Soy-Based Insulation

I’ve heard that there has been trouble in the past with soy-based insulation products maintaining consistent mixes and thus performance. Does anyone know anything about this?
I generally understand that the whole soy-based craze is basically a marketing ploy by the spray foam industry and that there really isn’t that much soy in the products. Do others agree with this assessment? What are your feelings on soy vs. non-soy products?
GBA Detail Library
A collection of one thousand construction details organized by climate and house part
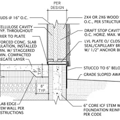
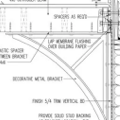
Replies
Yes there have been many stories about gummy sets and inconsistency with soy-polyols in the B-side of the mixes. I also agree that the bio-based element is largely marketing hype. Some of the companies are taking credit for water as part of the "bio-based component" in their mixes. In general the soy based polyols are less 35% of the B-side which is added 50-50 to the A-side to make the foam at the site so the bio-based component of the foam is usually less than 17% (not counting water as a bio-based component.) Check the B-side MSDS of the products you are considering using and pay special attention to the percentage of Bio-based polyols, water, and the percentage and composition of the flame retardants used in the mix. I would avoid using spray foam made by companies who list the flame retardant in the B-side MSDS as "Trade Secret".
Also ask about installer training, off ratio mixes can result in un-consumed Amine catalyst which can lead to the residual fishy odor you have undoubtedly been hearing about. And watch out for foam sales tactics that use inflated “R-value equivalent” claims. Multiply the listed R-value per inch by the contracted depth of the product to get the R-value. 5” x R-3.6/inch does not equal R-30. Anyone who believes that “the R-value of 11” of foam is basically the same as the R-value of 5” of foam” should not be selling insulation. (unless they will accept payment in lottery tickets.)
I would focus more on the flame retardants. I can accept TCPP as a less toxic (to humans) flame retardant but it's still non-biodegradable, bio-accumulative in marine life, brominated and halogenated. TEP is generally considered to be preferable as it is non-halogenated and biodegradable. But either should be separated from the living space with sheetrock or an air barrier and scraps and dust should be collected and landfilled. Treat un-cured spray foam in the same way you would tread Round-up herbicide, avoid skin contact and do not dispose in open water. Exposure of TEP to soil or garbage dump conditions breaks it down quickly. Not so with TCPP or the rest of the much more toxic halogenated flame retardants. The new class of polymerized flame retardants are extremely suspect. Less toxic, non-halogenated, and bio-degradable is a far better direction for the industry than polymerized from what I am reading.
At this point Bayer seems to be using just TCPP. So it gets the nod from me for least toxic until someone starts doing a spray foam with a TCPP-TEP blend or all TEP. I feel that we can manage the toxicity on-site with really thorough worker training but once it's in the landfill it's on the way to the ocean unless it's bio-degradable. I'll take TCPP over "Trade Secret" for now in hopes that someone will come out with a TEP-only spray foam in the near future.
I still use spray foam in my homes, but very carefully and deliberately. I avoid spraying in really humid or really cold conditions to optimize the potential for full consumption of the catalyst. I stop the crews if they don’t outline the edges of the wall or roof cavity first, spraying the sides of the framing members and filling corner cavities and then coming back with 2” to 3” “lifts” to gradually bring the thickness up the contracted depth. It’s important to allow each lift to fully expand before adding the next lift. Use a broomstick with a wire flag extending from the end of it to probe for foam depth especially near the walls and at the ridge. Don’t permit the use of shrink wrap to dam the soffits, the foam should enclose and seal the full width of the top of the wall plate so soffit dams should be on the exterior of the plate, otherwise humid air can escape from the top of the wall cavity. Finally keep people, especially children and women of childbearing age or younger, out of the spray foam area for three days after foam application to allow the foam to cure. I also avoid foaming the walls to minimize the dust and waste from shaving the excess. I prefer to use spider Micro-filament fiberglass in those areas.
Arlene Blum covers the science behind the flame retardant issue well at the Build Well Forum here:
http://www.ecobuildnetwork.org/the-build-well-forum/sarah/the-fire-retardant-dilemma-should-green-buildings-contain-toxic-fire-retardant-chemicals
Does bio-based insulation only come in open cell? Are there any real benefits to using bio-based open-cell spray foam rather than conventional open-cell spray foam? I assume both would use the same blowing agent and flame retardant given that they are by the same manufacturer?
If you spray 2,000 cubic feet of 1/2 lb/ cu ft foam to insulate your house and the product is 15% bio-polyols then you have used 150 lbs of bio-poloyols rather than petro-polyols. I don't see much advantage here but it might help you gather a few extra points in one of the Green Building Certifications.