Slab foam debate — contractor going bonkers

I want to do a slab on grade for the house that would consist of compacted AB, then 3″ of EPS 2.0LB rigid foam, a vapor barrier and then 4″ of reinforced concrete.
Oh boy, did I open Pandora’s Box!
One concrete contractor said my buildup will result in the concrete “shattering” and that I will get hairline cracks everywhere. He wants to put the foam UNDERNEATH 4″ of AB and no vapor barrier. He said I would have to sign off on waivers if I did my buildup my way.
How would one put the foam underneath 4″ of compacted AB? Is this normal practice? No vapor barrier?
GBA Detail Library
A collection of one thousand construction details organized by climate and house part
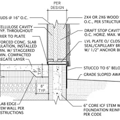
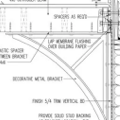
Replies
What's AB?
Stephen,
I thought, air barrier? Then -- must be "aggregate base."
Peter,
No - as you know from reading here for several years - that isn't normal practice. You have found a contractor who doesn't know what he is talking about. Don't waste time on this. Move on and get another contractor.
AB is aggregate base material
My 4" of foam went on top of compacted stone. Vapor barrier on top of foam, then 4" of concrete. Not one crack. You need a new contractor. And don't sign any waivers.
Peter L,
Whenever a contractor pops out of a time machine from the 1950s, I'm curious to know where we're talking about. Care to tell us where this anecdote occurred?
By the way, when you stop by the contractor's office to tell him that you're going to use a different contractor, you can drop off a printout of this article: Polyethylene Under Concrete Slabs.
Martin,
It's like pulling teeth. This contractor is fighting me on the buildup and claims he's been doing this for decades and that I am a novice and I don't know what I am talking about. I will of course be choosing a different contractor but I was not expecting such a fight and resistance on the slab buildup.
Doing it HIS way would result in a wrong build up but maybe the slab wouldn't crack but from a science standpoint, it would results in a wrong type of buildup.
So where do you live? Maybe you are willing to name your state or province?
Perhaps he would believe the NRMCA or the American Concrete Institute (note the cautions in both).
https://www.nrmca.org/aboutconcrete/cips/29p.pdf
https://www.concrete.org/Portals/0/Files/PDF/302.1R-15_Chapter5.pdf
Don't provide a link and not be prepared to defend it. From the ACI: "When placing concrete in direct contact with the vapor retarder/barrier, the potential effects of slab curling, crusting, and cracking should be considered." I dealt with this doing commercial and industrial construction for years. I'm not saying that the OP shouldn't place the slab directly on vapor barrier. That is probably the correct thing to do in a house. I've had engineers call for it the way the contractor proposed. There's more than one side to every construction condition.
Joel,
Placing concrete on an aggregate base provides more latitude to the contractor, especially when the batch plant delivers wet concrete. But the solution is to insist on concrete that isn't sloppy.
Contractors now have many years of experience placing concrete directly on polyethylene. In most parts of the country, this approach is routine -- and the resulting slabs are (for the most part) not plagued by curling or "shattering" (whatever that means).
So would a 3/4" or larger aggregate with no water added be the best for the house slab?
Do garages require a vapor barrier in a dry climate?
Peter,
As my article (Polyethylene Under Concrete Slabs) indicates, here are the layers you want, from the bottom up:
1. Crushed stone (no fines).
2. Rigid foam.
3. Polyethylene.
4. Concrete.
Here in Vermont, most contractors specify 3/4-inch crushed stone, because it is relatively easy to rake. Larger crushed stone would also work, as long as the contractor has the equipment and expertise to level the stone.
In my opinion, every house slab or garage slab needs polyethylene directly under the slab, no matter what the climate is, for the following reasons:
1. Many people who believe they live in a dry climate have ended up with an undesirable damp slab, because of local soil conditions that they didn't thoroughly understand before the slab was placed.
2. Garages are sometimes converted into living space.
3. Polyethylene is cheap.
4. There is only one chance to install polyethylene under a slab. If you get this wrong, you can't fix your mistake later.
Do most contractors compact the 3/4 stone? We were planning a polished stone slab for our finish floor. Our site guy spread the stone and thoroughly compacted it. We put 4" of reclaimed XPS, poly and the usual steel mesh. The floor polishing guy suggested 4000 psi concrete and pea stone aggregate. I don't know if it was the compacting, the concrete mix or just luck, but the slab is two years old and we have zero cracks.
Stephen,
Some materials, like pea gravel and 3/4" clear-crushed rock, are seen as self-compacting, but even aggregates that can't technically be compacted need consolidating.
You intuitively know the difference from putting bulk foods in jars. If you buy too many oats you can squash them down a bit to fit. Almonds you need to tap the jar until the voids are minimized.
All substrates benefit from compaction or consolidation - as your beautiful polished floors testify.
Get a new mason. The slab over the foam will be LESS LIKELY to crack. Mine is pristine over ten inches of compacted #2 crushed stone, then 2.5 inches EPS, and then poly. I sued 4000psi concrete and not one crack a year later.