Double Vapor Barrier

Arctic_Man
| Posted in General Questions on
My situation is such that I am building a little cabin in zone 6. Almost 2 years ago, we didn’t know all the information and built a t111 siding, tyvek wrap beneath it, and with OSB sheathing on the inside. Then, the 2×4 walls had a R13 fiberglass(faced). Just as we got ready to put up sheetrock, I decided to peel the insulation and check for potential moisture. I was horrified to see frost on the OSB. I decided to dry the walls and wait until spring/summer to continue.
After some delays and doing research on building science, I was sealing the Osb and stud joints with Great Stuff foam. This was done in Nov and Dec of last year. There was no mold that was visible at that time. Also, the t111 was pulled off and 3/4 inch straps were added on top of the tyvek wrap. When this past June arrived, I resumed the work. I peeled off the insulation and this time saw mold growing there. I was especially surprised to see it even where the OSB and stud joints were sealed off, so there wasn’t any air movement from outside. Of course there was movement on the inside and to top it off, some of the insulation batts were not installed snugly and OSB was visible from the room. However, no cooking was done on the inside and humidity during winter was low- in the 30s and 20s. Humidity started going up around April and from then on it reached about 50-70% by early June. My guess is that the mold showed up in spring. Or maybe OSB was compromised the previous year. But while reading Joe Lstiburek’s article, he mentioned that moisture is visible on the OSB when it has been saturated already. Not sure. Also, the weird thing is that there was no pattern to mold spots. It was mostly in the lower parts of the walls, by the floor, but also up towards the middle of the walls. I think the cold air was blazing through from the bottom of the floor, from outside, then traveling inside the walls and hitting warm air. My temperature on the inside was around 70s in the winter. I did turn it up to upper 80s and low 90s a few times to help dry the paint in the addition of the building.
After mold cleaning nightmare, we installed the wall extenders that made the stud bays from 2×4 into 2×6. One builder said that the R13 was not adequate fro this climate and the cold and hot air were hitting each other. Also, I sealed all of the OSB to stud joints and the floor and ceiling joints with caulk. R21 is being put in right now. I am taping the fiberglass joints as well to minimize any air movement. Once sheetrock is placed on top of this, I plan on priming and painting with 2 layers with water based paint. An architect also mentioned to us that adding a poly sheet to the walls and ceiling will prevent the moisture from traveling into the walls. I knew about this last year, but was afraid that if the vapor hits the poly and stays there behind the sheetrock, will not be able to potentially dry out from the walls. Since I didn’t know how to include the exterior XPS insulation outside, and keeping the walls breathing at the same time, I opted for the inside to outside breathing walls. My thinking is that when vapor hits the gypsum, it will be slowed by paint and then faced insulation. And if the vapor makes it to the OSB, it will hopefully be so minute that the drainage plane that is outside, will give it a chance to dry out in the spring and summer.
My question is this: Do you think if the poly is added on the interior, will it create a double vapor barrier together with the faced insulation? I understand this is potentially dangerous. But reading through Joe Lstiburek’s Double vapor barrier article, it seems that it could work. My understanding from the article is that a double vapor barrier can work if the air/vapor barrier is sealed off completely or close to it, on the interior of the room and exterior of the building. I think this means that sheetrock joints need to be airtight, together with the stud bay joints. My exterior tyvek wrap is sealed but not perfect. The stud bay joints and bottom and top plates are sealed well.
Any insight would be appreciated.
Thanks
GBA Detail Library
A collection of one thousand construction details organized by climate and house part
Search and download construction details
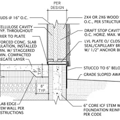
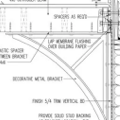
Replies
Arctic_Man,
I think you would be fine with poly, but I'm not sure it is necessary. Exterior air-barriers are very effective in preventing air leakage, but don't stop interior moisture from entering the stud bays and condensing on the sheathing. For that you need fairly well installed drywall, poly, or a variable-perm membrane. I'm fairly confident that the missing drywall is to blame, and once it's up the walls will be able to dry to the outside, even with the faced batts.
Thanks Malcolm. My exterior tyvek wrap is taped at most of the seams but I believe it is not perfect. Just wanted to confirm that I understood you correctly, the poly wouldn't create a double barrier?
Yes, I am thinking the same-that the drywall piece is crucial.
House wrap is an air barrier, not a vapor barrier. Kraft paper, the stuff used for a facer on fiberglass batts, is also not a vapor barrier, it's a vapor "retarder" (which means it slows, but does not stop, moisture migration).
The drywall is usually the primary air barrier. Look into the "airtight drywall" method, which basically involves a bead of sealant around the perimeter of all exterior walls prior to putting the drywall up. You get a lot more moisture migration with air leaks than you do through anything that is only "vapor permeable".
Malcolm is right that poly would probably work, and it's standard in a lot of Canadian codes (maybe all? I'm only at all familiar with Ontario). It works better in the very northern climate zones, where cooling loads are minimal. As you go further south, interior poly adds some risk. My recommendation would be to use a smart vapor retarder, such as Certainteed's MemBrain product, which is a safer alternative to polyethylene, and will also help to keep moisture out of your walls.
BTW, walls do not need to "breathe", but they should be able to dry in at least one direction. I would detail the interior drywall and the exterior sheathing to be air barriers, and also use a smart vapor retarder on the interior side under the drywall. That should be a pretty good assembly for you.
Bill
Thanks Bill.
I will look into the drywall method. When you said the very northern climate zones, do you mean higher than zone 6?
Looking at the MemBrain product specs, looks like great stuff. With MemBrain, do you know if it allows moisture to pass one way or both ways through it?
Does faced fiberglass function as a smart vapor retarder, at least in a way, or is it not enough for drying purposes?
Also, what are your thoughts about installing poly under the building floor(it sits on pier blocks)? Or should poly/MemBrain be installed above the floor joists, right underneath the plywood?
I would include Zone 6 in "very Northern". I know Canada has areas in zone 5 that have required interior poly for a long, long time, and I'm not aware of that presenting problems.
MemBrain changes in permeability based on humidity levels. The end result of that is that it will allow a wall to dry out, but will limit how much moisture can make it's way into the wall. That's a great combo. Poly doesn't allow moisture to move at all, and the general rule is that moisture is sneaky, so it can find a way in, but then the poly won't let it get out. That's where problems can arise with poly.
I would prefer rigid foam on the underside of the building and not just poly. There have been threads on GBA in the past about insulating houses built on piers. I have not worked on such a structure myself.
Bill
Thanks again, Bill.