Spray foam advice

Hi All,
I’ve been using open-cell foam on the underside of roof sheathing in a several attics in climate zone 5 (southern Connecticut) but have recently been reading about the possibility of moisture moving through the foam and making the OSB sheathing damp so I’m looking for an alternative. I originally decided to go with open-cell for two reasons: one being that it enabled me to do continuous insulation over the rafters, and the other that it was more cost effective then closed cell. I’ve gone back to some of the jobs and taken some core samples and from what I can see, the sheathing looks okay. I should mention that the houses were all about 50 years old and did not have OSB sheathing. I’m currently building a large new addition and would appreciate any thoughts on doing 2” or 3” of closed-cell on the sheathing with open-cell on top of it to achieve r-38. That way the closed cell would stop any moisture from getting to the sheathing and the open cell would keep costs down a little while allowing me to cover the rafters. So my questions are: do you think that is a good strategy to do the combo or should I move to using all closed-cell? If doing the combo, is 2” of closed-cell foam enough or should I go with 3” under the open-cell? Also, I recently took some core samples from insulation on a home (I did not do the insulation but was asked to evaluate it) with an open and closed-cell combo. The samples revealed a half-inch space between the two. Is anyone aware of any issues with the closed and open-cell not adhering to each other? Any thoughts or suggestions would be greatly appreciated.
Thanks,
Joe
GBA Detail Library
A collection of one thousand construction details organized by climate and house part
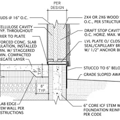
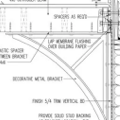
Replies
Joe,
Most building codes require a layer of gypsum wallboard on the interior side of spray foam insulation. If that is the case where you are, you should simply paint the drywall with vapor-retarder paint. That layer will be enough to keep your roof sheathing dry, even if you use 100% open-cell spray foam.
For more information on this issue, see Open-Cell Spray Foam and Damp Roof Sheathing.
If open-cell spray foam still makes you nervous, or if you live somewhere where interior gypsum wallboard isn't required, your plan to install 2 inches of closed-cell spray foam against the underside of the roof sheathing, followed by open-cell foam, will work. I have heard of other builders using this technique. It is a technique that Joe Lstiburek has recommended.
I haven't heard of any problems with voids when this technique is used, but of course the quality of any spray foam job always depends on the skill of the installer.
Thanks for the quick response, Martin. As long as there is a pull down hatch (not steps) the building code in my area will allow the use of an intumescent coating so that’s usually the option I use. I could paint the second floor ceiling with the vapor-retarder paint. Do you think that is just as effective as painting a vaulted ceiling being that the drywall isn’t right up against the foam? And I’m curious - does the intumescent coating act as a vapor retarder also?
Joe,
If you want to control water vapor transmission through open-cell spray foam, then no -- installing vapor retarder paint on the ceiling below the attic is not the same as installing a vapor retarder nearer the spray foam.
And as far as I know, intumescent coatings aren't vapor retarders (although you could ask the intumescent coating manufacturer the question). In general, even vapor retarder paints don't work as vapor retarders when sprayed on cured foam, because the bumpy, irregular surface of the foam makes it difficult to limit vapor flow.
It only takes an inch of closed cell foam to be fairly protective of the roof deck, and 2" would be quite protective. The issue then becomes wintertime accumulation of moisture in the open cell foam layer.
In a zone 5 climate as long as 40% of the total R is a low-perm type on the exterior you have sufficient dew point control at the high-perm/low-perm interface, as long as the high-perm goods are no more than 10 perms (high end of class-III vapor retardency) at the installed thickness.
With 2" of closed cell foam you're at ~R12, which would allow you up to R18 of open cell foam for a total of R30 for effectively zero risk.
With 3" of closed cell foam you'd be at ~R18, which would allow up to R27 of open cell foam for a total of R45. It takes ~7" of R3.7/inch half-pound foam to hit R27, which would come in at no more than 9 perms from any vendor. You'd be fine- any more than that would be a waste of good foam (and an unnecessary application of extra high global-warming blowing agent.)
This typical R3.7/inch half-pound foam comes in at R10-R11 @ 5.5"/R20, and would be a Class-III vapor retarder, about 7-8 perms @ R27:
http://www.icynene.com/sites/default/files/US%20content%20uploads/Classic%20LD-C-50%20-%20USA%20Technical%20Product%20Data%20Sheet%20Jan%202015.pdf
The ~R4/inch open cell foams are even-lower perm, and would all be under 5 perms @ R27, eg:
http://www.demilec.com/documents/Tech-Library/Sealection-500/Sealection-500-TDS.pdf
http://www.icynene.com/sites/default/files/US%20content%20uploads/CLASSIC%20PLUS/Classic%20Plus%20-%20USA%20Technical%20Product%20Data%20June%202015.pdf
The prescriptive R20 of low-perm for zone 5 in the IRC 2012 presumes R49 for total R (R38 was code for zone 5 under IRC 2009):
http://publicecodes.cyberregs.com/icod/irc/2012/icod_irc_2012_8_sec006.htm
Since open cell foam is not damaged by water, even if there is some minor accumulation in the foam over a colder than average winter it would still be unlikely to cause a problem. Going with 2" of closed cell (R12) and 6.5" of a higher R/inch open cell is probably the "rigth" solution here. Closed cell foam needs to be applied in lifts of no more than 2" to be fire-safe during installation and avoid shrinkage/adhesion problems, open cell no more than 5.5". With 2" of closed cell it's a single pass, and with more than 5" of open cell you'd be at two lifts on the open cell in either case. With a higher-R open cell foam at R27 you'd be at the low end of Class-III vapor retardency- any worst-case moisture accumulation would be minimal, and non-damaging.