Roxul Comfortboard in basement?

I spoke to someone at the Roxul company the other day who recommended the following basement insulation. First, tyvek or similar against the concrete basement wall, then 1 1/4 ” roxul comfort board for a thermal break, then a stud wall filled with roxul batts— sheetrock. Do you see a real problem with water condensing on the concrete with the comfort board and tyvek there? Still seems like too much work but I am curious performance wise.
I read the article about roxul board as a foam alternative under siding. It seems like such a solid long term product compared to foam.
Hopeful for cost effective foam alternatives for basement— no luck yet.
GBA Detail Library
A collection of one thousand construction details organized by climate and house part
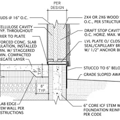
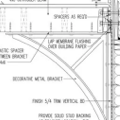
Replies
Nyle,
I strongly advise you not to use this approach.
Your concrete basement wall is in contact with the soil and is usually cool or cold. When humid indoor air contacts this cold concrete, condensation will form.
If you install insulation on the interior side of the concrete, you will ensure that the concrete stays cold.
If you install an air-permeable insulation like Roxul, the humid indoor air will have easy access to the cold concrete (or the cold Tyvek). You don't want that.
Instead, you want a type of insulation that is air-impermeable. I suggest that you install rigid foam board or closed-cell spray polyurethane foam.
Hi Martin, what if you used a smart vapor barrier on the inside, under the drywall? Say MemBrain or the likes? I too am looking for rigid foam alternatives and even now, 2 years from the date of original post, there is not much to choose from. My walls are block, a few rows below and rest is above grade.Climate zone 6. Alternatively, what do we know about fire retardands from rigid foam making it to the indoor air, when covered with drywal/texture/paint?
Igor,
My advice remains unchanged. I don't think that there is any way to install MemBrain in such a way that you will avoid the problem I describe.
I have never heard of any human illness that was caused by flame retardant chemicals in rigid foam when the foam was installed behind gypsum drywall.
Martin, I had a thread going a while back on this same topic. At the time I was persuaded by your advice, the same offered here. I ended up using polyiso for the project, but in the meantime I have had an extended back-and-forth with the technical person at Tremco Barrier Solutions in regard to their Fiberglass Insulation Board. A company pamphlet I picked up at a green building expo endorses this product for basement interior walls.
His argument: "As with most moisture topics relating to the home envelope, a simple condensation model [i.e. any condensation = problems] is not sufficient to characterize what is really happening and whether or not it creates a problem. As discussed above, moisture storage, temperatures, and durations are also key variables."
My question to him was about a hypothetical basement in CZ4, southern Ohio. He went on to say:
He also described mold problems behind XPS on basement walls. Of course he works for a manufacturer, but he's paid to communicate the science behind their product and, presumably, to avoid lawsuits over product failure. Aren't there some definitive studies that can be brought to bear on this? Are there some test walls somewhere?
Andy,
First of all, I'm happy to stipulate that it's sometimes possible to insulate the interior side of a basement wall with fiberglass batts without incurring mold or moisture problems. However, this approach is risky -- so risky that it's not worth using the method.
There are a lot of variables at play. If you're lucky, and your basement is dry and warm, conditions favoring mold development or extensive condensation may never happen. If you are unlucky, however, your wall will be a moldy mess. You are rolling the dice. So I advise builders to use rigid foam in this location.
Q. "Aren't there some definitive studies that can be brought to bear on this? Are there some test walls somewhere?"
A. Tests have been conducted and model homes have been built by Building Science Corporation, and studies have been conducted by Paul Ellringer (see Ellringer, P., May/June 2002, "Minnesota Mold Busting," Home Energy Magazine) and Don Fugler (see Fugler, D., March/April 2002, "Dry Notes from the Underground," Home Energy Magazine).
You may want to read a Building Science Corporation report titled Basement Insulation Systems. Here is a quote from that report:
“The approaches used early in the [Building America] program were interior stud wall framing insulated with fiberglass batts and ‘blanket’ insulation. These two approaches are the most common approaches to basement insulation used by the home building industry in general. The experience by the Building Science Consortium with these two approaches has been bad. The Building Science Consortium has concluded that these two approaches are unsuitable for use by the home building industry due to serious problems associated with mold, decay and odors. This is consistent with reports from Canada where basements are insulated in a similar manner (Fugler, 2002) and from other researchers in the United States, notably in Minnesota (Ellringer, 2002). Continued use of these approaches by the home building industry will likely lead to a disaster of unprecedented proportions and may result in the construction of energy efficient homes being set back a generation.”
Hi Martin, the studies and examples you have above are related to fiberglass , not wool or roxul, do you have any for this type of product? Doesn't fiberglass insulation absorb water and moisture where a product like Roxul or wool does not? I understand if it held the moisture and soaked and sat in the fiberglass it could cause issues. If the Roxul doesn't allow the water to sit, and instead allows it to move back and fourth as long as you aren't using a poly sheet or vapor barrier, what is the harm in that? Do you have any examples or studies tested for wool insulation where its failed? I'm being recommended by a local insulation company to go with concrete/roxul/frame/drywall/primer/paint. the primer and paint act as the regular barrier.
The wicking and moisture adsorbtive characteristics of rock wool and fiberglass are comparable. Neither are anywhere near as moisture buffering as cellulose, but that doesn't mean a whole lot. Unless the temperature of the cold side of the rock wool is above the dew point temperature of the room air it won't be transferring any moisture into the room, and when the concrete is BELOW the dew point of the room air the moisture will in fact move to the cold side of the rock wool.
The solution is a layer of air-impermeable insulation between the rock wool and concrete of sufficient R to keep the average temp at the cold edge of the rock wool above the dew point temp of the conditioned space air both in summer and winter.
For my mechanical room I want to insulate, but there are so many pipes and wires that are practically up against the walls that getting foam behind these sections is impossible, and then on top of that if I want to leave the foam there I need to get specific ones that are allowed to be exposed without drywall. For this area is there any harm in just pinning ROXUL to the walls? I'm not going to have any wood frames or drywall that are near it, and will have my whole basement dehumidifier down there keeping moisture at bay if it needs it, so whats the harm in letting the walls breath but also have some thermal and heat value added. Whats the viewpoint on this?
What about the outside concrete wall? Did you waterproof? Dimple membrane? Insulate below grade with Roxul? IMHO, you should waterproof both sides of your concrete wall and insulate on both sides too. I'd use Roxul on both sides and stay foam free.
Martin, has your opinion changed since 2014? Also, what about using Roxul Right in the foundation walls, framing, closed cell in the stud bays and then drywall? Would that be an acceptable/good solution?
User-7160310,
First of all, can you tell us your name? (I'm Martin.)
Q. "Has your opinion changed since 2014?"
A. The physical characteristics of mineral wool insulation haven't changed significantly since 2014 -- mineral wool is still air-permeable -- so my opinion (and my advice) hasn't changed since then.
Q. "What about using Roxul right in the foundation walls?"
A. I'm not sure what you mean. If you mean putting mineral wool insulation inside the concrete forms, and pouring concrete around the mineral wool insulation to embed the mineral wool inside the concrete, that won't work.
If you want to use mineral wool insulation, either (a) install the mineral wool insulation on the exterior side of the foundation wall, or (b) install the mineral wool insulation on the interior (between studs) after first installing an adequately thick layer of rigid foam insulation or closed-cell spray foam insulation against the interior side of the foundation wall.
My name is Manny. Sorry for the lack of clarity. I have rigid foam insulation (2” thick) on the exterior of the foundation walls. My question was whether the following is an adequate wall assembly (in your opinion): concrete foundation wall, roxul comfortboard, 2x4 framing, 2” of closed cell foam in the stud bays, drywall. I really appreciate your opinion. Thanks.
Manny,
It would be helpful to know your climate zone. But in most warmer zones, installing 2 inches of rigid foam on the exterior of the concrete foundation wall will be adequate -- it will keep the concrete warm enough to allow you to place mineral wool on the interior side of the concrete.
In Zones 6, 7, or 8, however, you'd probably want R-15 rigid foam, at a minimum, on the exterior side of your foundation before considering installing fluffy insulation on the inside of the concrete.
Martin
I have another interesting and related question for you. I have a concrete patio slab, under which is part of the basement. The drawings call for interior insulation glued to the ceiling of the basement. Do you think that installing insulation on top of the floor is a better solution? If so, would the assembly be: slab, drainage/dimple board, insulation, gypcrete, finished floor?
Manny,
If this concrete patio slab is exposed to the weather -- if it gets wind-driven rain or snow -- it needs roofing. Once you install some type of roofing -- perhaps EPDM or a similar type of roofing membrane -- above the concrete slab, you can then install dimple mat above the roofing, followed by some type of patio pavers to provide a walking surface.
If you are willing to install roofing, the system will work. If you also want to install insulation, you would want to install one or more layers of rigid foam between the concrete patio and the roofing; with this type of foam, you might need a coverboard between the rigid foam and the roofing, depending on the roofing manufacturer's requirements.
To recap: from the bottom up:
Concrete slab, rigid foam, coverboard, membrane roofing, dimple mat, patio pavers.
Thanks Martin. I am in climate zone 4 (long island, NY). As far as the concrete slab, it is a covered patio (roof that extends past slab on three sides and entry into the house on the fourth). Also, I did miss one detail; the slab has a layer of sika waterproofing on it already. So, slab, waterproofing membrane (sika), drainage board, insulation gypcrete, pavers? Thanks.
I came across this site while trying to find out if rockwool comfortboard 80 can be used on basement concrete wall instead of a foam type insulation. Martin is definitely against this but when I was at a home depot in Toronto, Canada I picked up information material on this type of insulation which is attached here with my message. I am confused here as why would rockwool promote this if this type of insulation has issues.
Just a short note to confirm Martin's opinion is correct, in my experience. The problem is not the insulation, it's the transport of the water vapor through the vapor permeable (fluffy, i.e. Fiberglas or Roxul or Cellulose) insulation to where it condenses on the cold concrete and runs down the inside of the concrete wall to create all kinds of problems.
I bought a house in Central NJ that had recently had a Rec Room newly finished out in the CMU concrete block basement. White wood studs, R13 fiberglas, sheetrock, and laminate floating flooring. No apparent problem in the unfinished adjoining rooms other than a bit of efflorescence (white mineral salt flash), but when checking the breaker box in a closet in the Rec Room a few years later, I noted wet walls, wet floor, black mold, rotted base plate (NOT treated) studs starting to rot bottom up, and the laminate flooring swollen and ruined.
Diagnosis: either condensation in the now cold concrete wall behind the fluffy insulation, or perhaps water coming from outside which could no longer evaporate fast enough off the face of the now colder CMU block walls given the finished wall built in front of it.
Solution: complete tear out, new stud wall placed with 2" gap inside face of the CMU block concrete wall, and closed cell foam filling behind the studs to seal the surface. Note just to be sure I foam filled the stud bays too, and trenched a full perimeter French drain around the inside of the basement wall to new sump pumps, drilled drainage holes in the bottom row of the CMU blocks, behind new plastic dimple drain on the lower 2 rows of blocks before the foam install. Rationale: I wanted to make certain if it was water getting into the CMU's from outside, then I wanted to give it somewhere to drain to.
But, I'm pretty sure it was condensation. given the appearance of the CMU's where visible in most of the rest of the basement. Forget the permeable insulation - the wall needs to be sealed eg with the closed cell foam as stated. I guess I could have tried the Canadian method of a very well detailed polyethylene vapor barrier on the inside of the stud wall to keep water vapor out of the wall on the inside, but I was not comfortable with the detailing needed around the stairwell and not completely certain the moisture wasn't sourcing from outside.
Of course, I took the opportunity to closed cell spray the rim joists on the whole house while they were there.
This all occurred before I knew about GBA, and Martin's longer article here:
https://www.greenbuildingadvisor.com/article/how-to-insulate-a-basement-wall,
but happy to find out in hindsight the solution I arrived at seems appropo.
Darren
Regarding electric panels, it’s best to not mount them directly to masonry basement walls. I’ve seen the backs rot out many times. What I like to do is get some 3/8” or 1/2” pressure treated plywood, and some 3/4” noncom (the red flywood treated with fire retardant). I make a sandwich with the pressure treated plywood directly against the masonry wall, then then the 3/4” noncom plywood, then the electrical box. I usually mount the plywood assembly to the wall with tapcons, then I mount the electric box to the plywood using wood screws.
The result is that the electrical box doesn’t rot out, and you have a nice clean mounting assembly that looks good. Purists might want to put a capillary break in the assembly, but I’ve never had a problem with one.
Bill
Re-reviving an old thread, Darren, I have become convinced that a French drain like you describe actually becomes a source of moisture that condenses on the masonry surface. I inadvertently created a 10-year test environment by starting and then pausing a basement finishing project. Starting with an interior drainage trench, drill holes, and dimple mat, I put up PolarGuard EPS (taped seams) and wood studs (PT sole plates). I only got halfway around the basement before life happened, and then left the remaining sheets of foam leaning against an unfinished wall. Several years later, I moved the stack and found a thin, but significant film of mold and an almost root-like web of some kind of fungus in a few places. My memory is failing me, but there may have been something organic like osb or cardboard as the first layer against the wall. Over time, I attacked the stains with various weapons like a stiff brush, bleach, Concrobium, Jomax, ammonia... It never came back like I saw that first time, but as stored items accumulated, a "shadow" would form on the walls near anything left sitting next to them for too long. Meanwhile, I studied the exterior grading, downspouts, and porch-to-house seam to see what could be making that wall wet (keeping in mind that the drill holes should allow most infiltrating water to drain away). My inability to solve this mystery is responsible for at least 5 years of putting off the rest of the project.
This year, I got serious about solving the mystery and finishing the basement. I was pretty set on a Tyvek sheet against the wall, tucked into the dimple curb to deal with any moisture that accumulates enough to drip. Without it, the foam sheets would just allow water to drip down and pool against the sole plate.
Over the past year, however, I noticed that the shadow only extended 12-24' above the dimple curb whenever it re-formed. That's when it hit me: the killer is inside the wall! Or, really, under it. The wall area in question is near the corner where the sump pump is. The pump runs fairly often during rainy weather and there is always a few inches of water in the sump. The drain trench in that part of the basement is probably damp nearly all of the time. It is very likely a reservoir for moisture to drift up and condense on the cold wall. Anything blocking air circulation kept the wall from fully drying out. Of course, humid air from inside the basement could also cause mold in areas with poor airflow, but I saw some more corroborating evidence today when I moved a metal cabinet for the first time. Sure enough, there was about 16" of "shadow" rising from the drain curb behind it, shaped a bit like a triangle. I think the triangle represents the places where air flow was lowest and proximity to the moist trench was closest. Why else would the higher parts of the newly revealed wall surface be growth free? Maybe because of stratification, but that's a bit of a stretch. Despite sitting there for more than twice as long as the foam stack, there was not a gnarly petri dish of growth. This is why I think there was cellulose in that stack, whereas this mold only had dust to snack on.
To further test my theory, I cut out a panel of previously-installed foam between two studs that are ~12' away from the exposed walls. I was relieved that it was not a moldy mess after 10+ years. There WAS some black spotting right around the drain curb but far, far from the rot I had seen when I pulled down the old pine paneling years ago. That old wall looked more like your electrical closet sounds. This new assembly has deprived the mold of a food source.
So now I'm actually considering running a bead of caulk along the top of the drain curb to keep the wet parts wet and the dry parts dry. I had previously liked the concept of giving the rare bulk infiltration a path to the drain, but I think that probability seems very low while the probability of drain moisture drifting up seems very high. It's gotta be close to 100% RH down there after a good rain.
If Martin or Dana make it this far, I'd love to hear your thoughts about sealing the gap at the top of the French drain dimple curb. In fact, should such curbs terminate below the slab surface to prevent the issue in the first place? My understanding is that their real value is keeping the drill holes clear under the slab so the walls can freely drain into the trench and tiles. The exposed part is meant for tucking in a sheet of poly, and as Martin tells us, just say "no" to that advice.
Am I off base here, or should I caulk away?
Mark, not sure of your exact situation, but if you put a french drain in an existing basement (by cutting the slab and then "trenching" and back-filling with gravel), you really need to re-concrete over the trench to cut off the source of moisture. The moisure is coming down the exterior of the wall, sure, but is also coming UP under the slab as the water table rises.
In my case I left the trench open (just filled with gravel) for a few years. I saw a marked reduction in humidity after I took out 4" of gravel and re-concreted the trench.
Bill
Hi Bill, thanks for your thoughts. You are correct that it's an interior French drain, and it is finished with hydraulic cement over the gravel; however, there is a plastic mat against the wall, half buried in the trench and half exposed above it. If you squint, it looks like baseboard. With it in place, the slab is 100% disconnected from the walls. The idea is that water can still penetrate the wall, but it will mostly drop through the cavities in the block until it drains out of the drill holes where it hits this plastic mat and drops into the drain tiles.
Installers very often ( or always?) extend the mat up the wall by a few inches, and mine told me I could tuck a vapor barrier into it before framing out the walls. As I learned more about building science, I determined that was a bad idea, but I thought Tyvek might be okay if it caught the condensation while still allowing the assembly to dry out. Now, I'm convinced that the drain mat should be fully enclosed below the surface or, if it must come up the wall, the gap at the top should be sealed.
It's great to hear about your experience correlating an open trench with higher humidity levels. If my trench is only mostly filled, and still able to breath through this thin gap, then I might be right about it being a source of moisture for the mold on the lower portion of the walls. Sealing it would make it harder for the trench to fully dry out, but I think I'm ok with that. It will re-wet with every decent rain anyway. Not to mention, it's a pathway for radon to bypass the slab.