Sanity check on load calcs and equipment selection

Hello,
I’m a frequent GBA lurker but first-time poster. I’ve learned a ton from this site and the community, and am now hoping to validate some of those learnings with a request for a quick sanity check before I pull the trigger on ~$20K in new equipment.
TLDR: I’ve picked out some heat pumps based on the load calcs and fuel use analysis that I did myself; I feel good about the numbers but the HVAC contractors all tell me that I’m undersizing. I’m looking either for some unbiased validation that my approach to sizing the equipment is reasonable, or for someone more knowledge than myself to steer me away from the cliff before I make a bad decision. Thanks in advance for your help.
The long version:
We’re in Halifax, Canada (CZ6). Almost two years ago we traded in our modern, efficient new construction home in a high density surburb for an older home on a beautiful lakefront property with much more space for our family of six. We knew that the house would need some work, but it had potential and I think it was the right tradeoff at the end of the day. Given that we plan be here for 25+ years, we made the decision with the intent of renovating the house to better suit our lifestyle and make some upgrades to improve comfort and efficiency. Hence, I’ve spent the past couple of years educating myself on building science in order to make good decisions about how to best invest in those improvements.
Our previous home was built by a reputable semi-custom builder that didn’t cut too many corners. It was reasonably tight (1.85 ACH50) and had an overall EnerGuide ERS rating of 85 (on the old scale). It was heated and cooled by a central ducted heat pump with natural gas backup. It was always very comfortable, and our energy costs were relatively low.
Our current home was built in 1994 with an addition in 2009. It’s well built and the construction details are typical for that era. It’s not as tight as our old house but wasn’t terrible (3.78 ACH50) and it was reasonably well insulated (R22 walls, ~R30 attic). It’s primarily heated by an oil-fired boiler and hydronic baseboard which is great for comfort in the heating season but also quite expensive to operate — 1,900 litres of heating oil per year adds up quickly at >$1.50/L. The boiler also handles DHW. The previous owner added an 18K Goodman ductless heat pump in the main living area (MSH183E15 — I believe it’s a rebadged Midea). We currently don’t have any cooling in the bedrooms which is a comfort issue for a couple months of the year. While the conditioned area of the new house is less than 10% higher than our old house, our first year energy costs were about double. We’re hoping to bring those costs down materially with our upgrades.
Our short-term plan is essentially to make targeted improvements to the envelope in order to reduce our heating and cooling loads, and switch to heat pumps for our primary heat source for most of the house. The boiler will stay operational for DHW and backup heating duty.
Long term, we want to decommission the oil boiler entirely as we fundamentally don’t like the idea of burning fossil fuels in the house and our 2009 vintage oil tank is going to need to be replaced soon for insurance purposes. We’ll either go with a small electric resistance boiler or better, an ATWHP if the cost and support issues are worked out by that time. We also plan to add as much solar PV as we can fit on our roof, but that won’t be for another ~5 years when our roof is due to be replaced.
I’ve gone down the rabbit hole of retrofitting a central ducted heat pump and evaluated both air- and ground-source systems for that purpose. Various factors make it quite difficult to retrofit ducting in our home, and the costs were out of control (multiple quotes between $60-100K CAD). I wanted to do air-to-water, but the costs are also quite high ($50K+ once we factor in new low temp emitters and fan coils) and the support for installation and service is nonexistent in our area. We also couldn’t get any traction with multiple low- or mid-static ducted systems — we refused to put air handlers or ductwork in the attic, and just couldn’t make it practical within the envelope. So, we’ve settled on keeping things simple and just adding three more ductless units to take on a larger proportion of our heating demand and add cooling coverage in key areas.
We had an energy audit conducted shortly after moving in, and the auditor rated the house at 121 GJ/year on the new EnerGuide scale. He assessed design heating load at 52,275 BTU/hr and design cooling load at 25,900 BTU/hr. Our auditor wasn’t great — he had been on the job for less than a year, and his answers to some fairly basic questions were not confidence inspiring. I felt that the design loads stated in the audit were too conservative, and following the audit I independently measured every room, window and door, and drafted a detailed floor plan. I used that information along with the R- and U-values stated in the audit to perform my own room-by-room load calcs via CoolCalc. My results indicated a design heat load of 43,600 BTU/hr and a design cooling load of 18,100 BTU/hr.
I also performed a fuel-based heat loss analysis using Dana’s method, both with the previous owner’s oil usage data and with our own data. With adjustments made to account for DHW usage, this analysis showed that the oil boiler was servicing ~32,000 BTU/hr of heat loss at our design temperature, with the rest of our heat loss being satisfied by the heat pump. Unfortunately this portion has been more difficult to quantify. The Goodman unit is not in the NEEP database and I’ve been unable to find lab-tested capacity or COP ratings elsewhere. I also don’t yet have monitoring on our electric panel so I’m not certain how much electricity it’s using. Anecdotally, the performance of the heat pump is quite suspect — it goes into defrost mode very frequently (sometimes as often as every 10 minutes) even when the outdoor temperature is ~50F. I suspect there may be a refrigerant leak or something else going on. In any case, my intuition is that it’s highly unlikely that this heat pump is offsetting 20,000 BTU/hr in it’s current state, and therefore the results of the fuel use analysis seem to at least broadly validate the idea that our actual heat loss was somewhat lower than the audit concluded.
Since the audit, we’ve performed air sealing work (most significantly, removing an unused wood-burning fireplace) and bumped our attic insulation from ~R30 to R60. We also replaced our 25-year old LifeBreath HRV (55% SRE) with a Fantech HERO 250H-EC (>75% SRE).
I ran the room-by-room load calcs again, this time accounting for the upgraded insulation, reduced infiltration (estimated 3 ACH50) and reduced ventilation losses. The result was a design heating load of ~37,900 BTU/hr and a design cooling load of ~16,500 BTU/hr. I then ran the calcs in a second tool (BetterBuiltNW) using the same source data, the results were pretty dang close: design heating load of ~37,800 BTU/hr and design cooling load of ~15,600 BTU/hr. Overall, this shows a reduction of 13% in heating load and 11% in cooling load. Everything seemed reasonable and I felt confident enough in my approach and these numbers to select some equipment and start soliciting quotes for installation.
We plan to attempt repurposing the Goodman heat pump to service our basement. We’ll have the system checked for leaks and recharge the refrigerant if necessary. We’ll start monitoring the circuit and try to collect some quantitative performance data to assess actual COP. If it works reasonably well, we’ll keep it — if it doesn’t, we’ll replace it down the road.
We’ll also purchase three new units to service our main floor. The units will be installed in our great room (living room / kitchen / dining room), the “owner’s suite” (primary bedroom / ensuite bathroom / wife’s office) and a large bedroom that houses our twin girls.
My goal for equipment selection is to size these units to satisfy our typical loads at as high a COP as possible while modulating as low as possible for efficiency and dehumidification during shoulder seasons. I believe that maximizing our turndown ratio is a critical factor in minimizing costs and optimizing comfort, and I would rather err on the side of under-sizing than over-sizing, particularly since our cooling loads are relatively low and we have a backup heat source. I also decided that we would only do 1:1 units for efficiency and redundancy purposes, and that we would not entertain multi-splits.
I selected the Mitsubishi FS series as they have the lowest minimum modulation available and offer smaller units that will be more suitable for the two bedrooms. Using my room-by-room load calcs, I determined that the most appropriate units would be an FS09 for the great room and an FS06 for each of the bedrooms.
Per my sizing analysis (attached for reference), these units seem to more than cover our main floor design heating load (118% of design load at max capacity) while modulating all the way down to 17%. Our main floor design cooling load is easily satisfied (256% of design load at max capacity) while modulating down to 43%. Combined with the Goodman unit in the basement, the four heat pumps seemingly satisfy our whole home heat load (114% of design load) and greatly exceed our whole home cooling load (271% of design load). Each of the three local Mitsubishi partners were of course nonetheless shocked when I told them I wanted the 6K and 9K units.
One of the partners stated that I would be “majorly disappointed” with my selections and instead quoted an FS12 for the great room and FS09s for the bedrooms. He said he was “certified in heat loss calculations” and offered to review my load calcs. He claimed that I did them incorrectly because I was “assuming a forced air system and ductless is a totally different ballgame”. I told him that my understanding was that heat loss is a function of the building and the environment and not the heat source, and explained that I had not specified anything regarding the heating system (BetterBuiltNW was in “ductless mode”) when performing my load calcs. I asked him to clarify what was done incorrectly, and at that point he backtracked and said that even if the BTU output was sufficient, that the airflow from the FS06 and FS09 wouldn’t be sufficient from a distribution standpoint. When I pointed out that the max CFM of the FS12 was only 11% higher than the FS09 at high fan speed and asked him to confirm that he felt that the difference of 43 CFM would cause us to go from satisfied to “majorly disappointed”, he offered to change the quote but would require us to sign a waiver in order to proceed with the project.
I felt fairly confident in our selections and the partner we are likely to proceed with will install whatever we want without a wavier, so it’s not a blocker. However, this back and forth has planted a small seed of doubt in my mind, and that’s what I’m hoping to resolve with this sanity check.
I think the one factor that has me second guessing the selection for the great room in particular is that there is a lot of glazing and the solar gain in the afternoons is pretty significant. The two tools I used for the load calcs actually vary considerably for this room — BetterBuiltNW shows the cooling load at what I’m guessing is the average throughout the day (3,949 BTU/hr) while CoolCalc seems to better account for the hourly differences and shows the peak cooling load from the late afternoon (6,135 BTU/hr). The FS09 does still seem to meet this peak demand with lots of headroom, but I digress.
Am I making a bad decision by putting in units this small? The cost difference in the equipment is negligible. The FS06 and FS09 are essentially the same hardware and have the same modulation ranges, so we could easily bump both of the FS06 to FS09 — apparently there is a small penalty in COP for doing so. The bigger issue is the FS12 — I’d really like to avoid going to the FS12 because the turndown ratio is substantially worse than the FS06/FS09. If we are unlikely to benefit substantially from the extra capacity or airflow of the FS12, I’d much rather have the improved performance in shoulder seasons that the FS09 would likely provide.
Thanks for taking the time to read the novel I have apparently written — any insights are very much appreciated. I can supply the other supporting data I’ve referenced (the load calc reports, the fuel use analysis, etc.) if it would prove useful for further discussion.
Cheers,
Mark
GBA Detail Library
A collection of one thousand construction details organized by climate and house part
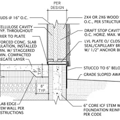
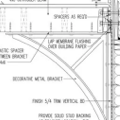
Replies
you did the calcs twice. sounds like the other guy guesssed. I would trust your math. I was told by couple of hvac friends my house would not work with the chosen equipment. I did Manual J and had subbed out the duct design. It worked out even better than expected. My hvac friends were speechless on the topic after that.....they ALWAYS go bigger than necessary.
With a basement it is pretty easy to run ducts, a central heat pump there with a bunch of home run ducts to each bedroom and maybe a wall mount for the main living space would be all you need.
Getting ducts installed seems to be very expensive in case of a retrofit, you might want to shop it around a bit. I've had better luck with getting the ducting install priced by a GC and having the HVAC tech only install the equipment.
Even if you just install a ducted unit in the basement without any connections to the main floor it will do a decent job of heating the living space as long as there is no door between the two spaces. You can than add rooms onto it as you the rads are removed or the place is renovated.
Your calcs seem to be in the ballpark, you definitely won't need larger equipment especially if you are keeping the boiler. Your plan does work but means keeping some of the rads and maybe moving it over to a resistance boiler would work (around me heating oil is more expensive than resistance heat).
I'm not a fan of wall mounts in a bedroom due to noise. Defrost is noticeable on most units, some have a pretty pronounced whoosh when the refrigerant reverses and even the better ones might get some thermal expansion noise from the large temperature change. Something to keep in mind if you are a light sleeper.
elementml- I am asking myself a lot of the same questions during our system design that you wrestled with in 2023. How did it turn out for you? Anything you would be willing to share...did your outdoor units turn out to be right sized? Anything you would have done differently? How did your COP turn out? Thanks in advance!
Here is my post: https://www.greenbuildingadvisor.com/question/advice-for-heat-pump-equipment-selection?discussion=new
Hi amovida123, happy to share my experience thus far, with the caveat that our system isn't yet fully operational and I haven't done any significant data collection, so my evidence is mostly anecdotal at this point.
We installed the heat pumps in August. We mostly stuck to the plan outlined in my original post, but did end up making two last minute changes. First, I backed down a bit and installed an FS09 in zone 2 rather than an FS06. I don't believe this was strictly necessary, but it did provide some added cushion at the top end of capacity without sacrificing the turndown ratio. Second, when our installer pulled down the existing Goodman unit, he confirmed my suspicions of a refrigerant leak and determined that the installation was botched pretty badly including some damage to the head that would make it difficult to reinstall with confidence. He offered to have me purchase a fourth unit from his distributor at his direct cost, and we installed a Mitsubishi FH09 in the basement rather than repurposing the Goodman. So, I ended up with a total of 38,800 BTU/hr of rated heating capacity vs. my modeled design load of 37,769 BTU/hr.
As far as performance goes, it's difficult to draw concrete conclusions just yet given:
(1) We did not use the FS09 in the main living area (zone 1) during the heating season due to an in-progress renovation in that space.
(2) We've not yet installed our MHK2 thermostats or remote sensors.
(3) We've not yet installed our Emporia Vue electricity monitor (and I therefore haven't measured COP).
I do have solid data on fuel usage: adjusted to account for DHW, our oil consumption per HDD decreased by >50% compared to the previous two years (producing a net savings of ~$1,100 CAD). I expect consumption to decrease further next year when the final heat pump is online.
Comfort has been acceptable, though it's not quite as comfortable as our hydronic heat. The main comfort downfall is that the temperature variance is more significant between rooms since the heat distribution from the ductless heads is less even than our hydronic system where we have emitters in every room. While we've opened up our mid 90's floorplan somewhat, it's still fairly compartmentalized with a long narrow hallway dividing the main living areas from the smaller front bedrooms, and we definitely notice the lack of airflow to these rooms. These rooms are also above the unheated garage, so it's a double whammy. We left the hydronic system running in this zone to maintain our 68F setpoint. It's possible that larger ductless heads with slightly stronger fans may have performed marginally better in this regard, but I'm skeptical that it would make a significant difference. Had it been viable for us, a ducted system would certainly have been better from a distribution standpoint. The other comfort disadvantage is that I notice the effects of radiative chill from windows a little more when the hydronic baseboards underneath are not running.
Akos's comments re: noise are absolutely worth consideration. The fan noise is pretty unobtrusive, but the defrost and thermal expansion sounds are indeed louder than I expected. It took us a while to get used to this in our bedroom. It's fine now, but if you're a light sleeper it may be more problematic for you.
One final observation is that our zone 2 unit cycles more often than I would prefer when outdoor temps are moderate -- I was expecting the modulation to be better given that this was one of the primary criteria I considered when selecting the equipment. I suspect the placement of the head may be causing the internal thermostat readings to fluctuate more than our other units (it's the only head that's in close proximity to both the ceiling and a side wall). I'm hopeful that once we install the MHK2 and remote sensor and use those temperature sensors rather than the internal one, modulation will improve.
Overall, I don't have any regrets about the sizing. I'm fairly confident that my load calcs were solid, and my advice would be to stick to your guns and don't let an installer steamroll you with rules of thumb or gut feeling.
I do still intend to completely decommission our oil boiler, and I'm still considering an ATWHP for this purpose. Several new options from more mainstream vendors have come to market in Canada over the past year (Taco System-M, Viessman Vitocal) and I'm somewhat more optimistic about finding an installer willing to take the plunge. My thinking is that the ATWHP would handle our DHW, and tag team heating with the ATAHP units. We have about 93 linear feet of standard fin tube deployed throughout the house, which means we should be able to produce ~15K BTU/hr of output at 110F water temps without installing low temp emitters. While this clearly wouldn't be sufficient to be our primary heating source on design day, it does seem sufficient to handle much of the load during the shoulder seasons, and to provide a base during heating season with the ductless units picking up the slack as outdoor temps fall. In theory I think this combination would address some of the comfort challenges I mentioned since we could leverage the distribution characteristics of the hydronic system to plug the gaps where the ductless heads can't throw enough air, and to offset the effects of radiative chill near the windows. I'll circle back with an update if we make any further progress on this front.
Hope this is at least somewhat helpful, and good luck with your project.