Structural Insulated Panel (SIP) roof decay

I have a BensonWood timber frame in Vt that is only 8 years old with significant panel roof decay. So much so that my standing-seam metal roof has begun to rust from the inside out. There is evidence of SIP seam failure in several places below the standing-seam metal roof. Is it likely this was the cause? It is a hot roof.
GBA Detail Library
A collection of one thousand construction details organized by climate and house part
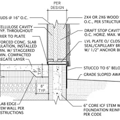
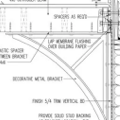
Replies
Gregory,
Have you talked with Tedd Benson or Hans Porschitz at Bensonwood Homes yet?
Here are their e-mail addresses:
Tedd Benson
tedd [at] bensonwood [dot] com
Hans Porschitz
hans [at] bensonwood [dot] com
If you hear back from Tedd or Hans, let us know what they say.
Gregory, when you say it is a "hot roof", is the metal installed directly on top of the SIP without strapping? And when you say there's evidence of SIP seam failure, can you describe this please? I think it's important to be sure where the moisture is coming from: condensation on the bottom side of the metal, or driven through the SIP joints from inside the building.
Hi Martin, Yes Ted and I have spoken. We are still investigating the cause. I will let you know when we have more decisive information. Curious if anyone has had my same experience and what their findings were.
Chris, the metal roof went on top of the sips with triflex between. The moisture is very obvious at the seams an appears to have leaked through from the inside of the home.
Best, Greg
Foam sheets, sips with joint leaks have failed in my area. So far much less of an issue if the roof is vented above the foam. BSC has good info and cautions at their site. Many failures looked at across Alaska.
SIPs need very careful joinery done by knowledgable up to date craftsmen and contractors.
The future of tightly constructed homes may have to move toward training and licensing soon. Wish I didn't have to state that though. Maybe we could do so voluntarily through an existing association like NAHB, or via GBA or BSC. Training certificates...
Moisture in SIP roofs is a problem that is most often a result of poor installation. The problem can be exaggerated by poor HVAC design, stack effect, and improper ventilation of the interior space or the exterior cladding. With all things perfectly installed, an environment that is heavy on wetting and short on drying can lead to similar moisture concerns. The goal of high energy efficiency almost always involves superior air-tightness. It is the very tightness of any energy efficient structure that creates a potential reduction in the rate of drying. And as a famous Canadian scientist is often heard explaining, "you have a moisture problem when the rate of wetting exceeds the rate of drying!" It is this reduced capacity to dry that dictates a roof cladding be back-ventilated. Some would call this a hot roof. However, most people who use this term are from the north and are thinking of ice-damming. If the back-venting is specified correctly in cold, dark, wet environments, it is for the sake of improving the rate of drying. Hence, back-ventilating the cladding on a SIP roof (Or any very energy efficient & tight roof assembly) should be referred to as a "Dry-Roof"
The need for better training and certification of SIP builders and installers has been improving as of late. The most recent certifying program to become available is the SIPA BEST program delivered on-line via Green Builder College. The other training options include the carpenters union and the training offered by yours truly.
The real problem with poor installs won't disappear until SIP manufacturers stop using the term do-it-yourself and stop selling to anyone without regard for their abilities to properly install the SYSTEM.
AL
Gregory,
Here's one report about the Alaskan rotting roofs:
http://www.greenbuildingtalk.com/buildcentral/sip/2001-10_juneau.pdf
Gregory,
Bensonwood Homes is a good company. I trust they will help you get to the bottom of your problem.
I wrote an article for the March 2004 issue of Energy Design Update that is relevant to the topic at hand. I will quote from that article at length:
Hans Porschitz is a building systems associate at Bensonwood Homes, a timber-frame company in Walpole, New Hampshire. Most Bensonwood Homes have SIP roofs. In recent years, Porschitz has been looking for ways to improve the airtightness of the seams of the Insulspan roof panels installed on their homes. “We usually don’t use SIP wall panels, but we use SIPs on the roof,” says Porschitz. “We foam the roof seams according to the standards of the SIP industry, but it just doesn’t work for us, especially when you have a frosty morning. With foam, you can miss a spot. What if it is freezing cold and the crew wants to get home? You’re supposed to keep the foam warm, but at below-zero temperatures, how good a foam joint will that be? We’ve had air leakage — that is why we want to do it better. We want to improve that joint by using a gasket.”
Bensonwood is committed to improving their construction techniques. “We’re getting smarter,” says Porschitz. “We would be stupid to always do things the same way just because that’s the way we always did it. When I came to work at Bensonwood, we decided that we need to start at the joints if we want to improve our houses.”
Porschitz convinced a customer to allow Bensonwood workers to use EPDM gaskets from a Swedish company called Trelleborg to seal the seams between the SIP roof panels on their new home. A Trelleborg gasket consists of two parallel 3/8-inch-diameter hose-type gaskets vulcanized to a strip of polyethylene plastic. These gaskets are available in a variety of widths, ranging from 31⁄2 to 8 inches. “I’m originally from Germany,” says Porschitz. “In Germany, the joints in panelized homes are always filled with rubber gaskets, because they’ve found that foam just doesn’t work in a wooden house.”
Bensonwood hired Bruce Torrey, an air-sealing contractor from East Sandwich, Massachusetts, to compare the airtightness of the gasketed home with a nearly identical home with foam-sealed SIPs. “We tested the two houses with infrared and a blower door,” says Torrey. “We saw what a dramatic difference there was. The seams with gaskets worked and the seams with foam didn’t. People assume that SIPs seams are airtight, but they’re not. You could really see it with the infrared — at the house with foamed seams, you could see infiltration coming in at every joint. When we depressurized the house, you could
feel it with your hand—where the SIP panels sit on top of the rafter on a cathedral ceiling, and where the panels butt each other. It’s easy to blame the foam, but the problem is that the foam is put on by humans. Depending on how careful the guy is with the foam gun, some beads are better than others. The gasket is more foolproof. It is consistent and has good memory.”
Porschitz agrees with Torrey that gaskets perform better than foam. “Foam doesn’t have the flexibility that we need on a wood-framed building,” says Porschitz. “There will always be some movement in the walls with a timber-framed building. The flexibility of the EPDM gaskets is far superior to what you can get with either one-component or two-component foam.”
Porschitz likes the fact that EPDM gaskets can be stapled to a panel in the fabrication shop, reducing the chance of installer error. “We attach the gasket to the panel, and the plastic sheet allows it to slide against the deck or another panel,” he says. “Because of that plastic sheet we can put the panel in place and still scooch it back and forth. Other products curl up when you scooch them.”
... For new home construction, Torrey now seals his window rough openings with gap gaskets, pushing the EPDM into place with a drywall knife. “With most windows, it’s hard to get a foam gun between the window and the rough opening,” he says. “A lot of times the crack is just too small to get a foam gun in there.”
Porschitz agrees that foaming small gaps is particularly problematic. “The general problem with all the liquid sealants, including construction adhesive or foam, is that you can create a tight seal originally, but as soon as the elements move, the seal is less effective,” says Porschitz. “The tighter the gap, the less likely it stays tight, because you have less material to give. If you squeeze foam in a tight gap — say a 1⁄4-inch gap — it will rip up right away. It will crack there. If you install windows, the framing can still move away from the window, so you have the same problem there.” Torrey, like Porschitz, no longer uses foam at small gaps. “If you put down a small bead of one-part foam over a long 1/8-inch crack, and then you go back later to look at it, you’ll see that it just disintegrates,” says Torrey. “It gets brittle, it bubbles apart, and it disintegrates.”
Another gasket material Porschitz has used for SIP seams is Willseal 600, a pre-compressed, self-expanding polyurethane foam gasket from Illbruck Sealant Systems. “It’s an impregnated sealing tape that comes in different widths,” says Porschitz. “It’s a memory gasket. As it gets warm it swells up and seals the joint airtight. Once we installed the product on a very cold day on Squam Lake in New Hampshire. It was so cold that it wouldn’t expand for two weeks. Then we had one warm day and two and a half inches of foam just opened up.”
Porschitz wonders why SIP manufacturers have been slow to embrace the advantages of gaskets. “We heard about all the disasters that happened up in Alaska, and more and more we are using gaskets for our panel seams,” says Porschitz. “But the SIP industry doesn’t seem very open to change. A supplier of the Illbruck product, Willseal 600, told me he tried to talk to the SIP industry to see if they want to work on a better way to seal cracks. Evidently they said, ‘If you do it according to our standards, you will never have problems.’ That was before the Alaska events. The supplier says that still, up to now, they’ve had no inquiries from the SIP industry about their products.”
Thanks Martin, these are interesting comments, some very similar to the same topic discussed this past July. I am very confident we will get through our issue soon as we are working with a good and reputable company. Your comments have been helpful to me and I will keep you posted as to the outcome.
Gregory,
Good luck. You've got the right attitude. If you work cooperatively with Bensonwood, I'm sure that a solution can be reached. Everyone at the company wants to do good work and satisfy their customers.
Window rough openings
Since the first home I built back in the eighties, I too found that the standard 1/2" allowed for space to insulate was too small too often. My solution since then has been to redo the RO larger. I also set Windows raised up off the RO bottom so that we can insulation and air seal below the window.
So basically IMO all builders should be doing this and actually all window and door manufacturers should adopt a new RO standard that is larger than 1/2" or ship windows with all that is required to air seal and insulate their products to a level that will meet forthcoming codes of air tightness.
I just (last week) finished a SIP roof install. Insulspan required "seam tape"- peel-n-stick type bituminous membrane applied to the inside of all seams. I've been seeing this detail for at least 8 years now.
In our particular installation, the seams had 2X8 in them- not foam. The lumber gets glued with a special foam-friendly adhesive. The top of the SIP gets a type of roof tar applied over the joints.
So current Insulspan installations require three levels of moisture protection at the seams. My understanding is that this is in response to past failures, and that many of the failures were due to poor installation. So this appears to be an effort on the SIP mfr's part to apply belt and suspenders to tight-fitting trousers.
Chris Koehn
TimberGuides Design & Build
Thanks Al, Martin, Chris, AJ, and all the other kind responses. This all makes sense and is well documented. What is surprising and frustrating to me is that it is not mandatory or "policy" to create a vented roof when utilizing SIPS, especially from the timber frame company. I am aware that Davis Frames in NH mandates vented "cold roofs'' with their custom frames. Although the approach of installation and seam sealing has improved with the use of memory gaskets and various sealing tapes, a vented roof system allows for an insurance policy or sorts. To expect a SIP installation to be 100% tight over its life span seems unrealistic and naive, as we all know wood is inherently moving. Even with the use of memory gaskets and improved installation practices, the construction of a vented roof would allow for any small leaks at the seams to self exhaust before resulting in a problem such as roof rust, OSB rot, etc. The simplicity of strapping and venting a roof is a very small economic undertaking and makes complete sense for the extended well being of the home. My situation has become clear that it was a result of sip seam failure. Moving ahead properly and proactively will require repairs to the SIPS, seams, and constructing a newly vented roof. Fortunately, my metal roof rusted from the inside out to alert me of a problem. I cannot imagine if I had an asphalt or cedar roof and there were no signs of a problem until a real disaster manifested itself from the inside of the home. Luckily, my sips do not have to be removed from my home. However, this presents an added challenge for my repair as I can only access the compromised seams from the tops of the SIPS. My concern at this time is whether or not I should utilize new foam once I expose the compromised joints and ice and snow on top of the repaired seams.....or repair the seams without ice and snow, install 15lb felt, and strap the roof. The thinking here would be to allow the likely potential for air flow through the previously compromised seams an avenue to escape and exhaust rather than fester mid-panel and further degrade the SIP? Perhaps I would utilize the ice and snow only at the point where the strapping crosses the SIP seams? I have to be realistic in my approach and repair. In summation, I think it is asking too much of a SIP installation without the combination of a vented roof or better yet "a dry roof" as Al Cobb refers to earlier in this discussion. The very small expense to vent a roof from eave to ridge cannot be an excuse to what may very well save your home.
Hello all,
I live in Ohio and also own a timberframe home that has a hybrid of roof SIPs and stick built roof construction. Our home is only 12 years old. I am in the process of researching the problems which have led to the rusting of the back side of our galvanized standing seam roof. At this time, I have two locations where I have noticed pinholes in the the metal: 1) at the ridge of our one of our SIP roofs and 2) at valleys where the stick built roof joins to the panels. Based on the information in this thread and my own speculation, these are highly likely to be areas where heat is escaping and perhaps what caused the metal to prematurely fail. We have determined that we are going to have to replace our current metal roof (constructed of zinc galvanized panels) with factory painted galvalum panels.
Like Gregory, my instincts tell me that when we replace the roof with a new metal roof we should vent the new metal roof using strapping (furring strips) or other similar mechanism. Also, based on the information above, it appears that we should try to do everything we can to seal up cracks that have developed over the years between SIPs. At this time, I also do not know if we have any rotted SIPs, but I have not noticed any squishy areas on the roof when I walk it and I have been up there more than I would like. Obviously we will know for sure once we open up the metal panels and see what we've got.
Since this thread was started 2 1/2 years go, has there been any new information to back up this method of strapping the roof to vent it?
Gregory, did you end up strapping your roof deck?
Your help is most appreciated.
Jason,
In your case, I think that installing the metal roofing on furring strips is a good idea. Needless to say, if an inspection shows that your SIPs are rotting, you may be in for further work.
Come on; this is not an assembly/install problem, it’s a design and original materials selection problem. Cold roof design is always necessary with steel and who in this day and age would use spray foam and complex gaskets to seal the inside SIP seams, blocking and top plate joints when ProClima tapes and polyether caulks are abundant. Sounds like a poorly though out design. It’s not airtight to begin with. So lift the lid, strap the top side of the SIPs (spaced for roof plane, deck top air flow), reinstall the panels, use fiberglass filters as insect mesh on the panel ends (not manufacturer supplied foam strips), let the moisture dry to the outside. Ventilate the interior in the cold months.
Flitch,
Can you quantify your statement that a ,"cold roof design is always necessary with steel..."? I don't see how the roof finishing material plays a role; whether one uses steel, asphalt or tile.
If the bottom/interior side of the SIP roof is properly air sealed and if one properly installs a peel & stick membrane on the SIP roof and then install a metal roof on top, I don't see why one would have any issues and necessitate a "cold roof" design.
The studies show that moisture coming from the interior and air leaks on the interior side is what causes SIP roof rot problems. The panel joints are the "weak link" in the assembly. If one uses a T&G SIP panel, caulks and then tapes the bottom side of the SIP, I don't see how this triple layer of protection would ever cause problems and require a cold roof design?
On a similar note: Have the SIP company install the roof. Don't let a roofing company with little to no SIP roof installs do the work. Have the SIP company do it.
Leaking joints have been a problem with SIPS for years, which is why most manufacturers clearly recommend a vented air space above the panels in their installation manuals. Most timber frame companies do not include the vented air space for cost reasons, leading to leaky panels and rotting OSB. Sealing SIPS with foam works short term but does not last, so I'm glad to see that rubber gaskets are finally being discussed as a better way to seal the joints. Rubber gaskets or not, venting should be a requirement for all SIPS roofs.
If you are re-doing an older SIPS roof, it's a good time to tape the SIPS joints, add one or two layers of polyiso, venting, and another layer of sheathing.
I built timber frames in the 70's and 80's and like most other framers we did not vent the roofs, as we understood it was not necessary, It was, however, shown in the installation manuals. Since then I have repaired several SIPs roofs where the OSB has rotted, and every manufacturer I've spoken to (major in terms of the New England market at least) said they recommended the practice in their manuals. No manufacturer that I'm aware of ever mandated the practice. I agree that your suggested method of caulk, gaskets interior and exterior tape would probably solve the problem, but interior taping is difficult at best when the joints are above timbers..
I want to further elaborate on my previous comments. The "SIP Rot" study and subsequent studies as those done by Dr. Lstiburek clearly show that the issues with SIP roofs is due to the interior air leakage. Hands down, 99% of all SIP rot roof issues is due to the SIPs not being properly air sealed from within and the air leaking through the joints and hitting the cold exterior sheathing/air and condensing. This process continues and over time (years) and you eventually end up with the SIP roof rot issue.
In his study Dr. Lstiburek's remedy is to properly air seal the SIP joints. Attacking the problem from within as that is the source of the problem. Joe goes on to also recommend a "cold roof" above the SIP. He calls for this as an added protection against poor in-field craftsmanship. It's the "backup" in case the installers don't seal the SIP joints properly on the inside. The cold roof allows the potential moisture to dry out and to curb the SIP rot. On a residential build that is being closely supervised and when one is applying the triple layer approach of:
T&G SIP Joints
Gaskets & Sealants at every joint
Taping of Joints
With the above being done properly, one should not ever have to worry about air leakage and the subsequent rot issues. I believe one can by-pass the cold roof if and ONLY if they are 100% positive that the above three protection layers are completed. On an unsupervised build or a large commercial project, then yes, I would utilize a cold roof as an added layer of protection against quality control defects in the interior air leakage practices.
Bob,
It is NOT true that, "most manufacturers clearly recommend a vented air space above the panels in their installation manuals" as all the major SIP manufacturers don't mandate it or even recommend it. "Cold roofs" are not the norm for SIP roofs.
QUOTE FROM JUNEAU STUDY:
"Manufacturers are generally against the application of cold roofs. Mike Tobin (AFM/RControl) believes that specifying a cold-roof as part of a SIP roof design may give the builder a false sense of security—a notion that flaws such as air gaps in the roof installation will be okay as long as there is a means for any moisture entering the panels from below to escape above. "
If one had to add one or two layers of polyiso, build a cold roof and vent it, and finally add another layer of sheathing, the costs would be outrageous and it would make no sense to do a SIP roof. If venting was a mandatory practice then SIPA would mandate it and the SIP manufacturers would require it on all their installs and especially if they are offering a warranty.
The problem as noted by the studies clearly shows that moisture in the SIP is NOT due to external reasons. It is all internal and goes back to the joints not being airtight and condensation forming during the right circumstances but all from the interior, not the exterior. If one uses tongue & grove SIPS, utilizes a high-tech caulk and gasket, and finally seals the panel joints with high-quality tape, you will not have any problems. This makes a solid belt & suspender approach.
Peter
Metal roofs always condense on the underside so there is an inherent moisture issue/drainage issue on any surface where metal is not separated by an (evaporating) airspace and a bulk water drainage barrier. In the case of the SIP panel, flushing the steel to the deck will almost completely eliminate an escape of the interior (stack effect) moisture laden air, thus preventing drying to the outside/causing pooling. The other roofing materials you mention are less of a problem this way, although the oft used plastic peel and stick bulk water barriers on any deck/assembly will cause the same failure.
Flitch,
I am somewhat confused by what you stated. You stated, "Peter Metal roofs always condense on the underside so there is an inherent moisture issue/drainage issue on any surface where metal is not separated by an (evaporating) airspace and a bulk water drainage barrier."
How would a metal roof condense on the underside of a roof SIP? Condensation on the outside is caused by warm interior air leakage hitting the cold exterior air. This doesn't happen with a properly sealed SIP.
You then stated, " In the case of the SIP panel, flushing the steel to the deck will almost completely eliminate an escape of the interior (stack effect) moisture laden air, thus preventing drying to the outside/causing pooling."
Why and how is there interior moisture laden air escaping through an interior sealed SIP? Besides the joints, how would vapor pass through 12" of polystyrene or 8" of polyurethane since that would be considered vapor impermeable? I cannot see how moisture laden interior air is escaping through 8" of polyurethane and condensing on on the cold roof.
You stated, "although the oft used plastic peel and stick bulk water barriers on any deck/assembly will cause the same failure." Peel and stick membranes are used on non-SIP roofs all the time and there have been no problems. Once again on a 8" SIP with a polyurethane core that is vapor impermeable, how does interior vapor lade air pass through all that and condense on the metal roof or the peel & stick membrane?
Peter
The thread is not about metal roofs per se, its about improperly sealed SIP joints (and probably about a fault with exhausting moist air as well). Steel will condense on the underside whether the SIPs are properly sealed or not. The condensation will exacerbate the SIP problem described in the above (due to improper sealing you are emphasizing), but even if the SIPs are installed correctly, the steel will still condense. If it has a drain and evaporation plane/space (on purlins for example), drying will occur under the steel. If the steel panels are flat and flush mounted to the deck they will hold condensation in place by capillary action and be slow to dry, so when the sun heats the roof, the vapor drive will push the moisture into the SIP panel faces (passing through any semipermeable bulk water barrier). But in this thread, if the SIPs themselves are poorly installed but a cold roof assembly was used, the interior moist air would have a chance to reach the outside and been able to dry-off to the atmosphere; probably not causing the SIPs to rot.
What about using the zip wall sheathing over the Sip panels and staggering the joins? Or would this make it way too costly?
I'm trying to figure out what the ideal is for building near Winnipeg Canada. I can build the timber frame myself but am not sure on wall type and insulation especially after reading this.
Scott,
I'm not sure if you are talking about walls or roofs. If you are thinking of installing Zip wall sheathing on the exterior side of SIPs, you could only do that on walls. (There is a different type of Zip sheathing for roofs.)
In either case, that would be an expensive way to air-seal the SIP seams. It would be less expensive (and just as effective) to seal the seams with high-quality tape.
Scott,
As Martin stated, just use a high quality tape like SIGA. Martin did some backyard testing on tapes and the SIGA tapes are top notch. They don't use any VOC's in the tapes and the tapes allow for proper air sealing and movement for the life of the structure.
There are usually SIGA reps/dealers in all the major regions. Where are you located at?