Should I care about thermal bridging thru cathedral ceiling? (rafters visible thru frost)

[email protected]
| Posted in General Questions on
When there’s frost on my roof, there’s no frost over the rafters. The location of the rafters is clearly visible.
Only R-7 (the 5’5″ wood rafter + roof deck) separates -20 Celsius from 20 Celcius (-4 F to 68 F).
Code for conventional attics is R-50 but for cathedral ceilings is only R-31. I have an unventilated vaulted ceiling, with 5.5″ bays. Between the bays is 5″ spray foam. Climate zone 5b, near Toronto.
Ice dams are not an issue – that part of my roof has no eavestroughs.
If an impermeable peel-and-stick roof membrane covers the first few feet of roof, that won’t trap moisture in the rafter, because even if the rafter has closed cell spray foam on both sides, humidity can migrate down into the room, right? (Or would that be like trying to exit thru the indoor at a busy event?) To prevent moisture accumulation, would it be better to have no peel-and-stick since I don’t have or need eavestroughs in this location?
For energy economy I would like to add rigid insulation above or below the assembly, but that creates other problems and expenses (extra framing + fascia + extra deck) that may mean it’s better to let R-31 be enough in the bays and R-7 thru the rafters.
Is there a way to calculate the cost of heat loss thru the rafters? Heating costs perhaps 30 cents per thousand BTU. (70% of heat from heat pump, 30% electric resistance; 17cents/kWh; 3142 btu=1kW.) The 200 sq ft room has coincidentally 200 linear feet of rafter, with 12″x1.5″ rafter-ceiling interface per linear foot, making a total rafter-ceiling interface of 25 square feet = 3600 square inches.
Should I care about thermal bridging thru cathedral ceiling? [Edit: Re-roofing is needed.] —– I have read articles such as:
“Five Cathedral Ceilings That Work”
“Sandwiching Roof Sheathing Between Two Impermeable Layers” “Three Code-Approved Tricks for Reducing Insulation Thickness”
etc
I asked a slightly similar question 6 months ago but the conversation focused on whether rigid insulation had structural value.
GBA Detail Library
A collection of one thousand construction details organized by climate and house part
Search and download construction details
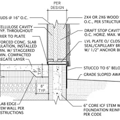
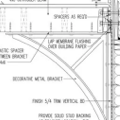
Replies
Yes, you can work out energy losses through those rafters. Chances are it would take a you a looong time in terms of energy savings to recover the cost of extra insulation to deal with the thermal briding though, unless you're already planning on a reroofing project.
You DO want the ice and water shield. That's extra insurance. I would never go without it. Code here is for one roll width' worth of the stuff at the eave, but at least two times that amount is really needed for proper protection. You don't have the same kind of moisture trap issues when the vapor barrier on either side is a fully adhered material (spray foam and ice and water shield both are), since those materials pretty much ensure that nothing can get in, so there is no need to allow for anything to get out. If you're worried about moisture geting through the rafter itself, don't be -- that rafter is acting like a pretty extreme wooden vapor retarder already, and if it's open on the interior it already has enough drying ability to avoid issues.
If you want the safest and best performing assembly, putting rigid foam above the roof sheathing is the way to go. Roofing polyiso is a perfect fit for this. I agree with you that the code minimum insulation requirements for cathedral ceilings leave a lot to be desired!
Bill
Thanks. If I use rigid foam on a sloped roof (7/12 or 8/12 slope), I need to add a 2nd deck, right? Seems obvious, but I'll ask in case there's a way around that. I intend asphalt shingles, but I think a 2nd deck is needed for any roof type, right?
+ framing, and not only at the perimeter. Again seems obvious, but: any way to avoid that?
Thanks
If I understand correctly, sounds a bit like a 2x6 wall insulated with 5" of spray foam. When there's frost on my east wall (2x6 w/spray foam and batts and exterior tng wood), I can faintly see the 2x6 framing. If I had to do over, I would have added a layer of continuous exterior insulation. With 5" of spray foam, you probably have good air sealing.
There's probably a calculator for 2x6 walls, bay insulation R-value and effective R-value that you could use to get an estimate for your roof. Here's an article from JLC: https://www.jlconline.com/how-to/insulation/understanding-r-value_o
Yes and no.
Your assembly is probably around R20 taking into account interior finishes, air film and thermal bridging from the rafters.
For 2000 sqft of roof over a season you loose about:
7200HDD*24h*2000sqft/R20=172 Therms.
At $0.72/therm that works out to $123 per heating season.
You can half that heat loss by adding ~3.5" of polyiso on the roof, but that would only save you $60/year, so ROI is never.
Unfortunately the ship has sailed on the cheaper fix.
In case some else finds this and is looking to spray foam a 2x6 ceiling. The simplest way is to cross strap the ceiling with 2x2 or 2x3 on edge perpendicular to the rafters and spray foam over the rafters. Even adding an 1" of SPF above the rafter while keeping the rest at 5" bumps the assembly up to close to R26 for not much extra cost.
In case of 2x3, 2" of SPF over the rafters or R8 rolls between the 2x3 and about 5.5" elsewhere makes it a pretty good roof.
Hitting R40 or higher with anything SPF or rigid is generally not worth it as the material costs and embodied carbon is simply too high.
I like this plan. You can put in enough closed cell spray foam to get dew point control, then fill the remainer with open cell spray foam and trim it flush with the strapping. Open cell spray foam is cheaper, greaner (less physical material per unit R value), and much easier to trim.
Bill
Thanks. That cost calculation was eye-opening, and it's just a single room with this roof, only 200 sq ft, not 2000, and the HDD is 4500, so the heat loss would be even less than you calculated.
I actually simplified by saying that the assembly has 5" of spray foam. That is the plan. The current situation is that a renovator installed 2"-3" directly against the sheathing, and left a "ventilation" channel below the foam above the drywall. @#$*! The shingles need replacing anyway (pronto!), so tearing down the drywall vs ripping up the sheathing seem roughly equal in cost.
Adding framing below / adding rigid insulation below the current ceiling height is an option but the 200 sq ft includes where the ceiling slopes down to 2.5' high, and since the ceiling has 2 sides, adding 3" below would eat up 6" of an already constricted space. I hoped it would be inexpensive to add rigid foam atop the roof, but since structurally-sound framing + another deck + fascia / custom flashing would be required, that might not be worthwhile.
So the plan is to remove the sheathing (difficult because of the spray foam) spray down 5", then replace the deck, add membrane + asphalt shingles. Ideally we could re-use some of the original deck, but I doubt it will be possible to remove the old deck without cutting it.
Ideally we wouldn't need to throw out the spray foam, but then there would be gaps between the 2 layers of foam, possibly allowing moisture in more easily than out. If we tear down the ceiling, we could keep the existing foam.
Another option would be to frame-up 2" then spray down 7". Only 1 deck required, only 1 type of foam required. Replacement fascia or custom long drip edge still required.
Or frame up 5", install batts. Being finicky, we don't want to lose more sun to our already sun-limited garden.
I wrote all that because you suggested a way someone in a similar situation could increase the depth/height of the roof bays, so I hoped you just might have a better idea for adding insulation upwards, but I now doubt there is any other practical option. Perhaps I'll stick with the 5" plan.
Thanks.
Toronto is 4000HDD Celsius. You need to multiply by 9/5 to get HDD F.
If you already have 2-3" of SPF under the deck, the simplest is to insulate with fluffy underneath. You get pretty much the same assembly R value as 5" of SPF without having to rip everything out and redo the roof deck and pay for new spray foam. 2" of closed cell spray foam is sufficient for condensation control for up to R30 of total insulation.
For such a small area, the easiest is to take down the drywall, touch up any air leaks around the perimeter with canned foam and squish either R19 fiberglass batts or R14 mineral wool under the existing SPF. Reinstall the drywall.
If you really don't want to pull the drywall, you can fill the gap with cellulose. You need to cut some holes in the drywall and blow in the insulation through there.
The box store cellulose machine with a reducer to 1.5" hose does a decent job of semi dense packing, it just takes time and patience as feeding in too much cellulose can cause it to clog up. Make sure the hose you get has no splices in it, those always clog. What I like to do is cut about a 16" x 6" hole directly over the rafter so the one hole can access two rafter bays. You can also drill round holes with a large hole saw in each rafter bay, I find patching a square hole easier.
Thanks. I love the thought that a flash-n-batt equivalent might work - with mineral wool or fiberglass batts or cellulose.
Alison Bailes' chart says I would get R11-R15 for my 2.5"-3.5" remaining cavity, using an R-15 batt. (energyvanguard.com/blog/compressed-fiberglass-insulation-really-so-bad/)
For an R-19 batt, he shows R-13 when compressed to 3.5", and no data for any smaller cavity, so I'd use an R-15 batt if I went fiberglass.
The current 2-3" of this spray foam (Dow Touch-n-Foam) is R-5.2/inch if installed under ideal conditions. I'd say it's currently R-10-R-15 at best, depending on thickness. Combined result: R15+R11 (where currently 3") / R10+R15 (where currently 2").
R-14 mineral wool is specified for 3.5" cavities. I don't know it's R-value if compressed to 2.5", but it seems it would on average perform just like fiberglass.
I had actualy thought of cutting holes and spraying cellulose - combined with 2" rigid foam on top. If I went that route, I would use a borescope to try to ensure cellulose didn't get blocked by obstacles like electrical wires. R-3.5/inch adds R9-R12.4.
I had also considered: ** Spray Foam thru holes? **
Cut holes into each bay, at 4', 8' and 12' (top), insert foam wand almost 4' (if that length exists), spray, moving side to side, pausing for foam to expand up the sloped cavity, so excess pressure doesn't break drywall. Somehow plug holes as I go. Use a borescope to ensure wand is actually reaching the end of the area, not just an obstacle. Better than if there was no ceiling in terms of completely filling the cavity without needing to cut excess. Slow, adding expense, but perhaps less to patch drywall than if all drywall came down. With no rigid foam on top, doesn't address thermal bridging.
Open cell r-3.5/inch. Same r-result as with cellulose.
Closed cell (if I can find a pro who will work this way), R-6/inch using a pro product. Result (current+added): R10+R21 (where now 2") / R15+R15 (where now 3").
Good idea? Bad?
Unless you fix the thermal bridging, adding more R value between the rafters won't budge the assembly R value much. 2x6+R32 spf -> R20 assembly. 2x6+R25 flash and batt -> R19 assembly. 2x6 with magical R100 insulation ->R27.
Exterior rigid is a good way to do it from the outside but adds significant cost and complexity. Not sure if it is worth it for a retrofit.
You can fix it from the inside using some insulation strips over the rafters which would give you space for 5.5" batts:
https://www.finehomebuilding.com/project-guides/insulation/breaking-the-thermal-bridge
Trying to fill the rafters with spray foam through holes is a disaster in the making. Besides near impossible to fill all space, it will ooze on you and might even pop the drywall off if you overfill a cavity.