Slab floor addition, add insulation/subfloor, not much height

Greetings all.
I’ve been researching so much, and things are becoming more muddy than clear. Maybe someone can help me. I’ll try to keep it simple.
– live in Western Washington
– adding one room addition on slab. Exterior done, now focusing on interior (approx 300 sq ft)
– slab (mono pour) has gravel/6 mil underneath and R-10 2″ EPS on outside
– slab poured last summer and closed in all winter, so good and dry
We have about 1-1/4″ allowance to add to floor before we run into height transition issues
Wondering…
1) is it worth adding 1/2″ rigid foam and 3/4″ subfloor for additional warmth and “cushion”
2) I’m considering layering like this: slab, polyiso, 3/4″ TG osb or ply, with 8-10 tapcons per board.
3) do I need 6mil under rigid foam?
4) 1/2″ Polyiso is avail at box store. Could prob get 1/2″ xps at lumber yard. Is one recommended over the other?
Any tips or recommendations? I’m a DYI gal who loves home projects. Built attached garage a few years ago, and small studio in backyard. Now into this “big” project and want to do it right, and keep the inspectors happy 🙂
THANK YOU for any expertise you can offer. I really appreciate it.
Kris
GBA Detail Library
A collection of one thousand construction details organized by climate and house part
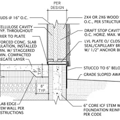
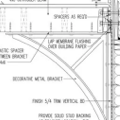
Replies
Kris,
It's too bad that you didn't think of installing a continuous layer of horizontal rigid foam insulation before the slab was poured -- under the slab is where it belongs. But it's evidently too late for that.
If you are able to install rigid foam insulation, go for it. Of course, 1 or 2 inches would be much better than 1/2 inch. Only you can decide whether the advantages of only 1/2 inch are worth all the expense and hassle you describe. From an environmental perspective, either EPS (the denser, the better) or polyiso would be better than XPS. For more information, see How to Insulate a Basement Wall.
The best thing to do is dig 2" deeper and install 2" of EPS under the slab, with a vapor barrier between the EPS and concrete. Has the slab already been poured?
At 2" EPS is only R8.4, not R10. XPS is R10 @ 2" but only for a few decades. As it loses it's climate damaging blowing agent it eventually ends up at R8.4.
If the slab is already poured, foam over the top of the slab is still a good idea from a thermal point of view (especially if you're installing a wooden subfloor) but it doesn't offer any more "give"- it's still a very firm floor, much firmer than subfloors on joists or sleepers.
Using polyiso under a subfloor is somewhat risky, since it can potentially load up with moisture, but would provide better thermal break than half-inch XPS for keeping the subfloor wood dry. Since you have 6 mil poly under the slab it's pretty safe to go with polyiso, which is also much greener than XPS. Give a foot or so of overlap between the seams of the subfloor and those of the rigid foam. If you use t&g subfloor and the slab is pretty flat you can just glue the foam to the slab (with foam board construction adhesive), and the subfloor to the foam without too much risk of "potato chipping" waves forming with seasonal moisture changes in the wood.
In western WA the seasonal changes in the wood dimensions are much smaller than in most of the US where the wintertime & summertime outdoor dew points can vary dramatically. In your area the mid-summer dew point averages are under 55F and wintertime dew point averages north of 35F, which is a fairly tight 20F band. East of the Mississippi most locations see seasonal dew point swings of 50F or more. Your deep subsoil temps may be lower than your mid-summer average, but with R3 between the subfloor & slab the bottom of the subfloor the wood will always be above the room air dew point (unless you actively humidify the room air above 50% RH for months on end.)
THANK YOU BOTH for your quick responses. So very helpful! One follow-up: do I need vapor barrier between the rigid foam and the slab?
I may see if we can eek out going with at least 3/4" poly ios (if available). Yeah... We asked our concrete foundation guy about insulating underneath slab and we're kind of given the "overkill" look. We did insist on the exterior rigid insulation... So guess we got part of it right :) We learn as we go. Thanks again! - KRIS
Kris,
If you already have 6 mil poly under your slab, you don't need any 6 mil poly on top of your slab.
The big orange & blue box stores tend to carry Dow Tuff-R or Rmax Thermasheath polyiso. Half inch and 1" goods are almost universally available, but many will also have 3/4" (R5-ish) versions at about $18-20/sheet. McLendon Hardware (multiple locations in Pierce or King county) usually has some vendor's polyisocyanurate in a range of thicknesses too. I'm sure you'll find some. Distributors catering to the building trades would have it too, often at a better price, if they have it in stock.
There are literally dozens of polyiso manufacturers in the US, and any of them (with any facer type) is good enough for your application. It'll range from R5.5 to R6.6 per inch in labeled performance, and in your application it will perform at or above the labeled R value.
Thank you! Thank you! Sending some "virtual chocolate chip cookies" to you both :)