Smell from first floor after finishing basement

Hello All,
Hope to get an assist with my smell situation.
I’m in Toronto, Canada and I have a bungalow from the 1950s. Last autumn we finished the basement, including exterior waterproofing, rubberized and damp proofing membranes, and spray foaming the interior wood 2×4 walls with closed cell insulation. The foundation wall is concrete block, with a (I think) double brick veneer above ground.
This spring/summer we have had a strong wet/damp/old brick smell coming from the floor/wall of one of NE rooms. I am not getting the smell anywhere else on the first floor. It seems to be strongest when the temperature changes drastically between inside and outside temperature, ie the weather has been cooler the last few days and it’s less noticeable, although I haven’t correlated a specific trigger for the smell.
The basement area under the room is the laundry facility and there is no odour there. I have checked for leaky dryer vent, moisture/leaky water line and no such success. Been in the attic looking for water penetration, also had the water proofer excavate down to the footing to check for water in the block that can’t evaporate and both cases no water. Opened up a piece of wall in the basement corner and scraped out the spray foam and no water, that said the brick and foam were moist to touch.
Based on a previous post and answer by Dana in this thread:
https://www.greenbuildingadvisor.com/question/musty-smell
I’m starting to suspect the odour is caused by not have a vapour barrier in the section where the floor/rim joists are ie between spray foam in basement and tarpaper barrier in first floor walls. I am now thinking of spray foaming this area to see if it will resolve the odour. I’ve attached a diagram of the current situation.
Has anyone ever run into a situation like this or have any opinions?
I would appreciate any feedback, I have my original contractor and others out to investigate and no particular help.
Thanks,
Henry
PS Updated the diagram to have the veneer on the block!
GBA Detail Library
A collection of one thousand construction details organized by climate and house part
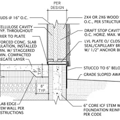
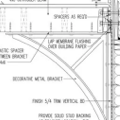
Replies
I wouldn’t be surprised if your smell is coming from the damp block by way of the air leakage path you show in your drawing. By sealing the block on the inside, it’s likely staying wetter longer. I’m surprised the gap shown in your drawing wasn’t already sealed, but I suppose it could have been missed.
What you don’t want to do is seal things with spray foam in a way that keeps your rim joist wet with no possibility to dry out. Make sure you have a good capillary break on top of the masonry part of the wall.
Bill
Could you explain a bit more on the capillary break? I'm looking to do CCF on my 1940's basement foundation wall/rim joints- do you think there is a capillary break between the sill place and foundation back then? The first floor walls are blown in insulation with a mix of drywall and original plaster walls.
Kevin
I doubt you had a capillary break intentionally installed back then. A capillary break is basically just a piece of water impermeable material placed between the top of a masonry wall and the wood structure of a house. The purpose is to keep moisture from wicking up the masonry wall and wetting the wood.
I’ve used pieces of HDPE (high density polyethylene) sheet for this purpose, mainly because it’s cheap and fairly stiff so it’s easy to slide into small gaps when doing a retrofit. Dana has often recommended EPDM, roofing membrane material. EPDM is more flexible, so a bit harder to stuff into small gaps, but it’s more commonly available at building supply places. Both materials will work well as capillary breaks.
Bill
Best guess: Like poured concrete (perhaps even more so), CMU blocks have a powerful capillary draw. If there isn't a capillary break between the footing and the walls, with closed cell polyurethane limiting the drying toward the basement, the only way for the moisture to go is up. With sufficient unpainted above grade exterior exposure (at least a foot, two feet would be better) it may be able to dry toward the exterior.
Rain/dew moisture in the brick veneer could be contributing to high moisture levels at that location too. If there isn't already weeps every third brick or so near the bottom course of the brick and vents every third brick or so at the top to create a convective drying drive adding them may mitigate the problem.
Thanks for the feedback Bill & Dana. There is a couple of feet of exposed block above grade, however being the NE side as well as the cedars that are planted which are obstructing sunlight, I'm not sure how much drying action it's getting.
As far as weeps go inside the brick. There are no weep holes in veneer. I doubt/haven't seen any kind of weep plate/sill or whatnot. Any concerns with putting weeping holes in the brick veneer around letting rain/snow in?
Thanks,
Henry
>"Any concerns with putting weeping holes in the brick veneer around letting rain/snow in?"
Weeps & vents are standard construction in plenty of rainy-snowy areas. The greater concern it keeping the insects out, which can be achieved with purpose-made inserts.
Understood and I've had a conversation around weeps and vents, the only catch is if they are installed during construction my understanding is that there should be a weep sill or something to allow any moisture/water to run out behind the brick. In the current brick, there is no weep holes so I'm pretty confident no weep sill. As part of a retrofit, would one need to be installed?
My concern is not to break the existing 'rainscreen'.
Is that a reasonable concern or am I over thinking this?
Henry
This is a good example of why more vapor permeable foam (eg, unfaced EPS) that allows more inward drying and results in drier block is better.
So you can dump moisture directly into the basement in perpetuity? No thanks. The block doesn't care if it's damp.
Run the numbers - it's insignificant. The block doesn't care, but the owner sure does.
Jon, I've been in plenty of damp basements, and find that owners prefer them to be dry. ;-)
>"Jon, I've been in plenty of damp basements, and find that owners prefer them to be dry. ;-)"
The rate at which moisture comes through the wall with even 1" of Type II EPS is comparable to what comes through standard interior latex paint (= "ain't much").
Jon R is right- it's insignificant in terms of what happens to the indoor RH in the basement, but makes a real difference in the moisture content of the wood in contact with the top of that wall. Even a tiny amount of ventilation with dry conditioned air from upstairs keeps the basement humidity in check, if diffusion through the foam is the primary source of moisture. In the "-A" climates leakage of high dew-point outdoor air in summer would typically deliver an order of magnitude or more moisture than a whole foundation wall would through 1" Type II EPS.
Adding photo of interior corner
Dana and Jon, I'm not a mechanical engineer so I'm learning these calculations on my own. In the interest of education, how does this math look to you:
Saturated block at 55°F = 0.45 in•Hg vapor pressure
Interior air 65°F, 45% RH = 0.27 in•Hg
Difference 0.18 in•Hg
1” EPS = 3.5 perms = 3.5 grains/hr per sf per in•Hg
At 0.18 in•Hg, that’s 0.63 grains/hr per sf.
Assuming 500 sf of wall area, that’s 315 grains/hr.
Assuming 5000 cf of volume in the basement at 0.08 lbs/cf, that’s 400 lbs of air. So the air is gaining a little less than 1 grain per cubic foot per hour.
1 grain of water per cubic foot roughly corresponds to a 1% increase in RH at room temperature. So as long as the air changes per hour in the basement exceed 1/hr there is not a problem. But if the air is changing less than once per hour, wouldn't the RH continue to climb?
So a trivial 1 pint per day that may or may not need to be removed. Compare that to the 8 pints/day that is attributed to an occupant. And to the value of reducing the chances of mold growing on the block and some of the odor making it into the interior.
Adding exterior photos
HgCanuck, Hopefully you've solved your problem by now. I've dealt with a similar issue in my 1955 brick/block home in Northern Virginia. Your story sounds like mine. Terrible smell and I also had moist moldy walls in a finished portion of the basement. Long story short, I believe you may be having moisture/condensation resulting from warm air escaping up the 3/4" gap between the plaster and brick, while sucking in cold air from your attic and through those soffits. That condensation inside the brick then leaks down into the top of the open (likely) block where it dries...slowly enough to smell up the place. I've lived in two old house built like this and finally solved the issue in the same manner.
Another source....if those are plastic or flexible metal vents in your eaves, I would check for rodents in the attic. Norway rats...they really cause a stink and can/will go down your walls into your basement block. I had this problem throughout....fixed this problem by removing those flex vents for rigid plastic soffit trim and vents. They climbed the exterior wall along the A/C lines, then squeezed into the soffit. Been there..done that...it's ugly.
I solved my moisture issue (and the rat issue) by crawling back in the attic eaves and foaming the top of the gap into the attic and then foaming the gap at the bottom of the wall (top of the block in the basement) where the warm air leaks up into the wall. Sealing the gap at the top of the basement wall made it significantly more comfortable. It also took care of most of the smell. Additionally, I had a waterproofing company seal the exterior of the basement wall with a mortar parge, apply a liquid waterproofing membrane over that, then installed a drainage board to a footer drain. That alone reduced RH in my basement by over 20%.
I just installed a two head Mitsubishi Hyper Heat Mini-Split which will help somewhat with any additional humidity.
Hope this helps. Some of this might not pass the 'smell' test of GBA, but it solved my problem and I've seen no ill-effects so far. I'll finish portions of the basement with 1/2" XPS glued to the block with rock wool in 2x4 walls.