Safely insulating old house with no sheathing

I’m fixing up an old ~1850s home in Upstate NY (borderline zone 5/6). The 1960s and 1970s were not kind to the house, as its original plaster walls were replaced with drywall, and awful replacement windows were installed. The exterior walls were “insulated” with loosely stuffed fiberglass bats, and aluminum siding was placed over good clapboards. No air sealing was done, so the house is quite leaky. The insulation is home to many varieties of insect and small mammal life.
The current walls are constructed as follows:
- Clapboards nailed directly on studs (no sheathing paper)
- 5″ thick studs of various widths (typically 2″-4″), approx 16″ on center
The house has braced-frame construction. The framing is beautiful, very well made with high quality wood. I’d like to insulate it in a way that protects it against rot in case of the inevitable leak, and preserves the framing details for future generations who wish to replace what I’ve done with the next great state-of-the-art insulation system of the future.
We’d like to save the exterior clapboards, as they are in good condition. We’ll be gutting it from the inside. I’m trying to think of an insulation plan that does the following:
- Allows the clapboards to dry as necessary
- Is tolerant of leaks (can dry to outside or inside)
- Does not require removal of exterior clapboards
- Serves as a decent air barrier
I’m thinking of a cut ‘n cobble-based approach, and would like opinions on whether it would meet my stated goals. Basically, I’d seal 2″ thick EPS boards into the stud bays, leaving a 1/2″ gap behind the clapboards to isolate the moisture and facilitate drying. The EPS would serve as an air barrier, and vapor retarder. Next, the remaining 2.5″ will be filled with un-faced fiberglass. Exterior electrical outlets would occupy this space as well, with fiberglass fit/cut around them.
I’ve attached a diagram. Does anybody think this is a reasonable approach? Anything I should be concerned about?
GBA Detail Library
A collection of one thousand construction details organized by climate and house part
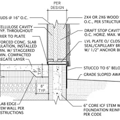
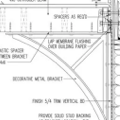
Replies
Aaron,
Your proposal is OK -- but not great. Dense-packed cellulose would be better than fiberglass batts, and your proposed air barrier won't be very airtight or durable (due to changes in the framing lumber dimensions due to seasonal humidity changes). Whatever you do, I recommend that you follow the Airtight Drywall Approach -- that way you will have a much more dependable air barrier.
Another approach: Install the rigid foam, and then fill the stud bays with spray foam.
Thanks,
Do you think the EPS would be able to handle the pressure of the dense pack, and is 2.5" enough space to work with? I'm assuming the walls would need to be netted, blown from the inside, flattened, then drywalled over. The widest distance between studs I've seen is about 20" (though most are 16"). If the EPS can take it, then I can see how dense pack cellulose would be preferable.
So, with the fiberglass replaced with dense pack (and airtight drywall, of course), does the plan graduate from 'OK' to 'Great, all things considered"? Aside from their insulation qualities, it looks like the drywall and dense pack would play the primary role of air barrier, with the EPS providing vapor retarding, physical containment of the cellulose, and enforcement of the ventilation/drainage channel behind the clapboards.
Aaron,
Yes, I think that 2 inches of EPS could withstand the pressure of dense packing.
If you use dense-packed cellulose, your walls will be improved. You won't end up with a high-R wall, but sometimes those of us who live in older houses have to be satisfied with what is possible.
Martin,
Thanks again. I think the proposed solution with EPS and dense pack will be very satisfying, working within the constraints we have and being very protective of the existing house structure.
I modeled the improvements in BeOpt. If we can take it down to 3 ACH50, it looks like the house could possibly consume ~110 MMBTU per year, with a peak 99% load around 62 MBTU/hr. For such a huge house (3500 sq ft, 9-10' ceilings, full walk-out unfinished, unconditioned basement), I'll take it!
Insulating & air sealing the basement is likely to take the total heat load under 50KBTU/hr then, and is usually well worth it, once you have the walls in better shape.
If you air-seal the edges of the EPS well with can-foam or FrothPak, the additional benefit of dense-packing vs. damp spray is miniscule. Dense packing is easily 3x as labor-intensive as damp-spraying, and often more than 2x the cost. The R values are essentially identical, and the adhesives in the damp spray reduce or eliminate settling over time about as well as dense packing (at least in wall assemblies with minimal humidity cycling, which is what you have with 2" of EPS on the exterior.)
Floris,
Your wrote, "Apply Intello Plus on the inside, add battens for services and blow in cellulose. ... Airtight drywall is very tricky and won't seal your floor beams."
Fair enough, I suppose. But I don't think that stapling Intello Plus on the inside of your studs will "seal the floor beams" either. (I think you mean joists, not beams.)
Aaron,
To make installation easier, faster and only have use cellulose as insulation, you can use the following approach (yes it relies on the materials I import with http://www.foursevenfive.com), but allows you to get a very airtight comfortable house without having to live in a foam box and the wall can dry to both sides.
To seal the exterior of your bays, you can use strips of Solitex mento and seal them inbetween studs. Making the outside tight (similar to the detail attached, but with the SOLITEX on the other side of the wall). Then apply INTELLO Plus on the inside, add battens for services and blow in cellulose. If you detail/tape you floors right you should have a very high performance and airtight wall.
Airtight drywall is very tricky and won't seal your floorbeams...the tighter you get the more condition air will stay inside (and doesn't have to get reheated).
you will have to tape the INTELLO detailed around joist or beams...takes some time, but worth it.