Solving issue of frost/moisture on inside of drywall — Insulators’ proposed solution

We have a house that was built in 2008 and has had frost/moisture on the inside of the house where we have a bumpout that contains a bedroom closet, bathroom, and another bedroom closet. Our house is located in region 4A.
We had an energy audit performed and had the auditor investigate the situation. Per his report, “The condensation problems on the west side of your house are incredibly abnormal. We’ve seen light condensation on walls during cold snaps but never frost on the inside of a wall.”
This bumpout is not a cantilever but it is closed off from attic access, however there were two soffit vents. The insulator has proposed filling the open area with loose fill fiberglass completely and sealing the two soffit vents. They will cut holes in the zip board in the attic so they can access the cavity and they plan on leaving the holes open after they fill the cavity. FYI there are batts currently in this cavity.
Please see the pictures I have attached of the actual house as well as a couple of drawings of the current situation and the proposed solution. We also have a cantilever that is also leaking and they are proposing the same solution.
We want to do as much as possible to minimize the potential for moisture/mold as a normal precaution, but with our son already having numerous health issues, this makes it even more important. Does anyone see any potential issues with this solution? Thanks in advance.
GBA Detail Library
A collection of one thousand construction details organized by climate and house part
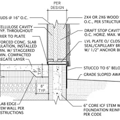
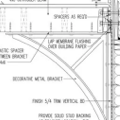
Replies
Brian: Sorry to hear. Can you provide any information on how the walls are insulated, and whether or not you have "cold corners" (the bottom of the insulation in the attic meets the inside edge of the wall insulation, leaving essentially nothing right in the corner)? I think you are going to hear about tearing off siding, etc, and properly insulating and air sealing. I don't think filling the cavity w/ insulation is advisable, but wait till the pros chime in.
Brian,
Looking at your photos, it seems that you have issues with the walls as well as the ceiling. We see this quite a bit with bumpouts like yours where there is a lot of framing and often non-standard sized wall cavities. The risk of poorly installed insulation goes up.
In the ceiling, the batts were likely installed before the drywall went up and it is possible that there is no insulation at all over the top plate. If that is the case, the drywall will be extremely cold, which of course is what causes the indoor humidity to condense and turn to frost.
To solve your problem, you need to air seal and insulate properly, which blown fiberglass will not do. I would recommend removing the batts and insulating the back of the drywall and all of the framing with spray foam. There doesn't seem to be a lot of room so you may want to go with a closed cell foam to get the higher r-value.
If you want to address the walls as well, they will have to be opened up. If your siding is easy to remove and put back, doing this from the outside is no big deal but if it isn't, it may be more cost effective to take down the drywall and work from the inside. Either way, the prescription is the same: air seal and insulate properly.
If your bathtub sits in the bumpout, there likely is an added benefit to tackling the walls. In standard construction there is almost never any air barrier between the tub and the outside wall sheathing, which can make the tub unusable in the winter. When we handle these jobs, we open the wall from the outside, remove the old insulation and install a suitable surface between the studs behind the tub. Then we air seal and insulate everything with sprayfoam before we caulk the frame as needed and put the wall back together again.
Brian, first of all, that's an excellent set of photos and drawings. It really helps give a sense of the construction.
I'm confused by the references to condensation in the text of your post vs. the indications of leak areas on the photos. You could develop those moisture signatures via condensation, but I would expect your house to be really, really humid, such that you have sweat on the windows that doesn't go away, or other obvious signs. Lacking that, I wonder if you have water leaking in at the bumpout roof, possibly where it meets the wall along the top of the roof slope. Your photos enlarge nicely but I can't see what the roof-to-wall flashing looks like there. The bumpout roof definitely does not appear to be vented. Do you get wind-blown rain against that wall? Any correlation between rain events and water stains showing up inside?
I doubt that we can rule out any possible cause here online without further information. If I were there I would need to carefully inspect the exterior for any possible water infiltration areas, and would need to check the interior, the crawl space, the attic, and everywhere else for signs of excess moisture. But, my hunch is that you have a flashing leak and that the insulation in the ceiling of the bumpout is fairly wet, such that it's wetting the sheetrock to the interior and conducting a lot of coldness in with it.
Did your energy auditor collect any interior humidity data, or anything else besides comment on the unusual nature of the situation?
John, Torsten, and David... thank you for the replies.
To answer your question John, the walls are insulated with a blown in fiberglass which if I am remembering correctly yields an r-15 in a 2 X 4 Wall.
Please note that the interior photos were taken the night of the frost/leaks (1/07/2010).
Weather Conditions
January 7th, 2010 (from weatherunderground.com)
High temperature 15 degrees
Low temperature 6 degrees
Precipitation T in T=Trace
Maximum Humidity 84
Minimum Humidity 51
Snow 0.10 in
Wind Speed 23mph (NNW)
Max. Wind Speed 32mph
Max.Gust Speed 41mph
We had another occurrence of moisture in the bathroom, two closets, and possibly the office soffit in the middle of January 2011 with weather conditions similar to the previous frost/condensation issues of 2010.
During these occurances we never saw any condensation on the windows. I can't say what the humidity level was in the house.
The energy auditor did collect humidity data as well as take some IR photos. I'm waiting on permission from him to post them here if necessary (I want to follow copyright since he took the photos). When he came the first time the outside temp. was 20 degrees, inside temp 70 degrees and relative humidity of 35%. The coldest interior surface from his tests was 50 degrees that day.
When he did a follow up on 2/2/2011, the outside temp. would have been between 1 and 14 degrees, inside temp. 72 degrees, relative humidity of 18% and the soffit vents to the bump out were sealed up to stop air movement coming in and there were no openings to allow air movement from the attic into the bump out.
Based on software simulating relative humidity of 40% there was an indication of the dew point being reached in the areas where the frost/moisture was initially found (the corners mainly, both inside and closest to the exterior wall) if that makes sense.
If you or anyone else has any other thoughts or more to add, please feel free. Thanks in advance.
I thought I was in zone 4A but your weather sounds much, much colder than ours. It doesn't sound likely that you had any rain at all in January 2010, or soon before that, based on the temps you are reporting. What zip code are you in?
Brian,
1. I believe that you're right -- the issue with the moisture in the cold corner is condensation.
2. I am confused by your labels on the photos of the room that you call the "office cantilever." You refer to a "leak." Do you mean an air leak or a roof leak? If it is a roof leak, please explain. If it is an air leak, what is going on there?
3. The proposed solution would create an unvented roof assembly using only fluffy insulation. That is not advisable. It is essential that you install a proper air barrier in your walls and ceiling along with adequate insulation. Torsten is right -- the easiest way to do this is with spray foam. If you don't want to use spray foam, you can address the issue with other air-sealing methods, but the workers need to understand airtight construction methods for the repairs to be effective.
50 degrees found on an inside surface is telling me there are serious areas in need of a fix. Outside cold air is getting in places it shouldn't be imo. You need someone local.
50 degrees found on an inside surface is telling me there are serious areas in need of a fix. Outside cold air is getting in places it shouldn't be imo. You need someone local.
Thanks again for all of the responses.
Martin: Sorry for the confusion...I really appreciate everyone's patience with me. When we have had the frost/moisture in the bump out we have also had it in the cantilever in the office (it hasn't happened any other times). I have attached a better picture of this as well as indicated where areas of moisture have occured.
What problems could occur with an unvented roof assembly with fiberglass packed completely? They do plan on leaving the holes they cut in the attic to add the insulation open so there would be some openings to the attic space. The insulators informed me that if this didn't work they would come back out to try something else. No matter what is done to remedy the situation I plan on having the energy auditor back out to recheck the areas to test the results. Again, thank you for your replies. They are greatly appreciated.
Brian,
First of all, this is probably an air leakage problem more than an insulation problem. Blown-in fiberglass is not an air barrier. So it's unlikely to help unless measures are taken to find the air leakage paths and to seal the air leaks.
Secondly, most building codes do not allow air-permeable insulation to be installed tight against the roof sheathing, because such installations have led to moisture problems in the past. The only way to install insulation tight against the roof sheathing is if you use air-impermeable insulation like spray polyurethane foam or rigid foam board.
Brian, your energy audit was done fantastically. What you need next is the contractor that follows up behind your auditor to give you a cost to rebuild that part of your home including adding a layer of cellulose to the loose fiberglass in the main part of you home. You also need blower door and air sealing most likely for the entire home as it seems 1980 developer style work is what your home is. What you see is nice but the bones were not what the low energy use contractors are doing.
Call your auditor and others till you find someone who has done many repairs like yours and well loved by his customers.
Myself I would start opening up areas inside and outside to peak in, if all the exterior was pulled, saved and reused as possible, then I would think sealing, and adding continuous insulation and venting could be done along with checking for rot. Changing to pressure treated framing... looking for carpenter ants. Pulling the outside would allow you to possibly use the space somewhat while doing the work. Pulling all the inside would most likely work too... For me if you had a week vacation, I would go in pull the drywall entirely, redo all, redo any exterior as needed and put all back by the end of the week.
Call contractors for detailed estimates... Demo, clean up rot if any, seal up air leaks (every joining of every piece of framing) decide where to insulate, vent, rebuild.
Martin,
First, thanks for your help. I think we are going to try to get something done as soon as possible. When you recommended air-impermeable insulation like spray plyurethane foam would you recommend open or closed cell spray foam? Open cell...at what thickness? Closed Cell...at what thickness? Our attic has R-38 loose insulation and I'm not sure what the batts are that are currently in the in inaccessible area. I'm not sure how much height there will be above the drywall before hitting the sloped roof. If I understand you correctly I will want an air path above the spray foam or foam board insualtion...is that correct?
Also, do you have a preference between the spray foam or rigid foam?
If we use spray polurethane foam or rigid foam would you recommend taking off the roof as it will be extremely difficult to access from the attic?
Trying to take care of the soffit in the office may be more difficult to remedy. How would you suggest getting the spray foam or foam board into the soffit cavity in the office?
I have attached a copy of the pdf report from the energy efficiency individual that covers two time periods (end of 2010 and 2/2/11). It shows infrared pics that may better illustrate our situation.
The following is an exerpt from an email sent by the energy efficiency individual after the 2/2/11 follow up:
Sorry for all of the questions. Again, thank you for your help!
Brian,
Fewer moisture problems are reported with closed-cell than with open-cell spray foam in applications like yours. Closed-cell foam can be sprayed directly to the underside of the roof sheathing, without an intervening ventilation gap, if you want.
In your climate zone, the code calls for a minimum of R-38 ceiling insulation, which is about 6 inches of closed-cell spray foam. Even if you can't install a full 6 inches, however, the spray foam will go a long ways to solving your problems.
I agree with AJ that it's probably easier to work from the inside than the outside. That means demolishing some drywall. You need to find a spray-foam contractor with air-sealing experience to help you.
Martin and AJ...thanks for your replies and answers. First, please accept my apologies as I am not sure I understand some of the information regarding the solution. I've attached a picture of what I am assuming a possible remediation would look like with closed cell foam on top of the drywall ceiling in the bump out (#1). If my picture is correct, I'm not understanding how to approach this from the inside. My problem in getting above the drywall is the existing roof sheathing and the side exterior wall. I am not seeing how the spray foam would be sprayed into area. Again, please accept my apologies.
I also attached another picture illustrating closed cell foam to the underside of the roof sheathing and around the rest of the soffit cavity(#2). Is either one of the images what you are imagining as a potential remediation?
Thanks again for your answers and your patience with my questions. Your help is greatly appreciated.
Brian, if you read all my posts as one I am back to my first post. If you called me, I would now talk costs, timing, dust control and start opening up the area to find out why the insulation and air stop materials are not working. The problems are hidden. I need to poke around.
My final solution would be determined while tearing the area apart. If I was there the problem all would be more obvious. I am also not saying spray foam over rigid. And the area my need to be framed different.
My bet, behind the finishes all is not done well enough.
By the way, thousands of homes have been built with similar problems in every subdivision in America. Your neighbors may have the same issues.
Why aren't you working this out with the builder? Builders and laws have warranties.
AJ,
We are out of warranty on our house. I'm just trying to figure out what scenario would work best. Each house in our subdivision has had a different builder. Anyone I have talked to/contacted either as a contractor, homeowner, etc. has seen this as unusual.
We had a blower door test done through the same energy effeciecy individual and the results were as follows:
You have my thoughts Brian. Why aren't you fixing this?
AJ,
I appreciate your thoughts. We had the original insulation company come up with a proposed solution which was shown in my very first post...but as Martin said:
He went on to further say that:
Torsten had stated
I was looking to follow that course of action but wanted to see if doing so through the bump out roof would be the easiest way to approach it. The suggestion of approaching it from the inside had me confused as to how to do this with spray foam...hence the two images in post #14 showing closed cell foam in two different postions. One on the ceiling drawall, and the second on the underside of the roof sheathing and filling the soffit.
Again, thank you for your thoughts and I'll see if Torsten, Martin or someone else wishes to provide their thougths.
Brian, one way or another you're going to have to find a contractor who can figure the problem out and fix it for you. I appreciate that you want to understand the solution yourself, but unless you are going to do it yourself, you still need someone who can take care of it correctly and completely.
You're either going to need one or two people/companies. This is a job requiring blower-door-guided air sealing. In spite of what is apparently low infiltration measured by your first blower door test, you probably have a major air leakage situation in this one particular area, and that is best solved with a blower door installed and running while the technicians are doing their work. If you can find an insulation contractor with spray foam capabilities AND a blower door, so much the better, but that might be two separate people.
Anyway, I would work from the inside, remove the drywall and insulation in the problem areas, then start the blower door. Find all the air leaks and seal them. Then, replace the insulation with whatever will get the R-value and other properties you need. If you need foam against the roof sheathing, use either rigid board or ccSPF. Once the insulation is replaced, install and finish new drywall.
Anyone who attempts to do this without blower-door-guided air sealing and probably further infrared is doing you a disservice in my opinion. It will take some searching to find the right person(s), but they are who you need. I would start with the energy auditor who did the report you attached, it appears to be competent and s/he should also know which contractors to call. If you can't find spray foam, use rigid board. My company would almost certainly use that approach because we don't have good SPF people here. We would do the blower door, air sealing, infrared, insulating, and whatever carpentry needed ourselves, and then bring in a drywaller and painter. You might get somewhere by looking for BPI certified people in your area, but I'm not sure how good their directory is.
A.J., your arrogance is intolerable and is not warranted by your level of technical knowledge. Give it a freaking break.
Brian, you can do this. David, really?
Steelers (were) winning. Get err done Brian...