Details for Spray Foaming an Unvented Vaulted Roof

Hi,
Thanks for all the insight on insulating vaulted ceilings – both vented and unvented.
16 years ago we did it wrong. Not enough vent space plus I think the space/void above our front porch did not help in generating proper airflow to the ridge vent. Inside, the top floor has a knee wall and vaulted ceilings. The rafter bays are 5.5″ deep and 24″ wide. Raftermates were placed under the roof sheathing – then 5″ of roxul (R22) – then poly vapor barrier – then the drywall. Ice damming was guaranteed each winter. We live in climate zone 6. Building code minimum is R-31 here in Sudbury, Ontario.
Now we need a new roof. I will be working from the top down. I would like to avoid needing to take down all the drywall/vaulted ceiling inside.FThe sheathing is coming off and I will be pulling the roxul and spray foaming – likely heading toward an unvented foam filled roof.
Q1. should I cut/pull the poly? will it affect the spray foam cure?
Q2. should I put up the new sheathing and then have the foam injected to fill the rafter bays / cavities?
or spay the foam into the empty rafter bays and then put on the new sheathing?
I am concerned about needing to trim off the excess foam before re-sheathing.
Q3. is it possible to flash & batt from the top down? 2″ of foam against the drywall ceiling and then put the roxul back in? being able to reuse the roxul cost-effectively somehow.
Q4. should I insulate the space above the front porch?
I will be adding horizontal strapping above the roof to correct some dips and straighten the plane of the roof. This would increase the depth of the rafter bays by 1″-1.5″ and give us a grid to work off of. At the same time I am hoping that it may also help negate some thermal bridging.
Thanks.
Peter
GBA Detail Library
A collection of one thousand construction details organized by climate and house part
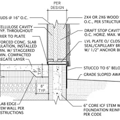
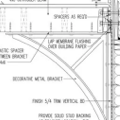
Replies
rough drawing attached . . . and sorry for the bad spelling - celing! (I really want to be able to edit it and fix it just like my roof!)
Peter,
You didn't mention whether you are considering the use of open-cell spray foam or closed-cell spray foam. In your case, you don't have much room to work with, since you have 2x6 rafters. If you use open-cell spray foam, your roof will still be plagued by insufficient R-value, so I assume that you are thinking of using closed-cell spray foam.
If you can manage to install 5 inches of closed-cell spray foam (it's hard to fill a cavity completely when installing closed-cell foam), you'll have about R-30 or R-32 -- still not enough, but better than the R-22 you have now.
A better solution than any of the solutions you are suggesting would be to block the existing ventilation channels at the base of the rafters and at the top of the rafters, and then to install about R-25 of rigid foam above the roof sheathing. But I know that approach requires adjustments to the exterior trim, and the work is expensive.
Q. "Should I cut/pull the poly? will it affect the spray foam cure?"
A. If you plan to install closed-cell spray foam, the polyethylene can stay.
Q. "Should I put up the new sheathing and then have the foam injected to fill the rafter bays / cavities?"
A. No.
Q. "Or spay the foam into the empty rafter bays and then put on the new sheathing?"
A. Yes, this is the approach I would take (given the two options you listed). Injecting foam is quick tricky.
Q. "I am concerned about needing to trim off the excess foam before re-sheathing."
A. Your spray foam installer will be careful not to fill the cavities completely. That is the usual approach with closed-cell spray foam.
Q. "Is it possible to flash & batt from the top down? Two inches of foam against the drywall ceiling and then put the Roxul back in?"
A. This might work, but it's an unconventional approach. If you go this route, it's important to maintain the ventilation channel.
Q. "Should I insulate the space above the front porch?"
A. That isn't necessary (although it might happen if you take my advice to install rigid foam above the existing roof sheathing). Just make sure that the "kneewall" shown in your sketch (it's actually an exterior wall) is carefully air sealed and insulated, just like any other exterior wall in your house.
Thanks Martin.
Our trim needs work anyhow!
If I go with rigid foam above the sheathing (via nailbase?) I would not have to touch the pre-existing roxul setup?? that is somewhat appealing.
Would I need to be concerned about the straightness / plane of the existing roof prior to install of rigid foam / nailbase?
With metal going on top is there benefit to venting on top of the roof? Or am I safe installing the metal directly to the nail base sheathing?
Thanks again Martin - very much appreciated.
Peter,
Q. "If I go with rigid foam above the sheathing (via nailbase?) I would not have to touch the pre-existing Roxul setup?"
A. The Roxul could stay. But I'll repeat: You'd have to find a way to seal the ventilation openings at the bottom as well as the top.
Q. "Would I need to be concerned about the straightness / plane of the existing roof prior to install of rigid foam / nailbase?"
A. If your roof is sway-backed (with a sag in the center of the 2x6 rafters), you could take this opportunity to shim the low spots before the nailbase is installed. But the shims would have to provide enough support (and be wide enough) to prevent the shims from digging into the rigid foam. Wide tapered shims would be best. This shimming work would provide aesthetic benefits, not structural benefits.
Q. "With metal going on top, is there benefit to venting on top of the roof?"
A. Venting is optional. If you are worried about ice dams, venting is a type of insurance.
Q. "Am I safe installing the metal directly to the nail base sheathing?"
A. It's perfectly OK to install metal roofing on an insulated unvented roof assembly, as long as the roof has adequate R-value. If you get very deep snow, however, a vent channel may be useful to reduce the likelihood of ice buildup.
Averaging over 5000HDD-C (base 18C) Sudbury is at the warm edge climate zone 7, not the cool edge of climate zone 6:
http://sudbury.weatherstats.ca/charts/hdd-25years.html
http://www.energyvanguard.com/hs-fs/hub/88935/file-30563967-jpg/images/iecc-2009-climate-zone-criteria.jpg?t=1473248044917
In zone 7 you need at least 60% of the total-R to be exterior to the first condensing surface to have sufficient dew point control with class-III vapor retarders. So for an R50 roof with the roof deck as the condensing surface you'd need R30 rigid foam above the roof deck, with R20 fluff below, using standard latex on gyproc as the vapor retarder. But R30 is would take 7" of expanded polystyrene, which is thick enough to be awkward to build.
You would also be fine with just R20 above the roof deck, and of 2" of 2lb closed cell spray polyurethane foam (R12-R13 ) on the underside of the roof deck, and R15 rock wool filling the rest of the rafter cavities for a total of R47-R48. The 2lb foam is a Class-II vapor retarder (meeting Canadian code definition of a "vapour barrier" ) which limits wintertime moisture accumulation at the roof without blocking drying toward the interior completely. The first condensing surface would be the interior face of the spray foam which would have more than 65% of the total R exterior to the rock wool, keeping the cavity with the rock wool dry. R20 only takes 4.5" of EPS, which is much easier to install.
If using nailbase panels, in a zone 7 location derate the labeled R of polyisocyanurate to about R4.5/inch of the thickness of the foam for calculating the dew point control ratio. For EPS it up-rates to R4.5/inch (or even R4.6) in your climate. While mid-winter performance average is comparable inch-per-inch, the shoulder season performance of the polyiso will be somewhat higher. So, for R20 it takes a 5" panel, independent of foam type.
With R20 of thermal break over the rafters, an R47 (center cavity) roof outperforms R50 installed fully between rafters.
Climate zone 7! why do I even live here!?
Thank you Martin & Dana.
I will think about both replies for a bit - likely come back with one more round of questions to ensure / confirm my final approach.
Enjoy your day.
Dana,
you have definitely upped the ante on this roof job. To meet your specs can you help with some clarification on the process:
- we currently have drywall - 6mm poly vapour barrier - 5" of mineral wool. We are working from the top of the roof down. Would we need to pull the mineral wool and cut-out the vapour barrier? or can we keep the poly (I know the answer is likely - no re: drying to the inside)
- we have 5.5" of depth in the rafter bays and a dippy roof plane. if we run horizontal 2x4 across the roof to correct the plane we would be adding 1.5" of depth to the rafter bays (except where we have the new wood); if we keep the 5" of mineral wool and fill over top the mineral wool with 2" of spray foam coming level to the tops of the new 2x4 strapping would this be acceptable practice? perhaps we compress the mineral wool below the new wood? I am trying to avoid cutting the mineral wool! (20 + 12 + 24 = 56; 36/56 = 64% above the inside face of the spray foam)
- if we do not add horizontal corrective strapping can we compress the 5" mineral wool to accommodate the 2" of spray foam (while maintaining enough R-value in the mineral wool)? 5"compressed to 3.5" still give us the R15 you mentioned earlier.
- since we need to remove the sheathing to meet your specs we would now be employing SIPS as opposed to nail base. I am assuming that we can attach the SIP to the new 2x4 corrective strapping (if we go this route) - but I will check with manufacturer about how deep the SIP screws to go into the attaching surface. I should also ask if you would use SIPS or simply put new sheathing on and go with nail base?
- if we do not use the 2x4 corrective strapping can we shim the SIPS to correct the roof plane?
- at the peak of the roof should the front layer of SIPS overlap the back layer ( so as to seal off the peak ) ??
One of the likely benefits of removing the existing sheathing would be that we could do a better job sealing up the soffits and get a better look at where the (exterior) knee wall comes into play as Martin emphasized the importance of doing a good job with sealing up the old venting.
Thanks again!
I think I need a drawing (or to re-read it in the AM when the coffee is still working :-) ).
Short answer on removing the poly is, as long as you have sufficient exterior R for dew point control it's not very risky at all to just leave it in place (and that's what I would do. YMMV.)
Here's a diagram . . .
Peter,
The reason that your image didn't load properly may be due to its title. I think that the plus sign (+) may be considered an "illegal character." Try naming it something like "Zwarich sketch." Don't name it "Image 1" or "Image 2."
Thanks Martin
Peter,
You've got lots of questions, and I probably can't answer them all (at least not all at once). But it sounds like you are leaning towards the idea of installing SIPs above your existing roof assembly. If you do that, the SIPs will provide the rigid foam layer for a type of sandwich assembly that consists of rigid foam on the exterior side of the assembly, and fluffy insulation (in your case, mineral wool) on the interior side of the assembly.
If that's your plan, you don't need any spray foam between your rafters (just an airtight ceiling made out of drywall).
You have to follow the ratio rules outlined in this article: Combining Exterior Rigid Foam With Fluffy Insulation.
Martin & Dana - I am doing lots of 'thinking aloud' here. Thanks for putting up with me.
I've read the article re: Combining Exterior Rigid Foam With Fluffy Insulation. I have my head wrapped around the importance of planning the roof with respect to the dew point. I think I may have dew on my brain at this point . . . time for a foam hat perhaps.
I initially mentioned that we were in Climate Zone 6 but Dana pointed out that in Sudbury, ON we were on the warm side of zone 7. 51% vs 61%. This can make a big difference in calculations. Since we are right at an average of 5000HDD's I am going to split the difference and use 56% for the foam value above the roof.
R-49 x .56 = 27.44 above the roof. Leaving room for R-21.56 below the roof - we currently have R22 worth of mineral wool. I can purchase R-28 6" nail base - which is bang-on for 56% above the roof.
Doing it this way means we can keep the existing sheathing and mineral wool insulation in place and save about $2K by not using spray foam. Less material costs and less work.
Perhaps we will use staggered layers of foam vs. nail base. Either way I will follow the directions here:
https://www.greenbuildingadvisor.com/articles/dept/musings/how-install-rigid-foam-top-roof-sheathing
I will be sure to seal up all the vent spaces but good Martin.
Thanks to both you & Dana - your help and patience is very much appreciated.
Peter
Please do let me know if I am way off base though . . .
Peter,
You are not way off base. You are on the right track.
If you end up with shims under your rigid foam (or SIPs, or nailbase), just make sure that the air pockets around these shims aren't connected to the outdoors. You need careful air sealing of these air pockets, so that you don't accidentally create channels that Joe Lstiburek memorably called "three-dimensional airflow networks." (The phrase bugs me, since all airflow networks are three-dimensional. We don't live in a two-dimensional world.)
Martin. Three dimensions? Not so fast. ;-) http://motherboard.vice.com/read/there-is-growing-evidence-that-our-universe-is-a-giant-hologram
Thanks Martin,
that's exactly what I've been mulling over. My current train of thought is to try to correct the plane using built up sections of the adhesive membrane that we will use for the entire roof deck.
And - air seal like crazy around the perimeter of the new foam. More research needed there . . .
Likely going with the 6" Nail base . . . cost is not far off and it should save time and some effort over using built up layers of store standard foam sheets.
Have a good day Martin
UPDATE - 4 years after roof install. We developed a moldy knee wall; I ripped the wall and ceiling apart and found condensation between the roxul and the foil backed poly iso (which I never intended on using - the supply company shipped it to me instead of plain EPS foam panels - I ended up using the poly iso - perhaps foolishly). I am checking back in as I want to remedy/finish the job properly now.
What ended up happening with the roof . . .
We removed the roof sheathing. We pulled out the old pink rafter vents and topped up the rafter bays with more roxul. We ended up with about 8" of Roxul on average. Maybe R-30-36
We placed 2x4's across the tops of the rafters (shimming where needed). In between the 2x4's, we placed 2' wide sections of 1.5" foil backed poly iso (foil on both sides). We taped the top joints with red vapour barrier tape. We did not have access to seal the bottom of the foam pieces (likely where this all went wrong).
We then installed another series of 2x4's vertically (perpendicular to the first set of 2x4's) and installed another layer of 1.5" foil backed poly iso between those. We have about R18.6 worth of poly iso above the Roxul. After taping the second course of poly iso, we doubled up the vertical 2x4's to create 1.5" high x 2' wide venting channels. We installed 3/4" plywood sheathing overtop the 2x4's. Diamond Deck (??) underlayment over the plywood with metal roofing over that. I should mention that I spray-foamed the entire perimeter of the roof to seal the edges of the foam layers.
Fast forward four years. One of my adult children finds mould behind some books. We found white mould within the wall cavities of the knee wall and some at the cap/top plate.
How did the moisture get there . . .
1) while we had the shingles off our old roof, remnants of a hurricane blew through and my tarp job was insufficient and Roxul in the knee wall cavities definitely got wet. We have log walls on our main floor and the Roxul/wall cavities were able to drain down onto the main floor walls. We should have pulled the drywall then-and-there but we did not because we were already overwhelmed with the roof. So, remaining moisture in the knee walls may have wicked up into the rafter bays.
2) Condensation took place between the Roxul and the iso poly - because:
a) the foil is impermeable
b) the bottom of the first layer of poly iso was not properly air sealed in the rafter bays (I am leaning toward this after rereading the earlier posts)
c) because of possible moisture trapped in knee wall insulation wicking up through the Roxul.
We will remove another section of ceiling on the other side of the house to see if something similar is happening there - this could help us figure out if the knee wall insulation was the issue or if the lack or air sealing is the issue (could have been both I guess).
The Fix
Thankfully we needed to do drywall work anyway . . . drywall is coming off the ceilings, Roxul is being carefully puled out of the rafter bays - we now have access to the bottom layer/surface of poly-iso. I am thinking that if I spray foam (DIY kit) the rafter bays with 2" of foam then the poly iso would become air sealed. With that we could put the roxul back in. And . . . finish the ceiling with wood this time around.
Questions:
Is it ok to put the Roxul back in, 5.5", after air sealing the poly iso above with spray foam?
(Poly iso - R18.6 + spray foam R-12 + Roxul R 24)
If not, I could likely stack more poly iso in the bays leaving room to spray foam in place and air seal.
Or, spray the entire bay which could safely hold 6.5" (likely very pricey - which, ideally we could avoid).
Also, if we add the 2" of spray foam + Roxul, should a vapour barrier be used between the wood ceiling and the roxul?
I gotta say - I love doing reno's but I feel like a schmuck . . . very interesting to see the condensation at play. Glad we caught this now. I learn a lot, unfortunately, from my mistakes.
Many thanks - hoping you can assist one more time here. Also hoping that in sharing my situation that others can learn about the perils of moisture. The mold has been cleaned. Looking forward to a solid fix. Our new roof is doing its job. No ice dams, no leaks.
Like many - I am looking forward to a better future.
(I should note - as Dana, mentioned, we are on the warm side of Zone 7)
We took down some drywall from the ceiling in the opposite corner of the house. No mould issues. Minor condensation - running fingers along the underside of the foam panels, that were installed on top of the rafters, you can feel a hint of moisture to be sure.
We will still proceed with taking down the ceiling, pulling the Roxul, air and vapour seal with 2" of closed cell spray foam, put Roxul back in. Not sure if we need a poly vapour barrier back up before finishing the ceiling (shiplap/wood this time - not drywall).
Update - completely gutted our upstairs living spaces. Cleaned up the mould. I think we had water intrusion through our exterior stucco walls as well as interior intrusion through holes in drywall + some condensation from our addition of foam panels with a foil face (vapour barrier) to the top of our roof.
If you are a DIY'er - this is complex stuff. Be prepared to undo your work and treat your home as an ongoing experiment. Do not assume that since you have finished your project and it somehow works in your headspace that it will actually work out in reality. Pay attention and observe. I do wish we had found our mould issue sooner. Life is always busy for us and the mould lay hidden behind some books on a shelf.
We have spray foamed 3-4" in all wall and ceiling cavities. We will add back some fresh Roxul to help with sound deadening (metal roof) and to bump up the R-value a bit more. We will put shiplap on the vaulted ceiling and drywall on the walls. I may paint/spray some anti-mould paint over the spray foam and framing before the Roxul and the shiplap/drywall goes back up. We will not install a poly vapour barrier as the spray foam is now our air and vapour barrier.
We will also be installing a spot HRV - Lunos e2.
We are now trying to figure out the best way to finish off our walls / shiplap.