Suggestions to control Thermal Bridging?

Many times the reading that I do on this site begins to make me a bit woozy,so I thought I might type a question to clear my head,ha!
My questions are regarding a 2×4 wood frame wall and a 2×10 cathedral ceiling with asphalt shingles above.,drywall as the inside finish.
I will insulate the walls and the ceiling with either fiberglass batts or blown cellulose.I am opposed to spray foam,as I know these assemblies are basically unusable and unrecyclable in the future.
I don’t intend to use a ton of ridgid foam on the exterior of the house.I am required by code to apply plywood sheathing directly to the framing.
GBA Detail Library
A collection of one thousand construction details organized by climate and house part
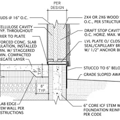
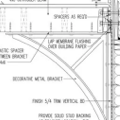
Replies
Dennis,
The most effective location for insulation installed to interrupt thermal bridging is on the exterior side of the wall or roof sheathing.
If you want to avoid rigid foam, you can use mineral wool (at least for walls). More information here:
Installing Roxul Mineral Wool on Exterior Walls
Installing Mineral Wool Insulation Over Exterior Wall Sheathing
Martin,thank you,I greatly appreciate your help.A few follow up questions if you please.
Is there any benefit to installing foam strips on the indoor face of the studs or rafters to help with thermal bridging?Are there risks,when installing foam on the exterior,if the foam thickness is too thin?If I were to install 15# felt on plywood sheathing,would it be a good idea to provide a 1/8" breathing space under the foam as per "Mind the Gap"?
Finally,if I were to put foam above the roof sheathing,of course I need to install additional sheathing for a roof nailing surface.Should I install rafter plywood sheathing,15# felt,rigid foam,2x3 sleepers,plywood sheathing,peal and stick, then roofing,creating a ventilation space?
Dennis,
Q. "Is there any benefit to installing foam strips on the indoor face of the studs or rafters to help with thermal bridging?"
A, Yes, but it's fussy work. Why not just install a continuous layer of interior rigid foam over the entire wall?
Q. "Are there risks, when installing foam on the exterior, if the foam thickness is too thin?"
A. Yes. More information here: Calculating the Minimum Thickness of Rigid Foam Sheathing.
Q. "If I were to install 15# felt on plywood sheathing,would it be a good idea to provide a 1/8" breathing space under the foam as per "Mind the Gap"?"
A. You didn't explain where the rigid foam is in this scenario. If you intend to put rigid foam on the exterior side of your plywood sheathing, you don't need a 1/8 inch gap, as long as the foam is thick enough, and as long as the wall can dry to the interior.
Q. "If I were to put foam above the roof sheathing,of course I need to install additional sheathing for a roof nailing surface."
A. Not necessarily. If you install metal roofing, all you need are purlins installed 24 inches on center.
Q. "Should I install rafter plywood sheathing,15# felt, rigid foam, 2x3 sleepers ,plywood sheathing, peal and stick, then roofing,creating a ventilation space?"
A. You can if you want. I would skip the peel-and-stick if I were you, and use asphalt felt instead.
Rigid stone wool panels are highly vapor permeable and low-wicking- it's sort of it's own "gap" from a drying & draining perspective.
The local climate and the ratio of sheathing-R to cavity R, and the possible drying rates through the sheathing determines whether you might need to make the interior more vapor-tight than standard latex paint. Unlike rigid foam, the drying rates through stone wool is nearly unimpeded, so with back-ventilated siding it can buy you a LOT. Where is this house located?
Putting foam strips on the interior facing of the framing does some good, but the fastener spacings necessary to keep the gypsum flat undoes some of it (the thermal conductivity of steel is more than 100x that of foam insulation). A mere half-inch of foam wouldn't net much, but an inch would. But that would do nothing to thermally break the joist ends & subfloor edges, etc, the way exterior insulation does.
If going with batts for cavity insulation, it's useful to keep the cavity depths at standard lumber dimensions, which would allow you to use high-density "cathedral ceiling" fiberglass or stone wool batts (preferable in my book for a few reasons), otherwise you'd have to look at what compresses reasonably into a non-standard depth. Using 2" of foam on a 2x4 gives it 2x6 dimensions, if you can handle that.
The ventilated nailer deck approach on the roof adds expense but also adds a lot of resilience. But it's better to use either 30# felt or a membrane between the foam and structural deck, as well as 30# felt at the nailer deck. There's little point to using the membrane under the shingles at the nailer deck in a vented stackup, since the nailer dries readily into the vent cavity. But putting it between the foam & structural deck provides both an air & vapor barrier at an appropriate layer, provided you meet an appropriate exterior R/ rafter-bay-R ratio to keep the roof deck from taking on and retaining too much moisture over the winter. When using the vented nailer approach ridge venting is appropriate, as is segmenting the furring with 1' gaps every few feet to allow cross flow ventilation.
Also, unless you use finger-jointed stock, the flatness and straightness of 2x3 furring leaves a lot to be desired. It's usually easier to use 2x4s instead.
(^^Posted before seeing Martin's response.^^)
Thank you both Martin and Dana for taking the time.I'll clarify a couple of things and then follow with a question or two.BTW,this is zone 4B.
The cathedral ceiling/roof in question is a one story structure butting into a 2 story exterior wall.It has a shallow pitch of 3/12,which requires the peel and stick membrane.The cathedral ceiling also contains a flat area of collar ties at the center peak,this area is vented with a gable vent.This is a big advantage over a ridge vent in this case where snow will occasionally pile up between the roof and adjacent wall.I much prefer to go with an unvented rafter cavity,and I would prefer to go with blown-in cellulose.If I go with the unvented cavity,am I then required to go with venting via the plywood/sleepers/airspace/plywood/peel&stick,asphalt assembly?
The other issue is the foam thickness on the walls.I would like to minimize the thickness of the foam to be able to install the doors and windows and flashing conventionally and have the siding meet the vinyl flanged windows correctly.For now the siding is vinyl,that could change.
Am I correct in believing that the exterior foam is sized to keep the wall sheathing warm enough to prevent interior condensation of any moisture within the wall? And that is necessary because the exterior foam,tight to the sheathing,does not allow any permeance of moisture to the outside?If a small gap,as per "Mind the Gap" between the foam and plywood sheathing(about 1/8"),would that then allow permeance to the outside and therefore require less foam on the exterior?
Dennis,
Q. "I much prefer to go with an unvented rafter cavity,and I would prefer to go with blown-in cellulose.If I go with the unvented cavity,am I then required to go with venting via the plywood/sleepers/airspace/plywood/peel&stick,asphalt assembly?"
A. No. Unvented means unvented. Just be sure that your rigid foam is thick enough, as explained in my article, How to Build an Insulated Cathedral Ceiling.
Q. "Am I correct in believing that the exterior foam is sized to keep the wall sheathing warm enough to prevent interior condensation of any moisture within the wall?"
A. Yes. For more information, see Calculating the Minimum Thickness of Rigid Foam Sheathing.
Q. "If a small gap,as per 'Mind the Gap,' between the foam and plywood sheathing (about 1/8 inch), would that then allow permeance to the outside and therefore require less foam on the exterior?"
A. I don't think we have enough experience or data to answer your question, but my gut says no. I think that would be a risky approach. I can't imagine that you'll get enough drying with a 1/8-inch gap to avoid moisture accumulation.
An 1/8" gap can function as a capillary break, but would make a lousy ventilation gap for actually purging moisture.
With vinyl siding (or a vented rainscreen gap) and a semi-permeable foam such as unfaced Type-I or Type-II EPS, (or highly permeable rigid rock wool insulation panels), in a sufficiently warm climate it can dry sufficiently to the exterior even during the winter months to not need an interior vapor retarder even if the exterior R alone wouldn't meet the dew point requirements. Assessing the risk isn't amenable to napkin-math modeling, but a WUFI simulation of the stackup can tell you if it still works even on the shady side of the house. (It's a freebie tool download available from the Oak Ridge National Laboratory website, but isn't dumbed down- you'd have to come up to speed on the building-science stuff to avoid "garbage-in, garbage-out" results. http://www.ornl.gov/sci/ees/etsd/btric/wufi/software.shtml )
In US zone 4B the minimum exterior foam R requirements for walls are not onerous, expensive or thick- it's ZERO. In wetter 4C climates with 2x4 construction, 1/2" of rigid polyiso or XPS would get you to the IRC prescriptive minimum, but an inch would give you significant margin, but with a back ventilated siding, no foam would be required. But even in zone 4B there's an economic & comfort argument for adding at least some exterior foam. Without exterior foam the "whole wall" performance with the thermal bridging factored in is about R9-R9.5 on a vinyl sided house with R12-R13 cavity fill. If you add an inch of iso that becomes R15 or more- cutting the heat loss/gain by more than 30%.
On roofs it takes R15 of exterior foam above the roof deck at IRC 2012 prescriptive total (R49) values in zone 4B, or about 30% of the total center rafter-bay R:
http://publicecodes.cyberregs.com/icod/irc/2012/icod_irc_2012_8_par100.htm
http://publicecodes.cyberregs.com/icod/irc/2012/icod_irc_2012_11_sec002.htm
So, in a 2x10 rafter fully filled with cellulose, or with compressed R38's (or better yet, compressed "cathedral ceiling" R38s) in there and 2.5" of iso or 4" of EPS on top you'd be about there.
Thanks Martin and Dana.Yes the required foam on the exterior walls is manageable,I will probably go with 3/4" and that will more than satisfy the requirement,and I can detail windows and flashings as regular.Most vinyl siding is installed in this are over foam this way.The big deal in my view is the thermal break it provides.
The foam and ventilation assembly on the roof does add quite an expense,but should be quite effective and long lasting.I am sure that these assemblies will become much more common very soon.
Instinctively,I am leaning toward the 1/8" air gap as something I may adopt.Joe Listiburek seems to be pretty enthusiastic about it,and I have removed tons of vinyl siding and foam over the years and have seen a lot of water and moisture driven through vinyl and foam back to housewrap or felt.It makes sense to me that a small gap may go a long way.I might mention that Joe recommends to de-rate the foam R-value by 5% if using a gap.
To take the sting out of the roof foam, snoop around for some reclaimed foam from commercial re-roofing & demolition, which typically runs 25-35% of the cost of virgin stock. Fiber faced roofing iso is typically 2lb density, sometimes 3lb and more rugged/rigid than the 1.5lb density foil faced goods you may be used to seeing, but it's also about R5.5-R5.8/inch rather than R6 or more for the lower density foil-faced stock. The thinnest stuff is usually 2" , and both 3" and 3.25" goods are pretty common, as is 3.5-5" in half-inch increments.
On a friend's deep energy retrofit project I helped out on last year we put 4.5" of iso on the walls, 5.5-7" above the roof deck, but by using predominantly reclaimed goods the material cost was somewhat less than if we'd gone with 2" virgin stock everywhere, savings well north of $10KUSD. The walls were done with a layer of 3.5" reclaimed goods with an outer layer of foil-faced 1" virgin-stock to improve air sealing plus the small performance boost from the low-E aluminum facing the rainscreen gap.
Many commercial roofing companies will stockpile pretty-good used-once material for their own projects, and will sell for a price. In my area there are multiple vendors in reclaimed and cosmetic -blem foam. InsulationDepot.com will ship larger quantities nationwide, but for smaller lots it's not worht it. Local is always better- figure out how much you need and start digging around- it's usually out there.
Dana,lol! Knowing how many dumpsters I have filled with this stuff,it makes me sick right now.I know enough people,I should have a good shot tracking some down.Makes great sense.
I'm not sure if this comment belongs here - it is related to the original issue but concerns a different application context. Moderators please feel free to move.
I have been looking at ways of reducing thermal bridging in an interior space I am converting for a wine cellar.
I will be using 8 cm of dual-sided aluminum faced polyurethane foam panels on the walls and 14 cm on the ceiling. The existing space is a basement room with painted CMU and poured concrete walls.
Because I will install drywall over the foam insulation I will need some method of providing myself with a minimum of 2 cm of a dense substrate for the drywall to be screwed in to. Probably the most typical and relevant construction method I have seen for this kind of a setting (i.e. no existing wood or metal stud framework and a desire for thermal efficiency and to conserve as much interior volume in the space as possible) would be:
1. Glue the foam insulation directly to the concrete walls and seal all joints.
2. Fasten furring strips of 2 cm thickness onto the foam by screwing through the foam and into the concrete substrate.
3. Fasten drywall to the furring strips with screws on 60 cm centres.
The step of fastening furring strips to the concrete substrate opens up the door for thermal bridging and by what I have read this effect is not negligible. Because of the intended use of this space as a wine cellar I'd like to keep thermal bridging as controlled as possible as I need the internal insulated volume to be as well insulated as possible (while also maintaining as much internal space as possible).
In reading around the topic of thermal bridging there are two thoughts that have occurred to me that I've not seen discussion of. I thought I would throw them out here to gather some feedback:
1. Fibreglass has very low thermal conductivity. It is also available in fastener form, as in threaded rod (I've seen diameters starting at 3/8") along with fibreglass nuts. It seems to me fastening furring strips through the insulating foam and into the concrete substrate could be done with fibreglass threaded rod, which could be threaded into traditional anchor fasteners of the appropriate size drilled and set into the concrete. With a 3/8" or 8mm threaded fibreglass rod anchoring the furring strip to the foam and the wall the attachment would be secure and more than able of weight bearing the load of 12.5 mm drywall that would be subsequently screwed to the furring strips. But more importantly, it would seem to me using threaded fibreglass through the insulating foam would greatly diminish thermal bridging. Part of me feels like I must be overlooking something, but I simply have not seen discussion of the use of something like fibreglass fasteners in the context of thermal bridging discussions. Very interested to hear comments on this.
2. The second thing my particular project has got me wondering about is why does a furring strip need to be a strip at all? There seem to be two primary purposes to furring when sandwiching a layer of insulation to an underlying wall - firstly, it helps mechanically fasten the insulation to the wall, and secondly, it provides a sufficiently dense substrate into which further coverings in the wall construction can themselves be attached. To fulfill either role I do not see why one need apply a long strip of wood up the entire length of the wall. If a wall covering such as drywall needs fastening on 60 cm centres, then is there any reason why furring material could not be for example a 6 cm diameter disc of 2 cm thickness (cut for example from plywood)? The 2 cm thickness of plywood would be dimensionally stable and give sufficient purchase for drywall screws, and the "furring disc" could be securely attached to the concrete substrate via fibreglass threaded rod as above.
Using discs instead of strips for furring would obviously require somewhat more work but to my mind would have 2 major advantages: firstly, their reduced surface area would further reduce thermal bridging, and secondly their reduced surface area provides opportunity for further insulation to be applied.
I could actually see exploiting this latter advantage quite neatly by purchasing my insulation in for example 6 and 2 cm thicknesses. I'd first mark out and drill the concrete substrate on 60 cm centres, and install anchors into the wall. In installing the 6 cm foam insulation I would first thread a short length of threaded rod into each anchor hole that would be covered by a given panel and leave these short lengths of rod a few mm proud of the wall. Their purpose would only be to temporarily allow me to transfer a marking of the location of the anchor holes, by positioning the panel onto the wall and then pressing the panel up against the projecting threaded rod segments in order to indent the back face of the panel. I'd then drill out the panel for my 3/8" or 8 mm threaded rod along this line, remove the small segments of threaded rod in the relevant anchor holes, and position the panel and glue in place. Once the 6 cm layer of insulation was installed everywhere I would turn to the 2 cm layer of insulation and do a similar maneuver with longer threaded rod lengths to register and imprint dimple marks on the back of the 2 cm panels at the location of the anchors. I'd then drill out the panels using these marks as a central registering point with a 6 cm hole saw and glue in place a 6 cm plywood disc of 2 cm thickness that was centre drilled and counter sunk so as to be ready to receive the 3/8" threaded rod and nut.
I'd then position each 2 cm foam insulation panel with its inset furring discs, run a bead of glue over the back of the panel and slide the appropriate length of fibreglass threaded rod through the furring disc, both layers of insulation and into the anchor in the concrete wall. Final installation would then be simply tightening the fibreglass nut on the centre of the furring disc which would cinch the 2 cm panel up against the 6 cm panel and leave me with 8 cm of insulation with plywood discs of 2 cm thickness on 60 cm centres. I'd then complete the wall by fastening my 12.5 mm drywall to the furring discs with drywall screws.
Yes, a bit more work, however it does seem to me that this would be getting me a very efficient use of space and doing my best to maintain the insulated value of the space. On top of that, using a hole saw etc. and the repetitive nature of the steps makes me think the actual work involved would not be that bad and could be done quite efficiently.
However both of these ideas (fibreglass fasteners and furring discs as opposed to strips) are not things I have seen discussed before. I'd be very keen to hear of whether there are any obvious flaws in my reasoning here.
Apologies if I am hijacking the discussion that was started with this initial entry. I posted this here because it is primarily about looking for ways to control thermal bridging, albeit for a different context than the original poster.
David,
1. What country do you live in? In the U.S., I don't think that rigid polyurethane foam panels are available. The options here are XPS, EPS, and polyisocyanurate.
2. You are overthinking the problem. The amount of thermal bridging from screws used to hold furring strips is negligible.
3. If you really want to avoid using screws, it is possible to attach the rigid foam to the CMU walls with adhesive, and then to install gypsum drywall to the rigid foam with more adhesive. Just be sure to apply pressure to the panels for at least 24 hours until the adhesive has cured. Use scraps of plywood and long 2x4s or 2x6s, wedged from wall to wall, to apply pressure to the panels while the glue cures.
Thanks Martin,
I live in Switzerland, and rigid polyurethane is definitely available here (the thermal conductivity of these panels is 0.02 W/(m*K).
I appreciate I may be overthinking the problem but I posted a query on another site about constructing the walls as you suggest - i.e. only gluing the foam insulation and then gluing the drywall to the insulation. I was ready to believe this would be an acceptable construction technique - leaving alone for the moment the question of how the ceiling would need to be dealt with. To my surprise I got quite alot of responses, all of which asserted that the adhesive would fail over time and the walls would come tumbling down.
Even if I would be ready to glue the walls I would not rely on the ceiling (14 cm of foam insulation and a 1.25 cm thickness of drywall) holding without mechanical fastening. The ceiling area prior to insulating in the room is 2.5 m x 5 m so we are talking about roughly 11 m2 when the walls come in as I insulate.
I did read here a great deal of back and forth on another discussion about whether the thermal bridging from fasteners is negligible and came away with the sense that it wasn't.
In any event, given that I feel I need to use mechanical fasteners at least for the roof I started thinking through why fasteners are not made from materials that are less thermally conductive, which led me to my ideas about using fibreglass and much smaller surface areas for the furring elements.
I'd still appreciate thoughts and some discussion here about both of these ideas.
Best,
Dave M