SCIPs Please?

I’ve been reading about SCIPs (Structural Concrete Insulated Panels) as another approach to my hopeful project for a single story ranch in Zone 3. I’m not finding objective (i.e., third party) information on SCIP performance and, even more, on detailing them as walls or other panels in a building enclosure.
I could go to the individual mfgrs, but would love to find I’d missed something here, or at BSC …
I’m guessing SCIPs will be pricey for me, even though mfgrs promise labor is severely reduced by the all-in-one approach. But, just in case they’re the best thing since sliced raisin bread, does anyone have links to info re:
SCIP as barriers: air, vapor or WRBs especially?
Sealing SCIPs at slab intersections?
Roof detailing at SCIP intersections?
Flashing windows/doors?
Or is it as simple as to compare SCIP to any masonry wall for detailing? If so, how would I compare the permeance (as an example) of “5700 psi shotcrete (gunite)” to other masonry systems?
Thanks in advance
Joe W
GBA Detail Library
A collection of one thousand construction details organized by climate and house part
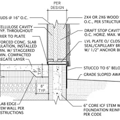
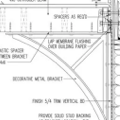
Replies
Since SCIP is a term that probably few have ever heard, perhaps you can list the specific wall systems you're considering. I assume it's something like Superior Walls? If so, there are many liabilities to such a system.
Sure, Robert, here are some links I’ve read. An informational faq:
http://www.ecotechbuildersinc.com/faq-all.html
And three companies. (Envirolast is fairly local, but unlike Superior the concrete work seems to occur on site rather than being shipped.)
http://www.envirolaststructures.com/home.html
http://www.metrockscip.com/
http://www.tridipanel.org/index.htm
As you see, it's basically an SIP out of concrete ("shotcrete") instead of OSB.
Joe W
Most of these systems were originally developed for commercial construction and are considered cost-effective where detailing is minimal and repetition of panel design is high. This is by and large not a great fit for single-family residential construction. Detailing is certainly not comparable to 'any other masonry' if by that you mean brick and block.
That aside, the principal components of these systems have little to recommend them as 'green' materials. The concrete and foam insulation both have high embodied energy and the panels are difficult to modify any time in the future without a major kludge. Sometime in the life of the building the need to remodel the exterior enclosure will arise and that time may come sooner than you think.
Wood framing and cellulose insulation are the greenest construction materials available in most of North America. They represent a level of long-term carbon-sequestrationwhich is available with no other construction materials and are re-usable, compostable and recyclable at the end of a long useful life. There's no good reason to look much further other than the quest for novelty, which is the most questionable of all the green motivations.
"Wood framing and cellulose insulation are the greenest construction materials available...."
Certainly I'm not prepared to dispute that fact, James. And thank you for weighing in. Wood/cellulose (or BIB) is my current thought ....
But then I read about SCIP in the GBA product guide. Yes,the origins and mfg of the components are unfriendly, but the panels are touted as efficient in energy conservation. Like all SIPs, they offer simple design and installation, and concrete SCIPs would provide exceptional durability.
But if they can't be detailed effectively, there's not much point, I think. And clearly, working with concrete would be quite different from what I'm used to. But concrete and stucco and SIP design combined, as this approach seems to be, offer different design opportunities (which I'd like) so I'm seeking info on detailing them.
If, as you say, their detailing is quite different from brick and block, what would it involve to join a SCIP wall to its roof or slab? How would you install and flash doors and windows?
Best wishes,
Joe W
Joe,
I think it's a stretch to call these products SIPS, because unlike all other SIPS sandwich panels (all of which are fabricated offsite) they have a steel truss penetrating the foam thermal barrier. But off-site fabrication and shipping of concrete wall panels, like with Superior Walls, merely adds high transportation costs on top of the other embodied energy of the system.
From my perspective, the most effective and justifiable use of a concrete/foam sandwich is the ThermoMass system (a true CIC), but only as a replacement for a conventional concrete foundation insulated on the exterior. This CIC, while not offering as much R-value as the walls you mention (but also not needing so much R-value underground), does offer considerable dynamic mass benefit (which a thin Gunnite would not).
Robert, you're aware that the the foam & truss are shipped but that the concrete is done onsite?
And I gather that this is a case where the thermal mass is reflected in the additional weight of the "true CIC" vs the "5700 psi shotcrete"?
And you're right that I find the enclosed insulation an attractive feature -- especially in this climate (zone 3) where thermal mass is less of an issue than termite infestation.
Thanks for your time.
Joe W
Joe,
Though sometimes confused with SCIPs, Superior Walls are different in many ways than (SCIP) Structural Concrete Insulated Panels. The Superior Walls panels are constructed in third party inspected factories under controlled environmental conditions so you will be provided with a quality product every time. Superior Walls panels are 5000 psi precast concrete and they are designed as a residential foundation wall but they are also used frequently as above grade walls. The standard insulation is located on the inside of the foundation wall so there is no concern about termites; two standard R-values are usually offered and you can choose the one that meets the energy code in your area. Additional insulation can be added for above grade applications. Go to http://www.superiorwalls.com and you will find a wide of assortment of product details in our builder guideline booklet, and in the design professional section of the website including roof details, panel to panel connections, and slab to wall connections. If you are creating slab on grade design or are using a heated slab we can provide you with special details if you call our office. You can also use the Rep Locator to find a factory near you. Superior Walls panels are also NAHB green approved product eligible to receive points toward a National Green Building Certification. Technical Staff is always available to answer your questions. Just click the contact us buttion at the bottom of our home page for our contact information. If you are interested in third party information you may visit http://www.toolbase.org and search for precast concrete. The National Precast Concrete Association can also provide you with information on Insulated Precast Concrete Foundations at http://www.NPCA.org. In 2009, a significant amount of language was added to the International Residential Code providing architects, builders, and code officials with guidance on precast concrete foundation systems.
Thanks for replying, Ed. I did look at Superior walls, but that was before the Atlanta franchise (apparently) went out of business.
One of the attractions of the SCIP to me is its local availability. Another was that the shipping involved the lighter weight EPS and truss systems rather than the concrete (which is applied on site). Another was its use of a lighter weight, and stronger (according to the mfgs), application (Shotcrete). Another was that SCIP professed to be substantially more economical than precast.
Am I wrong on these things? Yes, I've read the toolbase materials you mention. I've even contacted mfgrs and they have suggested schemes for the installation and flashing of windows/doors/roof junctions. But I've also understood that the success of the install depends on the skill of the 'nozzleman' for the shotcrete ... and experienced help seems in short supply.
As does third party experience and analysis of both systems in a residential application. So I'm not sure where to go from here. I'd be happy to hear of concrete (ahem) information or resources. If I can get past this hurdle, Ed, I may well take advantage of mfgr resources again.
Thanks in the meanwhile.
Joe W
Check out
http://www.gctm2.com/
Gulf Concrete Technology Insulated Concrete Building System
US made fast answers
More links and information at http://scippanels.com/
Pictured SCIP home ,Highland House, Denver, CO.
Structural Concrete Insulated Panels
There is a fair amount of misinformation about energy efficiency and SCIPs, SIPs, and ICFs
So here are two links for starters http://www.ornl.gov/sci/roofs+walls/research/detailed_papers/thermal/index.html
Although the words SCIPs SIPs and ICFs are not used if you know the products you know what and the difference between them are,
(Walls containing foam core and concrete shells on both sides)
(Concrete wall core and insulation placed on both sides)
(Walls where the insulation material was concentrated on the interior side)
(Comparative analysis of sixteen different material configurations showed that the most effective wall assembly was the wall with thermal mass (concrete) applied in good contact with the interior of the building. Walls where the insulation material was concentrated on the interior side, performed much worse. Wall configurations with the concrete wall core and insulation placed on both sides of the wall performed slightly better, however, their performance was significantly worse than walls containing foam core and concrete shells on both sides)
Most of the misinformation is about the wire trusses going from one side of the panel to the other. They make un substantiated claims so here are some facts
1. ORNL conducted thermal experiments in 1987 that tested concrete sandwich panels:
http://www.ornl.gov/info/reports/1987/3445602788810.pdf
a. This paper states that there is only a 7% reduction in the thermal properties of concrete panels with 32 – 3 mm diameter stainless steel connectors in a 103”x103” wall compared to walls without connectors or with fiberglass-composite ties.
b. The report evaluated the isothermal planes method (also called series-parallel method) of calculating the R factor for the wall assemblies and found that the method predicted a 5% decrease in the thermal properties which is very close to the measured difference.
c. The isothermal planes method for concrete walls is contained in ACI 122R “Guide to Thermal Properties of Concrete and Masonry Systems” which we used to calculate the R-factors for the GCT TER.
d. The walls also had a thermal lag of 5 to 6 hours, which helps to reduce the impact of daily high/low temperatures.
e. The thermal lag indicates the capacity of the wall to store energy and is useful for designing passive solar systems.
Two important points:
1 - Costs. How much does it cost to do a SCIP vs standard construction. If you can't afford to build a SCIP, then the point is moot. You are getting into commercial type of design. Most commercial contractors don't want to get involved in residential as it's not worth their time. Pulling a commercial crew for a residential project will mean you have a write big checks for them. Are you financially ready to do that?
2 - Technical availability. Are there local contractors that know how to do a SCIP home? All the trades will be in a learning curve; plumbers, electrical, HVAC, etc. Most will never have heard of it and if it's not straightforward, they will learn on your dime and on your home will be the guinea pig. Then you have the building department. Your inspector and building department will buy extra red markers to mark up your drawings as they probably never heard of SCIPs, let alone approved and inspected one. Get ready for a battle.
If the above is not an issue, then go for it! No doubt a properly done SCIP home will be much stronger and durable than a stick frame in extreme weather.