4. I am deciding what treatment to use on the interior of the above grade CMU walls [under the finishes] and looking for input regarding air barrier:
1. fluid applied vapor permiable liquid applied air barrier like Henry 17MR
2. parge coat like conproco structural skin
3. traditional lime parge [with or without salt?]
i don’t know the long-term durability of #2 — the fiber reinforced cements applied on one side seem like they might be worse for the existing CMU since they are impermeable, though it might be good to do something about the minor cracking of the mortar joints in the CMU.
I am also working though the rest of the assembly. Recently I’ve been looking at foamglas or roxul boards as a substrate for cement board walls or EIFS-type system — haven’t looked at embodied energy of these materials, but i don’t want to make my existing flame-resistant assembly into a something way more flammable.
Any thoughts or experiences would be appreciated.
GBA Detail Library
A collection of one thousand construction details organized by climate and house part
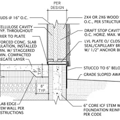
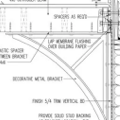
Replies
For treating the interior of above-grade CMU walls in a 1960s foundation with a brick exterior in climate zone 4, your considerations are well-placed, especially concerning air barrier options and the integrity of the CMU. Let's address each of your options:
1. Fluid-Applied Vapor Permeable Air Barrier
Henry 17MR: This type of barrier offers an excellent blend of air sealing and vapor permeability, allowing the wall to breathe while preventing air infiltration. It's a good choice if you're concerned about moisture management within the wall assembly. The long-term durability of fluid-applied barriers is generally high, provided the application is done correctly and the substrate is properly prepared.
2. Parge Coat (Conproco Structural Skin)
Fiber Reinforced Cement: While offering a smooth finish and helping to bridge minor cracks, the concern about impermeability is valid. However, Conproco Structural Skin is designed for compatibility with masonry substrates, providing structural reinforcement and some level of moisture management. If cracking and surface uniformity are significant concerns, this could be a viable option, but understanding its vapor permeability and how it interacts with the rest of your wall assembly is crucial.
3. Traditional Lime Parge
Lime Parge: Lime-based mortars and parges have excellent compatibility with masonry, offering natural vapor permeability and flexibility. Lime can self-heal minor cracks through autogenous healing, making it an excellent option for longevity and maintaining the breathability of the wall. The addition of salt is typically to improve the mix's workability and speed up set time, but it can be corrosive; unless you're dealing with specific conditions that require it, you might avoid adding salt.
Insulation Considerations
Foamglas or Roxul (Rockwool) Boards: Both materials offer non-combustible insulation options, with Foamglas providing an impermeable, durable insulation layer and Roxul offering excellent fire resistance and thermal insulation with some vapor permeability. For an EIFS-type system or cement board walls, either option can work well, depending on your overall goals for thermal performance, moisture management, and fire resistance. The embodied energy and environmental impact of these materials vary, with Roxul generally being considered to have a lower environmental impact due to its recycled content and manufacturing process.
Final Thoughts
When selecting materials and methods for your assembly, consider:
Moisture Management: Ensuring that the assembly can manage moisture effectively to prevent issues with mold or deterioration over time.
Compatibility: Materials should be compatible with each other and the existing structures to avoid long-term issues.
Fire Resistance: Maintaining or improving the fire resistance of the assembly is crucial, especially in retrofit situations.
Given the complexity of your project and the materials involved, consulting with a building science professional or structural engineer can provide tailored advice to ensure your retrofit meets your goals for durability, energy efficiency, and safety.