Spray foam insulation and barrier?

Getting ready to start construction on new home. Slightly over 1300 sq ft. We live in Oklahoma, Zone 3A. 2 x 6 exterior walls with OSB sheathing and 3/4″ wood siding. Cathedral ceiling with 12/12 pitch, 2 x 12 rafters on 24″ center. 24 ga galvalume roof, wood frame/high efficiency windows. Trying to make sense of the spray foam vs high density batting for ceiling and the best method for 2 x 6 walls. Had planned on having soffit vent>1-2″ baffle>ridge vent and spraying open cell foam on the ceiling side of the baffle and then sealing with gypsum board, but after reading concerns on open cell, began looking at high density batting. So my first question is…With good venting and sealed baffle, is open cell foam a bad idea for the ceiling with this design, and if it is, why is the moisture concern any different than fiberglass insulation? I know closed cell is recommended, but I don’t want the extra cost.
Second question..Since I was planning on using open cell on the 2 x 6 walls, what is the recommended layering of material for exterior walls based on the materials I listed above? Should there be a vapor and moisture barrier on exterior with gypsum on interior? This would seem to form the bad sandwich when using spray foam.
I have read multiple posts and articles on this subject so I apologize if I have asked questions that are clearly answered in other posts, but just want to get some answers to my specific home project. Thanks in advance.
GBA Detail Library
A collection of one thousand construction details organized by climate and house part
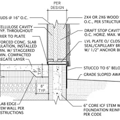
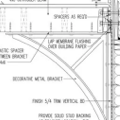
Replies
Scott,
If you include a ventilation channel above the open-cell spray foam insulation between your rafters, there is no risk of moisture accumulation in your roof sheathing. In Zone 3, most codes recommend a minimum of R-38 ceiling insulation; that means that you will need at least 10.5 inches of open-cell spray foam.
Of course, your plan doesn't address thermal bridging through the rafters.
Q. "What is the recommended layering of material for exterior walls based on the materials I listed above?"
From the outside in:
Siding
1x4 vertical strapping to create a ventilated rainscreen gap
A water-resistive barrier (for example, Tyvek or Typar housewrap)
OSB or plywood sheathing
2x6 studs filled with the insulation of your choice
Drywall
Vapor-retarder primer (paint)
Finish paint
Of course, this approach, like your planned approach for the roof assembly, doesn't address thermal bridging through the framing members.
Martin,
Thanks for the quick response. From looking at other posts and articles, could I assume that thermal bridging with a 2 x 12 rafter would be fairly minimal? And if not, what is the recommended method to deal with this issue?
Also,
Given your answer with the open cell insulation and vent baffle, is open cell strongly preferred vs high density batting?
Scott,
Comparing the R-value of 10.5 inches of softwood lumber and the R-value of 10.5 inches of open-cell spray foam:
Softwood lumber: R-13
Spray foam: R-38
The softwood lumber will make up about 6.25% of your roof area, so you'll end up with 93.75% of your roof at R-38, and 6.25% of your roof at R-13.
Under some conditions, the R-13 areas of your roof will melt the frost on your roofing, causing stripes.
Is this a big issue? Perhaps not, but the answer depends on your goals. Ideally, you would design a roof with a layer of rigid foam above the roof sheathing to address thermal bridging.
How about raised heel trusses and cellulose?
Scott,
Q. "Is open-cell strongly preferred vs. high density batting?"
A. Neither approach makes for a very well insulated roof, frankly. When it comes to cathedral ceilings, I'm a strong believer in the value of including one or more layers of rigid foam above the roof sheathing.
For more information, see these articles:
How to Build an Insulated Cathedral Ceiling
Plan Ahead For Insulation
+1 on the above-deck foam with no venting approach. In zone 3A it only takes an inch of polyiso above the roof deck for minimal dew point control on an unvented cathedralized ceiling at a cost of about 50-60 cents per square foot, but 2", (doubling the R-value of the framing fraction) would be a bit better, giving you more dew point margin and less risk of ice damming.
Rather than 6.25% framing fraction of a 24" o.c. roof is usually closer to 7-8%, since most roofs a have ridges, hips, framing around plumbing stacks, flues & chimneys, etc. . An infinite uninterrupted plane of 24" o.c. roof would have a "clear assembly" framing fraction of 6.25%. Real roofs are always higher. (A large survey of roof framing designs in CA came in at a bit over 7%.)
At a 7% framing fraction in a 2x12 roof, installing full depth R49 batts or cellulose or open cell foam delivers a U-factor of about U0.028.
Adding an inch of polyiso above the roof deck that drops to U0.023.
Adding two inches and it drops to U0.020.
At 2" it's a 29% reduction in heat transfer, but only a 24% increase in center-cavity R value.