Standing-seam roof, closed-cell spray foam, self-adhered membrane: Double vapor barrier?

Hi,
First Post.
I am designing/building (my profession) a 1378 sf 2-story house (no garage) in St. Helen CA.; which is California Climate Zone 2 or IECC Zone 3-c.
The average January temperature is 48 degrees F and average July temp of 68 degrees F. The extreme conditions from Manual J are 31 degrees F and 97 degrees F respectively. Average Rainfall of ca. 40″ from Oct to Feb. Average Relative Humidity 80% January and 55% July.
I plan to build a simple 4:12 Hip roof with cantilever trusses at 24″ o.c. over a conditioned attic space that does not contain any mechanical equipment. I will be using 6 of closed cell spray between the top cords of the trusses and will provide 12″ of clearance from the top chord to the top plate which will be solid blocked and allow the foam to tie-in the top plate. On the roof deck I will be using 3/4″ cdx, some sort of synthetic underlayment, and a standing seam metal (cool) roof. The roof will be unvented. The framing will be done in the hot summer, the moisture content of the plywood and trusses will be well below 15% at the time they are “dried” in.
In looking for help with the underlayment I turned to Hot Dry & Mixed Dry Climates by Joseph Lstiburek pg. 163 which is somewhat similar to my plan except for no knee walls and the space will be unoccupied. Why is he specifically calling-out fully self-adhered underlayment for the entire surface? This clearly produces an assembly that will have extremely low permeance on both sides. I like the minimal risk the roof could get wet from wind-driven rain but I don’t understand why I couldn’t use the self-adhered on the hips, ridge, etc then use a high-temp mechanically fastened synthetic on the rest of the roof. The ATASĀ spec sheets for both products state.1 perm for the self-adhered and .05 for the mechanically fastened.
I will be using an ERV coupled to my Carrier Greenspeed Furnace & Air Handler. My total heating load will be about 15k BTU and cooling load of 1 ton.
Any consideration to my confusion would be greatly appreciated.
Cheers
Michael
GBA Detail Library
A collection of one thousand construction details organized by climate and house part
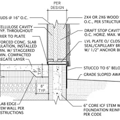
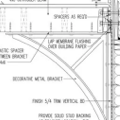
Replies
Michael,
I have no idea why Joe Lstiburek is advocating the use of self-adhered membrane. To me, it seems unnecessary.
Before you select a synthetic roofing underlayment, check with the underlayment manufacturer to determine installation limitations. Most manufacturers of synthetic underlayment forbid the use of their products on unvented roofs.
Hi Martin,
Thank you for your reply. Dead if I do - Dead if I don't? Several manufacturer's of mechanically attached synthetic high heat vapor barrier underlayments say exactly that. I have attached an example. The data sheet does say follow local building codes which permit unvented roof assemblies.
Of course no manufacturer wants to rubber-stamp an assembly over which they have no control.
I want to use a high heat underlayment not a felt paper. Local metal roof suppliers have strongly recommended I don't use 15 lb or 30 lb felt paper.
Dr. Lstiburek's book was written in 1998, I have the 2004 edition, and purchased the book in 2018 from their site. Has this issue been discussed or tested in the Building Science Community? Basically any unvented roof assembly with ccSPF and an effective roof system will be a vapor barrier sandwich.
I think I have controlled the interior relative humidity in my construction detailing, mechanical system design, and product selection. I see the risk to the roof structure from the outside in terms of bulk water entry ( our last storm reminded many builders that water can go up-hill) and intense solar radiation.
I still don't get it.
Michael
I can only guess, but self adhered will have better air sealing and no fasteners to possibly leak. Generically, perms should be an independent issue from "self-adhered".
Jon,
You are right, but until recently self-adhered membrane was synonymous on drawings and in specs with a fully waterproof, zero-perm product such as would be used on roofs. I don't see any indication Joe L. intend the subtle distinction you are making.
Michael,
I think the recommendation for self adhered comes from low slope standing seam installs. Simple insurance against leaks. 1/3 of my roof has this and no problems so far.
I'm not sure why everybody so down of felt, I pulled up a section of at least 40 year shingled old roof and the felt was still there, brittle but intact.
Akos,
I don't know how prevalent the problem actually is, but the worry with felt under metal roofing is that it can get hot enough to adhere to the panels and may tear. Many metal roof manufacturers insist on synthetic underlayment.
If I have the choice I would always use synthetic underlayments. Working on the roof is a lot safer, and it is much harder to tear than felt.
There are permeable fully adhered membranes out there that are suitable (eg Blueskin VP100).
Insulating with 6" of closed cell foam is the opposite of "green". If it's blown with HFCs it's VERY ungreen, but even with HFO blown foam the high polymer/R has real environmental costs.
In zone 3 it only takes 1" of closed cell foam (R6-R7) on the underside of the roof deck to provide dew point control on more than R35 of air or vapor permeable foam. Open cell foam uses less than half the polymer per R of closed cell foam, and is blown with very low impact H2O (water), not HFC or HFO blowing agents. To hit the code-min R38 it could be 1" of closed cell foam and 8" of open cell foam, 9" total depth, using the same amount of polymer of only 3" of closed cell (literally half the environmental impact). The net vapor permeance of that stackup is a bit less than 1 perm (compared to less than 0.2 perms for 6" of closed cell), which is an adequate drying path for the roof deck. A inch of closed cell and 7.5" of 1.8lb damp-sprayed fiberglass (JM Spider) would deliver the same performance and would use even less polymer.
Using and inch of polyiso above the roof deck and open cell or sprayed fiberglass below would also work.
The smallest GreenSpeed is 2 tons, which makes the system oversized. The Greenspeed can only dial down to 40% of it's max capacity, so even at minimum modulation the 2 ton is oversized.
At those loads a 1.5 ton Fujitsu 18RLFCD heat pump has a much larger modulation range (can throttle down to 3100 BTU/hr when loads are very low), and will deliver higher efficiency & comfort than the Carrier Greenspeed systems. It still has significant margin for those extra-hot and extra-cool days.
http://portal.fujitsugeneral.com/files/catalog/files/18RLFCD1.pdf
Regarding Joe L. specifying fully adhered roof underlayment, see BSC article BSI 092, top of page 2. Although this is a different application than Michael's, the article mentions mechanically fastened underlayment "fluttering" due to air pressure differentials and recommends fully adhered to correct this. This brings to mind two of the main advantages of fully adhered in ALL applications. One is that if there is a leak thru fully adhered underlayment, water intrusion into the sheathing is localized and limited, whereas with mechanically attached underlayment intruding water can run behind the underlayment over great distances and in greater volume. Second, fully adhered underlayment eliminates the hundreds of penetrations by fasteners to initially attach mechanically fastened underlayment (of course, subsequent roofing or siding fasteners will penetrate either type of underlayment).