Selecting an HVAC and hot water systems

We are building a new house. I need to select the guts for the heating/cooling. Solar and geothermal are not feasible. How does one whittle down the options/brands/models for a high efficiency (.95+) gas furnace? My builder is recommending a Trane furnace and cooling units. For hot water, he is suggesting tankless Navien units (NR-240A). I’m just not sure how to consider other brands and/or options. Any suggestions are greatly appreciated.
GBA Detail Library
A collection of one thousand construction details organized by climate and house part
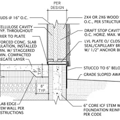
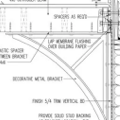
Replies
Can you provide any other details about your home? Knowing the size/layout/climate zone would all be very helpful so that folks here could provide some quality information. How many people living in the house? Lots of long showers?
This is a two-story contempory style house. 4 bedrooms upstairs with 2 baths. Downstairs has an open floor plan (kitchen, dining and living room with fireplace) with another bedroom. It is about 3200 sq ft. The house is zone 5A (western MA). There will be 4 living there (2 teenagers, aka hoolywood shower takers) with another 4-8 on the weekends when visitors come.
Sorry for not providing more details to start. Thanks.
Scott,
The brand and model of your furnace and water heater aren't that important. Choose equipment that is familiar to plumbers and heating contractors in your area so that the equipment can be easily serviced.
Here's what's really important:
- designing a tight, well insulated thermal envelope for your house;
- designing an efficient layout for your plumbing pipes; and
- careful design and installation of your duct system.
Get those details right, and the equipment choices don't really matter.
Without knowing the loads it's impossible to choose appropriate mechanical systems. If you take Martin's suggestion and spend the money on the highest-possible-efficiency-for-the-money building envelope the heating loads go down, and even the smallest condensing gas furnaces might be extreme overkill leading to lower, not higher comfort.
In fact, at IRC2009 code min R values and window U-factors (current code in MA), the smallest condensing gas furnaces are oversized for most 2000-2500' homes (but maybe not so oversized as to take a big hit in comfort), and more than big enough to handle a 3200' house. With a careful house and site design the loads can be brought lower still even without exceeding code min(!).
A tankless HW heater is actually a PITA to deal with (and the support reputation of Navien is spotty at best.) If you REALLY want to encourage your teenagers to take endless showers, but use less fuel than a tankless, get a 50 gallon condensing tank with a 75KBTU/hr burner (say, an A.O. Smith Vertex) and install a 4" x 48" (or 3" x 60") or bigger drainwater heat exchanger, which will deliver the same endless shower experience while using half the fuel. (see: http://www.witrendhome.com/media/watters-efi-powerpipe.pdf http://oee.nrcan.gc.ca/residential/personal/retrofit/13302 ) Most PowerPipe models are listed as a legally installable component under MA plumbing code- I'll dig it up for you if you like. EFI will sell at the wholesale price in qty=1 if you open an account with them over the phone with a credit card, and they don't mark up shipping. Last time I bought one it had to ship from their WI facility rather than their MA headquarters but it wasn't very much money.
A condensing hot water heater with a 75K burner and a 50%+ efficiency drainwater heat exchanger will keep up with shower flows greater than 2.5gpm literally forever (which is why I set the time-out on the motion-detector light switch in the bathroom to about 10 minutes, or my son would hang out in there for weeks at a time... ;-) ) My own HW system is an internan heat exchanger ona 48 gallon buffer tank on the heating system, supplied by a modulating boiler, but the modulated output never exceeds 60KBTU/hr output, even with all zones calling for heat while someone is in the shower. You'd make out just fine with the 76KBTU/hr Vertex + DWHX. Together will blow the Navien away on showering efficiency, (an effective efficiency greater than 100%, due to the recovered heat that would otherwise be literally going down the drain). It would be comparable to condensing tankless units on tub filling efficiency, etc. Only if you had a monster-tub to fill would a tankless be the better option. The ignition lag on some Naviens is notoriously long, making short-draws really wasteful and a pain from a "cold-water-sandwich" point of view. Seriously- get a tank, and back up the Hollywood showering set with a drainwater heat exchanger.
Open hearth fireplaces are an efficiency disaster, both as heating devices, and as a big hole in the thermal and pressure envelope of the house that is difficult to rectify. Air tight wood-burners with ducted combustion-air supply come with nice pretty windows for firelight ambience and 80%+ efficiency these days. If you size it right so that you can burn high enough long enough that the secondary burners are running most of the time, you hit the rated efficiency, and the viewing window stays fairly clean too- it may accumulate some ash-bits, but no creosote/soot to speak of. If you oversize it and keep it in a colder burning mode just to keep it from roasting you out it'll soot up the windows though.(Like I said, without knowing the actual loads, you have no clue as to what the right equipment would be.)
Even the best canned-fireplace solutions are lower than 25% efficiency, and properly air-sealing & insulating their flue chases is an afterthought to most contractors, requiring retrofit fixes. Masonry chimneys with air tight wood-burning inserts can hit the 70s for efficiency though.
Whatever woodburner you use, masonry chimneys on exterior walls are another big hole in the thermal envelope, that often have draft-induction problems. Putting the chimney & chimney-chase fully inside the thermal boundary of the house is important, but be sure to air-seal & fireblock the chase properly or it's just another big air infiltration driver sucking heat/coolth out of the house 24/365.
In a western MA climate ductless mini-split heat pumps will run at near geothermal efficiency, but getting satisfactory heating out of them in mid-winter or cooling at the July/August peaks requires some careful thought about the floor plan/layout, and room-by-room heating & cooling loads. On high-R houses you can often get there with one ductless head per floor, but at code-min you'd need more heads, which add considerably to cost. Most ducted heat pump solutions are at once too large and not large enough, and won't hit the efficiency numbers in this climate, but Daikin may have a reasonable variable-speed ducted mini-split solution up their sleeve after acquiring some Goodman air-handler technology recently.
It's not too tough to get a 3200' house to duck under 40,000BTU/hr @ 0F (Springfield's 99% outside design temp), and even under 30,000BTU/hr doesn't take superinsulation and world-class windows, but it's tough at code-min-everything. But either of those heat loads is within the scope of a ductless heat pump solution, if you preferred. If you're not on the gas grid and burning propane, heating with ductless would be dramatically less expensive too. From a comfort point of view as well as from a long-term NPV on lower utility costs point of view, there's a rationale for going 1.5-2x better than code-min, at least on walls and attic R, but maybe not window U-factor even with natural gas or heat pumps. As a starting point, take a look at the first chapter of this document, in particular Table 2, p10:
http://www.buildingscience.com/documents/reports/rr-1005-building-america-high-r-value-high-performance-residential-buildings-all-climate-zones
Note, those are "whole assembly-R", with the thermal bridging of the framing factored in. eg, an R30-ish wall starting at a code-min 2x6 would mean adding ~2.5" of rigid polyiso on the exterior of the 2x6/R20 wall. If your plan is to flip it 4 years it won't pay in other than comfort, but if you plan to stay there until your kids all die of old age the upgrades will pay for themselves many times over. Code min, even IRC2009 code-min isn't very aggressive, but WAY better than typical 1980s or earlier construction. (BTW: Reclaimed roofing foam can be had at 1/4-1/3 the cost of virgin stock from multiple vendors in MA. There's an uptick in labor costs going with exterior foam, but R-for-R reclaimed foam from commercial re-roofing & demolition is in the same range as batt insulation.)
I confirmed that the cooling load calc was 7-8 tons and was told that one furnace and condenser will provide only 5 tons. This is clarifying part of point 1 above.
Dana and Martin,
Great comments and insights. I also appreciated the outside references.
Let me provide a bit more info. The following is a high level summary of the "energy efficiency plan". Based on this plan, the target HERS rating is .62 (40% improvement over MA reference home).
Building Envelope:
-Basement Condition: Insulated, Unfinished NOT fullv heated
-Foundation Wall: Insulation Type = 2" polystyrene foam or Dow Thermax R-Value= 10+
-Slab Edqe and under slab at outer 4': Insulation type = 2" polystyrene foam R-Value= 10
-Rim & Band Joist: Insulation Type = 1" closed cell + 4.5" cell foam R-Value= 22.2
-Above Grade & Walkout Walls: insulation Type = 5.5" open cell foam + 1.5" exterior continuous polyisocyanurate foam board R-Value= 19.8 + 9 Grade=1
-Windows: U-value = .27 fixed, .29 operable SHGC =.22 fixed, .18 operable
-Glass doors: U-value = .28 inswing & sliders SHGC = .16 inswinq, .19 sliders
-Exterior Doors: Solid doors including to qaraqe U = .2 or lower
-Ceilings: insulation Type = 14" open cell foam + 2" min. polyisocyanurate exterior continuous; R-Value= 50.4 + 12 min.
-Blower Door Test: 4.5 ACH50 or better
-Thermal Enclosure Checklist Sections 3 5: Meet ALL checklist Requirements as verified by a HERS rater at pre-drywall and final inspection
Mechanical Specifications
-Heatinq Equipment : Propane furnace Efficiency: 95 AFUE
-Coolino Eouipment Tvpe: Central Efficiency: 14 SEER
-Water Heating: Type: On-demand e (2 units) Efficiency: .95 EF
-Duct Leakage 2 CFM per '100 sq ft conditioned floor area or less leakage to the outside at final inspection
-Duct Location: 100% within thermal envelope
-Whole House Ventilation (ASHRAE 62.2): Exhaust-only, 77 CFM continuous,24 watts or lower, adjustable speed
bath fan, 100 CFM+ full-speed capacity
Lighting and Appliances
Lighting: 80% or more compact fluorescent bulbs but will install LED
Refrigerator/Dishwasher Energy Star rated, 600 kWh per year or less/.70 Energy Factor
Questions:
(1) sizing the HVAC system: I am confirming the coolingload calcs but I think I heard that is was 7-8 tons (is that the correct metrics?). The furnace that is currently spec'd is 60,000BTU/hr and is TWO units. Your recommendation was 40,000BTU/hr. I obviously want to make sure that we size the unit(s) correctly and thus would appreciate any thoughts based on the plan above.
(2) Fireplace - completely understand your comments on this topic. Currently spec'd for a simple insert that is not efficient. I am struggling to find contemporary style efficient models. I found one that is .76% efficient and very cool looking but it is very expensive ($8K). If you ever are in need of a high efficient insert and price is not an issue check it out: the model is Phenix 120 by Bodnay & Godard (spec sheet: http://www.wittus.com/catalogs/phenix%20green%20web.pdf ). Any other brands worth exploring?
(3) ERV system - the plan above has for an HRV but I was thinking of installing an ERV instead even though my location is about on the "line". Does this need to be considered in sizing the HVAC system? Any other thoughts?
(4) Hot water heater - I hear you about the Vertex option. Unfortunately, our crawl space is small and I dont think this unit would fit. I need to confirm with builder.
(5) any other comments based on the plan above.
Thanks for the incredible insights.
Scott
60KBTU/hr is an insane heat load for a 3200 house with those U-factors & R values, even if you're fully heating the basement. But with a continuously variable or 2-stage system it won't affect comfort much.
7-8 tons of cooling load in a house like that would be off the charts- it means most or of your glass is unshaded facing west or that you have 18 people partying inside with multiple game machines running on multiple huge flat screen TVs while someone is roasting multiple 4th of July turkeys in multiple ovens. That's literally more than 25,000 watts of heat you'd be needing to be removing at the peak load condition- where is it all coming from? You'd need to have a HUGE solar gain at the worst time of day (mid afternoon) or be running a 100A 240VAC service at it's hard limits to come up with that much load. Old school hacks use rules of thumb like "a ton per 500 feet of space, add a ton just to be sure", which may be how they came up with 7-8 tons? (The same hacks use 25BTU/foot for heating loads on new houses, 35BTU/foot for older houses, and are dead-wrong on both.)
Even 1-ton per 1000' of conditioned space cooling would be on the high side for MA, which would put you at ~3 tons, not 5. And 60,000/3200= 19 BTU/foot, which is more typical of not-so-tight circa 1960 houses. Suffice to say, I suspect there are some discrepancies in the load calculation methods, or you have WAY too much glass.
I haven't done the heat load calc on this house and thus haven't recommended 40,000BTU/hr, but that's a totally achievable number for a 3000-4000' "better than code" house. C'mon, my sub-code 2400' antique is under 40K, @ 0Fat half your whole-wall R values! I'm hitting about 15BTU/ft of fully conditioned space, and if I count the semi-conditioned basement it's about 10BTU/ft. My glazing fractions are modest, but I don't live in the dingy dark either, but the glazing performance is about U0.5, not U0.18-U0.29. Either something is amiss in the load calculations, or you have a glass house.
At 4.5 ACH/50 you'd beat IRC 2009 code max, but that would exceed IRC2012 levels by 50%- that's a pretty low hurdle to clear if you're paying attention, if more than a mere stripe on the floor.
A 60K furnace and a pair of 200K hot water heaters is going to up-size your propane plumbing significantly. Even a pair of 76K Vertex w/ DWHX will provide better peak hot water flow, higher net efficiency, and waste less water, and would ease the propane regulator & line capacity issues. If one of those hot water heaters isn't serving more than one shower, if it can be served by a heat pump hot water heater it would reduce the cooling loads a bit (particularly the latent cooling load in the basement.)
If you really have no place to put the tank, but can squeeze in even a 4" x 30" drainwater heat exchanger, the payback in reduced propane use is remarkably short at todays propane prices and your anticipated showering loads. The fattest & tallest one that actually fits the space will have the shortest payback period, and the highest efficiency. (In my house at current natural gas prices & our relatively low showering use the payback is pretty long on fuel cost, but the reason for installing it was as much about net capacity during simultaneous heating & shower use as it was for the fuel savings.)
If you can replace the sub-slab XPS with Type-II (or Type-IX, if the inspectors insist on higher compression ratings, which it doesn't really need) EPS it would be a lot greener from a lifecycle greenhouse gas emissions point of view. Type-II EPS is usually cheaper than XPS R for R, and Type-IX is usually a wash, sometimes slightly cheaper, but not always. XPS is blown with HFC134a, which has about 1400x CO2 global warming potential, whereas EPS is blown with pentane @ ~7x CO2 GWP. Under an unheated slab the greenhouse payback on the R value of the XPS in reduced propane CO2 emissions is never in this application, and in 50-60 years when all of that blowing agent has leaked out it's R value will be identical to EPS of similar density. At 2.5" EPS would deliver R10 now, and R10 forever, and the global warming hit from the pentane is paid back in under a decade.
If the chimney is masonry on an exterior wall even a really great insert won't be hitting anywhere near it's efficiency numbers unless you insulate the outside of the chimney to a fairly high R.
For the more contemporary look in woodburners, the Hearthstone Tula(http://www.hearthstonestoves.com/wood-stoves/stove-details?product_id=36 ) or Bari (http://www.hearthstonestoves.com/wood-stoves/stove-details?product_id=27) woodstoves over any insert type fireplace, but clearly YMMV. Any of the imported European woodburners like the Wittus come with a serious premium. But once you're in the $8K range I'd be looking at a massive masonry heater like a Tulikivi or something over a Wittus on raw comfort alone.
At current propane prices getting a better handle on the true loads and looking seriously a ductless air source heat pump solutions may be in order. Sure, propane burners are dirt-cheap equipment by comparison, but a ductless would cost less than half to run, and would have a miniscule carbon footprint by comparison. See RMI's recent take on it: http://www.rmi.org/PDF_heat_pumps_an_alternative_to_oil_heat_in_the_northeast
BTW: If the 2" iso is on the exterior of the open cell foam with a roof deck between them, the roof R-ratios do not meet IRC prescriptive code for this area- you need at least R20 of the R50 total to be on the exterior to protect the roof deck from interior moisture drives in the winter.