Rockwool ComfortBatt in a double stud wall

I’m looking for feedback on the use of Rockwool Comfortbatt insulation in a double stud wall instead of dense pack cellulose. The reason being a lack of confidence in local insulation contractor to properly dense pack a double stud wall. building will be in climate zone 6.
the assembly I am considering is as follows
-1/2″ drywall
-smart vapour retarder
-10.5″ double stud 2×4 wall with 3 layers of
3.5″ R14 rockwoll comfortbatt insulation
-cdx ply wood sheathing / air barrier
-wrb
-1×4 strapping for rain screen
-cedar lap sidding
thanks
GBA Detail Library
A collection of one thousand construction details organized by climate and house part
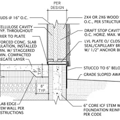
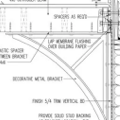
Replies
Michael,
Your plan will work. When using any type of batt -- fiberglass or mineral wool -- the key is careful installation. You want to make sure that there are no voids and minimal compression, and that areas behind electrical boxes and electrical cable are carefully detailed.
Use polyurethane caulk or other high quality purpose-specific sealant to air seal the CDX to the framing inside every stud bay, the seams of any doubled up framing such as top plates, jack studs, etc. and between the bottom plates & subfloor.
Invest in a batt knife to carefully sculpt around electric boxes etc, and to precisely split the batts around wiring & plumbing, etc.
To minimize voids & bypass channels, tuck the batts in around the full perimeter, sides top/bottom and corners, then gently tug them out until they are just proud of the stud edges to guarantee the fully meet the next layer of rock wool (or smart vapor retarder) without voids. Some insulation installers can do this level of batt detailing quickly and competently for a single studwall stud bay, and would be able to move up to doing a double-stud situation just as obsessively, but the average installer may need a bit more hands-on education (and not all are going to be receptive to it coming from anything but an expert installer.)
Hey guys
Thanks for the feedback. I am a lead builder for a local contracting company and have built many conventional homes but am new to green/ super insulated homes. I am planning to build my own home in the next few years. I would be doing all the work myself and am more than confident in my ability to install the bat insulation. Again this stems form a lack of confidence in local insulation contractor to do dense pack cellulose (clearly the preferred choice of seemingly everybody on GBA). I have seen them in action and after seeing how it should be done on GBA was not all that convinced. I am also looking at 2x6 wall with exterior insulation. However I would have to install upwards of 5" of comfortboard or foam to achieve the same r value as 3 layers of r 14 comfort bat. The bats are also much cheaper then comfort board or foam. I know that building 2 walls is more expensive than 1 but the simplicity of the exterior detailing on the double wall compared to 4 or 5 inches of exterior insulation appeals to me and may offset the extra cost of double wall framing.
I just want to say to Martin that I have your book and have read many of your articles including how to build a wall, all great stuff. I am sorry to bore you with questions about walls, but am just trying to learn as much as possible to become a better builder and to find an affordable wall system that I would be comfortable building.
Thanks for all the info
Don't over-count the R-value of the batts that are thermally bridged by framing. A 2x4/R15 rock wool wall is only about R9-R10 after thermal bridging is factored in, barely more than the R-value of continuous 2" of Comfort board. A 2x6/R23 rock wool layer comes in at about R15 after thermal bridging.
The intermediate layers that have no thermal bridging deliver almost full value, except for the thermal bridging of the subfloor & joists, and the top/bottom plates, etc (which can be designed with details to have less thermal bridging if you take the time.) At the same wall thickness it's higher performance to build a 2x4 structural wall, and add 2" of continuous rock wool than going with 2x6, even if the 2x6 is 24" o.c. and the 2x4 wall is 16" o.c., with a larger framing fraction.
In my opinion getting anyone to install batts into a double studded wall full of wires and pipes without voids is almost unthinkable. If you do not trust the dense pack installer’s, look for a wet spray cellulose installer.
What about the dense pack installer’s concerns you?
Your insulation is irrelevant unless your wall is almost air tight. Please take a look at the Zip sheeting.
Walta
CDX is a better choice for double stud walls than Zip sheathing because it is more permeable at high relative humidity. The exterior joints can be taped with Zip tape or 3M 8067, so I'm curious why Dana would recommend caulking every connection. I'm not opposed to belt-and-suspenders; I'm just not sure that it's necessary. With well-done cellulose insulation I would not worry as much about Zip because the borates in the cellulose protect the sheathing, but with Rock Wool you don't have that effect. I currently have data loggers in a Zip-sheathed, airtight, double-stud, cellulose-filled house I designed, and the RH is higher than I would like in the spring. I'm not worried about it, thanks to the magic of cellulose and rain screens, but on my current project we have switched to CDX for the walls and will likely data log it as well. I still like Zip for vented roofs and for projects with continuous exterior insulation, just not for double stud assemblies.
The Building Science Corp agrees, though everyone acknowledges that failed sheathing in a double stud wall is the Yeti of building science--nobody has seen it. But many moisture-related problems take ten years or more to make themselves apparent; I'm guessing that IF we see failures, it will be once the current popularity of double stud walls has resulted in more aged samples from which to choose.
If the wires are stapled to the back of the interior studs, installing batts should not be too cumbersome. There should be very few pipes in the exterior of a well-designed house. I would still prefer to use cellulose, for many reasons, but Rock Wool is a good product if carefully installed. If you're going through the trouble of doing this right, I would suggest making the wall 2" thicker and using R-23 batts for your center layer.
Exterior walls "full of wires and pipes". I see the same argument made for service cavities. What are all these wires and pipes? What are they doing in exterior walls? Very few if any pipes would be traversing them, and wires are easily routed through the bottom 8" of the bays with all vertical runs fastened to the studs.
Experienced insulation contractors in our area have been installing batts with few if any voids for decades. If the stud bays are fully enclosed and the batts proper installed, they perform very well. They also are a lot more resilient to minor work to the walls, and make remodelling a lot easier and DIY friendly. Even if there are good dense-pack installers in a region, I don't think batts can be ruled out as a good alternative.
OK, everybody has an opinion. Let's vote!
On the debate over exterior tape on the sheathing seams, or caulk on the interior joint between sheathing and framing, I vote for tape on the exterior.
On the debate over plumbing pipes in exterior walls, or no plumbing pipes, I vote for no plumbing pipes.
On the debate over blown-in insulation vs. batts, I vote in favor of careful installation of either material. Careful installation matters more than what type of insulation you use. Badly installed blown-in insulation, or badly installed batts, and much worse than well installed blown-in or well-installed batts.
I agree with Malcolm re: wires and pipes. All wires and pipes in exterior walls in our double stud wall are inside the inner stud space, except for exterior lights and hose bibs. We blew cellulose into the space outside the inner wall and installed batts in the inner stud spaces.
A combination of tape and caulk is necessary - tape works fine on most seams, but the bottom and top of the walls - any areas where tape isn't or can't be used - needs to be caulked.
+1 - what Bob said!
I'd vote for tape on plywood sheathing, plumbing pipes okay on interior side of double walls, but better in partitions for easier repair and less freeze potential. Try to keep electrical boxes in partitions when there's a choice near partition and wall intersections. Both dense packed cellulose or Roxul batts are great alternatives, but…Here's few other advantages of batts over cellulose in this case:
1. ComfortBatts are listed as R-4.2/inch vs. R-3+something/inch for cellulose, depending upon the density of the cellulose installation.
2. Let's not forget that Michael noted his lack of confidence in the quality of the cellulose installation. Its easy to specify dense-packed cellulose. Its tougher to do. Even experienced and motivated cellulose installers with the right equipment report that it is not easy to achieve the desired dense-packed densities. Seems clear that Michael has the skills, motivation and experience to install batts well.
3. Any small gaps between layers of ComfortBatts are likely much smaller and less critical than gaps across the top of stud bays after the cellulose compacts, following a likely mediocre installation.
4. Since Michael can do the batt installation, he doesn't risk possible delays from the cellulose contractor.
5. An owner-builder pockets the labor savings, instead of paying someone else for installation labor. What's the net savings (or cost) of materials plus labor for batts vs. cellulose in this case?
I agree that 5.5" R-23 (or even 7.25" R-30?) batts should be considered for the inner continuous insulation layer between the double stud walls. Many advantages of higher-R-value walls offset the increased materials cost.
Also might be good to move the smart vapor retarder to the exterior side of the interior double stud wall, rather than next to drywall. Would avoid more detailing around electrical boxes and partition-wall intersections. Avoids puncture when someone decides to hang pictures or cut into drywall.
My vote is for gaskets over tape over caulk over canned spray foam. And air sealing of both the exterior side of exterior sheathing and airtight drywall (skip caulking the stud bays).
That being said, data would be much more valuable than a vote.
>@Michael M
>cellulose-filled house I designed, and the RH is higher than I would like in the spring.
Just curious - are you using MemBrain or Intello to reduce the wetting rate?
"Just curious - are you using MemBrain or Intello to reduce the wetting rate?"
For zone 6 that's pretty likely, and may even be needed for overall resilience when using rock wool for the insulation instead of cellulose. Vapor barrier latex primer would work too, provided the wallboard is air tight.
Replacing the CDX with fiberboard sheathing could still fly with the rainscreened cladding approach without the vapor retarder in the US, as the "Vented cladding over fiberboard" exception in the IRC:
https://up.codes/viewer/wyoming/irc-2015/chapter/7/wall-covering#R702.7.1
But in Canada the broadsheet vapor retarder is often necessary to clearly meet the NBC to the satisfaction of the local inspector, even in stackups where it's not really needed.
@Jon R, on that house we used the airtight drywall approach at the interior, with gaskets and the works, in addition to airtight Zip sheathing. (It blower doored at 0.25 ACH50.) On the current project I spec'd Siga Majrex, Intello Plus or Membrain at the interior, at the builder's discretion. He used Pro Clima Solitex Mento as the WRB so I imagine he'll use Intello on the interior.
Dana,
I'm still trying to work this through. If a vapour barrier paint would add resilience to the assembly, wouldn't a poly vb do the same? If it does add resiliency, and drying to the inside isn't necessary, is there any harm in the Canadian poly requirement that isn't there with vapour barrier paint?
Malcolm- order of magnitude:
Standard latex interior paint is about 3-5 perms...
... vapor barrier paint is about 0.5 perms...
...4 mil polyethylene runs about 0.1 perm...
...6 mil polyethylene is about 0.05 perms.
At 0.5 perms any winter accumulated moisture can dry into the interior well before June, and bits of wind-blown bulk moisture getting in the wall can still dry before the end of the summer unless it's a chronic leak. The amount of moisture that 0.5 perms releases in one temperate temperature month takes nearly a full year's worth of consecutive temperate months though 0.05 perms, which is essentially never, or 5 consecutive months of 0.1 perm, which is "maybe, someday". It's a fairly big difference in the ability of the wall to dry.
There is no such thing as a "...Canadian poly requirement..." under the NBS, which requires only...
"... a permeance not greater than 60 ng/Pa-s-m2 measured in accordance with ASTM E96, “Water Vapor Transmission of Materials” by the desiccant method (dry cup). "
One US perm is 57.2 ng/Pa-s-m2, a bit less than 60, so the NBC maximum spec is really just bit over 1 US perm.
That means half-perm "vapor barrier latex" paint fills the bill per the NBC comfortably, but without the extreme vapor tightness of 4 or 6 mil polyethylene. The peak moisture content at the sheathing in winter is only marginally higher than with polyethylene and well under what it takes to keep mold/rot issues well bounded, but it can give it back up toward the interior at 5-10x the rate. That makes it more resilient.
Dana,
Thanks, that's very useful. The tenfold increase in drying between the two is a significant difference.
It was also good that you reiterated there is no requirement for poly in Canada. I was using it as a shorthand for both the common insistence of inspectors that it be included, and the almost universal use it still enjoys here in building assemblies.
I'm not sure on which vapour retarder I'll be using. Still in early planning. Not sure which products are avalible in Canada. Was thinking something like Intelo or membrane. Any Recomendations ?
Malcom, note that if you have good perms to the exterior (eg, 10 perms), then Winter moisture drying to the inside isn't necessary or significant. On the other hand, with low perms (eg, Zip) or AC use, then drying to the inside matters.
The below calculator will provide vapor pressure and from there it's easy to calculate delta-VP and moisture transfer rates.
https://www.weather.gov/epz/wxcalc_vaporpressure
Jon,Good point. It's a theoretical question for me as I never spec or use low-perm exterior sheathing and we have to install rain-screens here. What I was curious about (given we have to install a VB) is whether an interior finish as low a 0.5 perms would ever yield useful drying. Dana thinks it does in that situation anyway - and perhaps in ours.
Here in the PNW our sheathing doesn't get cold enough during the winter to inhibit mold, and depending on the site, often doesn't dry much over the summer, especially on the north side. Any inward drying would be very useful.
@JonR, I don't know where you're getting a 30:1 price difference. Perhaps it was a typo. Membrain runs about $0.15/ft² and Intello is about $0.41/ft², so less than a 3:1 difference.
Have you ever tried installing either Membrain or Intello? Intello is much, much more robust--you can even dense pack behind it if you're good (the insulator on this job is good). The cost difference for a whole house is a few hundred dollars--notable, but should not be a deal-breaker if you want a tougher product. That said, Membrain has slightly better performance numbers, so the choice of product depends on the situation.
With a ~30:1 (edit: see correction below) price difference (Intello to MemBrain), if I had a good (say better than 1:10) inside/outside perm ratio, I'd use MemBrain.
Poly is great for avoiding cold weather moisture in the walls - but not good if you run AC.
You are right, thanks for the correction.
No argument about other advantages of Intello. Don't know where "Membrain has slightly better performance" comes from. Intello has far less cold weather wetting (like 1/4) and opens up later (a good thing).
I suppose "better" is subjective. Going by their ASTM E96 wet cup/dry cup numbers, Intello ranges from 0.2 to 6 perms, and they claim to be vapor retarding up to 70% RH. Membrain states ≤1 to >10 perms, vapor retarding to 60% RH. Intello lists a wider permeance range using DIN EN 1931 but Membrain doesn't offer comparable testing data that I can find. I don't know what Membrains' low perm rating really is but you're right that Intello appears tighter. Membrane becomes more vapor-open, though the difference between 6 and >10 perms is probably not significant.
If you're trying to keep humid air out of an assembly, opening up at a higher RH is good, but if the concern is high RH within the assembly, I would rather have it open up earlier. 60% happens to be about what mold likes and nobody should have interior RH of over 60% (when it's cold out anyway) so I don't know why opening up later would be a better thing.
All in all I would say the differences are marginal, but for the things I'm usually concerned about, Membrain's performance numbers are slightly better. But I still prefer Intello.
"Membrane becomes more vapor-open, though the difference between 6 and >10 perms is probably not significant."
Given that the vapor permeance of a couple coats of standard latex interior paint & primer is 3-5 perms, it really doesn't make any practical difference at tall, at the higher cavity-air RH. The more important range is the %RH at which it's between 1-3 perms.
MemBrain is under 1 perm when the proximate air adjacent to the vapor retarder is ~35% or lower, and rises to above 3 perms @ ~50% RH:
https://foursevenfive.com/wp-content/uploads/2017/06/membrain-curve-open-to-early.jpg
(Note that vendors of Intello make the pitch that MemBrain becomes vapor open "too early".)
With Intello it's under 1 perm at ~ 60% RH or lower, but doesn't rise to 3 perms until nearly 80% RH:
http://www.foursevenfive.com/wp-content/uploads/old/2013/06/INTELLO-vapor-curve.jpg
One could just as easily argue that Intello become vapor open too LATE, given that mold risk is pretty high at 70% RH and above.
But in practice either one works just fine. In a Washington State University test building MemBrain was effective even when the interior RH was kept at a fairly high 50-55% range, with a less-than-favorable unvented stucco over OSB sheathing stackup. See the data for wall #2 on p16 (PDF pagination):
http://www.energy.wsu.edu/documents/AHT_ComparingTheMoisturePerformance%20Of%20Wood%20Framed%20Wall%20Systems.pdf
Given that at 50-55% RH MemBrain is running about 5 perms, in combination with latex paint the total permeance to the interior was probably about 2 perms when the OSB was cold, but no lower than 5 perms even when the OSB was warm and releasing the moisture. The sensor with the highest peak moisture content was the top plate of the studwall near the sheathing (see p14 for sensor locations), but it still peaked at less than 20% MC.
In more normal wintertime interior RH the MemBrain would have been more vapor tight, and sheathing would clearly stay drier, even with effectively zero drying toward the exterior (unvented stucco, in a rainy climate.) With a more favorable exterior stackup it would be drier still.
Re: WSU
It's interesting how poly + ventilation (#4) outperformed MemBrain (no ventilation, #2). Suggests that interior drying can be unimportant.
This source reports no risk of mold at 60%. Perhaps on other substances.
http://energyhandyman.com/knowledge-library/mold-chart-for-temperature-and-humidity-monitors/
"This source reports no risk of mold at 60%."
Sure at 60% it's low/no risk, but at 70F or higher the risk climbs pretty fast when it's above 70% RH.
At 70F, 80% RH it's less than 2 weeks to mold, which is the point. Intello isn't as vapor-open as standard interior latex paint unless the RH is 80% or higher.
The referenced mold-risk chart:
http://energyhandyman.com/wp-content/uploads/2012/05/TEMP-RH-and-MOLD-Charts.jpg