Rockwool and polyiso instead of spray foam to make a conditioned attic?

LukeSkaff
| Posted in General Questions on
I am looking to convert my attic to a conditioned attic. The property is a townhome in Charlotte, NC, climate zone 3A. The attic is 2×4 24” on center truss framed, 7:12 pitch, and the long-term plan is to convert the attic to living space which will overlook the city skyline. I have used spray foam in the past and have never been happy with how long it takes for the smell to go away in hot attics. Between the projects I have done and family member’s homes that have used spray foam it took 2-4 years for the smell in the attic to go away after spray foaming so I would like to move to other options.
I am looking to do a modified Cut-and-Cobble insulation method in the 2×4 truss bay, additional insulation will be added below the truss cord (truss bay) to bring the insulation up to R38 ceiling code in my climate zone. I want this post’s main point of discussion to be about the insulation in the truss bays though as that has the largest number of unknowns for me and concerns from a building science perspective.
Many of the truss bays in the attic do not have a clear path to a soffit vent so this will be an unvented assembly. My original plan was to insulate the attic per the Johns Manville AP Foil polyiso attic insulation application product bulletin, page 3 “Unvented Roof Sheathing”
<See attachment below from John Mansville product bulletin>
A 3.5in sheet of polyiso would provide R22 but with the roof nails and osb chips sticking out from the roof nails I would never be able to get the polyiso flush with the truss 2×4. My next thought was to use 3in of polyiso (R19) and leave a 0.5” air gap behind the polyiso for the roofing nails but I think the below solution would be better and easier to source.
Foil faced polyiso above 2in polyiso in my area is special order in large quantities and expensive. I am thinking to use 1.5” of Rockwill Comfortboard 80 (R6) then 2in of polyiso (R13) for a total R-value of R19. The flexibility of the rockwool will go between the roof shingle nails, fill any voids, and allow the polyiso to be flush with the truss 2×4 cord.
<See attachment of a rough mockup I drew in Chief Architect software>
The areas of the roof that have soffit vents will be blocked off with rigid foam or a small amount of spray foam to not allow vapor or air to enter the rockwool and the insulation will run up to the ridge vent. The attic will be air sealed by can spray foaming between the rigid foam and the 2×4 truss cords. As I currently have it planned the rockwool would go to the ridge vent, I do not know if this would allow for the possibility for moisture in the outside air that came in through the ridge vent and traveled through the rockwool to condense on the underside of the sheathing? Should I run the rockwool and polyiso down to about 6 inches away from the ridge vent and soffit vent and seal these areas off with 2-part closed cell spray foam instead (such as dow froth-pak)?
GBA Detail Library
A collection of one thousand construction details organized by climate and house part
Search and download construction details
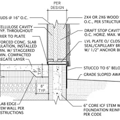
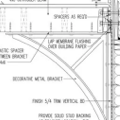
Replies
Luke,
You are in a townhome with other owners on each side of you. I think you need to consult your HOA agreements before spending anymore time on this idea. It is quite possible that restrictions are in place for any remodeling of the exterior surfaces. Particularly roofs, which I am thinking you would need to change with a lift dormer or possibly a large opening skylight like they use in Europe.
Your description of the attic space is confusing to me, you show a borrowed diagram of a fairly normally framed room and then a rendering of trusses which you have described as 7:12 pitch on 24" centers. Are the trusses actually framed with a defined room in the profile and code access to same? If the trusses are the usual forest of 2x4's at angles then the "attic" is not really meant to be accessed for anything other than minimal storage and checking pipes and vents.
The fact that there is no insulation on the underside of the roof has me thinking that the R38 required for code is on the floor of the "attic" and the trusses are not set up for a finished room. You absolutely must not cut any element in a truss without engineering analysis.
Even if there is a proper stair access and a room framed into the trusses the path you are suggesting for insulation is not going to work well. Rather than dive into the many points needed to be addressed about insulation and changing a vented roof to non-vented, you first need to check with building authorities and the HOA. Your insurance company will also need to be in on the plans.
Roger,
Thanks for your concern as these are major consideration items I would be telling someone considering this as well. I am on the board of the HOA and other units have rooftop terraces already so others on the board and in the community are open to the idea. I am an engineer and know there is a highly complex process to converting truss framing. I would never do anything this major to structure without going through extensive planning with load calcs and a PE stamped plan approved by the city and HOA board.
From a building science perspective is there any concern to have rockwool as the first layer of insulation against the sheathing going to the ridge vent? Will outside air moisture get into the rockwool from the ridge vent and condense on the underside of the roof sheathing on cool nights? I could leave a gap at the ridge and fill it with closed cell spray foam to lock the rockwool into a vapor tight space. You stated the R38 is for attic insulation and may not apply when used in a cathedral style ceiling or conditioned attic? My interpretation of the code is this is required regardless if this is a attic floor, conditioned attic, or cathedral ceiling. Is this not correct?
Luke,
Good to know you have to the two most critical concerns in the bag already. If the runway is clear for even thinking about the project, then I guess my main concerns would be with the choices of insulation and the plan to not vent.
Small air leaks like small water leaks don't go away and they typically don't leak to the good side of moisture control. I am a strong disbeliever in air sealing drywall as a primary plan for moisture management for the same reason I would question how successful you would be with the hundreds of feet of sealing facing you. Your climate is mild overall, but moist much of the year if my few visits to the area are valid experience. The cycling of air temperatures and humidity loads would most likely not lead to good results with anything but closed cell foam applied to the underside of the roof deck for an unvented plan.
Air conditioning of the attic space will be an issue as well. Do you have plans for separate heating and cooling? Can you control the air exchange between floors to satisfy comfort for all levels? Without a much clearer picture of how the room relates to the roof profile and vents, I am hesitant to say much more. There are much better minds than mine with much more experience dealing with humid climates here at GBA. I hope some will chime in and guide you better than I can. In my own build, I went totally non-vented with all the details of WRB and roofing choices made at the outset. Attempting a conversion after the fact will be very tricky.
The JM brochure is a bit frightening with the exception of figure 5. Figure 3 is especially insane (aside from ignoring minimum R values) where it specifies a minimum of 1/2" penetration for the fasteners going outward. Many roofs are decked with 1/2" or less sheathing. Putting myriad little holes in the roof underlayment is just asking for problem. Stacking up foam sheets between rafters and shooting ever longer fasteners would almost certainly end up with screws or nails poking all the way through to lift or penetrate the shingles. Yes the shingles are nailed on from the other side, but you get to cover the penetrations in a controlled manner. Plus what would be the scenario come time to re-shingle?
Anyway, if one could absolutely encapsulate the comfort board or batts against any air exchange then you might avoid moisture build up over time. However, please note the many references in GBA about roof failures caused by can lights, chimney pass thru-s and other seemingly benign details. Can you seal the soffits adequately, can you seal the roof vents, can you prevent stack pressure over what would appear to be three floors when the attic is done? Remember, like water leaks, air leaks of humid air into batts will tend to only get wetter and wetter.
It seems likely the room plan you have in mind will end up framing out much like the notorious Cape Cod second floor with knee wall issues. (At least on one side.) Since ice dams are unlikely where you live, why not go with the venting you have and drop the whole insulation envelope to the interior edge of the truss elements and new framing and let the venting be functional. Trying to bullet proof the insulation all the way down to the eaves will be an unenviable task even with a 7:12 pitch.
All good points, and I agree it would be very hard to guarantee air tightness between the rigid foam and the interior conditioned space. This is still in the early planning stages but I have been struggling how to do this without a large quantity of 2-part spray foam. Maybe I should have the truss bay filled now with 3.5 inches of spray foam and leave the ridge and soffit vents open to let it vent \ offgas for a year or so before sealing off the ridge and soffit.
I was thinking to do this in stages where stage one would be to condition the attic to make it easier to work in it while doing the long tedious conversion. Stage one would only be the insulation between the truss bays until the attic is converted. I will do a lot of work myself with helpers but am very detail oriented.
I wanted to go with mostly rigid foam for the higher valve per in as you start to cut into ceiling height quickly to hit R38 with rockwool or fiberglass. But going unvented with all batt insulation is an option too and supported in the 2018 IRC. That probably would be a safer bet as it would allow small amounts of moisture to dry to the inside.
https://information.insulationinstitute.org/blog/unvented-attic-with-fiberglass-and-mineral-wool#_ftn1
To answer some of your questions, I would not use fasteners in the polyiso, it would be sealed with can spray foam which I have never had issues with in smell and off gassing like 2-part foam. I know details matter a lot here to make sure it is airtight. The HVAC system is currently a full variable speed compressor unit and I will add zoning to it. With some rough manual J calcs it can support this extra space especially after I seal up the builder grade air sealing in the building. I will have a dedicated ERV and whole house dehumidifier by the time I convert the attic. The attic loft would be open air to the rest of the house, no driver door. The roof is new and they used a breathable underlayment, I know asphalt shingles are extremely low perm but this does allow some drying in the sheathing in ridge vent area and small amounts of moisture that would accumulate under the underlayment.
Unvented cut and cobbled cathedral ceilings (like you are proposing) seem to be pretty universally discouraged on GBA. The building science problem typically cited with this approach is that it's too difficult to do a perfect job with the air sealing, and even small air leaks can cause major moisture issue with this style of assembly. And if it's considered to be too risky cut and cobbling between conventional rafters, trying it between trusses sounds even tougher.
It'd probably be worth it to take a second look at if any of these approaches are plausible for you:
- Unvented, rigid above roof sheathing. In your climate zone, you don't need much rigid insulation above the sheathing (BSC lists R-5 rigid for an R-38 assembly in climate zone 3: https://www.buildingscience.com/documents/building-science-insights/bsi-100-hybrid-assemblies), so this might be easier than it is in other climate zones.
- Unvented, spray-foam. Perhaps the spray-foam smell problem is solvable?
- Vented. Perhaps the lack of continuous vents can be solved with a different approach to the shape of the roof?
Brendan, thanks for the suggestions. That link is a good read. Exterior rigid foam on the roof deck would be awesome but unlikely to be approved as it would add height to the road facing roof side and may look "goofy" next to all the other units roof lines. I may be able to do this on the back side that overlooks the city and can not be seen from the street.
Maybe I should just fill the truss bays with closed cell foam except the ridge and soffit to let it bake and off gas for a year then come back later and have the ridge and soffit sprayed to seal it up and condition it. At least that way it would be vented while it off gassed and not smell up the house every hot day.
It's easier to hit code-min on a U-factor basis (= < U0.030, or R33.3 "whole assembly" ) than it is to hit R38.
I agree with Roger Berry that several recommendations in the JM sheet are dubious at best, and some even constitute IRC code violations.
It's a lot safer to go vented, which is possible even though some of the truss-chord bays don't hit the ridge:
With 1x4 strapping screwed or ring-shank nailed perpendicular to the truss chords (so that even blind truss bays can be vented to adjacent/other truss bays), 5" of continuous foil faced polyiso (R30) or 5.5" of continuous roofing polyiso (R31.4) cap-screwed/nailed to the strapping , with another set of strapping through-screwed for mounting the ceiling gypsum easily clears the U0.030 hurdle with nothing between the truss chords after factoring in the R-values of the roof deck & roofing, the gypsum board, the air films between the gypsum & polyiso, the air films between polyiso and roof deck, and the exterior air film. That eats up 7-7.5" of interior space, but it's more resilient, less work, and cheaper than the rigid rockwool + cut'n'cobble, etc. especially if using reclaimed roofing polyiso at 1/4-1/3 the price of virgin stock goods.
Reclaimed foam also has a MUCH lower environmental footprint than any new insulation (rock wool or foam), since it's only extending the benefit side of the cost/benefit balance of an environmental hit taken years or even decades ago.
>" Will outside air moisture get into the rockwool from the ridge vent and condense on the underside of the roof sheathing on cool nights? "
The exterior of the roof will be colder than the interior through the ~R1 of roofing + roof deck, so any outdoor air entering the vent space will usually have a dew point lower than the temperature of the underside of the roof deck. Even when radiational cooling puts the roofing below the outdoor dew point temperature there will never be condensation on the interior of the roof deck, though some amount will be taken up into the wood as adsorb, then released when the roof deck temperature rises. There is no theory under which air transported moisture from the outdoors achieve wood moisture content high enough to create a mold & rot problem.
That said, air leaks from the interior can hit rot-levels at the roof deck, but only if the roof deck isn't vented to the outdoors and the air leaks are pretty significant.
Dana, for your first idea of using 5" polyiso with strapping is that something someone has documented online? That is certainly an interesting idea, I have seen something very similar that does not have strapping behind the rigid foam. Here is a dumbed down marketing video that shows a good mockup.
https://www.youtube.com/watch?v=6F_IkZJ8NOY
You mentioned reclaimed polyiso, is this reclaimed from old roofs? What is it reclaimed from?
To your last point about roof deck rot. Are you saying if there is a high level of air sealing on the interior side of the polyiso to the truss cords the rockwool against the underside of the rood deck would not be a risk for condensation even if exposed to the ridge vent?
>"Dana, for your first idea of using 5" polyiso with strapping is that something someone has documented online?"
I'm not sure if anybody has documented that approach, but interior side continuous foam is a common enough assembly. The use of cross-venting with the strapping would be less common, but is clearly better than an unvented cut'n' cobble, and with a 4" bay to dry into, doesn't need much actual air movement to work.
If all rafter bays could be vented at both the soffit and ridge it wouldn't need the 3/4" gap provided by the strapping- that's only needed to deal with the bays that terminate on other framing, not at the ridge.
>"You mentioned reclaimed polyiso, is this reclaimed from old roofs? What is it reclaimed from?"
Roofing foam is a commonly & easily reclaimed valuable material from commercial building demolition & re-roofing projects. Many foam reclaimers also trade in factory seconds/blemished foam, with dings in the facers, thickness that was slightly out of spec, etc. Factory seconds goods are usually more expensive than reclaimed goods.
Reclaimed foam has often shrunk a bit from it's original dimensions- a 4' wide sheet might actaully be 47.75" on one end, 47.9" on the other, and instead of 3" everywhere it might be 2.9" on one edge, 2.85" on another edge, etc. But it's still cheap and quite effective.
>"To your last point about roof deck rot. Are you saying if there is a high level of air sealing on the interior side of the polyiso to the truss cords the rockwool against the underside of the rood deck would not be a risk for condensation even if exposed to the ridge vent?"
The only condensation/adsorption risk at the roof deck is from interior side moisture drives, when the roof deck's average temperature over a season is below the average dew point of interior air. A tiny air leak on the interior can move a lot of moisture, a square inch of air leak moves more moisture than a whole ceiling's worth of vapor diffusion through unpainted gypsum board.
A roof vent open to the much drier outdoor air dilutes any moist air that's coming from the interior. That's the whole point of soffit to ridge venting- even modest amounts of convection will constantly replace any moist-air contamination of the air in the vent channel with drier (in winter) outdoor air, interrupting the path from the moist indoors to the cold roof deck, making it much more tolerant of incidental tiny air leaks, and totally tolerant of mere vapor diffusion rates. Even if the gap is only vented at one end some amount of drying occurs, but far less than when the air body in the vent cavity is getting purged with outdoor air multiple times per day via convection or wind pressure.