Sell me on rigid foam exterior in climate zone 3A

Starting building on our dream house in a few months. Plan to live in for 30+ years. House will have Zip Sytem sheathing and will be well insulated on the inside, I will just leave it at that. Not interested in installing rigid foam on outside of roof sheathing (I have my reasons, so please don’t try to convince me otherwise).
So…. House fully exposed to sunlight. 1″ rigid foam with foil face. Strapped with cement fiber siding.
Sell me on all the reasons why this is worth the time/cost.
Go….
GBA Detail Library
A collection of one thousand construction details organized by climate and house part
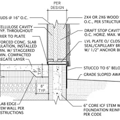
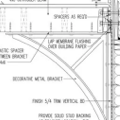
Replies
Build a double stud wall, no foam
In your climate zone, any thickness of foam would be acceptable. But an R-3 ZIP-R panel might be a simpler option to address thermal bridging.
What is your plan for insulating the attic space?
Farm,
First of all, it's your house. You can build it any way you want, as long as your local code enforcement official is happy. I don't see any reason to convince you of anything.
If, after researching the issue, you decide that you want to increase the R-value of your wall assembly, or reduce thermal bridging through your studs, you might want to take Steve's suggestion and use Zip R sheathing instead of ordinary Zip sheathing. But I see no reason to try to convince you.
Run the energy use/cost numbers by modeling the house in BeOpt (a freebie download courtesy of the US DOE). Then, given that it's "...fully exposed to sunlight..." compare that to the ROI for spending the same upcharge for rooftop PV solar (assume $3/watt-DC, all-in, before any subsidies such as the 30% federal tax credit).
In US climate zone 3 it's possible with a decent design to hit Net Zero Energy with 2x6/R20 walls, no exterior insulating sheathing with PV array that fits comfortably on a sun-drenched house, using better-class heat pump technology properly sized for the modest loads. See Table 2, p10 of this document, and note that the R-values are "whole assembly" values that include the thermal bridging of the framing, not merely center-cavity R:
https://buildingscience.com/sites/default/files/migrate/pdf/BA-1005_High%20R-Value_Walls_Case_Study.pdf
The R20 wall suggested in that table for zone 3 could be achieved with an inch of exterior foam or ZIP-R, but that document was created in 2009/2010, when PV cost $7-8/watt and was 15% efficiency, whereas now it's $3/watt and ~20% efficiency, requiring less rooftop real-estate to deliver the same amount of energy. And, better class heat pumps at that time were running HSPF 10-12 with SEER in the teens, whereas current better-class ductless mini-splits are in the HSPF 12.5-14 range with SEER well north of 20. Between those two technology advances you can now basically shoot for the zone 2 numbers in Table 2 and still make it work, if Net Zero Energy has any appeal.
A 2x6/R20 16".o.c.ZIP sheathed wall with a rainscreen gap behind fiber cement siding hits R20. So does a 2x6/R23 wall (rock wool batts) without the raincreen.
So, skip the exterior insulation, concentrate the investment where it pays more. Table 2 is still useful, and going for the zone 3 numbers isn't insane for all assemblies (the basement/crawlspace wall R is IRC 2015 code min, after all), and complying with the window specs for zone 3 are probably still "worth it" on a comfort basis even if it's an upcharge over current code-min, etc.
The cheapest thermal upgrade to add would be to take air sealing VERY seriously (shoot for under 1ACH/50), and installing heat recovery ventilation.
The other cheap thing upgrade is to simplify the footprint down to no more than 6-8 corners (not a dizzy array of step backs & bump outs), which minimized the ratio of exterior surface to floor area, reduces the fraction of thermally bridging framing to the overall wall area, and makes air sealing a lot easier. Architectural drama can be achieved by other means, such as changes in cladding, porches & porch roofs, etc without adding efficiency robbing complex geometry to the building envelope.
Dana,
Your response here is super informative for me. Just a clarification questions. You say:
"A 2x6/R20 16".o.c.ZIP sheathed wall with a rainscreen gap behind fiber cement siding hits R20. So does a 2x6/R23 wall (rock wool batts) without the raincreen."
I assume when you say "hits R20," you mean the true R-value of the full assembly. How does that work out with R20 cavity insulation??
Incidentally, is there a good resource you can recommend for finding true R-value? I found this: , but would like to know if there's one more accurate.
Thanks!
I was being sloppy (perhaps under-caffeinated?)
Perhaps that should have read " "A 2x6/R20 16".o.c.ZIP-R sheathed wall with a rainscreen gap behind fiber cement siding hits R20." (The "...-R.." was missing.) This is assuming 1"-1.5" ZIP-R, which has R3 -R6 of foam laminated onto half inch OSB.
The way that works is first calculating the U-factor of the studwall + insulation layer, then adding the thermal performance of the continuous layers, including air films. A primer on how that is done can be found here:
https://www.taitem.com/wp-content/uploads/2011/01/TT-NC-Calculating-U-values-Nov-2008.pdf
Most homes with 16" on center studs have about a 25% framing fraction, and most framing lumber runs about R1.2 per inch, and 2x6 framing is 5.5" deep, so the 25% framing fraction is about R1.2/inch x 5.5" = R6.6 or (1/R6.6=) U0.15, and the 75% framing cavity section is R20 or (1/R20=) U0.050 in the fiberglass batt case, R23 or (1/R23=) U0.43 in the rock wool case. So just the framing + insulation layer is worth:
(0.75 x U0.050) + (0.25 x U0.15) =U 0.075, or R13.3 "whole layer" with R20 fiberglass.
(0.75 x U0.043) + (0.25 x U0.15) =U0.070, or R14.3 "whole layer" with R23 rock wool.
To that we add:
~R3 for the inch of foam (1" ZIP-R, or half inch foam)
~R1 for the siding & wallboard (combined)
~R0.9 for the interior + exterior air films
So with no rainscreen gap the "other layers" add up to ~R4.9 yielding...
...R19.2 for the rock wool case...
...R18.2. for the fiberglass case.
So the rock wool case is about 4% shy of R20 whole-wall using 1" ZIP-R.
A 3/4 " rainscreen gap adds another R1 , the 1x furring creating the gap is also about (R1.2/inch x 0.75" = ) R0.9, so call it about R1 for that rainscreen + furring layer.
That would bring the R20 fiberglass batt case up to R19.2 whole-wall...
...and the R23 rock wool case up to R20.2 whole wall.
With an inch of polyiso foam or 1.5" ZIP-R adds another R3 to the whole-wall R, and even the no rainscreen case would hit a hair north of R21 whole-wall for the fiberglass case, R22 for the rock wool case, and with rainscreen about R22 (fiberglass) & R23 (rock wool) whole-wall.
With no foam at all you'd be looking at ~R17 whole-wall for the rock wool + rainscreen, about 15% shy of R20.
(May somebody should check my revised math- haven't had any coffee since noon! :-) )
"Sell me on all the reasons why this is worth the time/cost."
Your exterior walls are constructed with 2x4's and you don't want a PV array (ground or roof mounted) because you live in a s state that doesn't subsidize solar? *shrug*
UUHH? Am I missing something here? "Not interested in installing rigid foam on outside of sheathing (I have my reasons, so please don't try to convince me otherwise)... yet, you ask for it???
I design high-performing houses in NTX, which is CZ3, and outsulation takes care of rare winter and summer condensation, plus when taped properly, it becomes a second moisture barrier (more assurance). IMO, Zip-R sheathing has the foam on the wrong side of the OSB.
Along with insulation/outsulation, here are a few other important factors to consider (just in case you don't need any convincing): building design, ventilated or un-ventilated attic design, building tightness (1ACH50), moisture control detailing and rain screens, HERS 40s w/o PV, 1 ton AC per 1000-1500 sf and IAQ, ES lighting and appliances, and EPA WaterSense.
@Armando Cobo
The OP was talking about foam on top of his ROOF sheathing.
I think the OP will find that his broad question will receive broad answers.
John,
Two issues are unclear: (1) whether Farm House is talking about wall sheathing or roof sheathing, and (2) whether Farm House is dead set against exterior foam or open to a convincing argument.
The sentence "not interested in installing rigid foam on outside of roof sheathing" sounds like the discussion concerns roof sheathing.
The sentences "1-inch rigid foam with foil face. Strapped with cement fiber siding." sound like the discussion concerns wall sheathing.
My bad... I read up above about Zip-R and I started thinking walls; sorry. However, I think Zip-R is approved for wall sheathing only.
For conditioned attics, to avoid condensation and thermal bridging, installing flat, tile or metal roof, I do use 1" rigid foam on top of the roof decking and 8" of open cell foam under the roof decking. If using shingled roof, we spray 2" of closed cell foam follow by 7" open cell foam under the roof decking.
I think there are several articles here in the GBA about condensation in conditioned attics. Also see " Cool hand Luke" blog from Building Science Corp.
Here's another angle if you're looking for different arguments:
Reducing your use of fossil fuels (and other non-renewable resources) is an ethical choice from an intergenerational equity (aka think of the children) point of view. If exterior insulation is an effective way for you to do this, then it would be ethically responsible for you to add exterior insulation.
Whether or not that line of reasoning is important enough to you to justify the expense is a question only you can answer.
Confusing? I didn't think so, but maybe...
"So.... House fully exposed to sunlight. 1" rigid foam with foil face. Strapped with cement fiber siding." reads like an invitation to discuss wall assemblies.
"Not interested in installing rigid foam on outside of roof sheathing" seems to be a directive to NOT get into the roof details, and thus constrain the topic to foam vs. no-foam on walls only, not roofs.
Could be wrong, but Armando's initial impression was right- this is ALL about walls, nothing about roofs. Perhaps FARM HOUSE can weigh in on this.
Brendan: The future generations/fossil fuels discussion can go a number of different ways. Higher wall performance can be had with lower initial and long term carbon emissions by staying away from foam altogether (which has a very real carbon footprint), and using cellulose as the cavity fill (which is net carbon negative, and sequesters carbon), or rock wool (low carbon footprint relative to any foam) and/or using only electric HVAC combined with renewables-only electricity (site sourced or purchased.)
As indicated in response #4, in zone 3A it's possible to get to Net Zero Energy (or Net Zero Ready) with standard 2x6 framed walls and NO foam, with a reasonably well thought out design.
Rainscreen- YES!
Air tight- YES!
Energy-heel trusses sufficient to accommodate 16" of fluff in vented attic- YES!
Ducts & air handlers inside the insulation & pressure boundary of the house (not above the insulation in a vented attic)- YES!
Better than code-min windows- YES!
Foundation insulation- YES!
But exterior insulating sheathing- not NEARLY as important in that climate zone (but also not insane.)
BTW: In response # 4 I had stated that IRC 2015 code min for basement insulation was the same as in BA-1005 document Table. IRC 2015 calls out R5 continuous insulation or R13 in a studwall. The 2x4/R13 wall is roughly the same as the continuous R10 indicated in Table 2 of the BA-1005, but clearly R10 is twice the code min R5 c.i. spelled out in the code. See TABLE N1102.1.2 (R402.1.2) INSULATION AND FENESTRATION REQUIREMENTS BY COMPONENTa :
https://up.codes/viewer/int_residential_code_2015/chapter/11#11
Note that that 2x6 / R20 is now code-min for zone 3, and with 20% efficiency PV and HSPF 12+ /SEER 20+ HVAC equipment that code-min wall is now a good enough to hit Net Zero, as long as the rest of the house is up to snuff.
The reason I didn't give as many details about the rest of the assembly is because my experience is that it distracts people from my question. They spend a lot of time trying to talk me out of other parts of the build. I've reached a comfort level with the rest of the design and I'm spending substantial dollars on an hybrid insulation approach (NOT flash & batt) and taking air sealing efforts about as far as one can go. Also spending serious $$$ on Trane XV20i heat pump. Considering installing solar array once we build the detached garage a few years down the road.
Martin- most of the research I've found on exterior foam speaks to cold weather climates. I did find one video (promotional video for Rigid foam.....) that provided percentages of heat loss for air leakage, thermal conduction, etc......
I was hopeful the radiant barrier would help significantly with radiant heat gain from being exposed to the sun all day. Since the walls will be 2x6, 1" Rigid Dow Tuff-R (for example) would roughly double the R-value for the 25% of the exterior walls that is made up of 2x6s.
Regarding Zip-R sheathing. I think I had it quoted around $80/sheet vs $17/sheet for standard 7/16" Zip. I would expect adding 1" foam sheets would be the less expensive route. Maybe I'm wrong.
I have already paid a 3rd party to develop a Manual-J, Manual-D, & Equipment selection. It sounds like the first place for me to start is to have them modify the Manual-J to include 1" of foam and review the impact???
Farm House,
You wrote, "The reason I didn't give as many details about the rest of the assembly is because my experience is that it distracts people from my question."
Fair enough. So what was your question?
Does it concern your roof assembly or your wall assembly?
Can you state your question, please?
Hey Martin- I have a concern for the environment, reducing fossil fuel emissions, etc...etc.... that's a given for me, but I don't have an unlimited budget and I'm certain that at some point during an envelope design, one starts spending money for very incremental improvements in performance.
A blanket/easy answer is: Yes, exterior foam will increase the whole house R-Value, performance, etc.....etc..... so do it.
The question is: Does it make good sense? Will the radiant barrier perform? Is increasing the stud-to-siding R-Value from 6.5 to 13 going to have a significant impact? For example: What percentage of heat loss or gain is expected through the 25% of the exterior walls that's made up of 2x6 studs? (if it impacts the answer- My goal is to achieve between 1 and 2 ACH50)
We all know that an internal combustion engine is an glorified air pump. Faster you can get the air to go from intake to exhaust the better the performance. At some point though..... you're spending silly money to increase performance that can only be justified if you race NASCAR every weekend. Catch my drift?
I realize... justification is in the eye of the beholder, but I value the opinions of those that write on this Q&A.
Farm,
Q. "Does it make good sense?"
A. Adding rigid foam to walls in your climate zone will yield lower returns than many other energy upgrades, as Dana accurately pointed out. You have evidently decided to focus on air-sealing -- I guess you are aiming for the Passivhaus goal of 0.6 ach50, since you told us that you will be "taking air sealing efforts about as far as one can go" -- which is a good idea. PV is probably next.
Q. "Will the radiant barrier perform?"
A. A radiant barrier is useless unless it faces an air space. In most cases, upgrades in insulation thickness are less expensive, and yield a better R-value return, than adding a radiant barrier.
Q."Is increasing the stud-to-siding R-Value from 6.5 to 13 going to have a significant impact?"
A. Yes, but not enough to justify the cost of the upgrade. Whether to do it depends on your goals.
Q. "What percentage of heat loss or gain is expected through the 25% of the exterior walls that's made up of 2x6 studs?"
A. You'll need an energy modeling program to figure that out.
Q. "My goal is to achieve between 1 and 2 ACH50."
A. That statement contradicts your earlier statement that you will be "taking air sealing efforts about as far as one can go."
Q. "Catch my drift?"
A. I think so. I think -- although you never told us -- that your questions concern your wall assembly, not your roof assembly.
Thanks Martin- I feel like you have answered my question. I really think I will be able to achieve less than 1 ACH50, but this is my first go at it and my builder builds tight houses, but has never attempted this tight. So, I don't want to be unrealistic.
Just concerning wall assembly. Not roof.
I appreciate your input (and others). Big fan of GBA!
The smallest Trane XV20i is 2 tons, and while it modulates it only has a ~2.5:1 turn-down ratio, which could be sub-optimally oversized for a higher-performance 2500' house in zone 3.
In a new house design it's not super hard to hit the 2500 square feet per ton of cooling range, and even a code-min house can hit the ton per 2000' range, even with full sun exposure. The minimum modulated output of the 2-ton Trane XV20i is about 10,000 BTU/hr at 95F outside and even higher at lower outdoor temps. That means it can't really modulate at high efficiency if your load at your 1% design condition is only 12-15,000 BTU/hr.
See Alllison Bailes' plot of square feet per ton against house size for a number of Manual-J's he has performed. Most of these houses are in climate zones 2A and 3A, and many of them aren't even up to current code-minimum. In a new house you should be able to beat the averages here by quite a bit:
https://www.greenbuildingadvisor.com/sites/default/files/images/Bailes%20graph%20for%20Manual%20J%20blog.preview.png
Before spending the "...serious money..." chasing HVAC efficiency numbers within a particular product line, figure out what the loads are, and whether that product line can even be reasonably sized for the load.
If the ducts and air handlers in an unconditioned attic above the insulation with duct-boot penetrations of the pressure envelope you will add about a half ton to ton of load and blow any efficiency gains of the more expensive equipment too, even with radiant barriers under the rafters.
Radiant barrier (aluminized plywood) roof sheathing may be worth something, but keeping the roof pitch at least 4:12 and using a CRRC rated "cool roof" shingle with an SRI greater than 50 would buy you more performance than that. But it would be difficult to measure the effects of either if you went ahead with 16" of cellulose in the attic (R60 at full depth, but ~R50-55 "whole assembly" after factoring in the thermal briding of trusses/joists). At those R-values using IR -opaque cellulose the roof gains really aren't a problem, unless you went ahead and put ducts & air handlers above the insulation layer.
Then again, shading a south facing 4:12 pitch with a solar array cuts the gains even more than with cool roof shingles or radiant barrier.
At a 25% framing fraction of with 5.5" R1.2/inch wood (~R6.6) with R20 cavity fill, the framing fraction accounts for roughly half the total heat transfer through walls.
But the walls are only a fraction of the total heat gain/loss, and with 2x6/R20 construction staying at code-min with the windows means the total window area can account for as much heat transfer as the total wall area (or more).
These sorts of issues is why modeling the house with BeOpt can be useful, since you can then determine the bang/buck of different component upgrades. That tool was conceived an an easier to use add-on for the DOE2 energy modeling tool, for the express reason of making performance upgrade financial optimizations easier.
BTW: Another way to beat the thermal bridging of the framing fraction without a full foam-over
Build with conventional 2x4 framing.
Take sheets of 2" ZIP-R, and rip it down to some 1.5" and 3" widths, and glue it to the conditioned space side of the framing (nailing it in place with a few nails) making a 5.5" depth, with the OSB side facing the interior, foam side contacting the stud. (The 3" strips go over doubled up top plates, etc) If labor is cheap (2" ZIP-R isn't cheap) you can make your own edge strips, using 1.5" polyiso + 1/2" CDX plywood. Use only foam-board construction adhesive if using unfaced or fiber faced rigid foam.
Use conventional insulation designed for 2x6 framing in the 5.5" cavites.
Wallboard is easily supported by the nailed & glued edge strips.
That brings the framing fraction up from ~R4.2 to about R14 cutting the heat transfer through the 2x4 framing by more than 2/3, and the whole-wall performance improves by about 15% compared to a 2x6/R20 wall at the same wall thickness.
Tips & details on this approach can be found in this article:
http://www.finehomebuilding.com/membership/pdf/9750/021250059.pdf
If using 1x3s as in the article instead of ripped ZIP-R you need 1.25" foam to hit a 5.5" cavity depth and there will be side- fit issues if batts are used, but it'll be a stiffer somewhat more robust edge strip (though often not as flat, given the amount of twist & warp you get with 1x 3 furring.)
Interesting discussion as I've researched a similar question, also for climate zone 3A. A table I received (can't find the source right now) indicates:
2x4 wall @ 16" oc, with R15 cavity insulation + R3 sheathing has an effective value of R16.2
2x6 wall @ 24" oc, with R21 cavity insulation + R0 sheathing has an effective value of R17.0
I learned the above 2x6 option, in addition to having a higher effective R value, is a stronger wall, and costs slightly less to build.
Assuming the above is accurate, and given budget limitations, forgoing exterior sheathing, and going with the above 2x6 options seems to be the better choice, however I don't see this particular option suggested by the experts, so I'm wondering why...
Hey Dana- Allison Bailes is who I used for the manual-J. They also produced a manual-d and equipment selection for Trane XV20i. I'm not concerned with oversizing the unit.
That's a pretty neat approach for ripping down Zip-R. I haven't heard that before but it sounds like it would work to me.
How can Allison run an accurate Manual-J before the wall & attic details are known?
If you go with the 2x4 + edge strip approach it makes a real performance difference, as do the window & roofing details.
Whatever the numbers were when the Manual-J was initiated, they need to be adjusted as the building design evolves.
Dana- the wall and attic details are known. I see a good bit of chatter online about exterior foam but when I ask builders and building supply houses around here they get a confused look on their face. Not so much with other green building techniques I ask about and pursue.
I had a feeling this was because adding foam doesn't make a lot of sense in my climate zone. This thread has confirmed my suspicions. F If I was an architect professor looking to impress my co-workers, I'm sure I would be all over it but I am not.
If you're talking about adding or not adding exterior foam to the walls (or edge strips) that fact alone means the U-factor of the walls are not yet known.
@Farm House
IMO it's not as simple as you think.
It depends on what state you live in. For example in Georgia (CZ3), the code minimum wall is still and will continue to be the 2x4. So adding exterior foam to a typical 2x4 wall might workout better from a cost perspective vs a 2x6 16" oc especially if one resides in the northern edge of CZ3 (Alpharetta GA) instead of some place south like Tifton.
Also if net-zero happens to be a goal some states in CZ3 are not as solar friendly (i.e. Georgia) so that might require revisiting exterior foam as well.
It just depends.
Thank you Dana for mentioning the Bonfiglione approach. I ran some R and U calculations to compare options on the whole-wall heat flow assuming wall area is 25% studs and 75% stud bays. Roxul batts and exterior boards. I set 2x4 with batts as my comparison. Chart attached.
If my calculations are correct, the Bonfiglione insulates better than a 2x4 wall with 1.25" of exterior insulation. One might say "well 1.25" is too thin," however, a 2" layer only buys you a 3% improvement compared the Bonfiglione wall.
In my own renovation, I can implement the Bonfiglione wall myself over a couple of weekends for the cost of some EPS strips, 1x3's, and the upgrade from 2x4 to 2x6 batts. That seems like nothing compared to the additional complication and expense of including an inches deep layer of insulation on all exterior walls.
Gordon,
If you could include 2x6 studs at 24" O.C. batts only in your table, that would be a useful 5th option to consider. Any chance of including that? I'd be interested to see how the 2x6 @ 24" O.C. compares to the 2x4 with foam edge strips @ 16" O.C. I'd expect the edge strips to win, but I'm curious as to the margin!
Brendan: A 2x6/R23 rock wool 24" o.c. spacing solution is fairly comparable to the 2x4/R15 at 16" o.c. spacing w/1.25" exterior rock wool solution. It can come in slightly better or slightly worse, depending on your presumed framing fraction for the 24" o.c. wall. Going with a full-on OVE/AF solution for the 2x6 wall it'll do slightly better than the presumptive 25% framing fraction 2x4/R15 + R5 c.i.
Brendan: Dana is correct, it depends on the % of wall is assumed to be framing. I don't know what an accurate estimate is but I ran the numbers for 25% vs 20% for 24" o.c. Chart attached.