Rotten spray foam wall assembly fix

We are currently working on a project in Vermont (climate zone 6) for a customer where the original scope was to pull off the old vertical shiplap pine siding and replace with R-Zip (R6), rainscreen, and vertical LP siding. When we pulled off the siding we found significant rotting on most of the horizontal wooden members. We found it on the bottom sill plate, the rim joist for the second floor, and on headers as well. Here is the existing wall assembly:
– painted sheetrock
– 2×3 horizontal furring strips to run wire and hang sheetrock
– 2×6 wall framing
– both the 2×6 and 2×3 are filled with low density spray foam that was sliced with a saw flush with the interior surface of the 2×3’s. (this foam has numerous voids from mice over the years)
– there is no sheathing on the structure, a metal L-shaped bracing is let into the studs.
– There is a product called “Thermo ply” that is hung on the outside of the studs. It is nailed on with the seams taped. This is the WRB. It is basically a coated cardboard material.
– The vertical pine shiplap siding is furred off the WRB using two sets of 3/4″ strapping. The first is nailed vertically to the studs, and the second (that the siding is nailed to) is nailed horizontally to accept the vertical siding.
– One major thing to note is that the overhangs on this property are minimum. There is about 8″ on the eves, and nothing at the gables.
– They have a HRV system and suspect there is negative pressure in the house, which could be a driver for moisture.
I want to figure out exactly what is causing this problem, fix the structural issues, and put up a system that will not continue to cause problems in the future.
My current hypothesis for the problem relates to vapor transport from the inside of the house. It could also be water coming from the outside, but we do see rot higher up in the building which makes me think that rain coming in is definitely not the only cause. Also, the WRB should have prevented most of this rot. I am thinking that water vapor is coming into the wall system and condensing on the back side of the WRB in the cold months. This water is rolling down the back side of the WRB and the horizontal surfaces are catching it and wicking it into the framing. I will attach a couple pictures for reference.
My concern with putting on the R-Zip like we had initially planned is that vapor could now just condense on the back side of the OSB Zip panel. Given the issues that we are seeing, would it be better to put plywood directly on the framing, and then put insulation on the outside to keep the plywood warm and prevent condensation? How much foam would we need for that in climate zone 6 (Vermont)? I know in some cold climates there is a 2/3, 1/3 rule of thumb to basically ensure that the dew point is outside of your assembly. I’m not sure what the rule of thumb is for Vermont… Would it be a better idea to not sheath/insulate at all and put Tyvec with a rainscreen on so that we could stop any water from coming into the assembly from the outside, and still allow the assembly to dry to the outside?
Any advice on this problem would be appreciated. Thanks!
GBA Detail Library
A collection of one thousand construction details organized by climate and house part
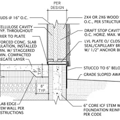
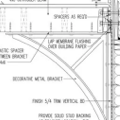
Replies
They did a lot of things right with that build but one major thing wrong.
If I remember correctly, Thermoply is very low perm. Essentially the wall has a cold side vapor barrier which why you see condensation and rot up high.
There are a couple of options to fix it.
You are on the right track with exterior rigid but you'll need more. In zone 6 you want 35% of your wall value as exterior rigid:
https://buildingscience.com/documents/building-science-insights-newsletters/bsi-100-hybrid-assemblies
The issue is you are starting with a high R value wall (~R30) so you need R16. That is a lot of rigid. Since the walls are well sealed with the spray foam, probably Zip R12 would work.
Another option is to strip the thermoply and re-sheath with something permeable (CDX/OSB/Gypsum) and paint the interior drywall with vapor barrier paint. If you go with something highly permeable such as exterior gypsum sheathing and vented cladding, you can probably skip the interior vapor barrier paint. There are now coated gypsum sheathing options that work the same as ZIP.
You can also skip any sheathing and go with housewrap only but you'll have more issues with mice.
Since the existing wall is already pretty high R value, I would vote for the gypsum option. Since you mention mice, I would do a bit of extra critter proofing such as hardware cloth on the bottom edge and building corners. Also a good idea to embed a stainless steel wool around door rough openings and any windows close to grade into the spray foam.
Thanks for the thoughtful insights Akos! I think we are narrowing in on a decision to use CDX to reinforce the structural damage. The thickness of the CDX will depend on the amount of structural damage that we see as we investigate further. It seems that CDX has relatively high permeability as the moisture content goes up. The CDX will also help with the mouse problem. At this point we are thinking of using a 5/8" thickness. On top of the CDX will be Tyvec as it maintains breathability outwards. We will either use the crinkly Tyvec or Cor-A-Vent rainscreen strips before putting on the vertical siding. Ahead of putting on the CDX we will attempt to fill all of the voids in the low density spray foam using off-the-shelf spray foam kits. The homeowner would like to take the extra step of pressurizing (or depressurizing) the house to see where air leaks are coming from and seal them all. Am I correct that open cell spray foam is air tight, but vapor permeable? I'm not sure how well the idea to pressurize the house and look for leaks will go. We would use a smoke pen or something similar....Do you have thoughts on this?
On another note, I had a question about your comment regarding the R12 Zip. Isn't the concept of the 35% rule that you would need 35% of the total insulation R-Value on the outside of the plywood (to keep the plywood warm)? With the Zip system your plywood is still on the outside of all of the insulation.... Some insight into this would be awesome as well.
Thanks again!
re: plywood & zipR - I think the suggestion is that since you have "metal L-shaped bracing" you can skip the plywood as sheathing & go with the zipR system.
then the first condensing/low-perm surface of the Thermoply (identified as the problem) is replaced by the urethane foam surface in the zipR that never gets below the dew point because 35% of the r-value is to the outside of that first condensing surface.
My 2 cents (former open/closed spray & inject foam contractor in VT)
Just to make sure, the plan is to strip the thermoply and replace with CDX? The thermoply has to go unless you add exterior rigid.
8" of open cell spray foam is about 6 perm. Painted drywall is about 10 perm, so your existing overall assembly permeability is 1/(1/6+1/10)= 4.
General rule of thumb in cold climate you want the sheathing permeability to be 10x the wall but even less tends to work as long as exterior permeability is higher than interior.
CDX permeability is about 3-4, close but not guaranteed to work. Gypsum sheathing is 30, so it will work for sure. My recommendation is to add CDX where needed to reinforce and sheath the rest of the wall densglass/denselement.
Since you are relying the sheathing to dry to the exterior, you also want a real rain screen. Crinkly Tyvek is not enough. Corovent or standard vertical rain screen strapping as per fig 10.d here is needed:
https://lpcorp.com/media/1951/lp-smartside-foundations-panel-siding-installation-instructions-english.pdf
Although not necessarily needed for air sealing, I would still tape all the seams of the new sheathing as critter proofing. Zip tape or 3m8067 both stick quite well to both CDX and Densglass.
P.S. How old is the build, curious as how long it took for the wall to fail?
Hi Akos,
Thanks again for your response. I think we have landed on a wall assembly now. It is a vented one that should allow drying. Here's the plan:
Pull off the Thermoply!
Install a 2x4 exo-skeleton by laying the 2x4's flat against the existing 2x6's and fastening into the existing wall with screws to get past any rot in the areas where it exists. We will add headers where needed in this layer as well. It is meant to add back the strength to the wall that was lost through the rot. It will be an exact overlay of the existing framing.
We will then go through and seal any gaps in the existing loose density spray foam with one of those spray foam kits.
After that we add a layer of 1/2" CDX to the top of the exo-skeleton. At this point, I'm not sure it matters what we put on top of the exo-skeleton because it is actually vented. The exo-skeleton will necessarily have gaps between the studs and holes in the bottom to allow air to enter, and will be vented directly to the attic (which is vented as well).
On top of the CDX we will put Tyvec crinkle wrap because we do not have the luxury of adding any more thickness to our wall structure, due to limitations of tucking this all under the existing roof. The Tyvec will flash with the windows and doors.
Lastly, we will add our layer of LP vertical siding on top of the Tyvec.
I'm feeling pretty confident that this vented system will allow the wall system to dry if vapor ever does get in there again. (and yes, we will install hardware cloth as well to prevent the mice from getting in and messing up everything we have constructed...)
Please let me know your thoughts on this system.
To answer your question on age, the home is only 17 years old. Kind of amazing that we already see the level of rot that we do.
From moisture perspective, what you propose should work. I would add another layer of housewrap over the walls as a secondary air barrier or move the CDX inboard of the 2x4 ie:
-existing 2x6
-housewrap with taped seams
-2x4
-CDX
-housewrap
-cladding
Most codes don't allow wall venting into the attic. Typically walls with the top vent closed off work well enough though.
Critter proofing is possible with the large vent cavity but you have to be very diligent about covering every possible entry point.
As for the structural fix, you might want to run this by an engineer as it won't work under prescriptive compliance. You'll also need to rest the bottom of the new studs onto something structural.
Might be simpler to sister the studs that actually need sistering (ie sheer walls), in most cases you only need an equivalent of a 2x4 for the loads, so missing a bit of the 2x6 is not an issue and replacing the rotten headers. Not fun but easier with open cell foam then with closed cell.
I just wanted to reach out and say thanks for all of the responses from both Akos and begreener. It has been very helpful for this project.