“Smooth” flex duct

I understand that flex duct is bad in most situations–it decreases blower efficiency and just generally impedes air flow. That said, for a longish (25ft) run of 6″ duct, I wonder if it wouldn’t be okay to use one of the ‘smooth wall’ plastic ducts on the market (see http://www.flexaust.com/product/grass-collection-vacuum-hose/) for a good example of what I’m looking at. This would be in a relatively low-pressure type of situation (Minotair hybrid HVAC system installation). The ‘problem’ with using rigid metal in this situation is that the TJI floor joists are spaced at 16″ o.c., so it’d involve a lot of mastic and short sections of rigid pipe to get this done. My thought is that if using this kind of pipe saves me X hrs of labor, that covers the add’l cost quite quickly…
Any experience/thoughts out there?
thanks!
GBA Detail Library
A collection of one thousand construction details organized by climate and house part
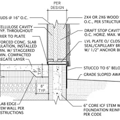
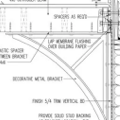
Replies
Jonathan,
You should only use duct materials that are sold for use in HVAC systems, for three reasons:
1. You want to be sure that the plastic can handle heat;
2. You want to be sure that the duct doesn't off-gas (introduce noxious odors);
3. You want to be sure that the duct is code-compliant, for safety reasons and legal reasons.
The duct you linked to is made of PVC and is not sold for use as HVAC duct.
All of this said, you can use conventional flex duct if you want. Install it carefully, supporting it as required so it doesn't sag. If you are worried about the corrugations introducing static pressure, you can oversize the duct.
In case you missed it, Allison Bailes wrote a great article on how to use safely flex duct (https://www.greenbuildingadvisor.com/blogs/dept/building-science/how-install-flex-duct-properly).
I hope you know (from a room by room heating and cooling load calculation) how much airflow the 25' flex run needs to provide. If you don't, find out before proceeding.
We generally figure no more than 100 CFM for a 6" flex run. A 25' run is fairly long. Assuming there is sufficient installation space it would be a simple and cheap change to bump the run up to 7".
There are 3 "S" rules for flex - stretch it, support it, and seal it. Done right it works right.
Most problems with flex duct arise when installers abuse its flexibility by failing to stretch and support it, or worse, kinking it or cramming it into spaces too small for it.
If space is tight rendering oversizing impractical, consider a hybrid of sorts - use sheet metal pieces wherever the run bends. You'll need to properly connect the flex to the sheet metal fittings. You'll also need to wrap the sheet metal fittings with insulation.
Avoid the typical practice of compressing flex duct's outer jacket at joints with a zip tie. While that practice is allowed by the governing trade association, it compresses insulation, reduces R-Value and increases possibility of condensation formation if ductwork is in unconditioned space.
At absolute minimum use a product like Hart and Cooley Smart Elbows whenever flex makes a 90* turn. Smart elbows enforce a gentle bend radius, improving air flow.
Another option to minimize airflow restriction to use HVAC rigid flat duct.
It's a rigid rectangular PVC extrusion specifically made for smaller HVAC jobs. For a 6" inline fan a 220 x 90mm profile rigid flat duct would be used.
Depending on where you purchase it from, it comes thermally protected or you can do line it yourself. The system also comes with self seal connectors which means no mastic need on the joints.
Not sure of who can supply it in the US, although here's a couple of links so you know what it is.
https://www.youtube.com/watch?v=w10HzVauEM0&t=5s
https://www.youtube.com/watch?v=Fx3zTf7CFck&t=2s
Giving this a bump to see if anyone has seen the ductwork Wayne linked in North America?