Roof/Wall Connection on a Pretty Good house, Zone 5A, Cold 6000HDD

Hello everybody. I’ve been perusing GBA for a while trying to come up with a wall for this 2 story, ~2000SF house that makes sense, is not too expensive, and is durable. I’m trying to avoid using foam unless absolutely necessary. In the attached drawing you will see my working idea for my roof and wall at the downward slope of what will be a shed roof (1 1/2″ / 12″ slope).
The basic build up of the wall is
- Painted GWB or Finish plywood (at some locations)
- 2×6 framed walls with dense pack cellulose
- zip sheathing, taped at exterior serving as air barrier and WRB
- 2 layers of 3″ Roxul Comfortboard 80 (6″ total)
- 1x strapping
- standing seam metal or wood siding, depending on wall
The roof is the same, except replace 2×6 framing with 14″ LPI18 (like a TJI)
I have indicated on the drawing what I think is the air barrier (taped zip sheathing).
This assembly gives a total of ~R43 at walls and ~R73 at roof. I am in the Hudson Valley (Cold 5A, ~6000 HDD).
My concerns are the following.
1. Am I doing something horribly wrong? Do I need some kind of venting?
2. Do I have a danger of cold sheathing?
3. Am I overinsulating? Underinsulating?
4. Is it wrong to use Zip+tape as my WRB/Air Barrier? Are there better solutions?
I think I saw someone who installed Zip w/ membrane on the inside chord of his roof craming… maybe using wood fiberboard as exterior sheathing at roof. That is an idea I’ve considered, to avoid condensation on outboard roof sheathing, but I’m trying to minimize different systems/labor costs…
Some of my thoughts… Though I think I could save some $ by going to 5″ Rock wool, I think having 2″ and 3″ boards on site will be confusing and not worth the hassle, so might as well go with the full 6″. I feel like 4″ of rock wool is cutting it too close in terns of cold sheathing. Perhaps I should eliminate zip and add WRB/Air barrier as a wrap outside of the rockwool?
GBA Detail Library
A collection of one thousand construction details organized by climate and house part
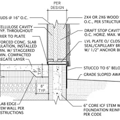
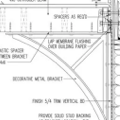
Replies
In zone 5 on an unvented roof you need at least 40% of the total R on the exterior of the roof deck. With R24 rigid rock wool in an R73 stackup (R49 in the TJI rafters) that's only 33%. That's insufficient dew point control on the roof.
With another 3" of rock wool up top (9" total) that would bring it to R36 up top, R85 total, and a ratio of 42% above the roof deck, which would work fine.
The alternative would be to back off to 9" TJI rafters (or 2x10s instead of TJIs) for R36 (or less) under the roof deck, which would be fine with R24 rock wool up top, and it would still outperform code-min by quite a bit.
Dana, Thank you for your reply. In my post, I alluded to the fact that I might suffer from the problem you expose. However, I am sad to reduce my insulation so significantly (from 73 to about 55) to solve the cold sheathing problem. What about the other ideas I suggest... Moving sheathing to the inner chord of the truss and using a fiberboard sheathing at the top chord? Or maybe this is a place where I should not be using OSB, and should look at densglas or some other material for my roof sheathing? Basically, I guess my question is could I look for a vapor open solution at the roof sheathing and/or move the wrb/air barrier towards the interior in order to avoid the problem you are addressing?
One more point... There are a variety of reasons why reducing the size of my roof framing members is not advantageous, so finding another solution to this problem is worth my while.
Deleted duplicate post...
I thought that the percentage rules didn't apply to rock wool, because it is so vapor permeable. Am I mistaken about that? (Don't worry, I haven't built anything based on that.)
Reid, thank you. I had thought that might be the case, but I'm not sure. I'm also wondering if I replace ZIP with taped plywood and a vapor permiable housewrap if I can keep my insulation levels as drawn.
On the walls, you are fine. No need to worry about the ratio of interior and exterior, as long as your WRB is vapor permeable. Your sheathing will be warmer than in a double-stud wall and any ratio will only make it better beyond what one gets with a double stud wall which is already OK if not ideal. And the concept of having the mineral wool outboard of the WRB is well established to work fine.
Where I think some more discussion is needed is the roof. I'm no expert, but here's what I'd want to think about: The ability of water that gets into the mineral wool layer to drain might not be as good as it is on a vertical wall. I would think that you'd want a roofing underlayment material above the mineral wool on the roof. Then you either need venting under that underlayment (between it and the mineral wool boards) or you need the underlayment to be sufficiently vapor permeable that you have no worries about condensation on the bottom of it.
I'm not sure how other people have handled that--I saw one reference to using another layer of plywood on top of mineral wool above a roof, but I didn't see details on what underlayment or venting was used where.
If you come up with a configuration that allows vapor out from the top of the roof mineral wool boards, and your decking below the mineral wool is vapor permeable, you needn't worry about ratios on the roof. If you do have sufficient exterior insulation according to that rule, you could then use a vapor barrier on the decking, and then you'd have very little moisture in the exterior mineral wool and although you'd still want a way for it to dry, you wouldn't need much venting or much permeability.
One other note about your configuration: Some people like to avoid connecting the rainscreen vent path to the roof vent path so that solar heating of the siding won't heat the roof and cause ice dams.
Drying an OSB or plywood structural roof deck toward the exterior with a vent channel above the rock wool only sort-of works, and it would be wise to run a WUFI on it if going that route. The vapor retardency of plywood & OSB goes up as it's moisture content increases, but it's nowhere near as vapor permeable as fiberboard, and even that might not cut it on a roof (though it wood on a wall in zone 5). The moisture coming from the interior has to leave by making it through the low permeance sheathing, whereas with a vented roof deck the moisture hits the dry air in the vented space before it reaches the cold roof.
SFAIK there is no fiberboard sheathing that would meet the structural capacity requirements of a roof with 24" o.c. rafters or even 16" o.c.,, so it's probably off the table anyway. You'd have to hire an engineer to design the structural aspects, which may require a tighter spacing on the TJIs, and most certainly would require a tighter fastener spacing.
An R50 stackup where R24 of it is continuous beats code minimum performance by quite a bit (due to the R23 thermal break). The heat load difference between that and and the riskier R73 stackup is pretty tiny- even PassiveHouse energy use levels don't demand R73 in an unvented roof, even though many PassiveHouses with vented attics pile on that much or more on the attic floor. Very high R on the attic floor is cheap- cheaper than gaining that very marginal improvement elsewhere in the building. An unvented R73 (or even R50-ish as described in my previous post) is by contrast quite a bit more expensive than R100 on the attic floor.
Ethan,
If you decide to stay with this assembly, you may want to place a layer of Intello smart vapor retarder between the TJI's and gypsum on your attic ceiling. That will help to eliminate condensation caused by water vapor from the inside of the house.
Like you I wanted to avoid foam as much as possible and have a tight exterior air barrier with the wall and roof sheathing taped together without rafter tails. I settled on Roxul on the walls and a polyiso (low GWP) nail base product on the roof. For the gabled roof sections, I am using a top vent nail base and for the flat roof sections an unvented nail base. I know you said you wanted to stick with the TJI's, but would this assembly work for you?
Ethan,
The concerns expressed by Dana Dorsett and Charlie Sullivan are valid. For more information on keeping your roof sheathing above the dew point in winter, see this article: Combining Exterior Rigid Foam With Fluffy Insulation.
Basically, you know that your roof sheathing will be damp, so you can either (a) follow the usual rules instead of designing an assembly with damp sheathing, or (b) come up with work-arounds to lower the moisture content of your sheathing or to help the sheathing dry quickly after it gets wet. This work-around include an interior smart vapor retarder, increasing the depth of your exterior ventilation channel, switching to a vapor-open sheathing like fiberboard (don't do this without talking to an engineer), or taking the European approach of omitting the sheathing and installing a vapor-open membrane where the roof sheathing usually is (ditto on the need to consult an engineer).
I'm in favor of either (a) the traditional North American approach (include a generously sized vent channel between the top of the insulation and the underside of the roof sheathing) or (b) installing enough continuous insulation on the exterior side of your roof sheathing to keep your assembly out of trouble.
-- Martin Holladay
Thank you everybody for your responses... Before I move on, perhaps it wasn't clear in my detail that I intended that the 1/2" air gap created by 1x strapping was intended to continue along the roof as well as the wall. Martin, would you consider this a "generously sized vent channel" or are you suggesting an even deeper air channel at the roof (more generous than 1x strapping).
Ethan,
No, a 1/2-inch air gap isn't considered to be "generously sized" for a ventilation channel in a roof assembly. The code-minimum depth is 1 inch, and many building science experts (including Joe Lstiburek) advise a minimum depth of 2 inches for this ventilation channel.
For more information on this topic, see All About Attic Venting.
Dana's point is a good one: while a ventilation channel on the exterior side of the OSB sheathing will work to reduce the moisture content of damp OSB, it will be less effective at keeping the OSB dry than a ventilation channel on the interior side of the OSB. The reason: the moisture comes from inside the house.
-- Martin Holladay
Charlie, is ice damming an issue on standing seam metal roofs?
Thank you everybody! I am going to look into the cost and energy implications of both of Dana's suggestions in response 1 and 9. I am also thinking of switching from ZIP to a plywood+housewrap (or something crazy like Magnesium Oxide Board ;) so as to avoid creating an oatmeal sandwhich for my heirs.
Do you recommend using a different tool than BEopt? I wish BEopt had rockwool option for insulation sheathing as a default.
Ethan,
Q. "Is ice damming an issue on standing seam metal roofs?"
A. Standing-seam metal roofs can get ice dams, but this type of roof (when faced with an ice dam) is less likely to leak than an asphalt shingle roof.
No matter what type of roofing you choose, it's a good idea to pay attention to air sealing and to include thick insulation that meets or exceeds minimum code requirements. These two steps are usually enough to eliminate ice dams. In snowy climates, it is also best to also include a ventilation channel under the roof sheathing.
-- Martin Holladay
I have created an approximate building using BEopt, and created representative values for window orientations, wall assemblies, etc. I then created 3 roof types to approximate those which have been discussed in this post (using Polyiso continuous exterior insulation to emulate the rock wool because rock wool is not an option for continuous exterior insulation in BEopt).
I am by no means an expert at using BEopt, so there is a good chance that I have done something wrong, but as others have noted, energy modeling can be useful, even for newbies, if you are using it to see comparative values.
In all of these simulations, I am using an R40 subslab and R43 wall as shown in the detail above. Then I ran the simulation with 3 roof assemblies:
2x10 joists w/6" Rockwool exterior
14" TJI w/6" Rockwool exterior, and
14" TJI w/9" Rockwool exterior
as drawn above. In all three simulations, Source Energy Use (MMBtu/yr) was about 100, with the difference (seen in the red swatches of the attached graph) being only 0.7 MMBtu/yr between the 2x10 Joists+6" Rockwool and the 14" TJI amd 9" Rockwool... So maybe the choice is obvious! I have confirmed that my inputs are reasonable, and the output from BEopt seems to bolster Dana's points above. I think the 2x10 wall performance will be similar to the 9 1/2" TJI/LPI performance with comparable insulation types and orientations.
I am going to rerun the simulation using the 2x10 roof framing and varying the subslab insulation from R-5 to R-40.
One thing I am not sure about is what is that large, grey "Misc" category in the BEopt output of energy use. It is hopefully immaterial to this conversation because it is the same in each model, but I am curious how the largest use of energy can be categorized as "Misc."
Having run a similar simulation using only the 2x10 framing and 6" exterior Roxul to see what the variation on heating energy would be using R10, R20, R30, and R40 subslab showed a variation from 16 MMBtu/yr for R10 subslab to 13.7 MMBtu/yr for R40 subslab.
Two layers of 2" Roxul would be R16 which would put us in the middle of this range, and perhaps adequate. Next up I'm going to look at a total of 5" Roxul vs a total of 6" Roxul on exterior walls.
You can see here for some support of the idea that less than condensing ratios of exterior insulation can work well if there is a) an interior side air/vapor layer and b) some permeability to the exterior.
It gets even better with more exterior insulation, more permeability, better interior side air sealing or cellulose fill (less interior to interior circulation).
One more energy model output comparing R-20 (5in) continuous exterior insulation (Roxul) and R-24 continuous Roxul (6in). Both of these are using R-16 (4in) Roxul subslab. For good measure, I've added in a 5kW PV system to see where I'm getting to in terms of a Net-Zero assembly. I think I am homing in on an envelope with R57 Roof, R43 wall , and R16 subslab. Looks like with a 10kW PV system I could approach Net Zero, depending upon shading.