Should there be a drainage path to daylight behind exterior foam?

To make a long story short, should the exterior insulation be continuous from footing to roof. Or should there be a way for any potential moisture to drain out? The house and addition are slab on grade with frost walls, Zone 7.
We are adding exterior insulation to an existing home and a addition. Our original plan was to have:
2×4 walls with R14 Rockwool insulation
3/8″ plywood sheathing
Tyvek Drain Wrap
Innie Windows
Two layers of 1.5″ EPS
3/4″ Strapping
Hardie Siding
For the addition we have two layers of 1.5″ EPS foam on the exterior down to the top of the footing on the addition. This is approx 48″ below grade. We left approx 4″ above rough grade so we could tie into this once we added the remainder of the exterior insulation. Our concrete curb stops approx 6″ above finished grade. We were going to stop the insulation and install a custom made flashing that would go behind the Tyvek and allow moisture to come out if any got behind the foam just below the transition from wood framing to concrete curb. Should this be the case or should we just have the insulation be continuous from top to bottom?
For the existing home where we are tying in. Our plan was to bring a portion of the EPS foam below grade a few inches and then follow whatever we did with the addition. In both cases we were going to skim the EPS with a surface bonding cement. On this portion there will also be a concrete sidewalk installed after.
Let me know your thoughts!
GBA Detail Library
A collection of one thousand construction details organized by climate and house part
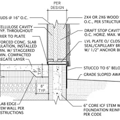
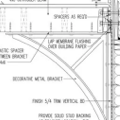
Replies
Chris,
I think it will help the forum members to see drawings or photos of the existing house and intended addition. Your use of the word "curb" is a bit puzzling. I suspect you mean the top of the poured wall. I am a bit concerned about the ultimate insulation value of the two layers of EPS down the sides of the foundation. Wet insulation doesn't insulate well. Have you ensured for very complete drainage of the soil packed up against your foam? EPS may drop water out of its structure faster than XPS, but only if there is a place for the water to go. This is relevant even up above grade.
The parge coat over the insulation that you are planning will be problematic in my opinion. At ground level, it will be subject to moisture loads from ground and rain that will likely keep it moist enough to be freeze thaw susceptible. At minimum, be sure to roughen the surface for adhesion. Addition of mesh to the coating process may help more. I would look to Parex as a source for higher strength skim coats. I used their product with mesh for my stucco base coat to battle flickers and woodpeckers. So far to good effect.
Hopefully carpenter or other ants and termites are not a problem in your area. Same for mice, chipmunks, packrats, etc. A skim coat of cement will, in any case, do little to protect the bottom edges you plan to put below grade. The addition of a sidewalk next to the parge coat strikes me as creating a heavenly haven for ants. In my own design, I elected to encapsulate the entire foundation insulation (3" recycled XPS) with Grace Bituthene 4000 all the way to from sill to footing. The footing perimeter drain is located at the side of the footing in a deep bed of washed rock protected by fabric before backfill. The Grace product is protected against weather and critters by off label usage of Hardibacker board. Tedious in detail, but it looks nice.
I would say that innie windows will generally be the weakest point in an outsulation job. Are you creating thoroughly flashed boxes around each rough opening? Can you guarantee bulk water will be directed out to the face of the foam insulation? If so, then maybe you could do a single insulation plane without a gap at the sheathing. That is a very unlikely condition over time and I don't see any advantage to skipping some form of gap. Any water intrusion that occurs behind the siding plane would best be allowed escape before sliding all the way to the footing, particularly in light of the buried foam layers lacking rapid drying options.
Another point, how do you plan to define the point where siding stops and "foundation" begins? This is not a trivial question as the furring strips which you are using as a rainscreen gap will necessarily create a series of channels behind the siding. All of which will look like welcome mats to bees, hornets, mice and so on. You will need to plan for some form of drainable filler/blocking at the starter level of the siding. Locating the bottom point of the platform might be a bit awkward with a continuous layer of insulation. Also, be sure to confirm that the strapping you place over the foam will give enough screw hold to meet Hardiboard installation requirements.
Returning to the original question of having a gap behind the foam, better advice than mine hopefully will be provided by GBA members with greater depth of experience. Personally, I would.
Tyvek is now offering different materials that incorporate gapping at the sheathing plane. How this and other materials offered in the market would work with foam, strapping and siding is beyond my real world experience. There might be hidden squishyness effects that could telegraph out to the finish siding plane. They might also be able to better advise on the density required for the EPS as well as the need or lack of need for taping the layers.
Finally, the question of your sheathing and insulation relative to your climate zone should be revisited. With a 2x4 wall you might be just in range of keeping the dew point far enough out to just kiss the sheathing so to speak. The sheathing proposed is also something I think needs a review. The current "1/2" plywood for sheathing seems to be closer to a wimpy 7/16". I shudder to think what "3/8" plywood actually measures. It may also be insufficient to meet code. I would worry that stamped 3/8" plywood would be so wavy on the framing as to cause regrets.
Hi Chris -
Roger raises some good points in his post; can you provide a drawing for more feedback?
Peter
Hi Roger, thanks for your response. It helped me come up with the answer that yes I do need to have a base flashing that drains out. Thank you for taking the time to respond. These posts seem to take way longer then you would think.
I have not had any time to post any drawings. I can post some photos in the next few days though.
The flashing we had made is approx 4” above finish grade. We will attach it to the mud sill so the back leg spans the seam between the top of the poured concrete and bottom sill plate. I used peel and stick membrane at the transition to seal it up before hand. Here we call the top of the poured foundation that sticks above the slab a curb.
This flashing will also now define our transition between siding and foundation. We will then use door screen taped to the wall and then wrapped around the bottom of the foam/strapping and attached to the front of the strapping to keep out insects. The flashing should help with larger varieties of critters.
We are already pretty far along with everything and only have the exterior to finish now that spring is here. So some of your other suggestions unfortunately can’t be followed.
We did use the 3/8 plywood as that’s what was on the original house. Could we have used thicker sure, but it passed city inspection and the structural engineer specc’d it so I believe it passes code here. Maybe the stuff up here is better!? :)
As for the below grade EPS foam, we used Type 3 for the below grade portion and are using Type 2 for everything else. I like your Hardie Backer suggestion for protecting the foam as it is durable and relatively easily completed. Not as easy as the surface bonding cement but I think it would be more durable. There was no original drainage on the home but we did put weeping tile with the sock around it where we could and covered it with washed rock. Not sure it really will do anything but seemed like the thing to do. Maybe I should have thought that portion out a little better. We get on average under 20” of precipitation per year here so we are fairly dry and about half that is snow.
We are using the Tyvek Drainwrap layer as our WRB so all our other flashings are at this level. We felt it was easier to keep everything on the same plane rather then build out window boxes and waterproof those. In hind sight I feel like the outie method might have been easier from a finishing perspective but maybe not from a waterproofing one.
Thanks again!