Should we install a rainscreen in a 10″ wall assembly?

We are building a new home in SE Washington state with 10″ thick walls and wondered if we need to worry about having a rainscreen behind the James Hardi lap siding. We get 17-20″ of rain here annually and have heard conflicting thoughts about whether it is needed in this climate. We just don’t want to end up with any moisture in the wall cavity, but are not sure where it would come from. Here are the details of the wall assembly:
Benjamin Obdyke’s Hydrogap housewrap or Sto Gaurd’s liquid applied WRB over 1/2″ plywood.
Dense pack cellulose in the 10″ cavity of the double stud wall.
Drywall with vapor barrier primer (code requirement)
We typically get blower door numbers at or under 1 ACH, so shouldn’t have very much air leakage.
We are using an HRV for ventilation which tends to make the home even dryer in the cold months.
Is there potential moisture drive from the outside that we need to worry about? Does the liquid applied membrane allow moisture vapor to enter?
Thanks for sharing your knowledge and experience, it is such a help having professionals to draw from!
Mark
GBA Detail Library
A collection of one thousand construction details organized by climate and house part
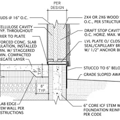
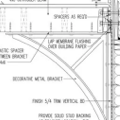
Replies
Mark,
To my mind, a rainscreen gap is relatively cheap insurance. A thick double-stud wall like yours makes the exterior sheathing colder (and wetter) than usual, and a rainscreen gap can help damp sheathing to dry out. For more on this topic, see How Risky Is Cold OSB Wall Sheathing?
Whether you are worried about rain penetration or the "cold sheathing" problem, the moisture comes from the exterior, not the interior. A rainscreen gap can help speed drying due to either problem.
That said, not every house needs a rainscreen gap. If you have wide roof overhangs, and if you have a one-story rather than a two-story house, your siding may never see rain. You live in a region with low rainfall, which reduces your risk. Ultimately, it's a judgment call.
Moisture sources
Vegetation near or contacting the home
Using the home in a moist way, not venting, plants everywhere, boiling water by the gallon w/ no lids........
Automated humidifiers gone wild
Manual humidifiers, users gone wild
Twenty year shingles that are forty years old...
Valleys that run into low pitch porch roofs...
Etc.... The list might be endless... Or not
My point.... If yaa build right and operate right, moisture issues are reduced or nil.
AJ,
I'm not sure why you think Mark is using OSB. In his original question, he stated that his wall sheathing will be plywood.
Mark, sounds like you are doing moisture mitigation right. The one upgrade I like is to stay away from OSB. Dry OSB is ok. Moist OSB is crap. PT plywood is much less vulnerable. And any good standard grade plywood is better to me than OSB. So think about upgrading your sheathing if anything.
Edit; time for a new seeing eye dog Mark and Martin. Plywood is in use, yeah.
Martin,
SE Washington get A LOT of direct sun. It's mostly high desert climate with big season temp swings. Might not a ventilated gap keep paint on the JH Lap longer and better?
Mark,
The "cheap insurance" for cold sheathing on a 10" wall is (in my opinion) a good idea. At that thickness, in SE WA the sheathing is going to regularly get cold. Venting the condensation that I'm betting will accumulate is a great idea.
I'm facing a similar problem but of course there are significant differences. I will have a bit thicker walls (11" cavity double stud) and a bit different exterior ( 1/2" thick brick using Ambrico EZ wall).
I opted against either OSB or plywood and chose 25/32" structural fiberboard because of it's much greater permeability (28 perms vs 1 or 2). I'll use Greenguard's 'C2000 high permeability house wrap taped and detailed as the primary air barrier. I'll use Greenguard's DC14 drainage mat (it is 1/4" thick XPS textured with drainage channels on both sides and has a permeability of 1 perm.). The low permeability DC14 prevents any moisture that is stored in the cladding from being driven inward when the sun shines and still lets the cellulose dry to the outside. The fiberboard and moisture permeable house wrap help quicken drying. I'm of the opinion that DC14 or equivalent is great insurance against moisture induced problems. the material cost for my 2300 sq ft one floor house is about $700. As a bonus the 1/4" of DC14 adds r1 to the wall.
Jerry,
You have described your wall assembly, but I'm confused by your opening sentence: "I'm facing a similar problem." What's your problem?
Jerry,
I'm curious what spacific structural fibre board you are using. Would you mind sharing a link to the product?
Martin,
Thanks for the reply, sorry about the delay in answering... Your article you mentioned was a good help to me, that is where we got some of the ideas for the details. I had read it before, but probably hadn't gotten the full good from it.
Have you or others seen or used the liquid applied WRB's much yet? Are they a good way to go from a longterm durability standpoint? They do tend to be more pricy, but may solve some of the problems with conventional housewraps if installed properly. re: sealing around fasteners, air sealing, etc...
Also, any further suggestions on rainscreen material besides rainslicker, eldorado batten or plywood strips? It is nice to have a somewhat solid backing behind the lap siding than plywood strips provide.
Thanks
Mark,
Q. "Have you or others seen or used the liquid applied WRBs much yet? Are they a good way to go from a long-term durability standpoint?"
A. Yes, I've seen them and written about them. By all reports, they perform very well. Here is more information: Housewrap in a Can: Liquid-Applied WRBs.
Q. "Any further suggestions on rainscreen material besides Rainslicker, Eldorado batten or plywood strips?"
A. Ordinary 1x4s work fine. Some builders use ripped lengths of Coroplast plastic sign-making material.