SIPs vs. panelized vs. stick built in CZ 5A

At the planning stage of a house build in Yancey County, NC. Climate zone 5A, 3000 ft elevation, 52 inches annual rainfall, 13 inches snowfall, rarely drops below 0. One lane gravel road for access, limited to 10 foot wide loads, so modulars are off the table. One story over a basement on a sloped lot, I was thinking SIPs would let me use the attic space as controlled air space for an office and guest room, but some people in this forum have cautioned against SIPs. I’d consider accessing the attic space through a side door over the attached garage, to avoid a ceiling penetration, but did want a bathroom at that level if I make it an office and guest room.
Given these parameters, what are arguments for or against SIPs ( or Thermobuilt.com, any experience?) , panelized, or stick built? Local crews would be most familiar with stick built, but one builder I talked to has gone to SIPs training.
Looking for low cost per square foot, and good airtightness.
Thanks, Steve
GBA Detail Library
A collection of one thousand construction details organized by climate and house part
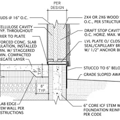
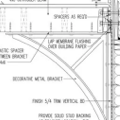
Replies
I am a SIPs guy. Built a major addition on my house 20 years ago and have had no issues. Used a SIP builder for the shell. He delivered and erected the shell all precut. Crew traveled and put it up in four days. I hired the subs for the rest of the work.
All sips are not the same. I think that can make a difference. My panels were based on 8X24 SIPS. Many builders use 4X8 SIP which are locally produced. Many more seams, more chance for error. My SIPs came from Insulspan, a national producer.
I do not understand why you would pay someone to work for months building a multi layered wall system with recurring chance for errors. Put up SIP, windows,,doors, roof, ready for siding in 10 days tops.