Roof buildup – Zone 4B

Curious as to this Shed Roof Build-up:
EPDM Roofing
2″ Thermax Rigid Insulation Board (R-13)
Roof Underlayment
5/8″ CDX Sheathing
2×12 DF#1 Rafters @ 24″ o.c.
Layered Roxul Batt Insulation (R-46)
Any issues or potential problems?
GBA Detail Library
A collection of one thousand construction details organized by climate and house part
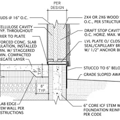
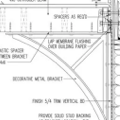
Replies
Peter,
Nope -- that won't work. You are planning a roof assembly with 22% of the R-value coming from the rigid foam layer, and the rest of the R-value coming from fibrous insulation.
You don't have enough rigid foam. In your climate zone (Zone 4B), with this type of roof assembly, at least 31% of the roof assembly's R-value has to come from the rigid foam layer.
What you need is R-20 or R-21 of rigid foam. If you pair that with R-46 of fluffy insulation, you'll be safe.
For more information on this topic, see Combining Exterior Rigid Foam With Fluffy Insulation.
If you wanted to cheat that you could do OK with air tight 2-mil nylon as an interior side vapor retarder, but it would be better/safer to go with more exterior R.
Martin & Dana,
THANK YOU for the information.
I couldn't open that article because I am not a prime member. What are the dangers out not putting enough rigid insulation on the outside? How does that roof stack-up dry since it cannot dry to the exterior?
Peter,
For the principles behind this type of assembly (one with exterior foam), see this article: Calculating the Minimum Thickness of Rigid Foam Sheathing. (That article is free for non-subscribers. While the article mostly discusses walls, the principles apply to roofs as well. By the way, if you find the information on GBA useful, you might consider purchasing a one-month subscription as a trial. If you have a building project pending, the information you learn by subscribing will probably save you more than $15, the cost to subscribe.)
Q. "What are the dangers of not putting enough rigid insulation on the outside?"
A. If your exterior foam is too thin, your sheathing will be cold during the winter, and it will accumulate moisture (a phenomenon sometimes called condensation, although the term "sorption" is more accurate). This moisture accumulation can lead to mold or rot.
Q. "How does that roof stack-up dry since it cannot dry to the exterior?"
A. It dries to the interior, which is why you shouldn't install any interior polyethylene with this type of assembly.
Roofs basically never dry toward the exterior- the roof deck itself is a class-II vapor retarder, and the typical shingles + felt layups are at the 0.1 perm boundary of being a true vapor barrier. EPDM roofing is less than 0.5 perms, well under 0.1 perms.
A roof deck that is vented on the underside has a dry layer of outdoor air that interrupts the migration of diffusion moisture coming from the interior when the roof deck is colder than the outdoor temp, and the roof deck stays dry.
An unvented roof always has to dry toward the interior. To keep the moisture level in the roof deck low enough to prevent mold, the amount of insulation above the roof deck has to be sufficient that the average winter temperature at the roof deck is above the dew point of the conditioned space air (typically 40-45F in a zone 4B winter.) The colder the climate, the greater the fraction of total R has to reside on the exterior.
When there is a sufficient ratio for dew point control at the roof deck layer, the interior side can be left fairly vapor open- even 5 perms (standard latex paint) is just fine, since the roof deck won't stay cold enough long enough to accumulate mold/rot levels of moisture, even if it drops below the dew point for hours overnight, or even a few days or even a week or more during an extended cold snap. Those ratios are built into the IRC code prescriptives, based on IRC code minimum R values. In zone 4B a code min roof is R49:
http://publicecodes.cyberregs.com/icod/irc/2012/icod_irc_2012_11_sec002.htm
...and the prescriptive exterior insulation for unvented roofs with Class-III vapor retarders on the interior is R15:
http://publicecodes.cyberregs.com/icod/irc/2012/icod_irc_2012_8_sec006.htm
R15/R49= ~30% If the total R is greater than R49, the exterior R has to grow proportionally to keep the average temp at the roof deck the same.
When there is NOT a sufficient ratio for dew point control, the vapor retardency toward the interior has to be much lower, but if you used a true vapor barrier (like 6 mil polyethylene) it becomes a "drys never" moisture trap. Smart vapor retarders such as 2-mil nylon have variable permeance. When the entrained air in the fiber layer is dry, under 35% relative humidity, the sheet nylon drops below 1 perm, and that's what happens whenever the roof deck is cold.
The dew point of the entrained air in the fiber layer will track the temperature of the roof deck during cold weather, since the roof deck takes on that moisture as adsorb. But when the roof deck warms up during the warm part of the day (or in the warmer weather of spring), releasing it's moisture burden, the RH in the cavity air goes way up, which causes the 2-mil nylon to become vapor open. So it's something of a moisture-diode, restricting the rate of moisture uptake, to levels roughly an order of magnitude slower that it lets moisture out. At moisture levels high enough to support mold the membrane is more vapor open than the ceiling paint, but standard latex paint is still a pretty good drying path- it's semi-permeable.
This material is pretty good, and it allows you to cheat a bit on the exterior R ratio since it's a Class-II vapor retarder restricting moisture uptake, but a Class-III vapor retarder when the moisture is being released from the roof deck. But it isn't good enough to allow you to skip the exterior insulation entirely, (at least not in a 4B climate.)