SIP overhang/soffit – Waterproofing

OSB 8″ thick Polyurethane roof SIP that overhangs the wall by 24″ – I am using peel & stick Ice & Water membrane to waterproof the roof and this roof SIP.
The build-up: For the 24″ overhang/soffit, I am looking to just continue with the peel & stick/Ice & Water membrane and wrap the overhang, fascia, and underside of the SIP soffit with the same peel & stick membrane. I will then use 26 gauge aluminum to cover the area to provide protection.
The soffit doesn’t need to be vented of course because it is a SIP and the peel & stick membrane provides the waterproofing.
Does anyone see a problem with this build-up?
GBA Detail Library
A collection of one thousand construction details organized by climate and house part
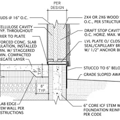
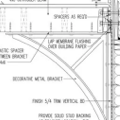
Replies
Peter,
I can't think of any logical reason to wrap the underside of a SIP soffit with a peel-and-stick membrane.
If you do as you propose, you will be locking in the moisture level of the OSB facings on the SIPs. Whatever moisture content these SIPs have on the day you cover them, they will have forever.
If it rained the day before you did this work... well, let's just say that you might want to wait for the dryest day of the year to do this work.
Or perhaps you might want to rethink your plan.
Use a proven design. Dreaming up unproven designs is an expensive experiment. Armchair engineering is just that. I run into the same armchair group in the homebuilt aircraft world, a few fly a lot crash...
Like everything discussed herein, success and risk for your proposal is climate-dependent. Joseph Lstiburek, in Builders' Guide to SIPs for All Climates, cautions against use of peel-and-stick: "The general rule for fully adhered impermeable membranes applied to the exterior of a typical SIP is that in hot-humid climates you can use them without restriction. In all other climates, you are going to have to do some hygro-thermal analysis. In residential occupancies, without humidification (i.e. controlled ventilation and interior RH controlled to 35% or lower during the winter months), fully adhered impermeable membranes will work in mixed humid climates, but not in marine climates and not in cold and very cold climates... This general rule also applies to roof SIP assemblies." (page 115.)
This concludes a chapter on the unique water vapor resistance properties of SIPs, and of course the incredible vulnerability caused by those pesky joints. He doesn't address a scenario in which roof SIPs are entombed at the overhang with peel-and-stick. To me, it seems like you're unnecessarily reducing some drying potential. If you really want the protection under the eave, why not switch to a liquid-applied weather-resistive barrier, which retains some permeability? Carry the LAWB clear down to the foundation, and you've got the best protection for SIPs money can buy.
Safest rigid foam roofs are vented.
The ice and water shield helps with external moisture but captures internal moisture.
SIP joints need to be bullet proof. Triple seal.
Venting above mitigates joint failures also minor external moisture build ups and leaks and capillarity issues.
My new plan is to run the peel & stick Ice and Water membrane on the SIP roof down to the 24" SIP overhang and down to the fascia, terminating just 2" on the underside of the soffit lip. Underneath the remaining 22" of SIP/soffit I will use Prosoco R-Guard CAT-5 LAWB. This will provide the waterproofing/air barrier under the SIP soffit area.
This is for a Zone 4B (high-desert) climate build.
I always thought peel and stick anything was a bad idea for any structural material/element in house construction. Why would you sandwich your roof deck (the compression flange of your SIPs) between air and water tight materials? You have no idea what and how moisture and vapor will make their way along seams and joints and migrate across your deck. Why not use something with a modicum of permeability just in case the sheathing needs to dry. Play it safe. Ice and water shield and Prosoco R-Guard are not needed in your application. They seem to be well meaning but overkill.
Flitch,
When installing a standing seam metal roof onto a SIP roof, you will have ZERO permeability, no matter what type of underlayment you install. So installing a permeable underlayment like building paper will only CREATE problems. The reason is simple. If water penetrates the metal roof somehow and hits the building paper, the paper will soak up the moisture and the OSB on the SIP will get wet. Once the moisture is in, it can NEVER get out because the SIP cannot dry to the inside nor can it dry to the outside due to the metal roof preventing it. The building paper will only exacerbate the problem of the SIP OSB rotting.
By installing a peel & stick membrane on the SIP and then installing the metal roof, it protects the SIP from any moisture intrusion from the outside. If water finds its way behind the metal roof, it will hit the peel & stick membrane but the water will not penetrate the membrane, thereby protecting the SIP from water damage. No water gets absorbed into the OSB SIP with a peel & stick membrane. The same could not be said for a permeable underlayment like building paper.
Interior moisture and/or vapor will NOT find it's way along the seams and joints of the SIPs. One must use numerous techniques in order to prevent this (T&G panel joints, joint gaskets, SIP tape at joints, etc). Interior air/vapor leaks through the SIP joints is what causes problems like SIP rot. Preventing this is what solves the problem. The Alaskan SIP Rot study clearly showed that the problem was NOT exterior water penetration but INTERIOR water vapor penetration at the SIP joints. The roof SIPs that were properly air sealed on the interior showed ZERO problems even when they had vapor impermeable exterior roofing materials installed.
Studies have shown that roofs do NOT dry to the outside when one applies metal roofs, asphalt tile, or any roof finishing material that is basically vapor impermeable. Roofs dry to the inside in such cases BUT when it comes to SIP roofs, they CANNOT dry to the interior because of the 6"+ of closed cell polyurethane/EPS which creates a vapor impermeable underside. Therefore, you have a panel that CANNOT dry to the inside and/or the outside. Why then apply building paper and create a bigger problem?
I've studied this for months now, called numerous SIP companies, including SIPA. They all conclude that a peel & stick membrane on the exterior roof SIP is the way to go. Plus very diligent interior sealing of the SIP joints to prevent any air leaks.
Peter .... seems to me we circled around some of this before ... and might still agree to disagree. My objection to air and water tight membranes on the outside of the roof deck are precisely the reasons you raised in this post: moisture inside the panel , moisture behind the ice and water shield.
If you have any interior moisture problems in the OSB, the ice and water shield will prevent drying.
No matter what type of roof. We all agree on this, I believe.
So this says to me: (1) don’t run the risk of an impermeable bulk water barrier membrane, (2) and don’t run the risk of an roof covering (or assembly) that prevents drying if drying to the outside is perchance, needed.
As we discussed one other time, flush fitting steel roofing to a deck is not recommended as it l prevents outward drying. And outward drying will be needed if you use steel. Steel roofs always condense on the underside. If the steel is flush fitted to the deck, the surprisingly significant quantity of condensation forms there (underneath) will pool and spread by capillary action.
So, instead of a double water and air tight impermeable barrier (steel plus ice and water shield), I would put the steel on purlins, over a semi permeable bulk water barrier. This way I manage the inevitable (i.e. the inescapable) condensation and protect my OSB if it should (and it will) get moisture behind the building paper and need to dry to the outside.
That gives the best of three worlds:
Drying off under the steel by evaporation and convection; to release vapor at the perimeter.
If any moisture arrives to OSB compression flange from above, it can dry out.
If any moisture gets to the OSB from the back, which is as you say, SIP systems Achilles heel, it has a pathway to dry.
I appreciate your aim of the perfect sealing job. And I agree, that it is possible for the bulk water sealing to be perfect (and remain that way for a few years). But as you related, that does not account for the main moisture problems challenging the assembly of modern houses and SIP houses: (1) condensation where ever there is a dew point and (2) upward vapor drive of buoyant , stack effect and upward positive pressure inherent to the physics in buildings. That is why I dislike peel and stick and raise my steel on purlins.
You said this: "...you have a panel that CANNOT dry to the inside and/or the outside." If that is true, there is an inherent fault in the design. Building paper does not allow bulk water in, it allows vapor out.
If you re-read your explanation, you are actually making the case for permeability. The last thing you want to do to your OSB is seal it up vapor tight.
Flitch,
We will have to agree to disagree with the build-up because of many problems with your build-up scenario. I think the confusion that is coming into play is that you are approaching this as if it was a standard truss roof with OSB sheathing. I am taking about a SIP roof which is a different animal altogether. By approaching it with your build-up recommendations you create other problems which I will mention below.
By using purlins you created extra problems to the design that were not there before:
1 - Most standing seam metal roofs with hidden fasteners CANNOT be attached with purlins and MUST be attached directly to the roof sheathing/OSB SIP surface. This is also in-line with the 2006 IRC and 2012 IRC. Unless the metal roof is of a special design for applications over purlins rather than decking.
2 - By using purlins you create a pathway for wildfire embers to enter and start a fire. I'm building in wildfire country and having a pathway for thousands of embers to enter and smolder underneath the metal roof and the OSB is a house fire waiting to happen.
3 - By using purlins it creates a pathway for flying termites to enter and devour the OSB sheathing.
4 - Purlins create the problem of "telegraphing" as stated by the metal roof company.
5 - Standing seam metal roof with hidden fasteners requires installation directly onto the roof sheathing as per the installer.
I appreciate your input but as with anything, there are many different opinions on how to skin this cat.
This metal roof underlayment provide airflow under the roof.
http://www.roofaquaguard.com/products/RoofAquaGuard-DRY-TECH/
Peter, details matter, following your last post, I agree you are doing the right build.
I also agree with Flitch for where I live, wet, snow, no huge bug a fire problems and.... most residential homes of average cost use lumber yard steel roofing that can be set on purlins verses the nicer clip style that we do use on top shelf projects.