Square timber cabin “efficiency update”

Have a square face (6″x6″) existing chinked square timber cabin. (Much to my surprise, it had T-111 over it). Climate zone 7, dry, cold, high rocky mountains (7000ft). My original plan was to insulate/rainscreen over the exterior face, but upon peeling back the T-111 and discovering it was “solid” I am considering alternatives. … it has a nice appeal. But, energy efficiency is a STRONG consideration. Any ideas on how to preserve the “look” on the outside and maintain a durable, efficient assembly? I am very well aware of the negative repercussions of all inboard insulation (Cold sheathing, condensation, etc.)
My initial thought: Figure out some way to insulate inboard, but backvent the timbers. (New airsealed SIP or insulated Stud frame walls inside with vent space between SIP and timber?)
Essentially, the timbers would become a VERY thick rainscreen-type siding assembly.
Budget is a concern…
Input?
GBA Detail Library
A collection of one thousand construction details organized by climate and house part
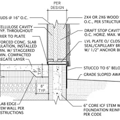
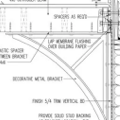
Replies
Erik,
I suppose it would be possible to do as you suggest. But it would be hard to detail well, and you would have tricky transitions where the wall insulation meets the ceiling insulation. And of course you would end up losing a lot of interior space. If I were you, I would photograph the cabin from the exterior, so you remember what it looked like, and then cover it with exterior insulation.
Post some photos Erik.
Air sealing that type construction is nearly impossible without resorting to an air-barrier layer that is somewhat loosely coupled to (or flexible and compliant with) the timbers. No matter how well you chink them, the seasonal expansion/contraction of the heavy timbers opens it all up again.
Heavy timbers at 6" thickness have a substantial amount of thermal mass as well as about R-7-ish R value. Insulating on the exterior with an air-tight rigid foam (or spray foam) would preserve the energy use benefits of that mass by keeping it mostly to the interior of the total R, whereas insulating on the interior would isolate the conditioned space from the thermal mass, all but eliminating the benefit.
From a dew-point control point of view it's worth putting about R12 of rigid or sprayed foam (2" of foil faced polyiso, or 2" of closed cell spray foam) on the exterior in that climate, otherwise insulating on the exterior could leave the cold side of the timbers at risk of accumulating too much wintertime moisture from the inevitable air-leaks and high permeability of the chinking to the interior air. If you're heating the place with propane, R18 in foam wouldn't be insane, from a longer term financial point of view.