Using Different Wall Assemblies on the Same House

Hi All,
In the pre-planning stage for a new construction is zone 6A. One of my questions is whether or not it makes sense to mix wall insulation strategies depending on the wall orientation (north, south, east, west) or wall cladding…i.e. stone veneer or vinyl siding.
For example, I like the idea of a double stud wall, but it’s potentially risky for a northern facing wall. Maybe that wall would get exterior foam, while the east, west, and south sides would be built double stud. Too confusing to be practical?
Another example would be a house with mixed siding material. Maybe the walls with masonry veneer could be building in a conventional setup of 2×6 with zip and blown cellulose to avoid a very expensive 14″ thick foundation wall, but the other sides of the house could get exterior foam or double stud.
If one wall has say 30% less total R-value than the other walls, is the loss proportional to the square footage, or does it function like a thermal bridge where a relatively small area loses a disproportionate amount of heat?
GBA Detail Library
A collection of one thousand construction details organized by climate and house part
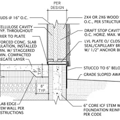
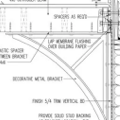
Replies
I'm not a production builder, but my sense is that this would be a practical and cost nightmare..perhaps aesthetic too when talking siding.
I would just choose an assembly that meets your performance and robustness desires regardless of orientation, etc.
Part of the reason is that most of these systems have unique details at corners, and trying to integrate the distinct systems seems prone to complication.
For heat loss, you may be interested in these:
https://www.greenbuildingadvisor.com/article/how-to-perform-a-heat-loss-calculation-part-1
https://www.greenbuildingadvisor.com/article/the-fundamentals-of-series-and-parallel-heat-flow
My vote would be to forget about it.
Spend more thought on doors and windows (fenestrations) as they are big ticket/cost items that you can vary. My thought is that on cooler sides you'd want fenestrations that were less conductive and more insulative: trying to minimize fenestration area here should be the first thing one does (keeping in mind egress requirements/code). On warmer sides it would be more about dealing with heat gain.
Rick,
I agree with the other posters. Choose a forgiving, well-performing assembly appropriate to your climate and site which can accommodate the differences in orientation and cladding types. A double-stud wall with the appropriate interior vapour retarder and exterior WRB which incorporates a rain-screen cavity, or a wall with the appropriate thickness of exterior insulation would probably both fit that description.
The only thing that makes double stud walls potentially risky is that people
insist on trying to fill them with cellulose ( I know! it's considered easy and cheep).
The better way is to place a layer of foam in the center (not on the exterior!).
Example section:
Interior side 2x4 @ 16" OC with fiber batts: R= 8 with fiberglass
Exterior side 2x6 @ 24" OC with fiber batts: R=14 with fiberglass
Then fasten 4" of foil faced polyiso to the interior side of the exterior 2x6s for an
additional R value of 20 ( aged R value) & your total wall R rating (your real R value
not this nominal nonsense spouted by contractors & some building departments)
will be around 42 (higher if you use mineral wool instead of fiberglass). THERE'S
A DOWNSIDE TO THIS - You will probably find it necessary to build the exterior
2x6 wall first and insulate it including! installing the polyiso before constructing the
2x4 inner wall (and other interior walls). Some contractors will balk at this
construction sequence. THERE ARE ALSO SOME UPSIDES!!!
1. The polyiso acts as the best moisture and air barrier money can buy
2. It's in the center of the wall and is therefore protected from damage, insects, fire
and thermal degradation at low temperatures.
3. You have your choice of fluffy insulations on both sides of it
4. No additional moisture barriers are necessary
5. The moisture barrier (the foil surface of the polyiso is only about 1/5th of the
thermal gradient into the wall (from the inside) this means you will never reach
the dew point at the condensing surface (SO NO MOISTURE BUILD UP INSIDE
THE WALL- which is where the risky comes in with double wall construction)
6. This method eliminates the problems that occur with attaching siding and trim
if you try to put the foam on the exterior
The only reason I bothered with all this is that your questions indicate that you are
open to creative ideas - not many are - good luck!
Deleted
Thanks all for the replies. I suspect you’re right, that switching construction methods would lead to confusion.
Forrest, your suggestion is very interesting. Occasionally I come across polyiso or EPS when working on demo projects, and I probably have somewhere around 60 sheets of 2” felt face iso.
Can you answer a few questions:
Do you install your windows as innies or outies?
Do you install the top edge of the foam flush to your top wall plate and do you tie the inner and outer walls together with plywood at the top?
Any concerns with cold exterior sheathing?
Rick,
The wall Forrest has proposed is a variant on the many assemblies that have mid-wall air and vapour barriers, some of which (like Stephen Sheehy's) have been featured in GBA blogs. The difference is those assemblies usually either move the sheathing to that location, or install a membrane there.
I'm not certain there is any real gain to using a lot of foam there as opposed to the other options. The location of the foam and Forrest's aversion to cellulose mean that the outer stud wall and sheathing stay colder and do not benefit from the moisture buffering cellulose provides.
Rick;
Last time I did this all windows were installed as outies - Polyethylene was installed across the ceiling prior to installing sheetrock and then taped to the polyiso before building the inner wall.
I did not tie the two walls together with plywood - merely fastened to the roof trusses & the floors. Yes the foam extended to the top of top wall plate. This was approx. 20 years ago - I am now an old retired curmudgeon living in a much less challenging climate - no longer building houses. But, during my working years I designed, built and lived in three of them (lived in them for over 26 years)
- all in the Rocky mountains ( at elevations of about 7000 ft.) - all double wall construction -
I found the heat bills to be roughly 1/16th of heat bills of same size houses on the streets in the subdivisions where we lived - over 26 years in a cold climate that really adds up. And last, no - you won't care anything about cold sheathing because no interior moisture can get through the polyiso to cause problems.
You didn't mention your climate zone/location, but there are differences in the microclimate at different walls. The north would tend to be colder in winter and damp, vs. the south especially. Sun exposure would lead the east and west to be hotter in summer, with the south warmer in winter, assuming they are not shaded by other structures or foliage. You might worry a bit more about damp walls on the north, for example. You might want to avoid black cladding on walls on the east and west (get very hot from summertime solar gain), but won't matter on the north.
I've used three different wall assemblies on one home. On the south side, there was much more area dedicated to windows. So using exterior foam became more of a hassle than the north and west sides, so it was deleted resulting in R-6 less insulation. The east side was planned for an addition, so a third assembly there, since most of it would likely face the interior in the future (so R-6 less and R-3 less insulation in different sections on the east side).
You need to calculate the heat loss on each wall separately, so the idea of a thermal bridge doesn't apply here, unless the wall intersections create some thermal bridge. Something you are likely to be able to avoid, if you note a potential problem and design the corner to minimize thermal bridging.
If you aren't doing or managing the labor yourself, you might consider if confusion or mistakes could result in hired help not building what you had planned if walls were to be built differently.
RICK;
Just a little more - I don't really have an aversion to cellulose, Malcolm, but I am concerned with moisture movement and wall thickness - in fact all of my homes have had cellulose in the attic. Here's the philosophy - the higher the R value of the insulation the less thickness of the wall required to reach any desired total for the wall and thicker walls mean more roof, more excavation, more construction materials, etc. for any desired floor space. with todays technology the highest R value commonly available is spray foam at around 7 per inch.
However, the cost is usually quite high. For that mater, all the various foams are more
expensive than the fluffy stuff in general, so for any desired R value for the total wall
the foams add to the cost. The pertinent question is does the house cost more to construct
with thicker walls (with the fluffy insulations) or more with thinner walls with foam. It's been my experience that the thinner walls win - you will have to decide for yourself.
The reasons for my recommendation to put polyiso in the center of a wall have to do with
both moisture migration through the insulation and wall thickness. It's true that cellulose
buffers the moisture but what does that actually mean? It means that it spreads it out - it allows it to go anywhere, it does not reduce it - there is some considerable discussion in the
literature about weather this is really valuable or not. In addition, there is probably a settling problem with cellulose in walls - I can't prove this to you but many people have noticed
cellulose settling in walls over long periods ( take a look Thorsten Chulps home in Fairbanks
Alaska, he went to a lot of trouble trying control the density of the cellulose in the walls but after some years a scan with a thermal imaging camera showed settling anyway). Until I see
thermal imaging studies of hundreds of homes done 10 or more years after construction, I refuse to believe the assertions of the cellulose industry with regard to no settling in walls if you maintain the proper density.
Last, the moisture problem. Moisture will migrate through all of the fluffy insulations, less in cellulose than the others but it will migrate. In cold climates (like yours - 6a) it will condense
at the point in the wall where the temperature drops below the dew point - what does it condense on - the fibers that make up the insulation, wood, structural sheathing, wiring, plumbing, etc. If you put in a non-permeable barrier in the wall (foil faced foam, Polyethylene
sheet, painted plywood or whatever) at the right place, the barrier will prevent any moisture
from migrating past it. The right place is about 1/3rd or less of the total R value of the wall (starting on the warm side) - at least in climate zones 6 or lower. This will result in the fluffy insulation on the warm side of barrier remaining above the dew point. Today most people
who are interested in this would like to have walls with a total R value above R 40 if they can afford it - this means about R10 inside the barrier and R30 or so on the cold side - with double wall construction and all fluffy insulation it becomes difficult (nearly impossible) to install the barrier in the right place - but install a few inches of impermeable foam on the inside of the exterior stud wall and presto-changeo everything works.
Why polyiso? Because in most areas at most times it is cheaper and has a higher R rating per inch than the rest of the foams (except closed cell spray foam) and all of the fluffy stuff.
HAVE FUN!