Siding and Insulation Help Needed – Pics Added
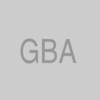
Midwest (zone 5b) ranch home (1500 sq. ft.) built in 1974.
Existing condition
– 2×4 fiberglass bat filled walls
– black fiber board sheathing (no WRB or felt)
– Original T1-11 cedar plywood siding (tested small amount of lead present in paint)
– Some sort of thin flexible WRB with foam insulation… prob not flashed properly judging by the quality of what I have seen so far
– Vinyl siding on top
– Aluminum flashing around most of the trim/windows/doors
– front of home has brick veneer instead of vinyl
– Existing windows are (5 total) 60″x 48″ double pane horizontal sliders and a couple smaller ones…that are in decent shape.. but as expected probably leak a good amount of air
Vinyl seems to sagging in some areas and poorly installed. Mainly in soffit and fascia where the weight is starting to pull old nails out and fascia is probably getting a good amount of water behind aluminum flashing
Goal – Would like to install LP SmartSide instead of vinyl and if possible without too much $/labor add some insulation and air tightness.
Not aiming for passive house…. just a boost of performance without getting too crazy.
Options
Sheathing
Seems fiberboard handles moisture well and helps with sound (near a busy road so that is a plus). Plus adds a bit of R-value.
Assuming leaving this in place would be wise.
Original siding
With having large overhangs and some sort of WRB in place.. I’m hoping the original siding isn’t in too bad of shape.
Thinking maybe should leave in place if no rot?
Insulation / New Siding
This is where the many options gets daunting.
Cheapest and easiest option I am guessing would be:
-Remove vinyl
– Install a proper WRB – maybe fluid applied type onto original plywood siding?
– Add minimum amount of exterior foam – 2″
– rainscreen
– Install the LP SmartSide
I know the optimal solution performance wise (for sides and rear of home), would probably be:
– install 4-6″ of exterior rigid foam on top of original siding
– move out windows/doors (replace with better units?)
– WRB and rainscreen
– LP SmartSide
My concerns for this option is cost.. and time. Also some details like bumping out the electrical/gas meters, attached deck in backyard, extending foam into ground around basement walls, etc.. but would provide a large upgrade to building envelope.
Is there a middle of the road solution?
What would give a boost in performance without driving up cost and labor too much?
Would adding interior insulation instead of exterior be a good option in this case since the front of the home is brick?
And if adding interior insulation, what would be the best option for this existing wall assembly?
What method/option do you think would work best?
Vented attic will be R-60 cellulose
Basement walls will be R-20 unless extending exterior foam down
GBA Detail Library
A collection of one thousand construction details organized by climate and house part
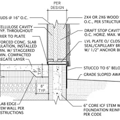
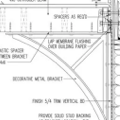
Replies
Hi Davin,
If you have photos & diagrams, that would really help. Not sure exactly the picture you're painting with words.
Just a note, my advice is to not try to reuse the existing siding. Taking it off to then put it back would just be a nightmare, or at least in my dreams.
Sounds like you have a hot mess on the outside. If you're ok with the look of the exterior, Maybe consider an interior approach? Demo drywall, airseal from the inside (maybe even aerobarrier), and upgrade insulation. Maybe even, dare I say, spray foam the interior? but that's expensive, bad for the world and not necesary, but it's fast. Also to note, In my parts, drywall crews are generally cheaper than siding crews, to the tune of around half.
Just a thought.
Also note you'll need (or should have) a good ventilation plan if you plan to airseal. If you're going to block the outside, you need to control then inside.
If it was built in 1974, it probably has lead paint inside. I would not demo drywall or disturb the inside unless you're willing to pay for professional lead abatement and willing to not live in the house for the duration of the project. Plus you'd probably need to remove all the carpets and anything else that might catch construction dust. Just my opinion, I'm extremely cautious wrt lead. People, children especially, are susceptible to lead poisoning and do not recover.
I'd stick with improving air-sealing and insulation (and siding) from the outside.
Good point. The exterior had some lead when I tested so I would guess the interior does as well.
Is it possible to leave the existing drywall up, kinda like an air and vapor barrier and build out another stud wall on the interior?
First, the front of the house is quite nice. The deep overhangs also reduce the load and therefore risk on that front facade. I'd just leave it as is. If funds were infinite and you wanted better comfort inside, maybe, maybe replace just the front windows with something tighter that was also the same color trim as the bay and front door. Maybe.
The siding around back is...well, it's vinyl. Shrug. Replacing it would spruce up the look, but that's a lot of money. If you do replace it then it's a good opportunity to do a little air sealing. Exterior foam would be a good call if you were in Northern Minnesota, but probably overkill for Zone 5. Look at your energy cost and make the call.
Working from the inside could be a good option though if there are other things you'd like to address like closets or old underperforming electrical, or a kitchen remodel. Bonfiglioli aka Bonfig wall could be an option for upping the R value of the walls at the expense of 2" less floor space and new trim for all the windows.
Lead paint is certainly possible inside, but there's a good chance there isn't any too. 1974 was pretty close to the cutoff for lead paint and even then the lead paint was more often on the outside or just on the trim. But instead of guessing go grab a couple sets of those 3m lead testers and find out what you've got.
Andy, thanks for urging me to test the interior walls for lead. I just got done with three different tests and it looks like there is no lead that I have found so far! :)
I like the idea of using a Bonfig approach! But it looks like he uses 2x6 plus the 1" of foam, and 3/4" furring (1x3) for the R-30.
With a 2x4.. I suppose I could still do it, but would have to use more like 3" of foam and then a furring strip.
Adding 3-3/4" inches to the wall before gypsum for R-30.
If I didn't want to tear open the walls and remove existing insulation. What are your thoughts on just adding R-20 rigid foam the the interior wall of the front facade? The layers of taped foam would act as my air barrier and provide some vapor control. Having an air gap behind the brick, and fiberboard sheathing should provide good drying from exterior.
Would be similar in width to Bonfig depending on what type of rigid is used.
Then, on rest of vinyl walls.. if I remove and replace with LP siding.. add some external insulation (R-20 again) since the siding is off anyway
I added some photos. Go easy on the current condition. Have lots of work to do still. including tearing down the chimney, new roof/vents/fixing downspouts, etc...
Okay with the looks. If made some repairs, and painted the vinyl to match the brown we used on the front.
I am a bit worried about underneath the vinyl though. Not sure what they did for flashing, WRB, etc..
This is what I found when I tore apart the bay window. It did not have the foam WRB under the vinyl so along with that and being more exposed... maybe why original siding was in rough shape.
Judging by the black on the fiberglass.. seems to have been leaking a good amount of air through...
Cut out hole in original post was from drilling out fresh air intake for furnace at rim joist.
What do you think would be the easiest way to add exterior foam to the vinyl sided walls on the right rear side of home?
Thinking of extending the foam down below grade...2-3'
See attached pics.
The left side of the home from the four seasons room is the garage. So I would not likely add exterior insulation on those walls.. but would air seal and add insulation if needed at the dividing wall from inside the garage.
There are four windows - 60" wide by 48" tall RO, and a smaller bath and kitchen window that would need to be built out. My guess is they might have installed these when the vinyl went up. .. as they are not original..and look to be of similar age.
Four basement windows.. that probably should be built out and replaced (existing single pane sliders) with double panes...
Would it make the most sense to:
- leave the windows where they are
- WRB
- Rigid foam
- vented screen
- siding
Best detail for extending out windows in this case?
Would it be safe to say the windows probably have a nail flange that is installed on top of the old plywood siding?