Mechanical Drying of Wall Assemblies

This came up in a GBA article regarding Managing Water and Insulating Walls Without Sheathing. My FHB All Access does not give me rights to comment on GBA prime articles so I am here.
Based on the level of skills, and or willingness to manage the detailing as we insulate our homes, isn’t something other than a passive approach to drying worth entertaining?
I like Risingers (or whoever) idea of the snorkels for the wall cavities. As long as things are open couldn’t we do a bit better and come up with a way to mechanically enhance the drying.
Seems as we travel further down this path that this is something that should be taken more seriously. Combining lots of thermal resistance with the requisite reductions in energy seems to be a recipe for some big disasters.
I am not talking about 400 lb radiators, but just blowing enough air to accelerate things a bit. Maybe its triggered by observed moisture levels surpassing some level.
An energy rater friend of mine talks about newer homes smelling like old shoes after only a few years. while the problems might be deeper, close monitoring along with some mechanical assistance might take us a long way to preventing some of the disasters we have seen in high performance homes. I am told this is sometimes done in the commercial world, why not in residential?
Repairing or even replacing a home that has mold or rot, is not an energy winner.
GBA Detail Library
A collection of one thousand construction details organized by climate and house part
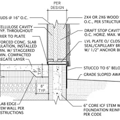
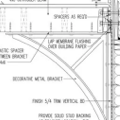
Replies
John,
Risinger was trying to come up with a work-around to ventilate walls in the rare situation where there is no sheathing or WRB (if he was really worried about them, he could have strapped the walls and re-sided). I don't see any reason that a properly detailed new house should have moisture problems in it's building assemblies or interior. That does seem to mean relying on mechanical ventilation for the inside air quality, but I can't see what would drive us to incorporate one into the building assemblies.
One of the main problems with high performance houses right now is the huge variety and proliferation of buildings assemblies, many of which are risky. You see it all the time here on GBA. Very complex and expensive walls or roofs which don't need much to push them into having moisture issues. To me that speaks of a need to find two or three that work in each climate zone and stick to them, rather than adding another layer of complexity for them to rely on, which if it fails renders the house as risk of damage.
I think going forward that is a great idea, though there are over 100 million buildings in this country alone. I agree that if it is all properly done, it should all work well. What is the percentage of windows that are properly flashed?
Mind you I am not talking about massive amounts of air, just enough to encourage drying. Martin H mad a great comment some place about turning on a ceiling fan to prevent interior frost on windows.
This mechanical ventilation would only be on when moisture is prevalent. That is the point of the monitoring.
WE never get to zero, net zero perhaps, but when you have reached a point where you are already mechanically aspirating the house why not a focused approach on the wall assemblies.
Again this goes to the trades who will actually build these walls. GBA provides a heavily biased sample or those who take the time understand, learn how and execute these details. No doubt many poorly executed assemblies will be built on the the newer codes. Absent a massive culture change I don't see it getting a lot better in the field.
Malcolm, it seems to me that a rain screen solves many of these problems, and is a nice passive way to "actively" ventilate a space with simple convection currents. I don't see any need for truely active things like fans or blowers here.
Overly fancy assemblies have too many things that can go wrong. Keeping things simple does have it's advantages. In the telecom world, power devices (although not as much as they used to be) tend to be convection cooled with big heatsinks with the fins veritcal. The reason for this is that fans can fail, convection always works. Things that can cool themselves without need of fans are thus much more reliable over the long term.
Bill
I don't think there is a right answer to this. A lot depends on what direction you believe building should take, and more generally the role of active or advanced technology in their function. I don't have the same pessimism John does about builders. Encouraged by a fairly thoughtful building code, the houses around me are constructed to a standard where envelope problems aren't a frequent issue anymore. The one exception may be interior moisture levels - and that's a direct result of occupants turning off their mechanical ventilation. Which makes me wonder how further less obviously beneficial systems would fare in terms of use or maintenance.
Maybe it's the climate I live in here in the PNW, but I can't think of a part of the building envelope that would benefit from having mechanically assisted drying. Perhaps elsewhere it's something to consider.
There seems to be a general belief that while all kinds of other ventilation are usually powered, wall/floor/ceiling/roof ventilation must be passive. But passive is often unreliable and sometimes quite expensive - so powered should be considered.
An uncommon example (see Dynamic Buffer Zone section).
Active ventillation comes with the downside of ongoing energy consumption, and moving parts that can fail. It has been my expierience that small muffin fans typically fail within 1-3 years, better quality fans and blowers may make it to 10 years or a bit over. There are blowers that can make it past 10 years, but they are pretty expensive.
If someone were to contemplate an active ventilation system for a wall, I would do a sort of ducted/plumbed system to allow the use of a single, central blower instead of a bunch of small fans. This will keep maintenance issues down, and result in a lower cost over time.
Bill
Thank you. That is exactly what I would anticipate. I would not run or recommend to run this fan continuously, only when drying needs to be enhanced.
Looking forward FHB recently rand a feature on active moisture monitoring. If even a small percentage of production homes had this the data would be very useful.
Maybe a right sized approach would be to employ this on north facing assemblies underneath window openings or likely failure points, like roof connections etc.
Running a small fan (intermittently, seasonally,, and only when needed) seems a small price to pay in energy to preserve the assembly.
I appreciate everyones comments and hope to see more on this, here or elsewhere.
Interesting. I am from Illinois so lets just say for many reasons we don't do as good a job as in say Wash or Ore. I just saw a project with a very good architect who has done many PH project in the area (truly outstanding world class projects) and the stucco wrap on the addition looks like it was put on with remnants. The part under the porch looked very neat and tidy.
I am really thinking to the day when we surpass R-13-19 walls and get to 30 or 40. mistakes will be far costlier.
Thanks gentleman I really appreciate the discussion here.
Interesting comment on turning off the mech vent. Same issue in my house. Its filtered its dryer etc etc. No I want "fresh air". There is no planning or design for that I guess.