Should SIPs really be classified as “continuous insulation” in modeling software or in general?

Today I was looking over a REScheck summary on a set of architectural plans and I noticed that SIPs are specified as “continuous insulation”; however, as I look at the plans I can clearly see that there is framing around the windows, double top plates, bottom plates, etc. Additionally, we are located in area with 150lb snow loads, so the SIPs have internal dimensional framing to increase their load capacity. How can these panels be considered continuous when they are filled with thermal bridges? I agree that SIPs have their benefits with certain application, but I feel as though their performance characteristics tend to be overstated.
GBA Detail Library
A collection of one thousand construction details organized by climate and house part
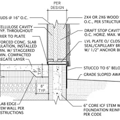
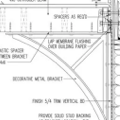
Replies
You're absolutely correct. The amount and type of thermal bridging within SIPS varies with manufacturers and installation technique, but they all require some kind of spline between panels as well as the other framing you mention. Additionally, they are installed with large continuous steel screws, which are also thermal bridges.
They are certainly not continuous insulation. They require extensive site foaming of all joints to maintain continuity and, if not properly sealed at joints, can cause air leakage and moisture problems.
I am not totally sold on using SIPS for walls yet. They may perform better and have a reduced amount of thermal bridging for the overall wall surface area, but you are missing places like your band boards for instance. I would much prefer stick framing and using a rigid foam insulation on the exterior like a blanket to cover everything and stop much more of the thermal bridging than SIPS can.
Robert, I didn't even think about the steel fasteners, great point. Josh, I agree that SIPs builders often miss critical air sealing details. I have seen blower door test results for several LEED certified SIPs homes and they have been overwhelmingly unimpressive.
I have no doubt that a properly detailed SIPs building can perform very well, but so can a stick framed building. If I had the choice between a house made up of styrofoam glued between sheets of strand board and a house with thick, breathable, thermally broken cellulose walls, I would go with the latter.
Have you folks experienced durability issues with SIPs in extreme climates such as rot, ice dams, or delamination?
You haven't heard?
http://www.greenbuildingtalk.com/buildcentral/sip/2001-10_juneau.pdf
Robert thank your for the link, yes I have read that article (despite my distaste for trade magazines). I intended to write "except in Juneau" in my post but apparently I spaced it. Nearly a decade has past since this article was published, and I am curious if there have been published instances of similar failures since then.
I like to run the SIPS right down to the foundation and keep the floor framing inside the panels, thus eliminating additional insulation details at the rim joist. I also use panels which do not require splines of any kind, but which use cam-lock connectors to pull the panels tight. This eliminates a very large portion of thermal bridging instances. It's true that structural lumber sometimes needs to be buried in a SIP joint to increase load-bearing capacity of a panel, but using interior timbers in strategic places (or a full timber-frame) minimizes the need for this also.
There is no question that diligence in air-sealing all joints is a must. For insurance, we also build a vented cold roof on top of the SIP roof to disperse any moisture-laden air that finds its way through a pinhole in a joint. As long as bulk water is kept out, a roof assembly constructed in this manner can dry if need be.
Structural material will always be needed around doors and windows, so I'm not sure how to get around that thermal bridge - but with SIPs, it is kept to a minimum. We're all doing the best we can and always looking to improve. Great discussion.
I have a 1,450ft2 house built with SIP walls and roof. I estimated a while back that there was about 5% dimensional lumber in the walls, once you add up all the bottom & top plates, rough openings and end plates. When you do the math, this makes my "R-40" SIP system about R-35 in practice.
The house is performing wonderfully (1.5 years so far), but If I had to do it over again, I wouldn't use SIPs.
Great posts ... Those who have SIPs... Your experiences are very enlightening verses just hearing from those that promote SIPs... Hope more posts are to follow.
I built a hybrid SIP type wall from Lincoln Logs LTD... It had extra wood in the walls to do with joining wall sections, and also had trouble with pulling sections together, total wall length adjustments to actual planned lengths, twisted lumber issues that most likely happened during the time between manufacture and use... and on and on. It did go up faster but... at the time I said never again.