Sub-slab insulation for walkout basement near Boston (zone 5)

Working on building a new home near boston with a 10ft walkout basement. Plan is to tile floor and want to make sure that it’s not freezing cold in the winter.
Walls planned using Demilec HFO Highloft Closed Cell SPF
Debating between XPS, EPS and Closed Cell SPF for below the slab.
Also debating what the appropriate R-Value would be for this. Do you do a basic 2″ R-10-14ish or a thicker 4″ R-20-28ish for this application. I don’t want to waste materials if there’s not a useful impact, but also don’t want to skimp on something that’s pretty much impossible to change once the house is up.
Appreciate your feedback
dave
GBA Detail Library
A collection of one thousand construction details organized by climate and house part
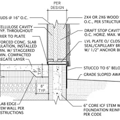
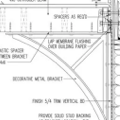
Replies
>"Walls planned using Demilec HFO Highloft Closed Cell SPF"
Why?
That is some of the lousiest bang/buck going, and one of the least-green methods of insulating a framed wall possible, despite using HFO blowing agents. Expensive (financially & environmentally) closed cell foam between framing is a waste. Review the math on just how LITTLE performance is gained:
https://www.finehomebuilding.com/2017/07/10/closed-cell-foam-studs-waste
Dense packed cellulose in the cavities would be cheaper, and only about 1000x greener (it's sequestered carbon, after all).
Save the foam budget for continuous exterior insulating sheathing, where it's performance isn't being robbed by the low-R wood.
>"Debating between XPS, EPS and Closed Cell SPF for below the slab."
XPS is the least green insulation in common use today, and pound for pound, inch for inch eventually falls to the performance of EPS of equal density, as the HFC blowing agents that give it it's first-decade's performance boost dissipates. EPS is blown with a low impact pentane variant, most of which escapes the foam and is recaptured at the manufacturing plant. Not all closed cell spray polyurethane does well under slabs, and it's the most expensive $/R going.
EPS is the winner.
>"Also debating what the appropriate R-Value would be for this. Do you do a basic 2″ R-10-14ish or a thicker 4″ R-20-28ish for this application. "
If it isn't a radiant heating slab, 2" of Type II or Type-IX (or even Type VIII) EPS is enough, and not too much, but if using inexpensive reclaimed Type VIII roofing EPS (there are multiple reclaimers operating in MA) it may still be financially rational to go with 4". See the Zone 5 row of Table 2, p10 of this document:
https://buildingscience.com/sites/default/files/migrate/pdf/BA-1005_High%20R-Value_Walls_Case_Study.pdf
They're calling out R7.5 as the financial sweet spot, but R8.2 EPS is usually cheaper than R7.5 XPS.
@Dana.. for a basement i wanted something that is a vapor and moisture impervious. The HFO doesn't use CFCs in the blowing agent and is green guard gold certified. I haven't heard of anyone using cellulose in basement walls.
I am still debating between straight closed cell above ground vs a 2" flash of closed and fill with open. I did read that article and understand the thermal bridging, but the open cell products don't seem to have green guard gold certification which is important as i have younger kids and want to not have offgassing issues.
I was also seeing things pointing me toward EPS but other than the spray foam guys didn't find much on closed cell below the slab and how it compares with EPS.
>"... for a basement i wanted something that is a vapor and moisture impervious. "
Then none of the above need apply! HFO blown polyurethane isn't any more vapor tight than XPS, nor is it more water impervious than EPS (@ 1.25lbs density or higher.)
Spraying foam directly onto soil or compacted gravel has a somewhat imperfect history. Moisture in the soil can affect the expansion rate/volume, and the temperature of the surface can be quite a bit different from the ambient air temperature, leading to errors in mixture settings, etc. Site applied foam always comes with some risk, but even more so (from a quality point of view) when applied onto soil or stone. By contrast sheet foam is expanded under controlled factory conditions and quality inspected.
Type-II EPS (1.5lbs density) is THE single most common material used in insulating concrete forms, and has a long history in sub-slab (sub-airport runway, sub-roadway) applications. Under a residential slab (not a footing, not a grade-beam) Type-II is arguably overkill for compression/creepage, but some still insist on Type-IX (2lbs density) even under basement slabs (for no reason other than the architect/engineer doesn't have to even think about it, entering the realm of extreme overkill.)
>"The HFO doesn't use CFCs in the blowing agent and is green guard gold certified. "
CFCs have been outlawed for the application since the Montreal Protocol some 30 odd years ago- I'm glad it's not actually contraband! :-)
HFO blown foam also doesn't have HFCs, which is the most commonly used class of blowing agents in the US, and that up until the Kigali Amendment (went into effect 1 January 2019), at least USED to meet the Montreal protocol.
How does Green Guard Certification matter on a product installed on the other side of a concrete air barrier & polyethylene air & vapor barrier from the conditioned space?
>"I am still debating between straight closed cell above ground vs a 2" flash of closed and fill with open. I did read that article and understand the thermal bridging, but the open cell products don't seem to have green guard gold certification which is important as i have younger kids and want to not have offgassing issues."
Open cell foam isn't all that green either. Foam just isn't green period- use less of it, and put it on the exterior side of the assembly where it's properties do the most good. Continuous foil faced polyisocyanurate on the exterior side of a wood sheathed building and using your least-offensive fiber insulation in the cavities is the best bang/buck. (Borate-only cellulose is pretty good: https://healthybuildingscience.com/2013/08/21/blown-in-cellulose-insulation/ )
At the same wall thickness at a 2x6 w/2" cc flash & fill, a 2x4/R13 cellulose wall with 2" of continuous foil faced polyiso on the exterior uses about half the polymer than just the 2" flash (foil faced polyiso is ~1lbs density instead of ~2lbs), thermally outperforms the flash & fill wall by about 30-35%, and puts an impervious aluminum facer between the foam and the conditioned space. And with the sheathing located ~9/22 of the way in from the great-outdoors and it's moisture drives, and being in contact with a wicking, moisture buffering insulation, the structural wood stays warm, dry, and mold free. (A 1.5 " or greater polyiso is also adequate for dew point control on a 2x6/R2o-cellulose wall too.)
For the basement polyiso foam board, possibly reclaimed or seconds, makes way more sense than spf. You can frame right against the foam board. Framing against a spray foam wall makes it challenging not to leave air channels as it is not flat.
If you have any concerns about air quality, spray foam has some non insignificant risks. The foam tested may pass, but the crew at your house will be running a complex highly temperature dependent manufacturing process in likely very different conditions than the lab samples were produced.
In new construction there is really little need for spray foams. Air sealing is easiest, more effective, and way more cost effective when done at the sheathing. Use foam board on the outside.
I personally have spray foam in my house, but this was retrofit work where it made the most sense.
+1 on the industry standard of EPS (plus a polyethylene vapor barrier for the slab). How much makes financial sense depends greatly on how long you intend to stay there.
There is no need for expensive/risky spray foam for new construction. For basement walls, you can use polyiso and tape the seams.
3" Type II EPS boards are probably cheaper than 2" XPS boards and like Dana said- far, far greener.
Planning this as my long term house so appreciate all the feedback. Sounds like 2-3” of eps are the right way to go for subslab
In terms of walls sounds like folks are very much anti spf and exterior rigid foam board. I have had really good experiences with closed cell in my current home but also understand the thermal bridging issues
Would you use the zip r sheeting or a different foam above the zip system. My other question is how this impacts the width for windows doors and trim. I was already planning to do a rainscreen with slicker max below hardie board to give it the ability to dry but not sure how adding inches works in terms of siding, trim and windows.
>"Would you use the zip r sheeting or a different foam above the zip system."
To have sufficient exterior R for dew point control on a 2x6 wall in US climate zone 5 with ZIP-R requires the 2" or 2.5" thick versions, neither of which will meet the structural capacity requirements without using other reinforcements. It's expensive stuff too- more expensive than an exterior foam approach.
I think many here are very pro exterior foam board using EPS or Polyiso. Zip R can work too if you can get enough exterior foam out of it and it works for any shear load requirements you have.
You have to choose where you want your windows and then align your WRB with that choice: https://www.greenbuildingadvisor.com/article/innie-windows-or-outie-windows
You would use vertical strapping as a rain screen in the case of exterior foam.
One more really quick question from my builder. When doing EPS on the slab, do you also run the EPS over the footing which would require the footing to be 2" deeper? Or, do you stop the EPS when you get to the footing and not have that thermal break to have the slab sit directly on the footing? We're digging tomorrow and want to make sure that if we need the foam to run over the footings that they are dug to the appropriate depth. thanks so much for all the feedback
Dave,
We designed our slab/insulation/footing detail exactly as Jon R shared below. You may get some funny looks from contractors but it is fine.
Note that this seemingly minor detail is required to achieve an Energy Star certified home. Consider taking pictures of this section after it is complete should you seek the rating later. I got nearly $6,000 back in Energy Star rebates for my new home!
For EPS suppliers, check out Branch River plastics. They offer borate treated versions too.
Good luck!
Like Figure 2-4 here but bring the polyethylene up a little higher so it can be lapped to the inside of some wall covering and put a strip of foam between the slab edge and the wall.
Thanks for much for all the great feedback on this thread. Really an amazing community. I spoke to branch plastics today and doing 2" of EPS for about half the price we had gotten for closed cell. Really a great solution.
On to the wall assemblies for the rest of the home. I hear loud an clear the feedback on using exterior rigid foam board and dense packing the stud cavities. After speaking some more with my builder and a couple others the downstream impacts on windows, siding and trim are just too much to incorporate in with about 41 windows in the house.
Looking for next best option, one builder recommended using the 1" zip-r board to get a thermal break outside the framing and still do the closed cell in the walls and back of the roof as i'd originally planned. That would let them do normal window and trim work without having to retrain a bunch of subs in skills they have no experience in. Given that the exterior foam board is just too much downstream impact, would changing from zip to zip-r still be a worthwhile half way point?
The 1" ZIP-R isn't much of a thermal break @ R3 on R6.6-ish 2x6 framing, but better than nothing. It is insufficient for dew point control without adding 1" flash of closed cell to the interior side.
With 1" ZIP-R and 1" of closed cell (R9-R10-ish total) there is plenty of dew point margin in climate zone 5 for filling the remaining 4.5" with blown cellulose (~R17) or 1.8lbs blown fiberglass or a compressed R21-R23 fiberglass or rock wool batt (~R19). Despite the much higher center-cavity R, the whole-wall performance difference between filling the full 4.5" fiberglass or cellulose vs. 4.25" of closed cell foam is negligible compared to what is gained with the R3 ZIP. Due to the large difference in thermal conductivity of the framing fraction, even at a 20% framing fraction (24" o.c. framing, single top plates) the framing would be conducting more total heat than the closed cell foam.
The closed cell foam in the cavity is buying next to nothing from a thermal performance perspective, so using more closed cell foam than is necessary for dew point control is pretty much a waste.
I am curious how OC foam fill would compare in this application. Closed cell at one inch is 1.5-1.7 perm depending on the foam. 5.5" of open cell would be 4.5 perm for Demilac's .75 PCF Agribalance or 7.7 perm for .5 PCF foam. Would OC with Membrane be work? I am thinking if there is simpler assembly that works with some Zip R on the exterior.
Thanks Dana! That’s really helpful. Looking at the fasteners and specs the 1.5” is R6 and potentially could work without impacting windows and trim as well. I assume that same rules apply.
So wall assembly would be hardie board, slicker max rainscreen, zip r3 or r6 as possible, 1” hfo closed cell, full with cellulose or blow fiber glass.
This sound like a reasonable plan?
> ... 1” hfo closed cell, full with cellulose or blow fiber glass.
Be conservative - I'd put some type of Class II vapor barrier on the interior side to meet the recommendations here. Even where your rainscreen makes Class III code legal.
Jon
Not sure I follow that totally. I was thinking the 1” flash of closed cell inside the zip R would act as a vapor barrier. Would I need something else and where does that fit in the assembly?
Thanks in advance
Vapor paint on the drywall would work.
One hopefully last question in the sub-slab.
In the basement have a 8” elevator pit for a 3 stop residential elevator.
The elevator is near a lally column so footings will be below the pit.
Do we cut out the insulation and slab 2”+4” and sink the footing 2” to get to the 8” and not have slab or insulation in the pit or drop the footing 8” and deal with the complexity of a separate pour height for a slab on insulation in the pit.
This is near the center of the house so it’s not getting cold from the outside walls so not sure it’s worth the effort and didn’t see much on elevator pits
Thanks in advance
Dave
I have to believe those numbers are in feet ( ' ) not inches ( " ), no?
Subsoil temps in the Boston area are in the low 50s, which represents a constant heat load drawing from the indoor space. An uninsulated slab also becomes damp in the summer when dew points in the basement can rise above that subsoil temperature. The total heat loss from the elevator pit many not be worth considering, but the summertime moisture aspects may still matter if anything going in the pit is susceptible to moisture damage/rust.
Installing the same amount of insulation between the pit walls & floor as what's under the slab to make a continuous, unbroken insulation layer is a good idea. If the floor/slab-let of the pit is structural, supporting the equipment you may have to forego the insulating that, or get an engineering analysis to specify the density & type of insulation, just as you would with any insulation under structural footings.
Just 8 inches. Just a little lower than the slab. Maybe hit the foam on the base but not the 8” walls as it’s pretty tiny