Metal Roof and Wall Cladding in Hot-Dry Climate

zox20
| Posted in Green Building Techniques on
I will be building a 2-story house north of Tucson Arizona at 4100′ elevation, zone 2. The building pad is on top of a treeless hill, so there is no shade for the occasional 105 degree summer day. It will have a hip roof, using 3/12 trusses, with 2×6 top chords. Outside the trusses will be 5/8″ Zip panels, 1″ polyiso, foil out, seams taped, and finally PVDF almond colored (cool roof, SRI 85) 24 gauge 7/8″ corrugated metal panels with exposed fasteners.
The attic will be unvented with 6″ of open cell spray foam on the bottom side of the roof sheathing and inside of the gable ends. There will not be any roof penetrations. There will be venting at the ridge and eaves for airflow between the polyiso and corrugated metal panels.
The walls will be constructed of 2x6s at 16″ o.c. Outside the framing will be 5/8″ Zip panels, 1″ XPS with seams taped, and clad with 24 gauge 7/8″ corrugated metal panels. The interior cavities of the framed walls will be filled with open cell spray foam.
Because heat is the primary concern when insulating and cladding in this location, are there any deficiencies in this design?
Relative to the walls, will fastening thru XPS into 5/8″ Zip panels be sufficient to hold up the 20′ metal wall panels? I will consult an engineer and the panel manufacturer. Just thinking, I may need to run several courses of 1″ thick horizontal furring strips fastened directly to the Zip panels and studs, omitting the thermal break at these locations.
Relative to the roof, would it be worth applying 1×4 furring strips at 45 degrees from horizontal between the polyiso and roof panels to provide additional air flow?
GBA Detail Library
A collection of one thousand construction details organized by climate and house part
Search and download construction details
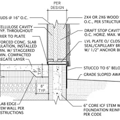
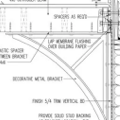
Replies
You mentioned, "There will not be any roof penetrations." Better check with code because the plumbing vent stack needs to vent at highest point of building.
I'd like to run the stack horizontally thru the gable end, then turn vertically to end above the ridge. That is on my list of questions for the building department.
One thought, the horizontal portion of the vent would likely give rain a path to run back to the sheathing? It would probably need some really thorough flashing.
The thru fastened roof panels thru the foam seem like a problem to me. Do you have a mfg detail showing that is allowed?
Will you be installing more than 1" of insulation? If you insulate the ceiling plane then the 1" is not needed on the roof.
I will be using 1" polyiso boards between the Zip sheathing and metal panels. The bottom side of the Zip sheathing will be sprayed with open cell foam. My main concern is stopping heat transfer into the conditioned attic in the summer.
The exterior rigid foam on your walls creates a thermal break regardless of whether or not you create what is effectively a rain screen by installing furring strips. Corrugated metal panels act like a rain screen themselves. In any case I would install them by screwing through the foam directly into the framing. You'll need to source screws which carry the weight of the panels. Furring strips don't alter that requirement.
As for your roof it seems confusing. Insulated roofs are built in this order Roof Framing -.> sheathing - > rigid foam -> (furring strips, optional or manufacturer requires) -> more sheathing + underlayment (if required by manufacturer) -> roofing material (asphalt shingles, metal, etc).
Long run of metal on a roof can flex in the heat (aka oil canning). Warranty on some roofing choices might require venting. This is why a vent channel using furring strips is created between the foam and the sheathing above it.
Potential issue is the thickness of the rigid foam on the exterior side of your roof sheathing. I don't know if 1 inch will keep the sheathing warm enough during the winter to prevent moisture from condensing out on the interior side of the sheathing in the winter.
John, my thought on the furring strips on the walls was strictly to support the metal panels. The furring strips would be attached directly to the Zip sheathing and they would be the same thickness as the XPS boards. I'll definitely consult the metal panel manufacturer about supporting the panels thru XPS. Also, I planned on the corrugated panels meeting any rain screen requirements.
As for the roof, the metal panels will be approximately 16' long. I'm not opposed to using furring strips between the polyiso and metal. I've seen examples of no sheathing between the foam and metal panels, so if I stick with 5/8" Zip, 1" of polyiso, 1x furring strips on the polyiso, and finally 24 gauge corrugated metal, wouldn't that be more than sufficient to provide a structurally sound roof?
As for the condensation at the roof, code requires R38 for zone 2. I don't think open cell alone will work. If I go with 2-3" of closed cell sprayed on the bottom side of Zip, then 6" of open cell sprayed on the closed cell and encapsulating the top chords of the roof trusses, then I shouldn't have any problems with condensation on the bottom of Zip, especially in Tucson's environment. Don't forget the 1" of polyiso outside of Zip when meeting R-38. Do you think this will work? Thanks.
At what panel length does oil canning become an issue? Of course this will vary with the panel design and gauge, but I'm interested in experience with this.
You would have to try extremely hard to oil can corrugated. This is normally a problem with standing seam roof panels without striations.
The problem with any corrugated is the exposed fasteners. The reason you don't want long lengths is that as the panels expands, you are bending the fasteners. This eventually works them loose either from the wood bellow or ovals the hole in the panel causing water leaks. There are guides out there for max length based on local climate. You can also mount them onto Z furring which allows for expansion without putting load on the fasteners.
A much better option is to go with snaplock panels. Here the fasteners are covered and they have slots to allow for expansion. Corrugated is fine for siding, but I wouldn't put it on the roof.