Roof: pressure-equalized rainscreen vs. vented roof assembly

Planning a budget PERSIST build similar to the attached BSI 096 drawing, but would like at least 18″ overhang to help protect siding from our avg 62″ annual rainfall. Average winter lows of 35F in Winter, with 8F record low and little snow. Avg Jul/Aug highs of 90F and low Summer humidity. Property is forest land in CA, so fire protective details important.
Adding 2x4s on their sides as furring strips over the external roofing insulation and under the roof top sheathing to provide a top frame member for separately built ladder type overhangs seems to be a good way to support the 18″ overhangs. It would also provide a rainscreen and allow the top polyiso (using polyiso instead of stone wool insulation) to provide radiant insulation as it would be directly exposed to the 1.5″ airgap. Standing seam metal roof, over roofing felt over taped plywood sheathing above the rainscreen gap in case that makes a difference. Thinking vapor permeable crest vents similar to BSI 096 detail on top, with more conventional under eave vents to allow draining of any water that enters the roof rainscreen.
Problem is that the very limited build area on the lot requires an L shaped floorplan, making standard full bottom to top venting of the underroof vent channels impossible. Because these channels would primarily function as a pressure equalized rainscreen vs a full roof ventilation system, can I connect the air gaps at the bottom of the valleys by shortening the furring strips similar to how rainscreen channels are connected under windows?
GBA Detail Library
A collection of one thousand construction details organized by climate and house part
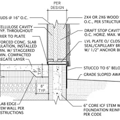
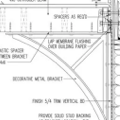
Replies
Mitchell,
If you are adding fluffy insulation between your studs and rafters, it isn't a PERSIST house -- it's just a house with some exterior rigid foam, along the lines of the homes discussed in this article: "Combining Exterior Rigid Foam With Fluffy Insulation."
The short answer to your question: In your climate zone, where you have no worries about ice dams, your suggestion for connecting the vent space above the foam at the roof valleys will work -- assuming, of course, that your rigid foam is thick enough. (The link above includes advice on minimum rigid foam thickness.)
That said, I have no idea whether your local code inspector will allow this approach in a region with a high risk of wildfires.
Hi Mitchell -
Pressure-equalized rainscreens depend on the 3-D geometry of the vent spaces to keep out water being driven into the vent spaces and are primarily used in tall commercial buildings, where the wind pressure is great. It's not really used much in lower residential buildings. And it's as much about the pressure resisting wind-driven rain as it is free-drainage.
I have never heard of the pressure-equalization approach being used on roof assemblies, probably because most high-rise commercial buildings don't involve pitched vented roof assemblies.
Peter
Can anyone give a possible reason why the drawing shows plywood on the interior rather than drywall? How common is it to install plywood on the interior?
Aaron,
You often see plywood used as an interior finish in high-end contemporary architecture. It is incredibly labour intensive, relying on perfect framing, and a lot of scribing of sheets.
Martin,
Thanks for the short portion of the answer - the rigid foam is more than thick enough thanks to your previous blogs on external insulation. Really appreciate the expertise and availability to help us build pretty good houses, and yes all the great advice in your book.
Since PERSIST stands for Pressure-Equalized Rain-Screen Insulated Structure Technique, I'm hoping you can help explain how this construct doesn't fit that acronym. The proposed build has a rain screen with enough exposed air gap top and bottom to help equalize the pressure on both sides of the of the outermost layer, thereby reducing pressure factors which could contribute to driving moisture through that layer. The structure is also insulated by the external foam layers. Though it doesn't follow the original PERSIST design exactly, it does have the same attributes that are referenced by the acronym, and it appears to capture many of PERSIST's benefits (including continuous, easily identifiable water, air, vapor and thermal layers), while substantially reducing costs.
I know many builders are still resistant to external insulation, but external insulation has become a little more common as we drive towards net zero requirements in CA because it helps so much with air sealing and thermal bridging. Costs are a little more with this proposed build method (see more details in attached), but the resiliency and efficiency gains appear worth it for my build and probably many others. Am I missing something besides maybe using the wrong terminology ?
Mitchell,
Here at GBA, we've been promoting the use of continuous exterior insulation for years. It's an excellent way to build. See, for example, these three articles:
"How to Install Rigid Foam Sheathing"
"How to Install Rigid Foam On Top of Roof Sheathing"
"Installing Mineral Wool Insulation Over Exterior Wall Sheathing"
The PERSIST technique was invented and named in the 1960s. Here is a GBA article on the PERSIST method: "Getting Insulation Out of Your Walls and Ceilings."
The PERSIST approach differs from your approach, because PERSIST buildings have no insulation between the studs or rafters. All of the insulation (usually rigid foam) is installed on the exterior side of the sheathing.
After the PERSIST method was developed and named, the researchers who included the phrase "pressure-equalized rainscreen" in the acronym were criticized for misunderstanding pressure dynamics in rainscreen cavities, and were informed that these cavities were not, in fact, pressure-equalized. In spite of the naming controversy, the technique (dare I say) persists, and the acronym "PERSIST" persists as well.
Thanks for the explanation that the PERSIST originators were off in their initial naming convention. Lots of great articles on exterior insulation in GBA, and have pretty much read them all.
One of the big distinctions between "just a house with some exterior foam" and PERSIST is that sealed sheathing joint between the roof and wall which creates many advantages for continuity of the 4 barriers - making it better model a perfect wall and roof. A product like Huber ZIP makes it much cheaper and easier to accomplish than PERSIST's peel and stick rubberized membrane. Seems to be a 'pretty good' way to build, especially when combined with a rainscreen like PERSIST's. Surprised that GBA hasn't come up with a name to describe this hybrid building method.
Mitchell,
Sealing the seam between the wall sheathing and the roof sheathing is part of the PERSIST method, as well as the chainsaw retrofit method. (Enter "chainsaw retrofit" in the GBA search box for more info.) Both of these excellent methods are decades old -- PERSIST dates from the 1960s, and the first chainsaw retrofit happened in 1982. (See "The History of the Chainsaw Retrofit.")
So, you're preaching to the choir -- builders focusing on energy efficiency have been promoting these techniques for a very long time.
If you like new names, consider the REMOTE approach. (For more information on REMOTE, see "REMOTE: A Manual.")
I'm not in favor of coining new names. The words "continuous exterior insulation" are useful, and not too hard to say. Many people also note, "My primary air barrier is at the sheathing, and after sealing the sheathing I built applied overhangs."