Slim ducted heat pump system design for house that’s not very open

I would love input on my proposed heat pump system design using 2 concealed ducted units (e.g., Fujitsu, Bosch or Carrier), each with a plenum.
I’ve attached an image of the proposed design with manual J results
Some context:
– Whole house load is 32K BTUh
— If include other equipment loads (i.e., ventilation loads), add another ~6K for a total of 38K BTUh
– I’m proposing one unit for zones 1+2 (unit A, 17K BTUh +additional 3K if include ventilation loads)
– I’m proposing another unit for zones 3/Fl2 +4/attic (unit B, ~15K BTUh +additional 3K if include ventilation loads)
— The units will be slim, concealed ducted units with plenums made
– Walls are currently open, so ducts can be hidden
– Attic will be conditioned
– I’m using https://ashp.neep.org for heat pump selection, zone 4a, 10 degree design temp
– I’ve struggled to find an HVAC contractor who will problem-solve in this way
***
Does this proposed design seem reasonable? More specifically:
– a) Are my 2 heat pump unit sizes reasonable?
– b) Should my unit choices accommodate the additional equipment heating load (ie ventilation loads)? In other words, should unit A = 17K load or 20K load (+3K to reflect ventilation loads)?
– c) Are the lengths and number of these ducts off of each mini split reasonable? (up to 15-20 ft)
– d) How do I determine the right duct diameters per run?
– e) In zone 1, will conditioned air successfully move across and past the kitchen from the register shown (~38ft, assume good insulation)?
– f) Are the return locations ok?
Thank you!
-Luke
GBA Detail Library
A collection of one thousand construction details organized by climate and house part
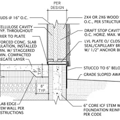
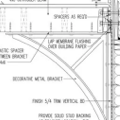
Replies
Here's my full manual J report in case it's helpful / interesting
Consider moving the zone 3 unit into the office closet. This dose 2 things it gets the fan noise away from the master bedroom and shortens the duct runs.
The smart move is to keep the units and ductwork below the ceiling and avoid conditioning the attic so you can cover the smaller attic floor with a thick layer of cheap fluffy insulation. This also put the return in the central hallway.
Avoid the flex duct if at all possible.
Consider slightly under sizing for you heating load and adding some strip heat for use on the coldest days. This let the unit get more run time at it highest speed when it make the warmest air and give it a lower lowest speed so it cycles less often under the light loads.
Walta
Thank you so much, great suggestion re: zone 3 and the closet.
Do you believe that the register in zone 1 in the kitchen can sufficiently cover all of zone 1—i.e., can the heat from that register reasonably "travel" to the end of the space, approx 38 ft?
The heat load for that space is not very high, but it's a decent "convection distance" and the ceilings are vaulted (though this technically accounted for in the manual j)
Luke
I agree the laundry room needs a duct. The question is how can you get one there.
Consider putting the laundry equipment in the bathroom it will feel more spacious and moving the exterior door closer to the kitchen.
Work on the spots where the doors can hit each other.
Walta
I was wrong when I said office closet. I think the air handler should go in the space over the stairs with the blue square in this photo.
Is the office closet necessary it seems awkward so close to the door and window?
Walta
That blue square would be great, but it's a slanted ceiling due to the stairs going up to the attic (imagine that the stairs shown go to the attic and right below is are the stairs that bring you up to the second floor, that's not represented well in the image).
I could potentially move the blue square forward in that hallway and have a drop ceiling hide the unit.
I was considering putting the unit in the attic and running the ducts down to avoid that (I plan to condition the attic w/ insulation against the rafters, I'm willing to absorb the costs I was quoted (not terrible), and the ceilings are very high, so the attic can become a nice, usable space).
(re: the awkward closet: it was already in place :/ , but agree maybe it's worth moving)
A:
If your ManJ is accurate, you can size the heat pump right for the load, no need for extra safety factor as ManJ itself is conservative. Make sure to check the performance of the units at your outdoor design temp. 10F is not too cold but you still need cold climate units with vapor injections compressors. You can always add a bit of resistance floor heat to the bath and kitchen area which would get you a couple thousand extra BTU of heat as a bit of safety factor.
B:
Ventilation loads are part of your heating load so unless you install a duct heater after your ERV, you need something to supply it. Simplest is to size your heat pump for that extra load.
C:
Duct length doesn't matter, what matter is the pressure drop across the ducts. No way to know unless you do the calcs. As a ballpark, 20' is not an issue with hard pipe if there are not any ugly bends. You can also go much longer than 20' as long as the ducting is large enough.
D.
Manual D. No way around it, you need to find the equivalent length of your planned duct runs and size the diameter so pressure drop is bellow (about 1/2) your air handlers capability.
E.
Nope. Too far unless you get high throw register which require a lot of static pressure. You also don't have any feed to the bath at the end. The bath could get floor heat though, so might not be needed. I would run a duct above the cupboards to the dining area.
I would also put a supply register into that outside corner of the living room.
F.
Mostly. I'm assuming the return is run to the living room, not the pantry, won't work from there. The slim ducted units are quiet and generally fine in a hallway but might be noticeable in the living room. You can put the return there, just make sure there is at least one bend in the duct and use duct liner to reduce noise.
Sorry I assumed this were new construction plans not something existing.
I assumed the blue square was dead space over the lowest part of the stairs and you could make use of the space.
The way I see it putting equipment and duct work in the attic is like shooting yourself in the foot on purpose. Moving the insulation to the roof line and gables will have a much larger surface area 50-100% larger generally. In the very unlikely event that you apply the same R value to the roof line it will lose 50 -100% more energy forever. Putting the insulation at the roof line all but forces you to use close cell spray foam that cost 10 times as much per R per square foot. For a song and a dance, you could cover the attic floor with R60 of cheap fluffy insulation. Most of the spray foam jobs get quoted at 4 inches or R28 when the job is done and they probe a few spots they find 3 inches at R21.
I don’t see how a conditioned attic ROIs it seems only slightly better than the stupid idea of putting equipment in a vented attic.
Walta
Thanks for all of your input! I see your logic and understand the argument. I think there are folks like me who attribute a lot of weight to having an attic be a usable, livable space, especially if you have a tall and spacious attic—that's worth something, in my view, a lot.
My assumption is that once you put fluffy insulation on the floors, you've essentially eliminated the option of making that space usable. Is this a wrong assumption? (If you put fluffy insulation on the floor and don't insulate the roofline at all, then your attic temperatures sway to extremes, making it unlivable / usable for big chunks of the year.)
Is there a viable path where you put in fluffy insulation like you suggest on the floor, cover it with flooring, and then ALSO insulate your roofline enough to make it livable/usable throughout the year, but likely less aggressively than had you only insulated the roofline to save on cost? I don't know if there's a major risk to this approach that I'm not considering (e.g., big humidity risks).
If one day you convert the space removing low-cost light weight insulation will be the fastest and easiest part of the project.
Making the attic in an existing home code compliant energy efficient living space is very expensive. When I have seen it done on a budget the results were neither compliant or efficient. Problem number 1 is the old ceiling joists were sized to support a drywall ceiling as 5 pounds per square foot not the 40 pounds required for habitable space so now you must install a floor system that is 6 inches taller than then the existing joists. Problem #2 a compliant stair case takes a lot of space 4’x12’ from existing rooms down stairs and trashes the current floor plan. With the new floor how big will the room be if you only count the space with 8 feet of head room? 6’x50? Now you want windows and more head room so you rip off the roof and rebuild it. Air sealing half story building is a nightmare.
Having an unvented unconditioned air space between two layers of insulation is a recipe mold and rot.
Walta