Subfloor Options

Eric_U
| Posted in General Questions on
I’m building a house and while I have most of the nitty gritty details planned out in my head, I can’t decide the most cost effective and comfortable detail for the hardwood flooring.
Despite being in Central NY we are doing a barndominium with an above grade slab on grade. There will be about 3″ of gravel on top of the house pad, 4″ of foam on top of that (R16), and a 5″ slab poured on top of that. That seems like enough drainage for the concrete to never have a moisture problem which makes me think I could probably glue hardwoods straight to it and call it a day. However, I’m from SC and every house I’ve ever lived in has a crawlspace so I’m not sure if glueing straight to a slab is ok for longevity or for comfort, the latter being my wife’s biggest concern.
Other options I’ve come across:
DRIcore: $1.89/sqft, it is 3/4 OSB with rubber feet
Single layer of 7/16: $0.61/sqft
Double layer 7/16″: $1.22/sqft
Two layers of 7/16 + STEICO which is a wood fiber underlayment: Same exact price as #1 ($1.89/sqft) but far more material
Single 3/4: $0.93/sqft
Advantech: $1.92/sqft (seems way to expensive to me, though I know this is a popular product)
Sleepers: Don’t know much about this setup. I’m assuming I would just lay down 2x3s ($614 for my entire ground floor) or 2x4s ($769 for entire ground floor) spaced maybe one per linear foot, then a layer of 7/16 on top of that ($0.61/sqft). I think this would be the most comfortable though I’m not sure about the risk of flor squeaking (think it would be ok since 7/16 is rated for 16″oc floor and I would do 12″oc). I would just glue the sleepers to the concrete and then use 1 1/2″ screws to attach the 7/16 to it
I should add that we have 12′ ceilings so floor thickness won’t be a problem. What are you guys’ thoughts?
GBA Detail Library
A collection of one thousand construction details organized by climate and house part
Search and download construction details
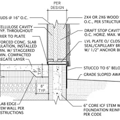
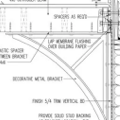
Replies
Some thoughts:
- Be sure to install a vapor barrier under the slab above the foam, you didn't specifically mention that.
- Be sure to let the concrete fully cure (could take a month) before applying anything non-permeable on top (check the glue properties to see if it would act as vapor barrier). The wood should be permeable.
- Check the flooring manufacturers installation instructions - do they require a vapor barrier on top of the slab?
- Wide hardwood (like >=6") cannot just be glued, it almost always requires nails plus glue. This will be difficult to do with slab. Tapcons are an option but the tongue on T&G flooring is too small to get a screw through usually.
- Hardwood directly on top of slab will be hard on your feet. For a softer floor you may want a subfloor. Also given the point above about nailing you may require a subfloor.
If I wanted a subfloor over concrete I would do this assembly:
- an underlayment such as Delta FL with taped seams
- then a layer of 0.75” subfloor using tapcons to attach to slab.
- another layer of 0.75” subfloor oriented perpendicular to the first one with staggered seams using wood screws to attach to first layer
- glue and nail hardwood flooring
If you are doing radiant flooring in this house you can substitute the top subfloor layer with Warmboard S 0.75” subfloor. The sleeper method only makes since if you need insulation on top of the slab (or possibly for sound deadening in a recording studio). Since you are putting insulation under the slab I see no need for raising the floor height up so much.
To your first point, the under-slab insulation I'm using has a built in vapor barrier https://www.amvicsystem.com/products/ampex/
As you can tell by the product radiant pipes are going in, though I'm not going to hook them up. I would never use Warmboard since it is roughly $20/sqft
Wait so it is for radiant heating but the pipes go UNDER the slab? Not even inside the slab? Is the goal to heat the entire earth? Response time will be crazy delayed and extremely inefficient. Quicker response panels are the way to go, if you're using radiant at all.
Correct. I don't think I would be heating the earth with R16 under the tubes though. I agree about response time, however, which is why I'm not hooking it up. Luckily a full radiant system was going to cost so much so I'm more doing it for possible resale value in the future. I bought the PEX early last year before I read enough articles on this website talking about response time, shoulder seasons, etc. I'm just doing a Mitsubishi air to air heat pump with a forced air system now.
AMVIC or Heat sheets are for basement or garage applications. They place 3 inches below the top of slab. Warmboard or equivalent are for above grade.
Glue down install is also not free. It is more work and adhesive costs do add. Also small water leaks can cause big sections to budge and can be expensive to re-lay.
I would go for some sleeper option with subfloor and standard nail down install.
I would make the sleepers at least 2x4 so you can run most of your services under there instead of under the slab. You can go up to 2x6 and put all your drains into the space plus room for some ducting if needed. The benefit of sleepers is that they don't need to be continuous so if the sleeper is in the way of a drain or duct, you can cut right through it.
The subfloor needs to be T&G, so 5/8" min even with tighter spacing.
I hadn't thought about the plumbing going there. I've been putting off pouring my slab for a couple of weeks trying to make sure everything is perfect for my rough-in, even 3D modeling the entire house since I only get one shot. I guess since you are saying 2x4 or 2x6 you're flipping them on their edges? That's a very interesting idea. This would also allow shorter pex runs as I have been planning on going up and over for delivery, making my longest run nearly 60ft. The only "weird" thing would be figuring out my thresholds since I've been planning on having little to none.
Yes on edge. Essentially making a mini floor over the slab. It makes a lot of things easier for not all that much extra cost. You can also save a bit of concrete as if it cracks you will never see it or cause any floor issues.
About the only drawback is the air gap adds a bit of extra R value, so if you do want to heat the floor the slab would have to be a bit hotter. Hotter water is not an issue with any fuel burner, so not a huge drawback.
As for the threshold, since it is a new build, you can compensate at the outside grade at the doors.
Do I need PT wood? I've seen posts elsewhere online saying yes but those usually seem like remodels and basements. Being that I have a vapor barrier and 4" of foam under the concrete do I even need to worry about moisture?
This is not a basement, I would not worry about. If in doubt you can add a strip of gasket sealer or poly under regular lumber.
Deleted