Seismic Integrity of Clay Floor over Foamed Glass Aggregate Base

Hi all,
Does anyone have any experience with earthen clay floors? I’m hoping to install the clay floor over expanded foam glass aggregate (with robust vapor barrier in between). I’ve attached a detail, I believe this assembly addresses any thermal, air/vapor, and bulk water issues. Other than the expected maintenance and upkeep of the clay floor, am I missing any performance or durability issues?
One issues I’m curious about: Most slabless slab assemblies I see on GBA use plywood sub-floor, which should help balance the lateral load on the perimeter wall. Since there is no lateral support in the form of a concrete or wood floor diaphragm in my assembly, is it at undue risk from seismic events? We are in seismic zone D2. The unbalanced backfill height on the perimeter wall is 2’, so I’m hoping to use prescriptive code to guide rebar reinforcement. Does this assembly make anyone nervous?
Thanks for your thoughts! (Climate zone 4 marine, Seismic D2, frost depth 12”)
Adam
GBA Detail Library
A collection of one thousand construction details organized by climate and house part
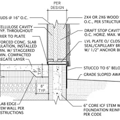
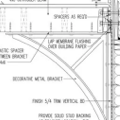
Replies
Adam,
- Stem-walls which are back-filled on both sides are laterally supported. I don't see any seismic concerns (beyond that we will all disappear no matter how well our houses are built in a strong shake).
- I don't know much about foam-glass, but I think it needs to be topped by a layer of sand or fine aggregate for leveling.
- Is your stem-wall really the same width as your wall framing? If not you may consider moving the plate in so that the sheathing and wood insulation are protected at the bottom by the concrete below.
Thanks Malcolm,
My thought with the backfill was that it would effectively be unbalanced since the foam glass is so lightweight, but perhaps after compaction it provide an equal resistance to inward pressure.
That’s a good idea to protect the sheathing and exterior insulation. One of our goals is to minimize concrete, but adding a 1/2” thickness will hardly matter and will at least protect the sheathing. Do you leave a gap between the bottom of the sheathing and the concrete to create a capillary break?
Adam
Adam,
Although it's light, the fill is compacted like any other substrate so it will resist lateral forces.
You can either keep the plywood and exterior insulation up 1/2", or extend the sill sealer underneath them.
Hello Adam,
We did an earthen floor in our house a few years ago. Our assembly was 12" of lava rock for capillary break and insulation, vapor barrier, 3-4" of road base, then ~2" of earth floor. The thinking with the road base is that it was something cheap we could compact to a very level surface to make troweling on the mud easier. I'm not sure it was worth the effort. Your detail looks like it would work to me but I'm far from an expert. Make sure you compact your base layers well.
We're pleased with the floor so far. It's beautiful. It's also quite hard...I think of it as similar to a hardwood floor in this respect. Our one regret was not using a wax on top. Ours is unwaxed and it stains easily. Not great with our young children. I believe these stains will be reduced with a maintenance coat of oil but we haven't yet mustered the energy to move all our furniture to do it.
Check out Crimmel and Thomson's Earthen Floors book if you haven't already. We used Sukita's oil for the top and were happy with it, though it was expensive.
We like the floor but probably will do a linoleum floor in our next project. Good luck!
Good to know about the wax. We have 3 little boys so I’ll be sure to add that. Would you feel comfortable with a waxed earthen floor in the kitchen?
Adam
Other options would probably perform better. That's where the most staining is in our house. I haven't lived with a waxed floor so I'm at the end of my knowledge.
I have no experience to offer but am VERY interested in this topic and ways to reduce the use of cement in general.
Are there specific building code issues we should be aware of? How do building departments respond when they see proposals like this? How do we present the material in a way that satisfies their concerns?
For owner/builders, are there ways to get this through without having to resort to stamps from architects or engineers?
As a way of further reducing concrete usage, are rubble filled trenches with a concrete "bond beam" an option in at least some locations?
It wasn't a huge issue for our building officials. I always talked about the hardening oil you finish it with, and described it as being similar in many ways to a linoleum finish. Also giving the concerned official a copy of a book on the topic could be helpful. I think having an architects stamp on the plans smooths the way. Check out the slabless slab BS and beer for other alternatives:
https://www.greenbuildingadvisor.com/article/the-bs-beer-show-concrete-free-slabs
I’ll let you know how the code officials respond when I present it to them!
Deleted
The stability will depend on the loads the footing and soils are expected to carry. At shear walls the width of the footing could be increased to add the needed stability or balance out the unbalanced fill. The geometry of the structure, location of shear walls and forces on each shear wall matter in assessing the stability. So I think to answer your question is - it depends.
Rubble trenches with a top bond beam are difficult to engineer in higher seismic zones. They typically don't provide enough sliding resistance or moment capacity for shearwall over turning.