Seeking insulation recommendations

I work with Habitat for Humanity in upstate SC (zone 3 – warm-humid), and we are researching practices to improve the energy efficiency of the houses we build.
We have been insulating the attic ceiling with blown-in fiberglass but are leaning towards insulating the whole building envelope now (cathedral ceilings and sealed crawlspaces).
First, is it cost-effective to put the HVAC unit and ductwork in the conditioned attic rather than the crawlspace?
Second, what type of insulation should we use in the roof?
We received a quote for closed-cell spray foam from Icynene, but the cost is pretty hefty, and that’s with them offering only R-20 (5.5″).
Open-cell spray foam, as I’ve been reading on these forums, seems to be somewhat out-of-the-question because of potential moisture issues.
We were looking at the Cool-Vent SIP product to combine with an air-permeable insulation to achieve an unvented attic, but the installation did not look to be suitable to use with volunteers, and that too seemed a little too pricey.
So, it seems a vented attic would be preferable. But what insulation should we use? Right now, the top cords of our truss members are 2×4’s.
Thanks,
Dylan
GBA Detail Library
A collection of one thousand construction details organized by climate and house part
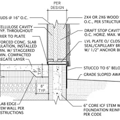
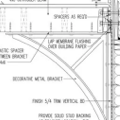
Replies
Dylan,
If it's possible to put your HVAC equipment in a sealed crawl space, that's certainly preferable to putting the equipment in an unconditioned attic. Just make sure that you know where all your ducts will be running, and make sure that all of your ducts are within the conditioned space.
If you end up with a vented unconditioned attic, blown-in fiberglass can work -- it just has to be very, very deep, because blown-in fiberglass has such a low R-value (about R-2.0 to R-2.7 per inch). In almost all respects, cellulose is a better insulation material for attic floors than blown-in cellulose.
Don't settle for R-20 roof insulation. Even though spray foam installers try to tell you different, R-20 roof insulation is a code violation -- the R-value is below minimum code requirements.
+1 for putting the HVAC in a sealed insulated crawl rather than in the attic.
The details of doing a vented unconditioned attic may also may take some training for volunteers to get right. Building with energy heel trusses, air sealing the ceiling plane and blowing in a foot of cellulose in there is more straightforward, (and cheaper.) Cellulose is preferred to fiberglass in an open-blown attic due to both it's higher air retardency and it's better opacity to infra-red radiation coming off a hot roof deck in summer, yielding somewhat higher performance at any given R value. (Fiberglass would need a top-side air barrier to perform at it's rated performance under all conditions.)
Dylan,
I live in Upstate SC also and have been looking at the same kind of things. We built a house that is incredibly comfortable for this area. My brother keeps his 1300 sq. ft. house in the low 60s (thermostat set at 62-64) during the summer and his electric bill is about $60. We did do pretty extensive air sealing with external insulation as well as dense pack cellulose.
I've also done under the floor insulation which is a serious pain - you are right to go with a sealed (insulated?) crawlspace - that would provide a much healthier environment for the homeowners as well as reducing energy costs.
You came to right place to get advice. These guys are incredibly generous with their time and knowledge when you have questions about building a more energy efficient structure.
Thank you all for your willingness to help. Lucy, I agree - this is a great site with a wealth of information and people committed to sharing their expertise. I have gone from knowing almost nothing about building an energy-efficient house to feeling like I have at least somewhat of a grasp on what factors are important and what details to pay attention to.
We would like to have the same floor plan and technical details for all of the houses we build to simplify the construction process. So, whether we build on a slab or a crawlspace, depending on the slope of the property, we would like to have the least possible amount of change between houses.
Thus, rather than putting the HVAC system in a sealed crawlspace (which we couldn't do on a slab house), we're talking about putting the system in a closet off the hallway and having ductwork run through a drop ceiling in this hallway to all the rooms in the house.
If we end up going with cellulose to insulate our attic floor, any recommendation for choosing between dense-packed and wet spray?
And, for the drop ceiling, would it be wise simply to fill the cavity around and on top of the ductwork with cellulose? Would we need to do any additional insulating/air sealing?
As for condensation forming on insulation around the ductwork in this situation, is this something to be concerned about? And if so, what could we do to prevent this?
Lucy, would you mind giving details of how you achieved "extensive air sealing?"
Dylan,
Q. "If we end up going with cellulose to insulate our attic floor, any recommendation for choosing between dense-packed and wet spray?"
A. When installed on an attic floor, the cellulose is installed with the "loose-fill" method.
Dense packing and wet-spray are approaches used for walls (or, in the case of dense-packing, for closed framing cavities).
When you say "drop ceiling," are you referring to a suspended ceiling or simply a lower ceiling than the rest of the rooms?
In either case, the ductwork should go below the ceiling air barrier in order to count as being within conditioned space. Your truss company may be able to provide a raised area in the middle in order to form a ductwork chase.
Dylan,
Air sealing is a perfect job for volunteers. My brother's house was built by 2-3 carpenters, me (the air sealer, insulation tyrant and board hauler), my brother (the cabinet maker), then plumbing, HVAC, and an insulation company for the dense pack cellulose. I figure no one air seals better than the people it impacts the most and technically, it is an easy job so that's why I took it on. Also I had been studying it for years on the web, particularly this site.
For attic insulation, loose fill cellulose is also an extremely easy job technically for volunteers. I've done that before as well. It's not particularly fun for most people (though I do consider insulation fun), but it is easy to do.
Martin wrote a great article in 2014 about insulating with cellulose using the blower from a big box store. Link below.
https://www.greenbuildingadvisor.com/blogs/dept/musings/borrowing-cellulose-blower-big-box-store
This article covers information from cellulose installers - very useful general information. https://www.greenbuildingadvisor.com/blogs/dept/musings/how-install-cellulose-insulation
Information on air sealing an attic.
https://www.greenbuildingadvisor.com/blogs/dept/musings/air-sealing-attic
I have a blog that I haven't updated lately, but it has a bunch of information on the air sealing I've done. http://greenvillegreen.blogspot.com. Just click on the air sealing label - the most recent posts are from air sealing my attic. The older posts are air sealing my brother's house. It is much easier to air seal a new building versus at 60 year old house. Also, I believe in redundancy in air sealing. I don't think air sealing at only one layer is sufficient. Martin and Dana may disagree, but I think you've got to do it at 2 layers in case there is a penetration or the tape fails or whatever. We actually did 3 layers - exterior taping, interior taping with some Prosoco joint and seam sealer or canned foam and then taping the air barrier Intello membrane which held the dense pack cellulose in place as well. We still do not get the air tightness that I hoped for - largely because of HVAC, plumbing penetrations I think.
I hope this helps a little bit. I am so excited to hear about Habitat moving in this direction. It will mean so much to the people who move into the home they helped build. Also it may have an additional benefit of educating people about the value of air sealing and insulation beyond code minimums.
Reid, thank you for the tip - our truss company will make the modifications to allow for the ducts to run underneath them. We will no longer do a drop ceiling - now, we will place OSB/plywood over the ducts, seal the seams, and place our blown-in insulation on top of this hump. I'm not sure this will be considered "conditioned space," but it would seem to be close enough with insulation on top and only the drywall separating it from the conditioned space.
Lucy, thanks for all your help and resources. I agree that blown-in cellulose would be a good choice, but we have been doing blown-in mineral wool, and we just purchased a blower machine - and I'm not sure if the machine is particular to mineral wool or if other materials could be used in it.
On a different note, we will probably be switching from 2x4 16" spacing to 2x4 24" spacing for our walls, and we will do in-line framing (lining up our floor joists, studs, and roof trusses). However, we've been doing vinyl siding and would like to continue if we can. But with studs 24" apart, how can we comply with the 16" spacing that the siding manufacturer calls for?
Our current wall is: Fiberglass batts --> OSB --> Dow XPS --> housewrap --> siding
Can the siding just nail into the OSB and not the studs?
I think you want to use drywall or plywood (and sealed seams) to box in the duct tunnel. Then it will be within the conditioned space. See page 17 in this document: https://ductsinside.files.wordpress.com/2011/04/ducts-inside-training-manual.pdf
Martin or Dana will chime in if I am offering misinformation. ;-)
Thanks for that resource, Steve. I noticed in there that ductless minisplits are recommended for houses less than 2,000 sq ft with open floor plans. I wonder if this would be worth looking into to replace our central HVAC unit....
Also, does anyone have any recommendations for what to do regarding the vinyl siding:
On a different note, we will probably be switching from 2x4 16" spacing to 2x4 24" spacing for our walls, and we will do in-line framing (lining up our floor joists, studs, and roof trusses). However, we've been doing vinyl siding and would like to continue if we can. But with studs 24" apart, how can we comply with the 16" spacing that the siding manufacturer calls for?
Our current wall is: Drywall --> fiberglass batts --> OSB --> Dow XPS --> housewrap --> siding
Can the siding just nail into the OSB and not the studs?
Run the Manual-J load calculations before picking the equipment, but yes, mini-splits are often the most appropriate solutions for smaller code-min houses (or even sub-code houses.) There's a ~1400' bungalow built in the 1950s in my neighborhood being heated & cooled (with margin to spare at the +5F outside design temp) by a pair of 3/4 ton Fujitsus. In a small house with an insulated crawlspace to accommodate some short duct runs it doesn't even have to be an open floor plan- there are some pretty good mini-duct cassette type mini-splits out there.
At the modest +22F +32F 99% outside design temps typical of SC heat loads of tight code min houses are typically on the order of 10 BTU/hr per square foot of conditioned space, and cooling loads on the order of a ton per 1000'. A 1.5 ton mini-split is usually good for over 20,000 BTU/hr at +22F, and would cover most 1500' houses. A slightly better than code 1500' house can even be within range of a 1 ton. The rated cooling capacity of a 1-ton is 12,000 BTU/hr but they aren't usually rated & tested at their maximum & full capacity, which is usually 1000-3000 BTU/higher.
Is there any way to convince you to use an inch of polyiso or EPS rather than XPS, or is that a function of donated materials?
XPS is blown with HFCs, which are powerful greenhouse gases (more than 1000x CO2 @ 100 years) that escape over the course of a few decades. Before 50 years are up you can't expect more than R4.2 or so out of that R5 labeled inch. An inch of foil-faced polyisocyanurate is blown with pentane (about 7x CO2 @ 100 years) labeled R6 or so but will eventually drop to R5-R5.5 in average performance. An inch of 1.5lb density (aka "Type-II") EPS also blown with pentane, (often recaptured at the factory and burned for process heat) and performs at R4.2 today, tomorrow, and pretty much forever, and it's cheaper than XPS. Foil faced polyiso is the easiest to air seal using appropriate temperature rated foil tapes, and has the highest truly long term performance. And with the inherent air space behind vinyl siding the foil facer adds another ~R0.5-R1 to the whole-wall performance.
Most 16" o.c. type vinyl siding can be nailed to structural OSB sheathing rather than directly to studs. It usually meets both code and manufacturers' specs as long as...
...the OSB is at least 7/16" thick (for OSB has to be structural at 24" o.c. stud spacing means it already has to be a minimum of 7/16" )...
...using ring shank or standard nails at the 16"o.c. spacing...
...with a ring shank nailed through at every stud.
For long-nailing through 1" foam it makes sense to use ring shank nails even on the 16" o.c. spacing, not just the extra at the studs, even if that isn't required by code or manufacturer.
If it's 3/8" OSB the wall usually needs let-in bracing or shear panels for structure, and the use of ring shank everywhere for the siding becomes a requirement, not just at the studs (and not all manufacturers would sign off on that, whereas most will with 7/16" OSB.)
This document has some short-sheet descriptions /slides regarding 24" o.c spacing, vinyl siding & 1"-1.5" foam that are relevant to your stackup:
http://energy.gov/sites/prod/files/2015/02/f19/ba_webinar_2-12-15_kochkin.pdf
Dylan,
I don't know much about minisplits in the South which would be true for most homeowners as well. I'm not sure people here "get" them. The only time I've seen them used is in poorly insulated upstairs bedrooms to make sleeping more comfortable.
What I'm saying is that for high tech energy efficient products, usually there must be some user familiarity for the product to perform as designed and I don't know if that is the case here. Also I am unsure about how well they can be serviced as they are less familiar to the HVAC technicians here.
Martin and Dana will probably know how user dependent these products are.
On the other hand, effective air sealing and insulation are kind of idiot proof. The major issue in the Southern summer is dealing with humidity. I often have to set my thermostat lower than I need just to deal with humidity (usually when cooking). My 1950s ranch is not nearly as efficient as my brother's house but I have done a lot to make it better - 2 inches of polyiso all around the outside of the house, rain screen with new siding, new windows and doors, improved insulation in the attic (from a sketchy R-5 to a much better, fairly well air-sealed R 20).
So a homeowner in this area with a well-insulated, air sealed house will have to know to run the kitchen fan while cooking and the bathroom fan for 15 mins after showering or bathing to reduce indoor humidity - concepts that are easily grasped.
I realize a minisplit solves the duct issue, but it may cause other issues that are more difficult to resolve. I look forward to additional information on this.
RE “Early” adopters of minisplits:
Lucy, I understand what you’re saying about people installing equipment that is not familiar to them, or that they don’t understand. But, if you believe what you read on this website and others that pay attention to energy efficiency in residential housing, there are precious few existing houses that have good design (including Manual J’s and ductwork design), good sealed ductwork, or have been commissioned, and then there’s the separate issue of putting ductwork outside the conditioned space. Basically, either the HVAC people don’t understand the conventional systems and equipment they are designing (?) and installing, or they have been forced to cut every corner to compete with the incompetent shysters that are providing competing quotes. Broad brush strokes, to be sure, but that’s the overall impression.
To me, the ductless minisplit is much closer to a solution in a box. Yes, you must accurately size the system after calculating loads, but you’re supposed to do that for any system. I’m hopeful that minisplits have the ability to eliminate a majority of the issues that accompany fully ducted heating and cooling systems.
I suspect that using minisplits will eliminate more issues than they create, and the second installation will be much easier than the first. I wish our local Habitat was moving faster in this direction.
I completely agree with you that air sealing is critical, along with eliminating thermal bridging, and that those improvements in the building envelope pay dividends starting immediately. [Don’t think I’m putting any words in your mouth, my apologies if I did.]
Dana,
I agree - polyiso or EPS would be better solutions; but the XPS is a donation to our affiliate from Dow.
Thank you for the document describing requirements for vinyl siding fastening specs. We plan to use ring shank nails every 12" (one in every stud and one in between).
Thank you, Lucy, and Andrew also for the thoughts on minisplits. We are trying to find out the possibility of utilizing these in our new houses, but our HVAC contractor does not seem eager to meet with us to discuss the possibility of the switch (I guess because they would not be making as much money with the change).
On a separate note, we are going to start receiving denim insulation through Bonded Logic. We will definitely request R-13 batts for walls, but what do you all think about using it for the walls of a sealed crawlspace? Do you foresee any issues with that?
Dylan,
You can't use denim insulation on the interior of crawl space walls, because crawl spaces tend to be damp. You need an insulation that is unaffected by moisture -- either rigid foam or spray polyurethane foam.
For more information, see Building an Unvented Crawl Space.