Suitable high R-value wall for Zone 2?

I’m designing a small house (710 sq ft) in Phoenix AZ (Zone 2) with the eventual end goal of it being net-zero. Most homes around here are built with 2×4 stud walls filled with fiberglass batts or blown cellulose and that’s about it (and all that’s needed for code). I want to take it a couple steps further.
I’ve attached a proposed mockup of a roughly R-32+ wall. Some notes:
1. The “service cavity” may be filled with insulation if it doesn’t cost much more
2. The 2×6 walls will have whatever makes sense money and build-wise, since all three options are roughly the same r-value.
3. Polyiso on the outside to take advantage of its foil-based radiant barrier as much as anything else.
4. Caulk and tape darn near everywhere, to make the 2×6 part air-tight.
Any criticisms or suggestions to improve with this? As in,
Is something outright wrong or missing here?
Is something about this worthless or at least not worth the cost?
Can this be improved by changing one or more small things?
GBA Detail Library
A collection of one thousand construction details organized by climate and house part
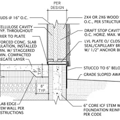
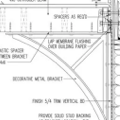
Replies
Kurt,
There's no economic or comfort justification to building an R-32 wall in Climate Zone 2. According to Building Science Corporation, an R-15 wall in your climate zone will perform very, very well -- as long as you pay attention to airtightness.
For more information, see "R-Value Advice from Building Science Corporation."
Very interesting! I do note in the interview with Lstiburek that he mentioned not following those guidelines for his own home, since they were mostly intended for production builders.
If we establish R-15 as the best bang-for-buck baseline and then say R-20 (from Dana's example) is a "known good" amount, then clearly each r-value above that is going to have notably diminishing returns. R-32, at double the most efficient amount, is clearly spending too much.
I do still like the idea of a radiant barrier on the walls (albeit with little to no research backing why that would be a good reason), maybe a 1" layer of foil-backed polyiso might still make sense? Barring that, maybe sheathing with an integrated radiant film?
I suspect that shading, orientation, and glazing will have much larger effects than the wall's thermal barrier. OTOH, one of the issues that we've had in Arizona is heat migrating from the attic into the ceiling, which appears to turn the drywall ceilings into giant radiant panels. So, aside from doing an excellent job of air sealing, you want decent amounts of some sort of attic insulation that is somewhat opaque to radiant heat; I think that's cellulose and not fiberglass.
Also, you should avoid any ductwork or mechanical equipment of any sort in the attic. (You are planning on ductless mini split for a smaller building, yes?) It's a huge energy penalty, and the #&*) pack rats will eventually make their way into your attic; you don't want to have to go up there for any regular service.
Also to consider: termites are a big deal in Arizona. As are Africanized bees. I would be leery of exterior foam insulation and wood cladding as shown in your cross-section.
Wrt Martin's emphasis on airtightness, I would try to use tape or gaskets where possible instead of caulk. Caulk always seems to dry up or pull away, for a variety of reasons.
You are right that most AZ houses are poorly designed and built wrt comfort and energy efficiency. I'm glad that you're thinking about these things now, in the planning stage.
I'm a fan of cellulose for the low environmental impact and cost effectiveness, but in what way is it more opaque to radiant heat than fibreglass? I've never seen this referenced before.
I tend to remember answers, not necessarily all the details that supported the conclusions. And now you want data? :) There was this thread on GBA:
https://www.greenbuildingadvisor.com/question/article-on-fiberglasss-ir-translucency
That's the best reference I have on short notice.
I heard a description of the of that problem (energy from very hot attic penetrating insulation and heating drywall ceiling, and subsequently radiating heat long after sundown), and have experienced it. The air temperature will read okay, but you can't cool down because the ceiling is radiating heat.
Yeah, this house is going to be well shaded and oriented so that most of the windows are on the North. I'm going to air-seal everything to excessive degrees and then the attic gets R50 or more of likely blown cellulose.
And yes, this will have a ductless mini-split. I was flip-flopping for awhile on a ducted mini-split, but it seems like one head unit should be sufficient. No matter what, there was never going to be duct work in an unc0nditioned attic.
For termites, I was going to have the soil treated and then put a metal flashing on the sill as a termite barrier. I saw that in the "Building America Best Practices Series" guide for Hot-Dry climates, put out by the US Dept Energy, so I'm assuming that'll be enough?
I'm not too worried about bees -- I see hives pop up every so often in Mesa, but not a lot where I'm at in Gilbert, so as long as we're making sure that there's not a huge influx of bees all of a sudden, we should be good.
In Phoenix AZ the money you are putting into this wall would buy a lot more watts in solar panels than you will ever save with this wall. The whole point of net zero is to stop buying insulation when you get greater benefit from adding solar.
Given less than 9 inches of rain per year, I think you should skip the rain screen.
I second the idea of keeping the ductwork out of the attic.
Will you have your HVAC equipment on the roof as is the local custom?
Are you planning a swamp cooler and AC or just AC.?
How big a roof overhang are you planning?
Downloading BEopt and modeling your house will help you understand how much insulation will pay off.
Walta
Finding the balance point between spending more on insulation vs spending the same on PV doesn't come naturally to me. I tend to lean towards reducing the number of panels by any means necessary. But I do know that that doesn't make fiscal sense in the end, so it's something I need to work on.
The rain screen is there mostly for non-rain reasons. The first is that it's naturally created by the strapping needed to be able to install cladding over foam. The second is that I wanted to benefit from the radiant barrier properties of the polyiso foil and that requires an air gap.
If I don't end up using foam at all, then I may still want that gap if only for a radiant barrier on the rigid sheathing itself...
AC will be a ductless mini-split.
The house will have substantial shading. The North and West walls are entirely covered with a 10' and 6' covered porch, resp. Half of the South wall is covered with a 6' porch. The other half of the South wall and all the East wall is covered with a 2'-6" overhang (but with other shade structures in play).
Thanks for the BEopt recommendation. I just started playing with that today.
A 2x6/R20 wall can easily hit Net Zero in zone 2B with judicious choices on windows, roof overhangs shading the windows, attic-R and keeping all of the ducts & air handlers indoors.
From a pure lifecycle energy use point of view that's the right range too. Look at row 2 of p10 of this document as a quick crib-sheet reference:
https://buildingscience.com/sites/default/files/migrate/pdf/BA-1005_High%20R-Value_Walls_Case_Study.pdf
Those are "whole assembly" R values. A 2x6/R20 24" o.c. studwall with single top plates beats the recommended R15 whole-wall, as does a 2x6/R23 rock wool 16" o.c. wall, with a bit of care in the framing design about minimizing the framing fraction. A half-inch of foil faced polyiso on a 2x6/R20 wall will pretty much make it at almost any framing fraction, but it's not necessary to hit Net Zero.
+1 on the BeOpt simulation approach to dialing in the design.
Thank you for the real-world numbers -- I saw your comments on another article about 2x6/R20 in Austin being very practical to hit net-zero targets.
The fact that the recommended r-values are "whole assembly" is interesting! This house is going to have quite a few expanses of glass (mostly patio doors) -- up to 46% of the North wall is glass!
Crunching some numbers, I see that the entire building is going to have 932 sq ft of exterior wall space with 201 sq ft of that being either windows or doors. Therefore, 78% of it will be the "wall assembly" numbers and 22% of it will likely average to R-3 at best.
My proposed R-32 assembly would look like: (32 * 0.78) + (3 * 0.22) = R-26
A simple 2x6/R-20 assembly would be at best: (20 * 0.78) + (3 * 0.22) = R-16
So it looks like the simple 2x6 setup would still hit the most-efficient target even with my setup, but just barely. Maybe a solitary inch of polyiso might take the edge off of that.
I just downloaded BEopt this afternoon and started playing with it. I'll see how close I can get to modeling any of this.
>"This house is going to have quite a few expanses of glass (mostly patio doors) -- up to 46% of the North wall is glass!"
That's probably going to be a Net Zero killer. Even north facing glass has solar gain from reflected light, and the heat loss and heating energy use is going to be pretty significant too. Any east or particularly WEST facing "...expanses of glass..." are not easily shaded by roof overhangs, which will increase peak loads and cooling energy use.
No matter how high the wall-R is it hardly matters, when a large fraction of the wall is R3 glazing. You can't fix the glazing gain/loss numbers even with R1000,000 walls.
The Wall Assembly Table 2 R value numbers is just for the wall-R numbers, not the aggregate wall + window numbers. The window U-factor & SHGC limits for windows are specified in a separate column. A "typical" new house has glass area that adds up to about 15% of the floor area (not wall area), but how that glass is distributed on the cardinal directions and shading factors make a huge difference in the amount of net solar gain. In most locations more window area is the opposite of better.
In Phoenix the window size and the SHGC have much higher impact on energy use than U-factor. Solar gain is substantially higher than the average loss at 0F in darkness, which is the temperature and light levels at which U-factors are calculated in the US. Part of the U-factor equation is a function of the absolute temperature (from absolute zero) to the fourth power. The 99% outside design temp for Phoenix is +37F- calculating the window gains/losses as a single R3 number would introduce a very large error.
BeOpt will let you play all the "what if..." games to find the right compromise, but the glazing size, orientation, and SHGC factors will make or break this house's prospects of Net Zero at any wall-R.
Thanks, Dana. I didn't realize that indirect solar can have a measurable impact! But this also exposes that maybe I don't know as much about calculating whole-wall R-value as I thought.
Okay, forgetting SHGC for the moment and assuming R-3 for simple conversion. If I installed my proposed wall assembly with a modified R-value of R-29 since a 2x6 wall has an effective rate of closer to R-17 than to R-20, then:
Wall = (29 * 0.54) = 15.66
Glass = (3 * 0.46) = 1.38
Total Wall R-Value = Wall + Glass = R-17
That seems like it's in net-zero territory right there, even if all the walls were like that and not just the one.
Even if we assume R-0 for the glass (but still an air barrier), I'm seeing an R-15 overall for that wall.
So yeah, that must mean that my understanding is flawed somewhere!
Moving on to the SHGC, having a low SHGC is pretty much a requirement for any glass as I'm shooting for Energy Star levels for all of them (0.28 or better). Trying to figure out the indirect solar gain impact is... iffy. Here's what I tried:
I'm using the calculator at https://susdesign.com/windowheatgain/index.php. With latitude at 33.36N and SHGC at 0.28, I first calculated assuming ground cover of grass at 0.25. I then re-ran the numbers with ground cover at 0. I finished by subtracting the two results to give me just the indirect part of the calculation.
That gave me a maximum of 8 kWh/m2 for the month of June. Given that I have 10.4 m2 of glass on the North wall, that suggests I'll use 83.2 kWh for June.
If that really is the number, then that doesn't seem likely to cause me any issues with reaching net-zero.
But it's surely not that easy, so what am I missing?
Ah, I figured out what I was doing wrong with the whole-wall calculation. The naive approach of adding the r-value times percentages gives a misleadingly high value. The true calculation comes from ASHRAE and it works with the U-Factor rather than the R-Value.
Back to my initial conditions, we have an R-3 for the glass and R-29 for the walls. That's U-0.33 for the glass and U-0.03 for the walls. The entire wall is 46% glass and 54% wall.
Naive Calculation:
Wall = (29 * 0.54) = R-15.66
Glass = (3 * 0.46) = R-1.38
Total R-Value = Wall + Glass = R-17
ASHRAE (Simplified) Calculation:
Wall = ((1/29) * 0.54) = U-0.186
Glass = ((1/3) * 0.46) = U-0.153
Total U-Factor = Wall + Glass = U-0.172
Total R-Value = 1 / U-Factor = 1/0.172 = R-5.8
Oof. From R-17 to R-5.8. And changing the R-value of the wall portion makes very little difference -- even DOUBLING the value still produces R-6.1 overall.
If I run the numbers for the entire house, where windows make up only 19% of the total exterior wall space (the entire East wall has no windows), then I'm looking at R-11 for the house.
I'm not sure if doing an entire house like that makes sense. I've never seen it done for any other house so I can't compare that whole-house R-11 to anything else.
Food for thought, in any event.
The "whole wall" number does not include windows. It's 1/U for the wall-assembly only, not the glass.
Windows are treated separately, but using the labeled U-factor is only valid when it's 0F outside, 70F inside.
But yes, even with better modeling on the windows, when 19% of the total exterior surface is window, the windows will dominate the heat load numbers, but also dominate the heat GAIN numbers, which aren't a function of U-factor, but rather SHGC.
Run BeOpt on it, and be very specific about SHGC and orientation of the windows, not just U-factor.
Hi Kurt -
First, great to see such a solid exchange in all the posts so far on your question(s). I just wanted to weigh in on:
1. Radiant barriers - they make the most sense in attics in hot climates where the delta-T gets extreme. There certainly will be benefit in walls, but nearly as much.
2. BEopt - first thing that came to my mind if you have the inclination and appetite. Really useful to optimize for your particular building.
3. What BEopt will confirm: focus on your ceiling/attic, air tightness, glazing, and shading. And help you know when it is no longer worth reducing loads and move toward PV capacity.
After the BEopt recommendation came up a few times, I resolved to spend some time with it and get as accurate as possible model of what the house might look like. I discovered the Options Manager which allowed me to add fairly precise definitions of what my windows and patio doors will look like in the context of the model (since none of the presets were very close).
So I modeled roughly what I described elsewhere in this thread and then chose middle of the road values for mini-split, u-factor, ventilation, air sealing, etc. With all that, BEopt predicts just over 4,000 kWh/yr for the house with a total yearly energy bill in the $550 territory!
Sweet. BEopt further suggests that a 3 kW solar array (which would trivially nestle on the South roof) could handle essentially 100% of the load. Maybe I'll complete the net-zero package immediately rather than wait a year or two to see how things settle out, since that's a relatively minimal outlay.
What did you end up choosing? I'm in a similar situation, and was wondering what did you do and how's it working for you? Thanks
I ended up building the walls like so (inside-out):
1. 5/8" drywall
2. 2x3 or 2x4 empty service cavity (depending on if plumbing or not)
3. 5/8" OSB
4. 2x6 wall 24" O.C. w/ wet-spray cellulose embedded
5. 2" foil-faced polyiso foam
6. 3/4" rainscreen with plywood "furring" strips
7. Fiber-cement planks
If doing it again, I would do 2x4 service cavity everywhere (that missing inch means having to get specialty electrical boxes and the like) and I would DEFINITELY put the OSB on the outside rather than the inside! The wet-spray cellulose was installed by a pro team because it was cheaper to go that route than literally any DIY option I could have done... and packed cellulose like that is a pretty great insulator.
The attic will eventually be R-50 blown cellulose but I haven't gotten that far, yet, since (even after FOUR YEARS), the house still isn't completed! Given that, I can't give any actual kWh usage since there has not been any.
I will say that the walls as-so plus the radiant barrier sheets on the roof have resulted in a house that stays a good 10-15 degrees cooler than the outside temperature. I have high hopes that a small mini-split will trivially handle the load in there, especially after the R-50 attic.
>"(that missing inch means having to get specialty electrical boxes and the like)"
As long as you have at least 1.5" of cavity depth, you don't need specialty electrical boxes. Use "4 square" (4" square) boxes, which a the commerical standard, and are readily available even at the box stores. Use mud rings to bring the devices up flush with the finished wall surface. Mud rings are available in a variety of thicknesses, and the box stores usually have mud rings in at least the depths you need for common drywall thicknesses. If you need more oddball thicknesses, commercial electrical supply houses will have a much larger selection. You can get mud rings in single and double gang sizes.
With a 1.5" service cavity, you have room for wiring, and you can use standard electrical boxes the way I've described.
Bill
I hear that, but I personally fit the metal boxes in the "specialty" realm. I simply don't have substantial experience dealing with them while I have installed quite a few of the plastic boxes. To date, I've used the metal boxes exclusively as junction boxes in attics and the like. As such, I wouldn't naturally have even considered a 4" square box for in-drywall work without a suggestion to try it.
But there's another aspect to all this. I coincidentally did the rough electrical for the guest house right in the midst of the worst of the pandemic supply shortages. The electrical aisle of HD and Lowes were picked practically clean for months. For my 2x4s walls, I could just pick through what was left and know that it would work. For my 2x3 service cavity "walls", I had to bring my tape measure and measure every single box that might possibly work... and almost none did. Even the metal boxes left tended to be the "deep" boxes. Oh... and I did go with 5/8" drywall and alas, there were NO 5/8" mud rings available at that time.
That's what solidified in my mind the idea that if you have 2x4 walls, then anything at all is going to work in them, even when pickings are scarce. With 2x3 walls, you are at the mercy of what is available because far fewer of the pickings will actually work!
More recently, I came across two limited-space electrical box cases that illustrated both halves of this.
The first was needing to install an outlet in a cabinet with limited space behind the drawer. I thought of what you said in this thread and given that, I chose a metal box with MC cable for the first time... and I really liked it! It was easy (enough) to work with and extremely flexible in how I could use it. I'll definitely consider metal boxes in quite a few more situations going forward as that'll open up my options quite a bit.
But on the flip side, I also needed to install a "media box" to house an embedded outlet + HDMI + other A/V cables all inside the wall. This wall was my 2x3 service cavity... and yeah, it was a reply of what I encountered before. All of the media boxes that I found and liked simply would not fit in that limited space! I ended up finding one (an Arlington unit) that did just-barely fit and it does work -- but it took a long time to find and it's not precisely what I wanted. Had I gone with a 2x4 service cavity, then I simply wouldn't have had to even think about it. All options would have worked, including the ones I really wanted.
Thanks for the update. I have an empty lot to build on but it wouldn't work for what I want now. With all the housing boom, I had to change my plans and move a bit further out of town and get a larger lot so we can still have the views. I currently live in Arizona city. Nice little town.
I was considering using SIPS. They may be over kill for our area and can be expensive. Plus, I now know that you can still have a well insulated house without breaking the bank as long as you are vigilant on how you insulate and keep hot air out by making sure everything is air tight. My plan so far is to have a walls around r- 20+ and attic r-50.
Hopefully you can post pictures and final updates when completed.
If your goal is to truly get to net zero in Missouri and I think most other states your will need to fool the utility into thinking you will use 20% more power than you end up using. As by state law they will not grid connect any solar system that is predicted to produce over 80% of the estimate. So if they get actual meter reading you will never get a 100% system connected. So your only hope is preconstruction when they will guess at your power consumption X number of watt per square foot. There business model does not work if you are not buying any of their product.
Walta