Sheathing needed with roof top insulation?

I am constructing a new roof on my home (adding a second story in Zone 5). Because there will be a knee wall and a sloped ceiling, I decided to construct the roof like a cathedral ceiling, even though there is a flat ceiling about 2/3 up the rafters.
I had specified 2×8 rafters with cellulose and 6 inches of polyiso on top of the sheathing. My contractor is encouraging me to skip the sheathing (if approved by the inspector). In other words, the rigid insulation would be installed directly over the rafters. On top of the insulation would be the underlayment and 2×4 purlins for the metal roofing. He said I could save about $4,000 to eliminate the sheathing and rely on the structural ridge beam and the purlins for structural rigidity.
Does that make sense?
GBA Detail Library
A collection of one thousand construction details organized by climate and house part
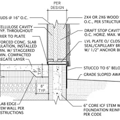
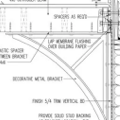
Replies
It's a heluva lot easier to air seal 4' x 8' sheet goods than it is to air seal skip sheathing. I'm not sure how using skip sheathing saves $4K unless the alternative/comparative roof deck was Zip(?). Using sheet goods for the sheathing and a fully adhered membrane WRB such Grace Ice & Water
or Blueskin Eaveguard between the deck and foam is very air tight.
Note: Your stackup with the 6" of continuous exterior polyiso would pretty much meet IRC 2018 performance on a U-factor basis, even without cavity insulation.
Sorry for the confusion. My contractor wasn't suggesting to switch to skip sheathing. He meant to eliminate the sheathing altogether. The $4,000 figure was off the top of his head, but it included both material and labor for a 1,600 SF roof.
The compressive strength of foam board isn't likely to handle the dynamic loads imparted where the purlins cross over the rafters- it will compress and wear over time with wind & snow loads, changes in temperature etc. Four grand on a legitimate air-sealable roof deck is money well spent.
The WRB between a roof deck and foam acts as a slip surface for the flexing & seasonal thermal/hygric dimensional changes, as well as distributing the load over a much larger fraction of the foam area.
Couldn't there also be a fire code violation involved? I would imagine that having exposed foam in the attic would be pretty iffy, especially if the attic is conditioned as it likely should be.
Let us know if such a design is allowed structurally (no doubt that it has an effect).
James,
I think the bigger issue is that this will be very hard to build. Part of the reason you want plywood ontop of your rafters is that you can walk on them. Besides being structurally sketchy, I think trying to build it with foam only would be cost more in labor than laying down 7/16 OSB.
About the only way I can see skipping the plywood is by going with 2x6 purlins on edge perpendicular to the rafters and fitting the foam in between. You would still have a lot of air sealing issues to solve with plus now there is the thermal bridging of the 2x6.
The other function of roof sheathing is to make the roof a diaphragm which contributes to the rigidity of the whole structure. Purlins do this to a lesser extent, but purlins on top of 6" of foam won't.
I guess your builder is a lot braver than me. As Akos said - I'd be scared working on that roof without sheathing
Hi James -
The GBA Q&A community, including me, is very dubious that you can add a 2nd story including a roof with no structural sheathing. You should ask your builder about this, and your building inspector, if not a licensed structural engineer.
Peter
I’d ask an engineer to review it even if the builder and inspector were ok with it. Using no structural sheathing at all is deviating so far from the well understood norm that I think it would be prudent to have an engineer actually verify the impact such an assembly would have on the structure as a whole.
I’m another vote for doing it the “regular” way, with OSB or plywood sheathing.
Bill