Scissor trusses and wood fiber batts

kate.h
| Posted in GBA Pro Help on
I am already sheepish about posting a question about insulating a cathedral-ish ceiling, using scissor trusses, and not having a definitive insulation plan dialed in..
But here goes:
We are building our own house in western Massachusetts, climate zone 5. We’re planning to use scissor trusses that have a 9 pitch roof and a 7 or 8 pitch ceiling. I wanted folks opinion on a plan to use the wood fiber batts from TimberHP and put 3 layers of 5.5” batts in the ceiling. They seem rigid enough that they could friction fit in the truss bays though filling between the webbing is a question- any opinions there? If they have a snug fit, is there a reason we can’t just install them such that they are flush to the bottom cord of the truss and all the space above creates a natural vent channel and would vent soffit to ridge? The truss design has a 2’3” heal cut but the triple stack of wood fiber batts would only equal 16.5” of insulation for an R-value of roughly 49. We are using intello as an interior air barrier so that would be attached to bottom cord, then 2x strapping for service cavity, then drywall. If this could work, we could avoid making or buying vent channel baffles or doing the double sheathed roof with battens and mento which would be cool to avoid if possible. If that could work, we could sheath on top of trusses and then use a non vapor smart wrb and then metal roof?
For the wall assembly, we are planning for drywall, 2x service cavity, intello, 2×6 frame with timberhp batts, 5/8” plywood, mento WRB, 2” rigid insulation (most likely recycled xps), 1x or 2x rain screen battens, wood siding (likely vertical)
Does this all make sense?
Thanks for any thoughts,
Kate
Thanks for any thoughts,
Kate
GBA Detail Library
A collection of one thousand construction details organized by climate and house part
Search and download construction details
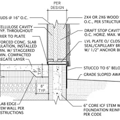
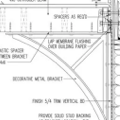
Replies
Cutting insulation to fill the webs will be vastly more labor than detailing vent baffles. Depending on the depth of the truss you will only need baffles extending for the first few feet off the eave. I think using anything besides cellulose for this situation would be crazy.
strausjw,
On an 8/12 scissor trussed roof you need to enclose and dense-pack the cellulose or it will all shift. The truss space gets higher as it rises, so you would also need some way of limiting it to reasonable depth, or you would end up too much near the peak.
@malcolmtaylor @michaelmaines
Thank you both for the earlier replies. I really appreciate it. I’m back with some follow-up questions as we try to pin down a plan. It seems clear that the only blown in application that would work for us with the 7:12 ceiling pitch would be dense pack. But as you mentioned Malcolm, this would require limiting the space above somehow and as I’ve been trying to wrap my mind around doing that with the truss webs, i keep coming back to thinking maybe it doesn’t actually seem simpler than notching the TimberHP batts within the webs. But maybe I’m not thinking of the right material to use to contain a dense-pack in this scenario with webbed trusses that are 18” at the heal, 7pitch ceiling, 9 pitch roof.
If we are to go with batts, could we just leave the space above them open as a vent channel with no added baffle? We could get 16+” of batts from eave to ridge but wondering about if we need a barrier/baffle material between the insulation and all that air space above especially towards the peak?
Thank you truly, for your valuable expertise…
Kate
Kate,
I hate to say it but there aren't any great options:
https://www.greenbuildingadvisor.com/article/insulating-scissors-trusses
Kate, cutting TimberHP batts are quite stiff, nothing like fiberglass batts, more like mineral wool batts but even stiffer. They make a nice friction fit between framing members. Working with them is essentially carpentry, so you would need to notch carefully around every truss web. You would need to fill large gaps with pieces of insulation. I think it's very do-able, just a lot of work. Have you considered having wood fiber or cellulose blown in instead? That's usually much simpler when working with truss roofs.
Otherwise your plan sounds fine. There is no need to have a variable permeance membrane under your roofing; regular, synthetic underlayment will be fine.
Thanks for the feedback. All that notching does sound like it might not be worth it…
In a combined follow up question to these responses, if we did blown in, it makes sense that it would need to be dense packed because of the pitch. Could we install baffles to hold back the blown in at a reasonable depth towards the peak? Would they be parallel to bottom cord, creating say a 2’ cavity for insulation all the way to the ridge but with 3” of vent at the eaves and obviously more as it goes up?
Lastly, is it reasonable to rely on the Intello with the service cavity battens already installed to sufficiently hold back a dense pack?
Thanks so much for the advice…
Kate
I've done vertical baffles before to try to keep cellulose in place on an incline. I would say it "kinda sorta" works. What you end up with is a sort of terraced insulation layer, think the ancient farms cut into the sides of mountains. That works, but it's not ideal. Vertical baffles and cellulose is probably still easier than cutting wood fiber batts (I've never worked with those though), just keep in mind you'll probably end up using more cellulose than expected since you won't have an even layer. I'd try to target the minimum depth areas at the top of each baffled compartment to be your minimum R value, then let the lower parts "overfill" a bit. You're still likely to get some shifting over time, but it won't be as a bad as it would be without the baffles.
Bill
I'm doing my own house with Timber HP batts right now. We are using dense pack on the cathedral ceilings, so not your exact application. Regardless, they batts are certainly stiff enough to friction fit between the trusses. One approach would be to find used 1-1/2" rigid insulation and cut that to fit the triangles between the truss chords; then you would be able to do simpler cuts on the batts.
FWIW, we have found the best tool to cut the batts is a very sharp machete.
Thank you so much for this input- the recycled 1.5” rigid in the web triangles was exactly what we’ve been thinking and then the batts friction fit- it seems like though labor intensive (and if we had to do over we’d avoid the scissor trusses all together) I feel like the timberhp batts feel like the best solution to avoid having to contain dense pack or to block/baffle for blown in. I’m just wondering if we do that, if there needs to be anything between the upper face of the batt and the vent space before the underside of roof sheathing. Any thought there?
Kate,
No you are fine leaving the batts uncovered. The losses due to wind-washing will be minimal.
That need for a "back side" air barrier is less of an issue with denser insulating materials. Low density fiberglass batts, especially when oriented vertically (think R11 in attic kneewalls) could take a significant performance hit if they didn't have an air barrier on the back (attic) side. Mineral wool is much less affected by that missing air barrier.
Horizontal, or mostly horizontal applications like yours, are less of an issue, and dense insulating materials like woodfiber batts really won't see a significant performance impact here. If anything, just put a baffle out at the eave where the end of the batt is perpindicular to incoming airflow. (that's the worst-case place for wind washing) The rest of the vent channel isn't an issue at all.
Bill
If your trusses are not too deep, you can do loose fill. Even if you need more of it, this tends to be the cheapest insulation and least labor.
One option is to install regular baffles and frame in a mini attic near the peak. You then loose fill the trusses and overfill this mini attic area. Any settling in the sloped section would then be take up from the extra fill in the mini attic.
The mini attic doesn't have to be that big, just enough for access, plus a bit of flat ceiling makes installing light fixtures and fans much easier. Access to this space could be through an oversized gable vent from the outside.
Kate,
I have built certified Passive Houses (Phius) with scissors trusses and loose fill insulation. My trusses have been lower than yours--7/12 exterior and 4/12 interior. To maintain the insulation thickness I staple Insulweb fabric to battens above the bottom chord--in my case, 24" above, with raised heels to allow a minimum 2" air channel at the choke point. At the bottom I used Siga Majrex for my current project, and particularly like Siga's double-sided tape. I add 1x furring 16" o/c to support the weight of the insulation, and provide a channel for low-voltage DC lighting--my first use of LumenCache Renata. I used TimberHP loose fill this time and like it; previously I used cellulose. This isn't dense packed though I use a two-motor machine. Since the insulation is contained between two fabrics a colleague and I call it "snuggle packed"--unlikely to settle or shift. One photo shows blowing the insulation, which eventually fully filled the space. I'd rather not try to fit batts around trusses, my only origami is with the Insulweb, which I have down to a reasonably simple layout.
The structure is autoclaved aerated concrete (AAC), my favorite structural material since the 1990s. The AAC is wrapped with 6" of Rockwool Comfortboard 80, with U-Stucco, hydrophobic, permeable stucco directly applied to the mineral wool--likely the first demonstration of this method in the US and Canada.
This is a duplex on NY 23 in Hillsdale NY, a few hundred feet west of NY22. I keep my projects open for tours for a few years; drop by if you'd like. After completion one duplex will be available for short-term rentals so others can experience an AAC Passive House. GreenspringBuilding.com