Floor Assembly for Small Workshop

Hi all,
I’d like to build a small shop on a budget, maybe 20×20.
I’d prefer a plywood subfloor over a concrete slab but I don’t want to go to the trouble of pouring a perimeter foundation either. This structure will not be permitted.
Any cool ideas for simple and effective “outside the box” floor systems that stay closer to ground level than a building up on piers?
thanks for your ideas
GBA Detail Library
A collection of one thousand construction details organized by climate and house part
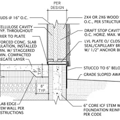
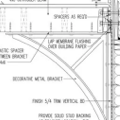
Replies
How is the building going to be supported?
There will be a base of compact gravel. From there I am not sure yet, I will look at the link you posted, thanks
A 20x20 building is going to need some sort of foundation
Agreed, what exactly that foundation looks like is what I am asking
Just to be clear the floor is not the same thing as the foundation. The foundation holds up the walls and via the walls the roof. In some construction the floor rests on the foundation as well but it can also rest on the ground.
You haven't said what climate you're in. The foundation always has to hold the roof and walls, and depending on climate may also need to hold snow on the roof and keep the walls from lifting in high winds. If you live someplace where the ground freezes in winter the freezing causes the ground to lift, the foundation needs to protect against that. If you are in an area prone to earthquakes the foundation needs to be reinforced for that as well.
Simple sheds can be built just on beams set on the ground, called skids. A 20x20 is probably too big for that to be practical. In agricultural areas pole barns are popular because they are cheap, cheap, cheap. Do a google image search for "pole barn collapse" to get an idea of what they are like. Helical piers are also a non-concrete alternative.
Otherwise I think you're looking at concrete, either footings below the frost line or a slab that "floats" on the surface.
Check out the shallow wood concrete-free foundation:
https://www.greenbuildingadvisor.com/article/minimizing-concrete-in-a-slab-on-grade-home
I'm doing something similar- my plan is ~8" of glavel carefully compacted and leveled, poly vapor barrier, then 2 layers of 3/4" advantech screwed together (seams staggered, top layer at 90 degrees to the bottom layer). Considering a layer of epdm between the glavel and poly to help resist abrasion.
Cool, I have seen someone do this, worked out nicely. I think he said he used a top layer of sand before the vapor barrier.
Joe, more information would be helpful. That said, I've designed sheds with 6x6 landscape timbers for the perimeter, backfilled with crushed stone and topped with stone or concrete pavers, or bricks. You could lay sleepers or joists on the crushed stone instead. No guarantees, just an idea.
Joe,
I fairly regularly get requests to convert accessory buildings into other uses - B&Bs, bunkhouses, etc. It's often difficult to impossible because they had been built under the premise they either didn't need, or the owners didn't want to get them permitted.
Right now I'm also almost a year into trying to get a building permit for a new house on a property which had five older buildings built without permits that need to be brought into conformance before the house plans are approved (two will probably end up being demolished).
While I can see circumstances where an owner might decide not to get permits, I'd never advise building something that can't easily be made to meet current codes.
Can you tell us a little more why you'd prefer a plywood subfloor?
Just throwing this out there - if you think an easily formed foundation is trouble, you're going to be in for a world of hurt. No disrespect, just think about it a little more before you rule out any options.