low/no concrete basement? (ship-hull)

GBA regularly sees questions about non-traditional foundation building techniques: “concrete-free slabs” are presently a hot topic, and permanent wood foundations come up occasionally. Along these lines, could a waterproof membrane be used in conjunction with an internal frame on well-drained sites? I’ve attached two sketches, which remind me of a ship’s hull in cross-section.
Assumptions:
– a load-bearing internal frame (of steel, reinforced concrete, large timbers, etc) transfers the weight of the building to the footings.
– the site is well-drained, so the membrane never experiences significant hydrostatic pressure.
– the “walls” only need to resist lateral earth pressure (the weight of the superstructure is supported elsewhere, and the site is well-drained). Lightweight fill and an “up-and-outward” sloping wall can be used to reduce this pressure. If frost-heaving and/or expansive soils are of concern, then the wall should slope “up-and-inwards” instead. The wall membrane is then supported from within by light framing (think roof trusses or rafters) and infill (planking, OSB, wattle-and-daub, etc). If the membrane is warm and dry, you can skip the expense of pressure-treated lumber.
– the “floor” area is weighted down with ballast. This could be fieldstone, gravel, cannonballs, etc.
– the membrane is well-protected on all sides. Rigid insulation and/or drainage mat might be good solutions.
– the membrane is continuous and/or seams are welded. The roof membrane and pond liner industries have this down to a science.
Benefits:
– easy access for inspection/repair. Uncover the membrane from the inside, and cut/patch to your heart’s content. Appropriate techniques are well-known for materials such as EPDM and reinforced polyethylene. Cutting through the membrane to access “sub-slab” systems (drainage, radon, septic) shouldn’t be a big deal.
– reduced carbon footprint? My guess is that a membrane won’t last as long as a standard poured concrete basement, but it ought to live an exceptionally long and happy life (stable temperature, no UV, managed water, accessibility for repairs, etc). Estimates for embodied energy still have big uncertainties associated with them, but 45mil EPDM represents ~1/3 the embodied energy (per unit area) of your average 8″ concrete wall, and 15mil poly is <10%.
– end of life management? The holy grail would be ready re-reuse, which probably won’t be the case for membranes. But re-use might be possible with the load-supporting structure (bolted together steel/concrete/timber columns and beams). The membrane could be rolled up for recycling/disposal. Good luck salvaging much from a poured concrete foundation.
All in all, this is probably a solution in search of a problem, and certainly not in the IBC, but an interesting thought experiment. Feel free to poke holes in the membrane concept!
(EDIT: 4/24 title updated to better-reflect content)
GBA Detail Library
A collection of one thousand construction details organized by climate and house part
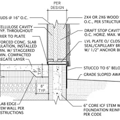
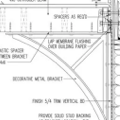
Replies
Neat idea, you've worked out a lot of the details. I'm not the target audience, as I don't have an issue with concrete in construction assemblies - there's no better material to ensure long assembly life (well, except for maybe dry stacked stone?) and minimize sound transmission in dense environments.
Building on your hull metaphor, continual maintenance and inspection are going to be important. The assembly might resist soil pressure and moisture, but mechanical damage will be harder to prevent. The manual "Guidance on Inspection, Repair, and Maintenance of Wooden Hulls" published by the Coast Guard might be a good way to start validating repair strategies and material selection, it's only seventy pages or so.
Another area to look at would be root cellar designs, but from what I remember most recommend poured concrete or block from a longevity standpoint. Historically though, wood was common and there might be some good ideas there.
Sam,
Thanks for the references. The Coast Guard publication largely concerns itself with the complications introduced by marine life and saltwater corrosion, but includes some useful details. I imagine that if a "ship hull" design were to be attempted in an area with a high water table, a much more robust cross-section (like those employed in larger ships) would be in order. As long as water is well-managed (i.e., drainage runs to daylight) and the walls are well-designed, my gut instinct would be to treat each wall as a "sideways roof".
You are of course correct that concrete is a near-ideal material for foundations. That it's strong, stable, cheap, form-able, nontoxic, AND doesn’t care if it gets wet: nothing short of miraculous. And it has Martin's blessing (e.g., https://www.greenbuildingadvisor.com/article/do-i-really-need-a-concrete-basement-floor).
Another thought: for older houses with fieldstone basements, a ship-hull design could probably be retrofitted within the fieldstone walls (with or without the load-bearing structure). I think that spray-foam over a sheet of poly is the usual approach for these situations, but access to the inner wall surface could be improved. Especially if those walls will need repointing in the future.